Selecting the Right CHO-FORM Form-in-Place Material: A Comprehensive Guide
November 25, 2024
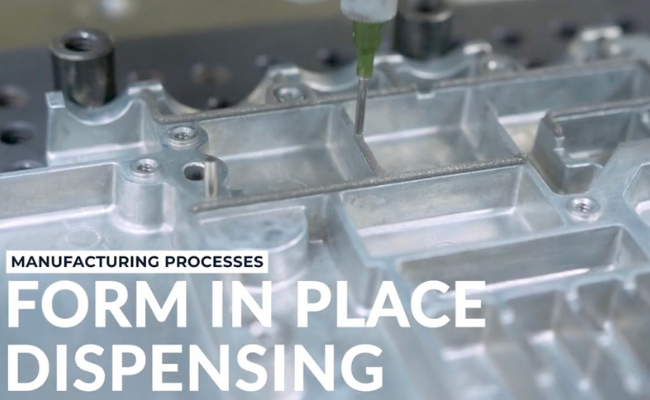
Manufactured with Speed and Precision
The manufacturing capabilities you need and the engineering support you want, all from a single partner.
Submit a DesignKey Points
Don't have time for the full read? Here are the critical takeaways you need to know:
✓ Material Selection Impact: Selection of the right CHO-FORM material is critical for both EMI shielding performance and manufacturing efficiency. Your choice affects everything from electrical conductivity to production speed to long-term reliability.
✓ Environment Drives Performance: The operating environment should be your primary selection driver. For aerospace/defense applications, look to CHO-FORM 5560 (Ni/Al filled) for superior corrosion resistance. For medical devices, consider CHO-FORM 5526 (Ag filled) for highest conductivity and cleanroom compatibility.
✓ Processing Trade-offs Matter: Thermal cure materials offer faster processing (test/ship same day) but require specific equipment. Moisture cure materials provide more flexibility but need 24-hour cure times. This choice significantly impacts your production timeline and capabilities.
✓ Engineering Success Factor: The most successful implementations aren't just about material selection – they require careful attention to design factors like bead size (aim for 30% compression), surface preparation (verify surface resistance <0.01 ohm), and environmental considerations.
Want to explore these points in more detail? Keep reading for a comprehensive analysis, or reach out to our engineering team for guidance specific to your application.
Form-in-place EMI gaskets play a critical role in ensuring electromagnetic compatibility and environmental sealing in modern electronic devices. Parker Chomerics offers multiple CHO-FORM materials, each engineered for specific performance characteristics and applications. This comprehensive guide will help engineers and designers navigate the material selection process by examining key considerations, comparing available materials, and providing industry-specific recommendations.
Key Selection Criteria
Choosing the right CHO-FORM material involves balancing multiple technical requirements and practical considerations. Understanding these key selection criteria will help ensure your chosen material not only meets performance specifications but also aligns with your manufacturing capabilities and budget constraints. The following factors should be carefully evaluated when selecting a CHO-FORM material for your application.
Before diving into specific materials, let's examine the main factors to consider when selecting a CHO-FORM material:
1. Conductivity Requirements
EMI shielding performance starts with the electrical properties of your gasket material. Understanding your application's specific conductivity needs helps narrow down material options and ensures adequate protection against electromagnetic interference.
- Volume resistivity needs
- Shielding effectiveness requirements
- Grounding requirements
2. Environmental Considerations
Your gasket must maintain its performance throughout its entire service life, despite whatever environmental challenges it faces. Evaluating environmental exposure helps determine the level of protection needed and influences material selection.
- Operating temperature range
- Exposure to harsh environments
- Corrosion resistance needs
3. Mechanical Properties
Physical characteristics directly impact gasket performance and longevity. The right balance of hardness, compression force, and tensile strength ensures reliable sealing and durability in your application.
- Compression force requirements
- Hardness needs
- Tensile strength requirements
4. Processing Requirements
Manufacturing capabilities and production needs significantly influence material selection. Consider your facility's processing capabilities and production volume requirements when evaluating different cure types and handling needs.
- Cure type preference (thermal vs. moisture)
- Production volume and speed needs
- Storage conditions
5. Substrate Compatibility
The interaction between your CHO-FORM material and housing substrate is crucial for long-term performance. Proper material selection ensures good adhesion and prevents potential galvanic corrosion issues.
- Housing material (aluminum, magnesium, plastics)
- Surface treatments and coatings
- Adhesion requirements
Material Comparison
To facilitate material selection, we've compiled comprehensive data on all available CHO-FORM materials. This side-by-side comparison allows engineers to quickly evaluate and compare critical properties across the entire product line. The following table presents key technical specifications and performance characteristics that typically drive material selection decisions.
Property | CHO-FORM 5513 | CHO-FORM 5541 | CHO-FORM 5550 | CHO-FORM 5560 | CHO-FORM 5526 | CHO-FORM 5528 | CHO-FORM 5538 | CHO-FORM 5575 |
Conductive Filler | Ag/Cu | Ni/C | Ni/C | Ni/Al | Ag | Ag/Cu | Ni/C | Ag/Al |
Cure Type | Thermal | Thermal | Thermal | Thermal | Moisture | Moisture | Moisture | Moisture |
Volume Resistivity (Ω-cm) | 0.004 | 0.030 | 0.035 | 0.13 | 0.003 | 0.005 | 0.050 | 0.010 |
Hardness (Shore A) | 53 | 75 | 55 | 55 | 38 | 40 | 65 | 75 |
Shielding Effectiveness (dB) | >70 | >65 | >65 | >90 | >90 | >70 | >50 | >80 |
Galvanic Corrosion Resistance | Not Recommended | Good | Better | Best | Not Recommended | Not Recommended | Good | Excellent |
Tensile Strength (psi) | 350 | 500 | 175 | 165 | 80 | 125 | 325 | 180 |
Compression Set (%) | 28 | 30 | 25 | 25 | 45 | 45 | 45 | 40 |
Maximum Use Temp (°C) | 125 | 125 | 125 | 125 | 85 | 125 | 85 | 125 |
Minimum Bead Height* (inches) | 0.018 | 0.026 | 0.038 | 0.038 | 0.018 | 0.018 | 0.015 | 0.034 |
*Minimum bead height as recorded by the manufacturer. Need to push the boundaries of bead size? No problem. Read this case study about how we helped dispense a custom small bead size for one of our customers.
Detailed Material Analysis
Each CHO-FORM material has been engineered with specific performance characteristics to address different application requirements. Understanding the unique properties, advantages, and limitations of each material is crucial for making an informed selection. Let's examine each material in detail to understand where it excels and where caution may be needed.
1. CHO-FORM 5513 (Ag/Cu Filled)
This high-performance material combines excellent electrical properties with strong mechanical characteristics, making it ideal for applications where conductivity and durability are paramount considerations.
Best for: Applications requiring excellent electrical properties and strong adhesion
- Superior electrical conductivity (0.004 Ω-cm)
- Excellent adhesion to various substrates
- Moderate hardness (53 Shore A)
- Two-component thermal cure system Limitations: Not recommended for applications requiring corrosion resistance
Read more about CHO-FORM 5513.
2. CHO-FORM 5560 (Ni/Al Filled)
Engineered specifically for harsh environment applications, this material offers industry-leading corrosion resistance while maintaining excellent shielding effectiveness.
Best for: Applications requiring superior corrosion resistance
- Excellent corrosion resistance
- High shielding effectiveness (>90 dB)
- Good balance of properties
- Single component thermal cure Ideal for: Military and aerospace applications exposed to harsh environments
3. CHO-FORM 5526 (Ag Filled)
When maximum electrical conductivity is required, this pure silver-filled material delivers superior performance with the lowest volume resistivity in the CHO-FORM lineup.
Best for: Applications requiring lowest electrical resistance
- Lowest volume resistivity (0.003 Ω-cm)
- Excellent shielding effectiveness (>90 dB)
- Soft and compliant (38 Shore A)
- Moisture cure for room temperature processing Limitations: Limited corrosion resistance, lower maximum temperature (85°C)
Read more about CHO-FORM 5526.
4. CHO-FORM 5541/5550 (Ni/C Filled)
These versatile materials offer an excellent balance of performance and cost, making them ideal for high-volume commercial applications where reliability and value are key considerations.
Best for: General-purpose applications requiring good corrosion resistance
- Good balance of properties
- Excellent adhesion (5541)
- Lower closure force (5550)
- Cost-effective solution Ideal for: Commercial electronics and telecommunications equipment
Read more about CHO-FORM 5550.
Read more about CHO-FORM 5541.
5. CHO-FORM 5528 (Ag/Cu Filled)
This versatile material combines excellent electrical properties with the flexibility of moisture cure processing, making it ideal for applications where thermal curing equipment isn't available.
Best for: Applications requiring excellent conductivity with room temperature processing
- Superior electrical properties (0.005 Ω-cm)
- Good shielding effectiveness (>70 dB)
- Moderate hardness (40 Shore A)
- Single component moisture cure
- Good adhesion to various substrates Limitations: Not recommended for applications requiring corrosion resistance, lower maximum temperature (125°C)
Read more about CHO-FORM 5528.
6. CHO-FORM 5538 (Ni/C Filled)
Engineered specifically for applications requiring small cross-sections, this material offers good corrosion resistance while maintaining the ability to be dispensed in very fine beads.
Best for: Applications requiring minimum bead sizes with good corrosion protection
- Smallest available bead size (down to 0.015 in height)
- Good corrosion resistance
- Moderate shielding effectiveness (>50 dB)
- Relatively high hardness (65 Shore A) for durability
- Single component moisture cure Ideal for: Small form factor electronics and tight space constraints
Read more about CHO-FORM 5538.
7. CHO-FORM 5575 (Ag/Al Filled)
This material provides an excellent balance of corrosion resistance and electrical performance, making it particularly well-suited for harsh environment applications requiring reliable shielding.
Best for: Applications requiring both good conductivity and corrosion resistance
- Excellent corrosion resistance
- High shielding effectiveness (>80 dB)
- High hardness (75 Shore A) for mechanical durability
- Good conductivity (0.010 Ω-cm)
- Single component moisture cure Ideal for: Military and aerospace applications where both environmental protection and shielding are critical
Read more about CHO-FORM 5575.
Industry-Specific Applications
Different industries face unique challenges and requirements when it comes to EMI shielding. Understanding these industry-specific needs is crucial for selecting the most appropriate CHO-FORM material. The following sections break down key considerations and recommendations for major industries where form-in-place gaskets play a critical role.
Defense and Aerospace Applications
The defense and aerospace sector demands the highest levels of reliability and performance under extreme conditions. EMI shielding solutions in this industry must meet rigorous military specifications while providing consistent performance in challenging environments.
Key Requirements
Military and aerospace applications present some of the most demanding operating conditions for EMI gaskets. Understanding these requirements is essential for proper material selection and design implementation.
- High reliability in extreme environments
- Superior shielding effectiveness
- Resistance to temperature extremes
- Corrosion resistance
- Compliance with military specifications
Recommended Materials
Material selection for defense and aerospace applications must prioritize reliability and performance over cost considerations. The following recommendations are based on extensive field experience in military applications.
- Primary Choice: CHO-FORM 5560 (Ni/Al filled)
- Best corrosion resistance
- Excellent shielding (>90 dB)
- High temperature resistance
- Proven track record in military applications
- Alternative: CHO-FORM 5575 (Ag/Al filled)
- Better conductivity than 5560
- Excellent corrosion resistance
- Good for applications requiring lower volume resistivity
Common Applications
Defense and aerospace systems rely heavily on EMI shielding for mission-critical functions. These applications typically require the highest levels of protection and reliability.
- Radar systems
- Military communications equipment
- Aviation electronics
- Missile guidance systems
- Satellite communications equipment
- Ground-based defense systems
Design Considerations
Proper design implementation in defense and aerospace applications requires careful attention to environmental factors and performance requirements specific to military and aviation environments.
- Consider salt spray exposure for naval applications
- Account for altitude effects
- Plan for extreme temperature cycling
- Factor in vibration resistance
- Consider maintenance accessibility
Medical Device Applications
Medical devices present unique challenges for EMI shielding, requiring solutions that balance electromagnetic protection with strict regulatory compliance and biocompatibility requirements. Material selection must carefully consider sterilization processes, cleaning protocols, and long-term reliability in healthcare environments.
Key Requirements
Medical device EMI shielding must meet stringent regulatory standards while ensuring consistent performance in healthcare settings. These requirements often go beyond typical industrial applications to address patient safety and medical device reliability.
- Biocompatibility considerations
- Cleanroom compatibility
- Sterilization resistance
- Reliable performance
- Precision dispensing capability
Recommended Materials
Material selection for medical devices must prioritize cleanliness, reliability, and compatibility with medical-specific processes. These recommendations are based on extensive experience in medical device applications.
- Primary Choice: CHO-FORM 5526 (Ag filled)
- Highest conductivity
- Soft and compliant
- Excellent shielding
- Room temperature cure
- Alternative: CHO-FORM 5513 (Ag/Cu filled)
- Better mechanical properties
- Good for higher stress applications
- Excellent electrical properties
Common Applications
Modern medical devices rely heavily on electronic systems that require sophisticated EMI protection. These applications demand materials that can maintain their integrity while ensuring device accuracy and reliability.
- Medical imaging equipment (MRI, CT, X-ray)
- Patient monitoring devices
- Surgical equipment
- Diagnostic devices
- Therapeutic equipment
- Laboratory instruments
Design Considerations
Medical device design must account for unique healthcare environment challenges while ensuring compliance with relevant regulations and standards. Careful attention to these factors helps ensure successful long-term performance.
- Consider sterilization methods
- Account for cleaning agent exposure
- Plan for EMI protection of sensitive equipment
- Factor in regulatory requirements
- Consider patient safety requirements
Telecommunications Applications
The telecommunications industry demands EMI shielding solutions that can perform reliably in both indoor and outdoor environments while meeting aggressive cost targets for high-volume production. Material selection must balance performance requirements with economic considerations for competitive markets.
Key Requirements
Telecommunications equipment often operates in challenging environments while requiring cost-effective solutions suitable for high-volume manufacturing. Understanding these dual demands is crucial for successful material selection.
- Cost-effectiveness
- Outdoor durability
- High volume production capability
- Reliable long-term performance
- Field serviceability
Recommended Materials
Material selection for telecommunications applications must balance performance with cost considerations. These recommendations are based on proven success in high-volume telecommunications deployments.
- Primary Choice: CHO-FORM 5541/5550 (Ni/C filled)
- Cost-effective
- Good corrosion resistance
- Reliable performance
- Suitable for high-volume production
- Alternative: CHO-FORM 5560
- For outdoor applications
- Superior environmental resistance
- Better shielding effectiveness
Common Applications
Modern telecommunications infrastructure relies on effective EMI shielding for reliable operation. These applications typically require solutions that can be implemented across large-scale deployments while maintaining consistent performance.
- 5G infrastructure equipment
- Base station electronics
- Network switches and routers
- Cellular equipment enclosures
- Satellite communication systems
- Data center equipment
Design Considerations
Telecommunications equipment design must account for various installation environments while ensuring efficient manufacturing processes. These considerations help ensure successful deployment and long-term reliability.
- Consider outdoor exposure requirements
- Plan for thermal management
- Account for installation conditions
- Factor in maintenance requirements
- Consider cost targets for high-volume production
Processing Considerations
The selection of a CHO-FORM material significantly impacts manufacturing processes and production capabilities. The cure mechanism - either thermal or moisture cure - brings distinct advantages and limitations that must be considered early in the design phase. Understanding these processing requirements helps ensure smooth production implementation and optimal performance results.
Thermal Cure Materials (5513, 5541, 5550, 5560)
Thermal cure materials offer faster processing times and superior adhesion properties, making them ideal for high-volume production environments with appropriate curing equipment.
Advantages
- Faster processing
- Better adhesion properties
- Higher temperature resistance
- Can be tested and shipped same day
Requirements
- Cure temperature: 140-150°C
- Cure time: 30 minutes
- Frozen storage (-10°C ±5°C)
Moisture Cure Materials (5526, 5528, 5538, 5575)
Moisture cure materials provide greater flexibility in processing conditions and are particularly well-suited for temperature-sensitive applications or facilities without thermal curing capabilities.
Advantages
- Room temperature processing
- No special equipment needed
- Suitable for temperature-sensitive substrates
Requirements
- Cure conditions: 22°C, 50% RH
- Cure time: 24 hours
- Room temperature storage (22°C ±5°C)
Design Recommendations
Successful implementation of CHO-FORM materials extends beyond material selection to encompass proper design practices. Following established design guidelines helps ensure optimal gasket performance and manufacturing efficiency. These recommendations represent best practices developed through extensive field experience and customer feedback.
1. Bead Size Selection
Proper bead size specification is crucial for gasket performance. Understanding the relationship between bead dimensions and compression characteristics helps ensure reliable sealing and electrical performance.
- Consider minimum bead height requirements for each material
- Typical recommendation: 30% compression
- Avoid compression below 20% or above 40%
2. Surface Preparation
Surface preparation plays a critical role in gasket adhesion and long-term performance. Proper surface treatment and cleanliness are essential for achieving optimal results.
- Ensure surfaces are clean and free from contaminants
- Proper surface treatment for substrate material
- Verify surface resistance <0.01 ohm
3. Environmental Considerations
Environmental factors can significantly impact gasket performance and longevity. Careful consideration of operating conditions helps ensure reliable long-term performance.
- Account for temperature cycling
- Consider exposure to chemicals or harsh environments
- Evaluate UV exposure if applicable
Cost Considerations
While technical performance is paramount, cost considerations play a crucial role in material selection. Understanding the full cost implications of different CHO-FORM materials helps engineers make economically sound decisions without compromising performance requirements. Cost analysis should consider not just material prices, but the total cost of ownership throughout the product lifecycle.
Material Cost Hierarchy (High to Low)
Understanding the relative cost positioning of different CHO-FORM materials helps in making informed decisions that balance performance requirements with budget constraints.
- Pure silver filled (5526)
- Silver/copper filled (5513, 5528)
- Silver/aluminum filled (5575)
- Nickel/aluminum filled (5560)
- Nickel/carbon filled (5541, 5550, 5538)
Total Cost of Ownership Factors
A comprehensive cost analysis must consider all aspects of material implementation and long-term use, not just the initial material cost.
- Material costs
- Processing requirements
- Production speed capabilities
- Scrap rates
- Long-term reliability
Final Thoughts
Selecting the right CHO-FORM material requires careful consideration of multiple factors. While the initial selection may seem complex, understanding your application requirements and prioritizing key properties will help narrow down the choices. Consider these general guidelines:
- For highest shielding effectiveness: CHO-FORM 5526 or 5560
- For best corrosion resistance: CHO-FORM 5560
- For lowest cost: CHO-FORM 5541/5550
- For fastest processing: Thermal cure materials (5513, 5541, 5550, 5560)
Remember that material selection is just one part of the equation. Proper design, processing, and quality control are equally important for achieving optimal performance in your application.