Aeroglaze Z307 Replacements and Alternatives: Conductive Black Coating
April 9, 2025
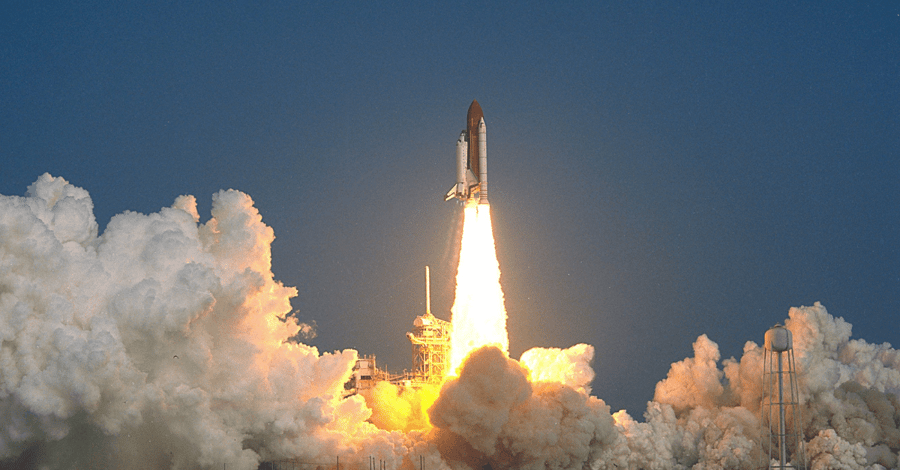
Manufactured with Speed and Precision
The manufacturing capabilities you need and the engineering support you want, all from a single partner.
Submit a DesignKey Points
- Due to a recent natural disaster, Aeroglaze Z307 coating products are currently unavailable to the market, creating an urgent need for alternatives.
- AZ Technologies MLS-85-SB-C Black Thermal Control and Electrically Conductive Paint/Coating offers a viable replacement with comparable optical and thermal properties.
- MLS-85-SB-C provides excellent electrical conductivity with a nominal surface resistivity of ~105 Ω/sq, making it suitable for static dissipation applications.
- Unlike Z307, MLS-85-SB-C has significantly lower outgassing and doesn't require controlled temperature and humidity during application.
- The replacement coating is suitable for both space and terrestrial applications with an impressive temperature range from -180°F to 600°F.
Engineers in aerospace, defense, and optical systems industries are facing a significant challenge. A recent natural disaster has disrupted the supply chain for Aeroglaze Z307, a widely used conductive black coating critical for many specialized applications.
This disruption has left many projects in limbo and engineers searching for alternatives that can meet their exacting specifications without compromising performance or reliability.
At Modus Advanced, we understand that finding the right material replacement isn't just about maintaining schedules—it's about ensuring the integrity and functionality of mission-critical systems. When coating materials impact thermal control, optical properties, and electrical conductivity, substitutions cannot be made lightly.
This article examines how AZ Technologies MLS-85-SB-C offers a viable alternative to Aeroglaze Z307, providing engineers with a solution during this supply chain disruption.
Understanding Aeroglaze Z307 and Its Applications
Aeroglaze Z307 has been an industry standard for years, particularly in applications requiring specific optical and electrical properties. Before discussing alternatives, it's important to understand what makes this coating so valuable to engineers.
Key Properties of Aeroglaze Z307
Aeroglaze Z307 is a flat black polyurethane coating designed for use in applications requiring high absorptivity and low reflectance. It provides a combination of properties that make it particularly valuable:
- Low reflectance in both visible and infrared spectrums
- Electrical conductivity for static dissipation
- Good adhesion to various substrates
- Durability in harsh environments
These properties have made Z307 a go-to choice for optical systems, spacecraft components, and sensitive electronic equipment where controlling light reflection and static buildup is critical.
Visit the Resource Center: Advanced Coatings for Aerospace Optics
Common Applications
Engineers typically specify Aeroglaze Z307 for applications including:
- Space vehicle interior and exterior components
- Optical baffles and light shields
- Instrumentation requiring low-reflectance surfaces
- Static-sensitive equipment housings
- Thermal control surfaces
With the current supply disruption, finding a suitable replacement that can match these performance characteristics has become an urgent priority for many engineering teams.
Introducing MLS-85-SB-C: A Viable Alternative
AZ Technologies MLS-85-SB-C offers a compelling alternative to Aeroglaze Z307, providing comparable and in some cases superior performance across critical parameters. This silicone-based conductive coating has been developed specifically for applications requiring excellent optical properties combined with electrical conductivity.
Material Composition and Key Properties
MLS-85-SB-C consists of a highly specialized pigment with a silicone binder, creating a flexible coating that can be applied to complex surfaces. This composition delivers several important performance characteristics:
- Nominal surface resistivity of approximately 105 Ω/sq
- Excellent thermal emittance (ε_t) of 0.91 ± 0.02
- Superior solar absorptance (α_s) of 0.98 ± 0.01 at ≥ 1.5 mils thickness
- Impressive temperature range capability from -180°F to 600°F
- Non-specular optical black appearance
The coating forms a bendable conductive layer that maintains its properties across a wide range of environmental conditions, making it suitable for both space and terrestrial applications.
Application Process Advantages
One significant advantage of MLS-85-SB-C over Aeroglaze Z307 is its simplified application process. MLS-85-SB-C features:
- Low outgassing properties
- No requirement for controlled temperature and humidity during application
- Ability to be applied over complex surfaces with relative ease
- Option for spray or brush application (though optical properties may vary slightly with brush application)
- Full cure within 48 to 72 hours
These application advantages can translate to reduced processing time and costs while still achieving the required performance specifications.
Aeroglaze Z307 vs. MLS-85-SB-C Comparison Table
Property | Aeroglaze Z307 | MLS-85-SB-C | Notes |
Base Material | Polyurethane | Silicone | MLS-85-SB-C's silicone base offers better temperature resistance |
Color/Appearance | Flat black | Nonspecular optical black | Both provide low reflectance black finish |
Solar Absorptance (α_s) | 0.94 - 0.97 | 0.98 ± 0.01 | MLS-85-SB-C has slightly higher solar absorptance |
Thermal Emittance (ε_t) | 0.89 - 0.91 | 0.91 ± 0.02 | Similar thermal emittance properties |
Surface Resistivity | ≤ 5 x 10^5 Ω/sq | ~10^5 Ω/sq | Comparable electrical conductivity |
Temperature Range | -320°F to 230°F | -180°F to 600°F | MLS-85-SB-C offers significantly higher upper temperature limit |
Application Requirements | Controlled temperature and humidity required | No controlled temperature or humidity required | MLS-85-SB-C offers simpler application process |
Outgassing | Higher outgassing | Low outgassing | MLS-85-SB-C is advantageous for vacuum and space applications |
Cure Time | 7 days at 77°F for full cure | 48-72 hours for full cure | MLS-85-SB-C offers faster processing time |
Adhesion | Good adhesion to various substrates | ASTM D3359A Grade not less than 3A | Both offer good adhesion properties |
Atomic Oxygen Resistance | Limited | Resistant to AO flux in LEO | MLS-85-SB-C has better space environment durability |
Application Method | Spray or brush | Spray recommended (brush possible) | Similar application flexibility |
Recommended Thickness | 1.0 - 2.0 mils | 3.0+1.0, -1.5 mils | MLS-85-SB-C typically applied slightly thicker |
Space Flight Heritage | Extensive | Equivalent formulation (MLS-85-SB) flown on OPM mission | Both have space flight validation |
Note: This comparison is based on available technical data. Engineers should verify specifications for their specific application requirements.
Comparative Analysis: MLS-85-SB-C vs. Aeroglaze Z307
When evaluating MLS-85-SB-C as a replacement for Aeroglaze Z307, engineers need to understand how the materials compare across key performance metrics. This analysis helps determine suitability for specific applications and identify any potential trade-offs.
Optical and Thermal Properties
MLS-85-SB-C offers excellent optical properties that compare favorably with Aeroglaze Z307:
- MLS-85-SB-C's solar absorptance of 0.98 ± 0.01 provides exceptional light absorption capabilities
- Its thermal emittance of 0.91 ± 0.02 ensures effective thermal radiation
- The non-specular optical black finish creates minimal light reflection
These properties make MLS-85-SB-C suitable for optical baffle systems, thermal control surfaces, and other applications where controlling light reflection and thermal properties is critical.
Electrical Conductivity and Static Control
For applications requiring static dissipation, MLS-85-SB-C provides reliable electrical conductivity:
- Surface resistivity of approximately 105 Ω/sq allows for effective static charge dissipation
- Consistent conductivity across operating temperature ranges
- Maintained electrical properties even with mechanical flexing
This conductivity makes MLS-85-SB-C appropriate for protecting sensitive electronic components from static discharge and for applications requiring grounding capabilities.
Read the guide: Optical and Thermal Coatings in Aerospace
Environmental Durability
MLS-85-SB-C has demonstrated excellent durability in challenging environments:
- Resistance to Atomic Oxygen (AO) flux makes it suitable for Low Earth Orbit (LEO) applications
- Excellent performance in vacuum environments
- Wide temperature range tolerance from -180°F to 600°F
- Good adhesion properties with an ASTM D3359A adhesion grade of not less than 3A
The coating's proven performance in space environments provides confidence in its long-term reliability, with heritage data available from the Optical Properties Monitor (OPM) mission.
Application Guidelines for MLS-85-SB-C
Successfully implementing MLS-85-SB-C as a replacement for Aeroglaze Z307 requires understanding proper application techniques to achieve optimal performance. The following guidelines help ensure successful coating application.
Surface Preparation
Proper surface preparation is essential for achieving good adhesion and uniform coating properties:
- Ensure surfaces are clean, dry, and free from contaminants
- Apply appropriate primer if recommended for the substrate material
- Consider light abrasion of surfaces for improved adhesion
- Verify surface temperature is within recommended application range
Taking the time to properly prepare surfaces will help ensure the coating's performance meets specifications.
Application Methods
MLS-85-SB-C can be applied using various techniques:
- Spray application is preferred for achieving consistent optical properties
- Brush application is possible but may affect solar absorptance and thermal emittance values
- Apply to achieve a nominal dry thickness of 3.0+1.0, -1.5 mils over 85% of the coated area
- Consider multiple thin coats rather than a single thick application
For critical optical applications, spray application typically provides the most consistent results.
Curing and Testing
After application, proper curing and verification are important steps:
- Allow 48 to 72 hours for full cure at room temperature
- Verify coating thickness meets specifications
- Consider adhesion testing to verify proper bonding to substrate
- For critical applications, verify optical properties meet requirements
Proper curing ensures the coating achieves its full performance potential and long-term durability.
Primer Requirements: A Significant Advantage
One of the most notable advantages of AZ technologies coatings is their simplified surface preparation requirements. This difference translates directly to production efficiency and cost savings.
For Aeroglaze products, for most substrates, it is required to apply primer to ensure proper adhesion and performance of the coating. This additional step adds processing time, material costs, and potential quality control points to your production process.
In contrast, AZ Technologies coatings can be applied directly to many substrates without a separate primer, significantly streamlining the coating process. This direct application capability:
- Reduces overall processing time by eliminating a complete application/cure cycle
- Lowers material costs through elimination of primer materials
- Simplifies quality control with fewer process steps to monitor
- Decreases potential for contamination between coating layers
For more challenging substrates that do require a primer, MLP-300-AZ primer provides excellent adhesion to difficult materials including:
- Composite materials
- Nickel substrates
- Gold-plated components
- Other traditionally adhesion-resistant surfaces
This flexibility in primer requirements gives engineers more options for streamlined production while still ensuring proper adhesion across diverse material systems.
Space Flight Heritage and Validation
For aerospace applications, flight heritage data provides valuable confidence in a material's performance. MLS-85-SB-C has a pedigree that helps validate its suitability for space applications.
Optical Properties Monitor Mission
MLS-85-SB-C has equivalent properties to MLS-85-SB, which has proven space flight heritage:
- MLS-85-SB was flown on the Optical Properties Monitor (OPM)
- The material was returned after 9 months of exposure in the space environment
- Pre- and post-flight reflectance data validated its performance stability
This flight heritage provides engineers with valuable validation of the material's performance in actual space conditions.
Testing Considerations for Specific Applications
While MLS-85-SB-C has demonstrated excellent performance, engineers should consider additional validation for their specific applications:
- MLS-85-SB-C has had limited Atomic Oxygen (AO) testing
- Evaluation of coating performance for particular applications is recommended
- Consider testing on representative substrates under application-specific conditions
This testing approach ensures the material will meet all requirements for your specific implementation.
Final Thoughts
As engineers navigate the supply chain disruption of Aeroglaze Z307, AZ Technologies MLS-85-SB-C offers a viable alternative with comparable and in some cases superior performance characteristics. Its excellent optical properties, electrical conductivity, and environmental durability make it suitable for many of the same applications, while its simplified application process offers potential advantages.
At Modus Advanced, we understand the critical nature of material selections in aerospace, defense, and optical systems. Our team of engineers can help evaluate MLS-85-SB-C for your specific application and ensure a smooth transition from Aeroglaze Z307. With our expertise in advanced materials and manufacturing processes, we can support your engineering team through material selection, testing, and implementation.
Because when mission-critical applications depend on the right materials, one day matters. Contact our engineering team today to discuss how MLS-85-SB-C can meet your conductive coating needs during this supply chain disruption.