Idea to Ignition: Discontinued Gore Materials
April 22, 2021
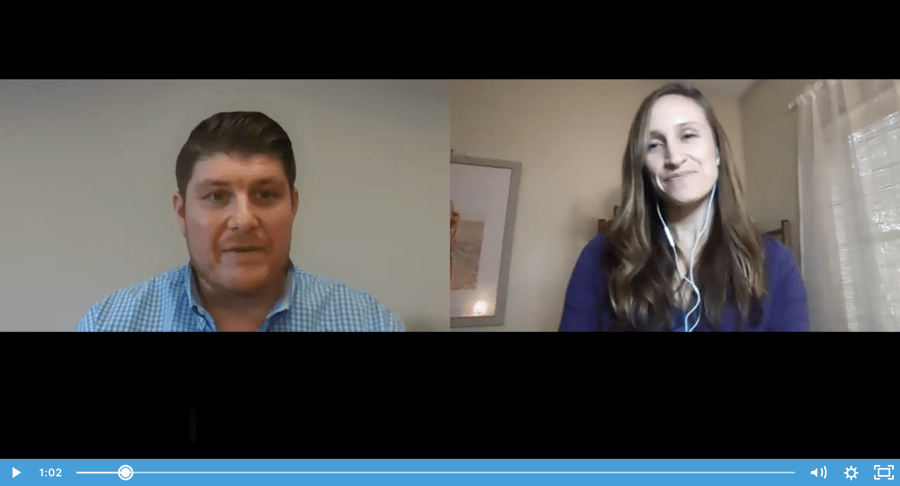
Manufactured with Speed and Precision
The manufacturing capabilities you need and the engineering support you want, all from a single partner.
Submit a Design
This episode features a discussion with:
- Dominic Testo
- Role: Business Development Manager, Specialty Silicone Products
- Drinking: Green tea (decaf)
- Stacy Willis
- Role: Marketing at Modus Advanced, Inc.
- Drinking: Herbal tea
The team discusses the discontinuation of Gore EMI materials and what you can do about it. Read a summary of their conversation below.
Which Gore Materials Have Been Discontinued?
Gore electromagnetic (EMI) shielding materials are rubber gasketing materials that shield from electromagnetic interference (EMI) and radio frequency interference (RFI).
There’s a simple way to explain what these materials do: if you put a standard, non-shielding rubber gasket around a metal box with your cellphone inside of it, you could still call the phone and make it ring inside the box. If you covered that same box with an EMI shielding gasket, the call wouldn’t go through. Shielding materials are filled with a conductive metal or particle, making the gaskets both environmental and effective EMI-RFI seals.
In electronics for military and defense applications, these materials are critically important. A few of the most popular of these materials were recently discontinued.
Gore announced in November of 2019 that they were going to discontinue their EMI shielding materials. The following three products were discontinued:
- GORE GS2100
- GORE GS5200
- GORE GS8000
The last orders for these products were due by April 2020, which was right at the beginning of the COVID-19 pandemic. Because of unprecedented world events and the long life cycles of these products, many people do not yet realize that Gore discontinued these three products.
What Do the Gore EMI Shielding Material Discontinuations Mean?
In the world of specialty materials, die-cut gaskets and custom parts, people don’t change parts and materials suppliers very often. The testing and onboarding of a new supplier takes a lot of time, effort and money. Generally, a supplier switch only happens for one of the following reasons:
- Problems with product quality
- Big price increases
- Service problems, such as long wait times to get materials
Even in the face of any of those problems, they have to be pretty enormous to convince someone in this industry to switch suppliers. The discontinuation of the Gore EMI shielding materials forced a lot of industry players to make the switch when they otherwise wouldn’t have done so.
The engineering and procurement folks at firms around the world are left with no choice but to replace the products.
How to Find a Gore Material Replacement
To meet the needs of those who were left without a solid replacement after the Gore material discontinuation, Specialty Silicone Products (SSP) set out to offer a perfect replacement that would meet all the buyers’ requirements and specifications. Here’s how they did it.
Selecting the Perfect Gore Shielding Material Replacement
SSP worked with Modus Advanced, Inc., to evaluate the possible products that could replace the discontinued Gore materials. They identified some materials that have been working well as direct replacement for the discontinued items.
The SSP team put themselves in the shoes of a design engineer or other stakeholder who has to change out a critical material like an EMI shielding gasket. It’s nerve-wracking — the part might be on a weapons system, communications system or aircraft, so the material has to be the exact right replacement.
To address this concern, SSP selected a product that has been on the market for years and performed testing to verify its usefulness as a replacement for the discontinued Gore materials. Instead of building an entirely new product, working with an older product gives volumes of test data and years of real-life performance to look to, which builds trust with the market. In this case, the product passed the rigorous new tests.
Meeting OEMs’ Needs
To provide a viable replacement, SSP evaluated the unique needs of OEMs that had been using the discontinued Gore EMI shield gaskets. One of the things many OEMs liked about the Gore products was that they were low outgassing materials — a feature that is particularly important in space and satellite applications. SSP tested its existing materials using the ASTM E595 method, and they passed the low outgassing standard. That was the first hurdle.
Then, SSP wanted to provide a replacement for the Gore materials that had UL94 V0 certification. The existing products had passed the UL94 V1 standard, so SSP guessed its products would pass V0. They were right.
What was the result of all this testing and modification with Modus Advanced, Inc.? OEMs are saying they are happy with the replacement — something they can trust after years on the market rather than something that SSP and Modus Advanced, Inc., have only been making for six months.
Get the Best in EMI Shielding Materials
In partnership with SSP, Modus Advanced, Inc., works hard every day to provide the best replacements for the discontinued Gore products and the best silicone materials in general. When our clients need a product, we give them the best on the market.
To speak with the team or learn more, contact us today.
Video Transcript Starts Below:
Stacy:
Welcome to today's episode of Idea to Ignition. Manufacturing might be a big subject, but that doesn't mean people can't learn a lot in a short amount of time. We know people are busy, but they are hungry for better ways to bring their product ideas to life with the help of key manufacturing partners. As such, we regularly host 15-minute coffee chats with innovators and thought leaders in the manufacturing and material space to provide big insights in a bite-sized format. I'm Stacy with Modus' marketing team. And today we're here with Dominic Testo, business development manager at Specialty Silicon Products. Hi, Dominic. Can you tell us a little bit about yourself?
Dominic Testo:
Hey, Stacy. Sure can. And first of all, thanks for having me.
Stacy:
Of course.
Dominic Testo:
I really enjoy working with Modus and I commend you guys for putting together the coffee chats like this in the Ideas to Ignition, so I really appreciate you having me. Yeah, I've been with Specialty Silicone Products in several different sales roles from inside sales, account manager up to the business development manager for about 11 years now. And I specialize in some of our more advanced materials for aerospace and defense and in particular, some of the stuff we'll talk about today and the EMI RFI shielding world.
Stacy:
Great. Thank you so much. Well, this is a coffee chat, so I always like to check in and see what everybody's drinking. I myself am a big herbal tea fan because it's too late in the day for coffee. Otherwise, I won't sleep. How about yourself?
Dominic Testo:
I'm actually doing the same thing. I've got my Yeti filled up with some green tea. And it is decaffeinated because I have had probably four coffees-
Stacy:
Oh boy.
Dominic Testo:
... already today. So, I needed to slow it down for our chat.
Stacy:
Yeah. I learned not to do coffee on these chats because then I talk too fast to even be understandable.
Dominic Testo:
Yeah, exactly. Exactly.
Stacy:
Well, today we're here to talk about the discontinuation of some Gore shielding materials and what you can do about it. So to start with, what are the materials that have been discontinued and what does that mean for people who use them?
Dominic Testo:
Yeah. No, it's an interesting topic. So the Gore shield materials are basically in a nutshell an EMI RFI gas getting products. So we had to break that down and what it does. My favorite way to explain it is if you took your cell phone and you put it in a metal box and that box had a standard rubber gasket around it that wasn't a shielding material, you could close that box, call the cell phone, and the RF would actually go through that gasket into your phone and your phone would ring. If you took the material similar to our materials or the Gore material, it would not. And the reason for that is they fill the material with a conductive metal or particle basically making it a dual environmental seal and EMI shield. So as you can see in the world of military and defense electronics, they're pretty important products, even though they're just a gasket.
Stacy:
And it sounds like they're highly specialized as well, right? So hard to find potentially replacements for.
Dominic Testo:
They are. So the particular materials that were discontinued, I believe, were the GS 2100 and GS 5200. There was three total materials. We're only talking about two today because those are the two that we think we can help folks out with.
Stacy:
Gotcha.
Dominic Testo:
November of 2019 is actually when they announced the end of life of the product. And then the last orders had to be in in April of 2020. So if you can imagine what was going on in April of 2020, these replacement materials probably [crosstalk 00:03:34].
Stacy:
Could I not remember?
Dominic Testo:
Yeah, I know. I know.
Stacy:
[inaudible 00:03:37] just pretend.
Dominic Testo:
But I think it's important because it was a crazy time and it took a little while for people to realize that the products were discontinued. So I think we can help some people today go down the path of how to select a replacement because it's not always easy.
Stacy:
Yeah. And I imagine with different product life cycles as well. I mean, it could be quite a while before you need to reorder or rebuild something that you had maybe used in the past.
Dominic Testo:
Sure. For sure.
Stacy:
So, there's plenty of people probably just figuring it out today.
Dominic Testo:
There absolutely is. And I mean, that's a good segue. We can take a step back. I mean, in our world of specialty materials and dye cut gaskets and custom parts, the main three reasons that people typically would move from a supplier in our world, number one would be the quality of the product. If there was major quality issues over time, that might be something where you would look to change suppliers.
Dominic Testo:
But even with that, you really have to be going through a lot of pain to go through all the testing, the onboarding of a new supplier. There's a lot of pain in switching a product like this. So quality would be one. The next might be price. But when you think about these materials as well, even if the price went up, sometimes these are super special gaskets. So they may be a hundred dollar gasket, which sounds like, "Oh my gosh, that's a lot of money." But it also might be on a billion dollar satellite. So a price increase-
Dominic Testo:
Yeah. So a price increase on the gasket might not really get you to move to a new supplier. And then, the third most common would be service or lead times it's taking a long time to get it. Again, you have to weigh, do we wait a little longer or do we go through the pain of switching? This situation is a lot different because the market basically decided that, "Hey, we don't have this anymore." So there's no choice in terms of the engineering and procurement folks to go replace the product. So I think we can go through some steps on how to replace these products with the most cost efficient unlimited risk path in mind.
Stacy:
Yeah. First and foremost, from a design perspective, to be able to swap out a material that may involve redesigned conversations, which becomes much bigger problem. In this particular instance, do you see that needing to happen? Is it something where it's just a straight rip and replace? What does the design phase look like to make sure that you can replace the material with the ones that SSP offers?
Dominic Testo:
Yeah, so that's a very common question. And what we do is we offer the materials in so many different ways and we work so closely with folks like Modus that we try to take our standard run of materials whether it be one hour 10 different products, evaluate the application, evaluate our different materials and then evaluate Modus' different ways to cut and make the materials custom.
Dominic Testo:
So, we really try to make sure you don't have to change your enclosure or your housing, which is where most of these gaskets are. So there's only been maybe one instance out of many, many, many situations where there was a design. And that was a customer who was down the road of changing their design anyway. But no, we have some materials we think we can get to work as a direct replacement as long as we're strategic about it.
Stacy:
Awesome. Well, then let's talk a little bit about the how that you were leading up to.
Dominic Testo:
Sure. So here's the very important thing. If we put ourselves in the shoes of a design engineer or somebody who has to make a decision to change out a critical material in a very critical application, that can be a little nerve-wracking because it might be a weapon system. It might be a communication system. It might be something that is on an aircraft that's in flight. So you really need to make sure that the material is the correct replacement.
Dominic Testo:
So one of the things we did to build some trust with the market is we like to make sure we explain that we didn't develop a product to offer as a replacement of the discontinued material. We took a current product we've been making for years and years and added extra testing to the product. So we knew we were very close. And so, one particular important attribute of some of these material is that they were low outgassing material. So, specifically ASTM 595, which is a very important specification for anybody working with satellite or space.
Dominic Testo:
So we knew our materials probably had a good chance of passing. We invested in the testing. We had our standard formulation tested and it passed the testing. So that was the first hurdle. And then the second hurdle is that we know that there's a lot of folks who were using this material because of its ULV-0 certification. So we had a material that we've been making, developed. I want to say, actually, maybe even in the '90s or early 2000s for a customer in Europe that we have a lot of data on and a lot of batches we've made over the years that we actually specify to UL94 V-1, which is just a little bit different test than the V-0. We set for the V-0. We have that test data back and we pass that.
Dominic Testo:
So, we basically took what we thought would work and modified it. We also took that material and we modified it to lower the durometer or the shore A. One of the attributes about the Gore material, the GS 2100 is that folks really liked the very soft compressible material. A lot of times that gives you a little bit of room in terms of your hand design. So with all that said, basically, we took products that we already make. We modify them slightly or we edit extra testing to replace the two materials. So here's the competence standpoint. Our customers seem to be very happy with that instead of, "Hey, it's been new. We've been making it for six months. [inaudible 00:09:54].”
Stacy:
Yeah. That's a big leap of faith right there.
Dominic Testo:
Yeah. It's very important that we communicate that. And one thing that's powerful when Modus is working with the OEMs is the transfer of communication from the material manufacturer through Modus down to the OEM, because we want to make sure all the communication gets there and the folks there do a great job to get all the information and then we can work together to decide, "Hey, this is, I think, the material you should go with.”
Stacy:
And I mean, it really helps to that relationship from the Modus and during the design for manufacturing review, understanding directly from the material supplier what different processes are going to do in terms of effecting the tolerance levels, how they fit in with the design. And so, it's definitely incredibly important to us to have that level of communication with you as well, particularly in those instances where a customer's having to take a little bit of a leap of faith and try out a new material.
Dominic Testo:
Well, yeah. A company like Modus, I would guess cuts maybe a thousand different types of material. When you talk about all the different raw materials out there, all the different thicknesses and the hardnesses, just silicone alone there's probably a hundred types of silicone that folks work with. And then you have all the other rubbers and the other plastics and materials that Modus works with. So it's very hard to be an expert in just one specialty niche material because you just don't have somebody at the time to do it. So that's why we leverage our relationship and Modus vice versa to make sure we have all the information when you're working with some of these folks. And so, it is very hard for the fabricator to know everything there is to know. So they really lean on us and we appreciate the trust.
Stacy:
Yeah. Do you have any interesting insights or quick wins that have happened since that fateful day in April where the discontinuation happened and you guys have been starting work with people in replacing that material? Any interesting insights?
Dominic Testo:
Yeah, we sure do. So I'll give an overhead, not customer-specific-
Stacy:
Of course.
Dominic Testo:
... in terms of application-specific. But when we received inquiries very early on, they were coming in asking us to basically meet every single specification that was on the Gore material and we had to explain that. We have something that we think is very close. We never say it's the same exact thing because it can't be. And so, those folks went back out to the market. They ended up really circling back around saying that you've got the closest product, right?
Dominic Testo:
And so, one good example of how we work with people on this is we've had someone come to us and say, "We really want this material. Here's what we were using. Can you replace it?" And so, as we talked to these folks, so why are you using this material? And this particular application was a satellite application. And they were specifically using it because it was an EMI shield and also provided outgassing data, showing that it was passing the specifications.
Dominic Testo:
So, when you go down, especially, well, is the ULV-0 a very important attribute to you? Well, no, it's not. Okay. So here's now four or five other products that we have in our lineup that are less expensive, more readily available for the way you want to take it in this molded part. And we were able to just connect the dots to show you don't absolutely have to have the exact same product. Let's talk about what's important and that particular customer is now a happy customer and placing orders.
Stacy:
And that sounds like they may have even improved based on what they had before to what they have now.
Dominic Testo:
Yeah. From a cost standpoint, as long as we can hit all the attributes that they're looking for, we might suggest a different material. If we need to go with what we call the offset, we'll do that too. But we like to work with everybody to make sure that they are getting the best product possible for the best price.
Stacy:
It's always nice to hear that. So, that's who we tend to partner with are those people that like to be more consultative in their approach that really want to be there to find you the best solution and not just sell whatever they can sell.
Dominic Testo:
Absolutely. Absolutely.
Dominic Testo:
We need the help from the OEMs as well, right?
Stacy:
Great. Well, this has been super helpful. Following up on this, I'll definitely make sure we include some links to some resources that we have about this.
Dominic Testo:
Great.
Stacy:
And some contact information for where you can reach out should you be interested in replacing one of these materials that has been discontinued. Thank you so much for joining us today. And we'll see you on our next Idea to Ignition. Bye.
Dominic Testo:
Thank you, Stacy. Bye-bye.