Aeroglaze Z306 Replacements and Alternatives: Non-Conductive Black Coating
April 9, 2025
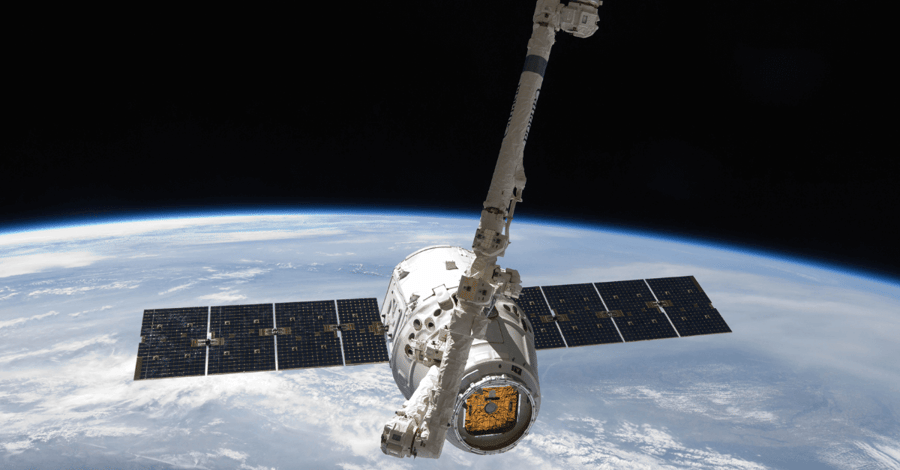
Manufactured with Speed and Precision
The manufacturing capabilities you need and the engineering support you want, all from a single partner.
Submit a DesignKey Points
- Recent supply chain disruptions have made Aeroglaze Z306 difficult to source, creating urgent needs for alternatives in aerospace and defense applications.
- MLS-85-SB Black Thermal Control Paint from AZ Technologies offers comparable optical properties with 0.98 ± 0.01 solar absorptance and 0.91 ± 0.02 thermal emittance.
- The replacement coating provides extended temperature range capabilities from -292°F to 1,112°F, significantly exceeding Z306's operational limits.
- MLS-85-SB offers simpler application requirements without strict temperature and humidity controls, reducing production complexity.
- Flight-proven in space applications, MLS-85-SB has been validated through actual orbital deployment on the Optical Properties Monitor.
The Critical Need for Thermal Control Coatings in Aerospace
Specialized thermal control coatings are essential components in aerospace and defense applications. These coatings manage thermal properties, controlling heat absorption and radiation in environments where temperatures can fluctuate dramatically within minutes. When a critical material like Aeroglaze Z306 faces supply chain disruptions, engineers need reliable alternatives immediately.
Recent events have severely limited the availability of Aeroglaze Z306, a widely used non-conductive black polyurethane coating with extensive aerospace heritage. Z306 has been the go-to solution for thermal control across dozens of flight programs and defense applications, with approvals from major aerospace manufacturers including Boeing, Lockheed Martin, Northrop Grumman, and NASA.
With engineering teams scrambling to identify qualified replacements, understanding viable alternatives becomes mission-critical for maintaining production schedules and performance requirements.
Visit the Resource Center: Advanced Coatings for Aerospace Optics
Understanding Aeroglaze Z306's Critical Properties
Before selecting a replacement material, engineers must understand the key properties that make Aeroglaze Z306 so widely specified. Z306 provides a specific combination of optical, thermal, and mechanical properties that have made it an industry standard.
Z306's primary performance characteristics include:
- High solar absorptivity (>0.95) and normal emissivity (0.90)
- Low outgassing properties (1.0% TML, 0.02% CVCM)
- Operating temperature range from -238°F to 220°F
- Flat black, non-specular finish with low gloss (≤10 at 85°)
- Moisture-curing polyurethane chemistry
- Extensive qualification across aerospace and defense programs
These properties make Z306 ideal for thermal control applications where managing solar absorption and emissivity is critical to maintaining operational temperatures. The coating's established heritage and wide approval across major aerospace manufacturers has made its sudden limited availability particularly challenging.
Introducing MLS-85-SB: A Viable Replacement Solution
MLS-85-SB Black Thermal Control Paint from AZ Technologies offers aerospace engineers a qualified alternative to Aeroglaze Z306. This specialized silicone-based coating provides comparable optical properties while offering several distinctive advantages for critical applications.
Developed specifically for aerospace applications, MLS-85-SB has flight heritage and proven performance in the space environment. The coating was deployed on the Optical Properties Monitor (OPM) and successfully returned after nine months in orbit, demonstrating its durability in actual space conditions.
This real-world validation provides engineers with confidence that MLS-85-SB can perform reliably in the most demanding environments, from ground testing through operational deployment.
Comparative Performance Analysis
When evaluating MLS-85-SB as a replacement for Aeroglaze Z306, several performance characteristics stand out as particularly relevant for engineering applications. Understanding these comparisons helps engineers make informed decisions when qualifying alternative materials.
Side-by-Side Property Comparison
The following table provides a direct comparison of key properties between Aeroglaze Z306 and MLS-85-SB:
Property | Aeroglaze Z306 | MLS-85-SB |
Optical Properties | ||
Solar Absorptance (αs) | >0.95 | 0.98 ± 0.01 |
Thermal Emittance (εt) | 0.90 | 0.91 ± 0.02 |
Appearance | Flat black | Non-specular optical black |
Performance | ||
Temperature Range | -238°F to 220°F<br>(-150°C to 104°C) | -292°F to 1,112°F<br>(-180°C to 600°C) |
Outgassing | 1.0% TML, 0.02% CVCM | Low (unspecified values) |
Application | ||
Binder Chemistry | Polyurethane | Silicone |
Cure Mechanism | Moisture cure | Heat cure |
Cure Time | 12 hours handling<br>7 days full properties | 48-72 hours full cure |
Environmental Control | Strict temp/humidity<br>requirements | Minimal requirements |
Recommended Thickness | 1.5-2.0 mils | 3.0 +1.0, -1.5 mils |
Validation | ||
Flight Heritage | Extensive | Flown on Optical Properties<br>Monitor (9 months) |
Industry Approvals | Multiple OEMs and<br>defense contractors | Limited documentation |
Space Environment | Validated | Validated for LEO and GEO |
Adhesion | Not specified | Not less than 3A<br>(ASTM D3359A) |
This comprehensive comparison shows that while both materials serve similar purposes, they offer different advantages depending on specific application requirements.
Optical Properties
MLS-85-SB offers exceptional optical performance with:
- Solar absorptance (αs): 0.98 ± 0.01 at ≥1.5 mils thickness (compared to >0.95 for Z306)
- Thermal emittance (εt): 0.91 ± 0.02 (compared to 0.90 for Z306)
- Non-specular optical black finish similar to Z306's flat black appearance
These values demonstrate that MLS-85-SB provides equivalent or slightly superior optical properties compared to Aeroglaze Z306, ensuring consistent thermal performance in spacecraft and optical applications.
Temperature Range
One significant advantage of MLS-85-SB is its substantially broader temperature capability:
- MLS-85-SB operating range: -292°F to 1,112°F (-180°C to 600°C)
- Aeroglaze Z306 operating range: -238°F to 220°F (-150°C to 104°C)
The extended temperature range of MLS-85-SB provides engineers with greater design flexibility, particularly for applications that may experience more extreme thermal environments or thermal cycling.
Application Process Advantages
MLS-85-SB offers several application advantages over Aeroglaze Z306:
- Doesn't require strictly controlled temperature and humidity during application
- Simpler application process with less sensitivity to environmental conditions
- Full cure in 48-72 hours at room temperature
- Can be applied by brush or spray methods
- Excellent adhesion (not less than 3A per ASTM D3359A)
These processing advantages can significantly simplify production operations, especially when manufacturing environments cannot maintain the narrow temperature and humidity ranges required for optimal Z306 application.
Read the guide: Optical and Thermal Coatings in Aerospace
Implementation Considerations for Engineering Teams
Transitioning from Aeroglaze Z306 to MLS-85-SB requires careful planning and validation. Engineering teams should consider several factors when implementing this alternative coating in their applications.
Primer Requirements: A Significant Advantage
One of the most notable advantages of AZ technologies coatings is their simplified surface preparation requirements. This difference translates directly to production efficiency and cost savings.
For Aeroglaze products, for most substrates, it is required to apply primer to ensure proper adhesion and performance of the coating. This additional step adds processing time, material costs, and potential quality control points to your production process.
In contrast, AZ Technologies coatings can be applied directly to many substrates without a separate primer, significantly streamlining the coating process. This direct application capability:
- Reduces overall processing time by eliminating a complete application/cure cycle
- Lowers material costs through elimination of primer materials
- Simplifies quality control with fewer process steps to monitor
- Decreases potential for contamination between coating layers
For more challenging substrates that do require a primer, MLP-300-AZ primer provides excellent adhesion to difficult materials including:
- Composite materials
- Nickel substrates
- Gold-plated components
- Other traditionally adhesion-resistant surfaces
This flexibility in primer requirements gives engineers more options for streamlined production while still ensuring proper adhesion across diverse material systems.
Qualification Testing
Before full implementation, teams should conduct appropriate qualification testing including:
- Adhesion testing on relevant substrate materials
- Optical property verification post-application
- Environmental testing under expected operational conditions
- Compatibility assessment with adjacent materials and systems
- Outgassing verification if required for sensitive applications
Since MLS-85-SB uses a silicone binder rather than Z306's polyurethane chemistry, engineers should verify compatibility with other materials in their assembly to prevent any potential silicone contamination issues.
Application Specifications
MLS-85-SB's recommended application parameters include:
- Nominal dry thickness: 3.0 +1.0, -1.5 mils over 85% of the coated area
- Full cure time: 48-72 hours at room temperature
- Surface preparation similar to other high-performance aerospace coatings
- Can be applied using conventional spray equipment
Engineers should note that while brush application is possible, it may result in optical properties outside the specified ranges. For critical thermal control applications, spray application is recommended to ensure consistent performance.
Environmental Considerations
MLS-85-SB has been specifically tested for space environment resistance:
- Demonstrated resistance to atomic oxygen (AO) in Low Earth Orbit (LEO)
- Suitable for both Low Earth Orbit and Geosynchronous Earth Orbit applications
- Excellent performance in vacuum systems and optical instruments
- Successfully flown and returned on the Optical Properties Monitor
For applications with unique environmental exposure, additional testing may be warranted to validate performance under specific conditions.
Quality Assurance for Critical Applications
Maintaining strict quality standards is essential when implementing alternative materials in aerospace and defense applications. Engineers should establish appropriate inspection and validation protocols when transitioning to MLS-85-SB.
Key quality considerations include:
- Verification of coating thickness using appropriate measurement techniques
- Visual inspection for consistent appearance and coverage
- Optical property testing to confirm absorptance and emittance values
- Documentation of application parameters for traceability
- Adhesion testing to ensure proper surface preparation and bonding
Proper documentation of these quality parameters helps ensure consistent performance and supports future qualification or certification requirements.
Why Choose Modus Advanced for Your Coating Needs
At Modus Advanced, we understand the critical nature of thermal control coatings in aerospace and defense applications. When supply chain disruptions threaten program schedules and performance, our engineering team works directly with customers to identify and implement qualified alternatives.
Our vertically integrated approach to manufacturing allows us to support the entire coating application process, from surface preparation through final inspection and testing. With AS9100 and ISO 9001 certifications, our quality management system ensures consistent results for even the most demanding applications.
Our engineering team — making up more than 10% of our staff — provides expert guidance on material selection, application processes, and performance testing to ensure successful implementation of alternative materials like MLS-85-SB. We understand that in aerospace and defense applications, failure is not an option, which is why we maintain the highest standards across all our manufacturing processes.
When program success depends on finding qualified replacements for critical materials like Aeroglaze Z306, Modus Advanced delivers solutions that keep production moving without compromising performance or reliability.
Final Thoughts
The limited availability of Aeroglaze Z306 presents significant challenges for aerospace and defense manufacturers, but viable alternatives like MLS-85-SB offer comparable performance with several potential advantages. By understanding the key properties, application considerations, and quality requirements, engineering teams can successfully transition to this alternative coating while maintaining the critical thermal control performance their applications demand.
At Modus Advanced, we're committed to helping our partners navigate material supply challenges with engineering expertise, quality manufacturing, and a deep understanding of critical aerospace requirements. Contact our engineering team today to discuss your specific thermal coating requirements and learn how we can support your transition to qualified alternative materials.