Aeroglaze A276 Replacements and Alternatives: Polyurethane White Coating
April 9, 2025
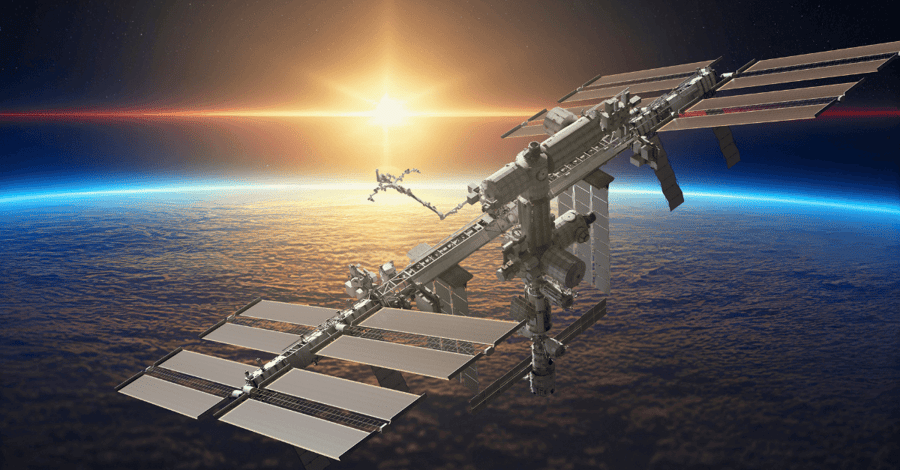
Manufactured with Speed and Precision
The manufacturing capabilities you need and the engineering support you want, all from a single partner.
Submit a DesignKey Points
- Recent supply chain disruptions have created critical shortages of Aeroglaze A276 polyurethane coating, impacting aerospace and defense manufacturing timelines.
- AZ-400-LSW white thermal control paint serves as a viable alternative with comparable performance characteristics for many applications.
- This silicone-based replacement offers several advantages including extreme low outgassing properties and easier application without requiring controlled temperature and humidity.
- Engineers should understand key technical differences when transitioning between these materials to ensure optimal performance in critical applications.
- Early consultation with manufacturing partners about material substitutions can prevent costly delays in mission-critical projects.
The Current Aeroglaze A276 Supply Crisis
Many aerospace and defense manufacturers are facing a significant challenge. The recent natural disaster has severely disrupted the supply chain for Aeroglaze A276, a widely used polyurethane coating essential for numerous critical applications.
This white reflective coating has been the industry standard for decades, specified in countless designs and approved by major aerospace companies including Boeing, Lockheed Martin, Northrop Grumman, and Raytheon.
For engineers working on projects with tight deadlines, this supply disruption creates urgent questions about viable alternatives. When lives depend on your innovations, material substitutions require careful technical evaluation, not just quick replacements.
Understanding Aeroglaze A276 Performance Requirements
Before exploring alternatives, it's important to understand the key performance characteristics that make Aeroglaze A276 so widely specified in aerospace and defense applications. This moisture-curing polyurethane coating delivers specific technical properties that engineers rely on.
Aeroglaze A276 provides critical performance in several areas:
- Low Outgassing: Exhibits minimal gassing properties in vacuum environments, essential for space applications
- Chemical Resistance: Cures to a hard surface resistant to acids, alkaline detergents, lubricants, and chemicals
- Color Retention: Delivers excellent colorfast, non-chalking finish
- Solar Absorptivity: Features a low 0.23 value, important for thermal control
- Appearance: Cures to a high-gloss white finish
The coating's technical specifications include 54-58% solids content by weight, with an optimal dry film thickness of 1.5-2.0 mils. It performs within operating temperature parameters common in aerospace applications and adheres well to properly prepared substrates.
These requirements establish the baseline for evaluating potential replacement materials.
Visit the Resource Center: Advanced Coatings for Aerospace Optics
Introducing AZ-400-LSW: Technical Overview
AZ-400-LSW white thermal control paint offers a compelling alternative for engineers facing Aeroglaze A276 shortages. This specialized coating was developed specifically for spacecraft and satellite applications, with a focus on thermal control performance.
The technical composition features a specialized pigment in a silicone binder, creating a flexible organic non-specular white coating. This formulation delivers several key performance characteristics:
- Extremely Low Outgassing: Meets or exceeds stringent requirements for space applications
- Thermal Properties: Provides thermal emittance (εt) of 0.89 ± 0.02
- Solar Absorptance: Features αs of 0.169 ± 0.02 at ≥3.0 mils thickness
- Temperature Range: Functions from -180°F to 700°F
- Appearance: Non-specular optical white finish
- Application: Can be spray deposited with airbrush or HVLP systems
- Compliance: Meets flammability and toxicity requirements of NHB 8060.1C
AZ-400-LSW requires a nominal dry thickness of 3.0 ± 1.0 mils over 85% of the coated area and demonstrates good adhesion with ASTM D3359A adhesion grade not less than 3A.
Engineers should note the full cure time of 48 to 72 hours when planning production schedules.
Comparative Analysis: A276 vs. AZ-400-LSW
When evaluating AZ-400-LSW as a replacement for Aeroglaze A276, engineers must understand key technical differences between these materials. While both serve similar functions, their formulations and performance characteristics differ in important ways.
The table below provides a direct technical comparison of critical parameters to help engineers quickly assess compatibility for their specific applications:
Parameter | Aeroglaze A276 | AZ-400-LSW | Potential Impact |
Base Chemistry | Polyurethane | Silicone | Different chemical resistance profile |
Appearance | High-gloss white | Non-specular optical white | May affect optical properties |
Solar Absorptance (αs) | 0.23 | 0.169 ± 0.02 | Better thermal control with AZ-400-LSW |
Thermal Emittance (εt) | Not specified | 0.89 ± 0.02 | Important for heat dissipation |
Application Method | Spray or brush | Airbrush or HVLP spray | Similar application techniques |
Environmental Control | Temperature sensitive | No specific temperature/humidity requirements | Easier application with AZ-400-LSW |
Dry Film Thickness | 1.5-2.0 mils optimal | 3.0 ± 1.0 mils | Different thickness specifications |
Curing Mechanism | Moisture cure | Silicone cure | Different curing timeframes |
Curing Time | 14 days for ultimate properties | 48-72 hours for full cure | Faster cure with AZ-400-LSW |
Temperature Range | Not fully specified | -180°F to 700°F | Potentially wider range with AZ-400-LSW |
Solids Content | 54-58% by weight | Not specified | May affect application thickness |
VOC Content | 503 g/L (4.2 lb/gal) | Not specified | Environmental/compliance consideration |
Adhesion | Varies by substrate | ASTM D3359A grade not less than 3A | Verification testing recommended |
Outgassing | 0.99% TML, 0.08% CVCM | Extremely low (specific values not provided) | Both suitable for space applications |
Beyond these technical parameters, there are additional practical considerations when transitioning between these materials:
- Base Chemistry: A276 uses polyurethane chemistry while AZ-400-LSW employs a silicone binder
- Application Requirements: AZ-400-LSW does not require controlled temperature and humidity during application, unlike other similar coatings
- Appearance: A276 provides a high-gloss finish while AZ-400-LSW delivers a non-specular finish
- Curing Process: A276 cures by reacting with moisture in the air while AZ-400-LSW follows a different curing mechanism
- Operating Temperature Range: AZ-400-LSW offers a potentially wider temperature range depending on specific application requirements
For many applications, these differences won't impact functionality, but engineers should evaluate specific requirements for each implementation.
Implementation Considerations for Engineers
Transitioning between materials requires careful planning and testing to ensure performance meets specifications. When implementing AZ-400-LSW as an alternative to Aeroglaze A276, several technical considerations should guide your approach.
Primer Requirements: A Significant Advantage
One of the most notable advantages of AZ technologies coatings is their simplified surface preparation requirements. This difference translates directly to production efficiency and cost savings.
For Aeroglaze A276, the technical data sheet specifically states: "For most substrates, apply primer to ensure proper adhesion and performance of the coating." This additional step adds processing time, material costs, and potential quality control points to your production process.
In contrast, AZ-400-LSW can be applied directly to many substrates without a separate primer, significantly streamlining the coating process. This direct application capability:
- Reduces overall processing time by eliminating a complete application/cure cycle
- Lowers material costs through elimination of primer materials
- Simplifies quality control with fewer process steps to monitor
- Decreases potential for contamination between coating layers
For more challenging substrates that do require a primer, MLP-300-AZ primer provides excellent adhesion to difficult materials including:
- Composite materials
- Nickel substrates
- Gold-plated components
- Other traditionally adhesion-resistant surfaces
This flexibility in primer requirements gives engineers more options for streamlined production while still ensuring proper adhesion across diverse material systems.
Additional Implementation Considerations
Beyond primer considerations, surface preparation remains critical:
- Ensure surfaces are thoroughly cleaned to remove all contaminants
- Consider aluminum substrate preparation requirements, particularly for hard anodized aluminum
- Evaluate substrate compatibility for your specific application
Application technique differences matter:
- AZ-400-LSW can be applied using air brush or HVLP systems similar to other silicone paints
- Unlike some thermal control coatings, AZ-400-LSW doesn't require controlled temperature and humidity during application
- Maintain recommended wet film thickness to achieve proper dry film specifications
- Allow adequate curing time of 48-72 hours for full performance development
Performance testing should validate:
- Adhesion meets minimum requirements for your application
- Optical properties match specified parameters
- Environmental resistance meets mission requirements
- Long-term aging effects align with program lifetime needs
Early product testing helps identify any application-specific concerns before full implementation.
Read the guide: Optical and Thermal Coatings in Aerospace
Manufacturing Partner Selection: Critical Success Factor
Finding the right manufacturing partner is essential when navigating material transitions. The complexity of aerospace coatings requires specialized expertise to ensure consistent quality and performance.
A qualified manufacturing partner should offer:
- Deep understanding of aerospace coating specifications
- Experience with both polyurethane and silicone-based coating systems
- Proper equipment and facilities for controlled application
- Quality systems aligned with aerospace requirements (AS9100, ISO 9001)
- Testing capabilities to verify critical performance parameters
- Engineering support for application questions and problem-solving
At Modus Advanced, our team includes engineers with specific expertise in aerospace materials and coating processes. We understand the critical nature of these applications and provide technical guidance throughout material transition processes.
Our vertical integration approach reduces risk by keeping more processes under one roof with consistent quality standards. When lives depend on your innovations, this technical partnership becomes essential to your success.
Planning for Long-Term Material Strategy
While addressing immediate Aeroglaze A276 shortages is urgent, developing a long-term material strategy helps prevent future disruptions. Engineers should consider several approaches to build supply chain resilience.
Consider implementing these strategic approaches:
- Document detailed technical requirements for coatings separated from specific brand names
- Develop and validate multiple material options that meet performance specifications
- Create transitional implementation plans for alternative materials before emergencies occur
- Engage manufacturing partners early in design phases to identify potential material challenges
- Maintain current information on material availability and lead times for critical components
These proactive steps help minimize the impact of future material shortages on critical programs.
Engineering Your Way Through Material Challenges
Material shortages create significant challenges, particularly in aerospace and defense applications where performance requirements are stringent and qualification processes lengthy. AZ-400-LSW provides a viable technical alternative to Aeroglaze A276 for many applications, offering comparable or superior performance in several key parameters.
By understanding the detailed technical characteristics of both materials, engineers can make informed decisions about suitable replacements that maintain critical performance while addressing supply chain challenges. When supported by qualified manufacturing partners, these material transitions can be seamlessly implemented with minimal program disruption.
At Modus Advanced, we understand that one day matters when lives depend on your innovations. Our engineering-first approach helps you navigate material challenges with technical precision and urgency. Contact our team to discuss your specific Aeroglaze A276 replacement needs and explore how AZ-400-LSW might fit your application requirements.