Setting Tolerances for Elastomeric or Flexible Parts
March 30, 2021
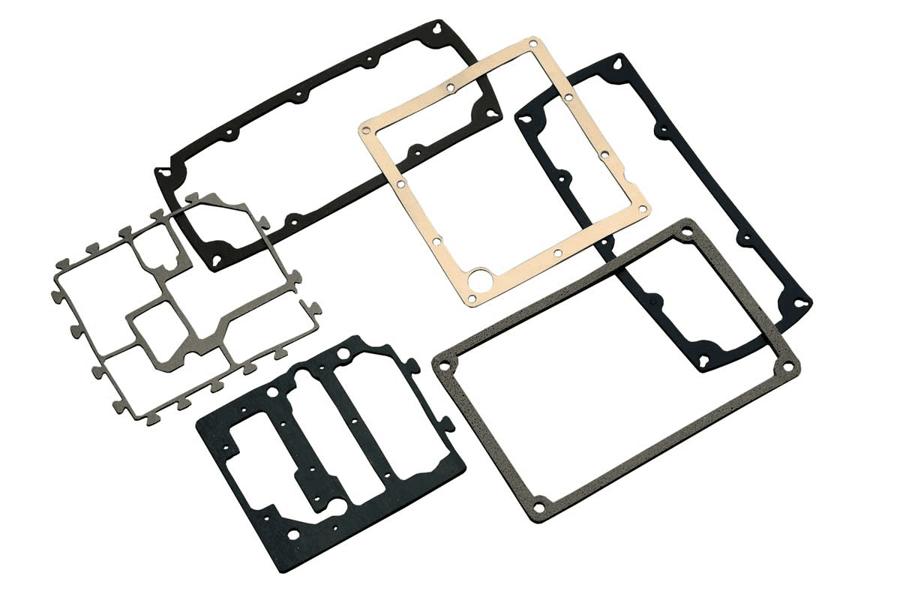
Manufactured with Speed and Precision
The manufacturing capabilities you need and the engineering support you want, all from a single partner.
Submit a DesignIn our years of working with engineers building custom gaskets, the single most common issue we run into is the misconception about setting tolerance for elastomeric parts. In many of the designs submitted for quote review, we often see requested tolerances that are impossible to achieve regardless of the production method used to create them.
The primary reason this happens is quite simply because elastomeric materials are highly compliant, and as such, it is very different than setting a tolerance on rigid parts.
-- Article Continues Below --
Avoid frequent design mistakes in our free guide.
Shifting from Rigid Parts to Flexible Parts
Most engineers are comfortable, and have plenty of experience, defining tolerances for rigid or machined parts, taking into account many variables such as Cpk (process capability), tolerance stack, maximum mass, thermal expansion, etc. A common mistake we see for elastomeric materials is applying the tolerance used for rigid materials.
Generally, rigid part tolerances are defined by the ASME Y14.5 GD&T Standard. The standard specifies five fundamental types of tolerances:
- Form: This portion of the standard covers how to properly denote tolerances for straightness, flatness, circularity, and cylindricity.
- Orientation: This portion of the standard covers how to use tolerances to control rotation of a feature and are measured by angularity, perpendicularity, and parallelism.
- Location: This portion describes how to use tolerances to define the location of features in relation to each other and is measured in position, concentricity, and symmetry.
- Profile: This type of tolerance controls the shape of a surface relative to an “ideal” version of that surface. The two types of profile tolerances cover the profile of a surface, and the profile of a line.
- Runout: This type of tolerance is a measure of variation in a surface when it is rotated around an axis.
For the materials covered by the ASME standard, suggested tolerances are based on an understanding of maximum mass of the material in question, and a typical Cpk of 1.33. The science is very well understood and manufacturing processes are more controllable due to the relative inert state of rigid metals when compared with elastomeric materials.
However, elastomeric materials do not adhere to the same set of rigid principles, and as such, need a wider tolerance to meet inspection criteria.
By their very nature, elastomeric materials can flex and adjust shape, and cutting out large chunks of a material can significantly affect the ability of that material to hold a specific shape.
In general, we recommend that engineers take a look at Modus’ standard tolerances or standard RMA tolerances for a better understanding of what is possible to expect from elastomeric materials. That’s not to say that tighter tolerances are impossible, it just means that it is going to take a lot more resources (and typically budget) to create a part that meets more severe requirements.
Material Properties
When working with elastomeric materials, there is a common misconception that the method of manufacturing (e.g. die cutting, waterjet cutting, etc.) is the primary determinant of the tolerances that are possible to uphold.
In reality, the material itself is far more of the determining factor, and when combined with part shape and function, tolerance can become a cost driver and bottleneck for production.
Adding another layer of complexity to the situation is that the same type of material made from two separate manufacturers may well have differences in how they can hold to tolerances. Small changes to the way a material is formulated or produced can have pretty significant effects on how that material handles being cut into specific shapes.
Additionally, the thickness of a material also has huge implications on the tolerances it can hold. Typically the thicker an elastomeric material, the larger the tolerances needed to meet a Cpk of 1.33.
Release of Tension
In addition to the thickness of the material and its makeup, yet another factor to take into account is the material’s reaction to the release of tension imbued into the material at time of manufacture.
When you remove a substantial chunk of material, for instance through die cutting, much of the tension the material holds will be released with it as well. Given part size, this can substantially affect the final shape of your custom gasket.
This reaction to the release of tension is not necessarily consistent between materials, and should be taken into account when selecting the material for your application.
Read Now: Guidance from start to finish on your custom gasket production.
Measuring Tolerances
If all of this isn’t enough, another challenge when working with elastomeric materials is the ability to accurately measure part features. With rigid parts, having machined surfaces, this is not such a problem, but for elastomers, the cutting process is much different, and depending on material, can be very challenging. At Modus, we employ state-of-the-art laser measuring systems, video measuring and utilize coordinate measuring machines (CMM) to ensure parts adhere to design specifications.
All these tolerance conditions are accounted for in both the Modus tolerance tables and RMA tolerance tables. At Modus, we have established tolerances with the smallest range which will minimize risk of deficient parts (Cpk of 1.33).
Let’s Get Creative
Never ones to back down from a challenge, we are always willing to work with the engineers who submit designs to us to learn how we can help meet the needs of their application.
During our Design for Manufacturability (DFM) review process, we work with engineers to determine what is critical to the fit, form and function of the part in question and look for opportunities to simplify and streamline the design in an effort to reduce lead times and part costs.
Often some of the misconceptions with tolerances can be addressed at this point and, as long as we are involved early enough in the design process, help to facilitate a design that still meets all the functional needs of the project and is much easier and less expensive to manufacture.
And then there are times when the constraints are so tight, we work with those engineers to get extra creative in finding ways to manufacture their custom gasket with tighter than standard tolerances.
Keep in mind, extra creative usually means more steps in the manufacturing process and thus longer lead times and higher costs. As such, we usually look to help engineers minimize these so they are getting the most bang for their buck.
Some examples of ways we’ve gotten creative to meet very tight tolerances on elastomeric parts include:
- Stress-relieving the material before processing it. This involves cutting the material to release the tension before cutting the final part out of the material, alleviating some of the “release of tension” issues we discussed above.
- Adjusting other parts of the design. Sometimes the constraints applied on the elastomeric material are the result of design decisions to the housing or other parts the gasket will contact. Because we have a team of engineers who also understand machining deeply, we can provide feedback on other parts of the application design that would make it easier to produce the custom gasket best fitting the application.
- Varying production processes. Because we have a wide range of capabilities including die cutting, waterjet cutting, digital or CNC cutting, and form-in-place dispensing, sometimes we work with designers to vary the type of process we are using to create something that can meet their specifications.
Avoiding Issues with Tolerances
Often, the most painful result of these misconceptions is the additional time that redesigns and design changes can incur.
When we receive designs with problems like this, we work with engineering teams to remedy the problem. Sometimes it can take a few minutes to change a minor part of the design, and sometimes it can take weeks to retool the larger part design overall.
The best way to avoid this is simply to involve the right people sooner in the design process. Having a relationship with a supplier that has a wide range of capabilities, and acts as a true partner, comes in handy in cases like this.
Bringing them in very early in the design process, and leveraging their expertise will help you get the design right the first time (and allow you to be aware of any concerns the finished part may pose based on the design).