Is Die Cutting the Right Fit for Your Custom Gasket?
February 11, 2021
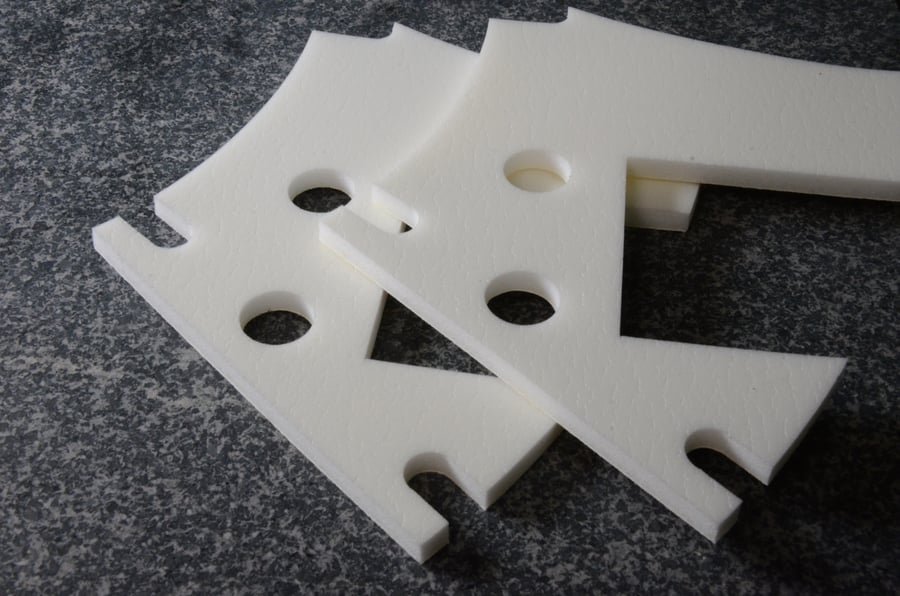
Manufactured with Speed and Precision
The manufacturing capabilities you need and the engineering support you want, all from a single partner.
Submit a DesignThis article is a member of our series on different manufacturing processes for custom gaskets. It follows the same structure, and includes similar introductory text, to ensure that whether you read a single article in the series or multiple, you’ll have all the information you need.
Choosing a Process
Choosing the right manufacturing process for producing your custom gasket is as much of an art as it is a science. The right manufacturing partner should be able to review your design, understand your needs for volume, and help you decide the appropriate method for production.
As much as we all wish it was an incredibly simple decision to determine the right manufacturing process fit for your needs, there are a ton of considerations that go into the decision. Any manufacturing partner worth working with long-term should have a very thorough Design for Manufacturing (DFM) process to help work through this with you.
Choosing the right manufacturing process is about balancing all of the following factors:
- Lead time
- Cost
- Volume of parts
- Quality and/or tolerance levels
- Material selection
-- Article Continues Below --
Learn how to avoid these common gasket design mistakes in our free guide!
Often making a decision that improves one factor can have an affect on the other factors, so understanding which process to choose ultimately comes down to prioritization. Deeply understanding how to achieve the requirements of your design as well as understanding what matters to you outside of the design itself leads to the right choice. And that is what the DFM process is all about.
This article breaks down some of the considerations that would lead to choosing die cutting as the correct manufacturing process. It is meant to provide some general guidelines, but is by no means exhaustive, nor is it a replacement for undergoing the DFM process on a specific design.
How it Works
Flatbed die cutting uses steel rule dies, solid milled dies, and male/female or compound dies to cut or punch sheets of gasket material. Steel rule dies are the least expensive type. Steel rule dies are typically the least expensive type and once the design phase is complete, they're a good choice for low to high volume production, especially when you need dies in just a few days.
A solid milled die costs more and takes longer to make, but they provide increased cutting accuracy with both larger and smaller parts. Male/female dies or compound dies are ideal when fine details and very tight tolerances are required.
Before production begins, a die must be built according to your design. Then this die is used to produce a consistent set of parts that all fit your design.
When is Die Cutting a Fit?
Die cutting is often the standard method of choice for two dimensional gaskets being produced at high volumes.
Depending upon the number of parts being produced, the material being used, the complexity of your design, and the speed at which you need the parts delivered, die cutting may well be your lowest cost option.
In general die cutting is a good choice if all of the following are true:
- You are producing a high volume of parts
- The part isn’t too large
- The part isn’t too small
- The part doesn’t have very narrow walls
- The material you are cutting isn’t too thick
- You have a lead time of over a week
Take a deeper look at some of these considerations in the sections below.
Material Considerations
One of the most important aspects of the DFM process is an understanding of the material you are looking to make your gasket with.
In general there is a misconception that tolerances for a specific design are determined primarily by the machines cutting or producing the gaskets. In reality, the ability for a manufacturer to meet tolerances on a specific gasket design depends far more heavily on the material itself than on the manufacturing process.
The interplay between the material itself and the method of gasket production is a very large part of the DFM process. Getting the right match between the two is a big part of the battle. Traditional elastomeric materials, both solid and cellular, react to die cutting much differently than films and thermal materials.
Density and thickness of the material being cut is often a large part of the determination of if die cutting will work to achieve the desired result. And unfortunately, it isn’t as simple as just looking at the material properties themselves; it is actually more a factor of how the design of the gasket and the material properties will affect each other.
For instance, if the gasket is being made from solid rubber, the design cannot have wall thicknesses narrower than the thickness of the material itself for die cutting to be an appropriate process.
Because die cutting deforms the material as it punches through, understanding how the skin of the material will be affected by that punch is also important. Some skins will depress more uniformly during this process than others. The DFM process comes down to knowing how the material will react to the punch, and if it is possible to maintain design tolerances through that process.
In general, thicker materials are not often a fit for die cutting if you are also looking for very strict tolerances. Wall deformities and other tolerance issues become noticeable for solid materials over 1/8th inch, or open or closed cellular elastomers over 3/8ths of an inch. In these cases, projects will require loosened tolerances and/or a different manufacturing process.
Design and Quality Considerations
Up next in the list is the design of your part itself. Arguably this factor has the most sway over which manufacturing process will be the right fit.
When a design comes our way for DFM, the first thing we will look at is the tolerances listed in the design. Often a big part of the communication that happens with a customer during the DFM process is to understand if there is leeway on any of the tolerances listed (and in many cases there is).
Understanding what is a hard and fast requirement, and what can be adjusted helps us determine the right manufacturing process that will also help balance other important factors like cost and lead time.
The size and shape of the design is one factor that determines fit. Designs with very narrow walls or for very small parts made out of soft materials are usually not the best fit for die cutting. Designs that are larger than the size of the die press, or larger than 30 inches, are also usually best made with a different manufacturing method.
Workmanship quality requirements and tolerances are another part of the design that must be considered. Because die cutting can deform material when punching through it, we weigh the tolerance requirements of the design with the material properties (basically how well the material is able to withstand those forces) and thickness to see if it is possible to achieve your design requirements with die cutting.
-- Article Continues Below --
Read the Guide: DESIGNING FOR SUCCESS –
DIE CUT GASKETS
Cost Considerations
The next consideration in what is beginning to feel a bit like a mile long list is your cost. While die cutting is often thought of as the “lowest cost” manufacturing process, it may not always be the case.
If you are producing a relatively small volume of parts, sometimes it won’t be the most inexpensive option. In order to die cut parts, you first have to build the die (usually somewhere between $300-700) and then pay for production of parts. In prototype situations, where you need just a few parts, and the design itself may still change, this often isn’t worth it.
There are other factors, or creative ways in which your manufacturing partner can work with you, such that other manufacturing processes may result in lower costs, depending on your design.
For instance, some examples include:
- Material waste: Sometimes using different methods for manufacturing can reduce material costs. If your design is just a small square for instance, it might make more sense to use a CNC knife and cut a bunch of them out side-by-side and reduce the amount of material wasted (reducing your material costs).
- Stacking or layering: Sometimes when using waterjet cutting for instance, we can get creative with how many parts we cut at once. Depending on the thickness of your material and your design, we can potentially stack multiple layers of material and cut out multiple parts at time with a waterjet machine.
All in all, there is no blanket rule that says die cutting is cheaper than other manufacturing processes. It is all situational, and going through the DFM process will help raise options like this that you might not have considered.
Lead Time Considerations
Yet another item to consider is lead time. If you need your part like yesterday, die cutting may not be the best fit to get it to you that fast.
In general, the process to make the die itself can take upwards of a week. Most manufacturers will have options to expedite, but you’ll pay more for doing so.
Once into production, time considerations come in with how fast an operator can produce parts. In general, a manual operator can complete somewhere between 3-4 punches per minute. If there is an option to use another process with layering (as discussed in the previous section), it can sometimes reduce the amount of time it takes to complete the full volume of parts you require.
The Bottom Line
There is no easy way to say die cutting is or isn’t a fit in general terms. It always comes down to a review of the interplay between your design, selected material, and production requirements.
Hopefully this article provided you with some clarity on what we review in order to determine if die cutting might be a fit, but if you are looking to see if it works for a specific design, we highly recommend submitting it to us for a DFM review.