Precision Thermal Management: Advanced Thermal Gel Dispensing Capabilities at Modus
March 5, 2025
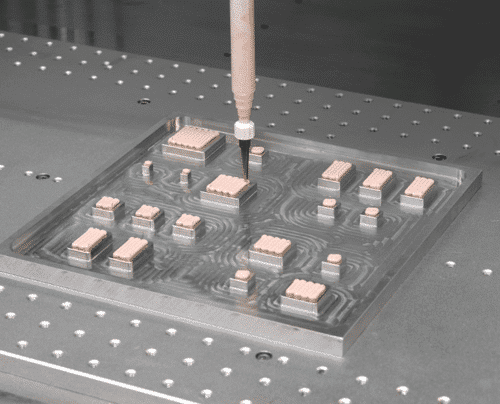
Manufactured with Speed and Precision
The manufacturing capabilities you need and the engineering support you want, all from a single partner.
Submit a DesignKey Points
- Parker Therm-A-Gap silicone-based thermal gel materials provide excellent thermal conductivity for critical applications in aerospace, defense, and medical devices.
- Our advanced dispensing systems, including progressive cavity pumps, allow for precise application with minimal waste and maximum efficiency.
- Different dispensing patterns (dots, serpentine, and spiral) offer flexibility to optimize thermal performance based on your specific application requirements.
- Automated dispensing can significantly reduce assembly time while improving consistency and reliability compared to manual thermal pad placement.
- Modus Advanced's engineering team provides design support to help you select the optimal thermal material and dispensing pattern for your application's precise needs.
Understanding Thermal Gel Applications
Thermal management plays a critical role in today's sophisticated electronic systems where heat dissipation directly impacts device performance, reliability, and lifespan. While traditional thermal pads have long been the standard, dispensable thermal gels offer significant advantages for complex geometries and high-volume production.
At Modus Advanced, we've invested in advanced dispensing technology to support mission-critical applications where thermal management is non-negotiable. Whether you're designing life-saving medical equipment or aerospace systems where reliability is paramount, our thermal gel dispensing capabilities deliver precision and consistency that standard thermal interfaces simply can't match.
-- Article Continues Below --
Essential Guide to Thermal Management: Get it Here
Parker Thermal Gel Material Advantages
Parker Therm-A-Gap thermal gels represent the cutting edge of thermal interface materials, with unique properties that make them ideal for demanding applications. These silicone-based materials arrive fully cured and ready for precise dispensing onto your components.
Our extensive work with these materials has revealed several distinct advantages compared to traditional thermal pads:
- Excellent Gap Filling: Gels naturally conform to an uneven surface and irregularities, eliminating air gaps that reduce high thermal conductivity
- Immediate Adjustability: Unlike pads, gels can be repositioned immediately after dispensing if needed
- Superior Target Area Coverage: Gels flow to fill complex shapes and surfaces that pads may not adequately cover
- Higher Volume Capability: Thicker application is possible without the handling challenges of thick thermal pads
- Reduced Assembly Time: Automated dispensing significantly speeds production compared to manual pad placement
The silicone base provides exceptional temperature stability across a wide operating range, making these materials suitable for applications that experience significant thermal cycling or extreme conditions.
Advanced Dispensing Systems and Methods
Precision dispensing of thermal conductive gel materials requires specialized equipment designed to handle the unique properties of these materials. Our engineering team has tested multiple dispensing technologies to identify the optimal systems for different application requirements.
We've found that progressive cavity pumps provide the most consistent and reliable dispensing for most thermal paste applications. These systems offer:
- Material Integrity: Progressive cavity design minimizes shearing forces that could degrade the thermal material
- Precise Volume Control: Accurate dispensing amounts reduce waste and ensure proper coverage
- Consistent Flow Rates: Critical for maintaining uniform thermal interface thickness
- Compatibility: Our volumetric dispensing system works exceptionally well with Parker Therm-A-Gap materials
Additionally, our Datron system provides an alternative dispensing option for specific pattern requirements, particularly serpentine patterns that require more complex motion control. Our dual-system approach ensures we can match the right technology to your specific application needs.
Optimizing Dispensing Patterns for Performance
The pattern used to dispense thermal gel can significantly impact thermal performance and manufacturing efficiency. Through extensive testing, we've identified the advantages and limitations of various dispensing patterns.
Each pattern offers distinct benefits for different applications:
- Dot Patterns:
- Fastest and simplest to dispense
- Provide excellent coverage when compressed
- Minimize air entrapment during assembly
- Ideal for high-volume production where speed is critical
- Serpentine Patterns:
- Cover rectangular areas efficiently
- Work well for specific component shapes
- Can be precisely controlled for consistent coverage
- Best dispensed using our Datron system for optimal results
- Spiral Patterns:
- Excellent for circular components or heat sources
- Provide uniform coverage from a central point
- Can be optimized for different compression ratios
- Dispense efficiently with our volumetric dispensing system
The optimal pattern depends on your specific component geometry, thermal requirements, and production volume. Our engineering team can provide simulations showing how each pattern will perform under compression in your specific application.
Selecting the right dispensing pattern dramatically impacts both thermal performance and manufacturing efficiency.
Design Considerations for Thermal Gel Applications
When incorporating thermal gels into your design, several key factors will impact performance and manufacturability. Our extensive experience with thermal applications has revealed important design considerations that help ensure optimal results.
Height and dimensional specifications play a critical role in thermal gel applications:
- Height/LxW Dimensions: These are the most critical specifications we need from customers to properly design the dispensing program
- Pattern Selection: Different patterns have different measurability characteristics that impact final quality verification
- Tolerance Requirements: We can typically achieve tolerances comparable to die-cut thermal pads
- Size Considerations: Larger patterns generally produce more consistent and reliable results
- Needle Selection: Larger diameter needles are recommended to avoid shearing the material and affecting thermal properties
For optimal results, we recommend:
- Working with our engineering team early in the design process
- Providing detailed information about the components being joined
- Considering the compression force available in your assembly
- Allowing for appropriate tolerances in the initial prototype phase
Early collaboration with our engineering team can help identify potential issues before they impact your production timeline.
Manufacturing Advantages of Thermal Gels
Beyond the thermal performance benefits, dispensable thermal gels offer significant manufacturing advantages over traditional thermal pads. These advantages directly translate to reduced production time and costs for our customers.
Our automated dispensing systems provide:
- Reduced Material Waste: Our volumetric dispensing system has demonstrated dramatically reduced material waste compared to manual methods, using as little as 1/4 of a kit for a typical application including setup
- Faster Processing: Automated dispensing eliminates the need for manual handling and placement of individual thermal pads
- Consistent Application: Machine-controlled dispensing ensures uniform material distribution across all components
- Simplified Inventory: Single material source versus multiple pre-cut pad sizes
- Design Flexibility: Changes to thermal interface dimensions require only program adjustments rather than new pad tooling
The most significant advantage comes in high-volume production, where these efficiencies compound to provide substantial time and cost savings while maintaining exceptional quality.
Why Choose Modus Advanced for Thermal Management Solutions
At Modus Advanced, we understand that thermal management isn't just about keeping components cool—it's about ensuring your mission-critical devices perform reliably under the most demanding conditions. Our thermal gel dispensing capabilities represent just one facet of our comprehensive approach to solving complex engineering challenges.
What sets Modus apart from other manufacturers is our engineering-first approach. With engineers making up more than 10% of our staff, we bring deep technical expertise to every project. This expertise allows us to:
- Recommend the optimal thermal material for your specific application
- Design dispensing patterns that maximize thermal performance
- Optimize manufacturing processes to reduce costs and improve quality
- Provide comprehensive design feedback to improve overall product performance
Our AS9100 and ISO 9001 certifications ensure that every thermal management solution we provide meets the highest quality standards, while our vertical integration capabilities allow us to handle multiple manufacturing processes under one roof—reducing lead times and simplifying your supply chain.
When one day matters in bringing your life-changing innovations to market, choose a partner who understands the critical importance of every component in your design.
Ready to Optimize Your Thermal Management?
If you're designing a new product or looking to improve the thermal performance of an existing design, our engineering team is ready to help you explore the advantages of dispensable thermal gels. Contact Modus Advanced today to discuss your specific requirements and discover how our thermal management expertise can help bring your innovations to market sooner.