Is Waterjet Cutting the Right Fit for Your Custom Gasket?
February 25, 2021
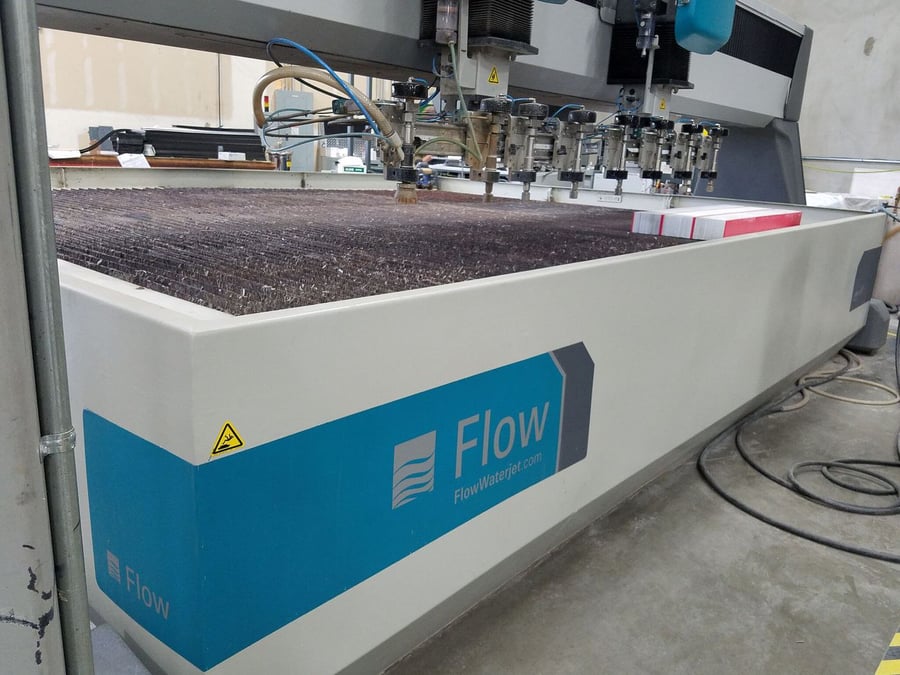
Manufactured with Speed and Precision
The manufacturing capabilities you need and the engineering support you want, all from a single partner.
Submit a DesignThis article is a member of our series on different manufacturing processes for custom gaskets. It follows the same structure, and includes similar introductory text, to ensure that whether you read a single article in the series or multiple, you’ll have all the information you need.
Choosing a Process
Choosing the right manufacturing process for producing your custom gasket is as much of an art as it is a science. The right manufacturing partner should be able to review your design, understand your needs for volume, and help you decide the appropriate method for production.
As much as we all wish it was an incredibly simple decision to determine the right manufacturing process fit for your needs, there are a ton of considerations that go into the decision. Any manufacturing partner worth working with long-term should have a very thorough Design for Manufacturing (DFM) process to help work through this with you.
Choosing the right manufacturing process is about balancing all of the following factors:
- Lead time
- Cost
- Volume of parts
- Quality and/or tolerance levels
- Material selection
-- Article Continues Below --
Learn how to avoid these common gasket design mistakes in our free guide!
Often making a decision that improves one factor can have an affect on the other factors, so understanding which process to choose ultimately comes down to prioritization. Deeply understanding how to achieve the requirements of your design as well as understanding what matters to you outside of the design itself leads to the right choice. And that is what the DFM process is all about.
This article breaks down some of the considerations that would lead to choosing waterjet cutting as the correct manufacturing process. It is meant to provide some general guidelines, but is by no means exhaustive, nor is it a replacement for undergoing the DFM process on a specific design.
How it Works
Waterjet cutting works by using a high-powered stream of water (try 90K psi) to cut through some pretty tough materials, which is a little amazing! Mix in <.040” garnet into the stream and you can cut through 6” stainless steel, but that is another article altogether.
Because waterjet is a form of computer numerically controlled equipment, it can cut very precise lines, smooth edges and corners. It also means there are no hard tooling requirements for using waterjet.
When is Waterjet Cutting a Fit?
Waterjet cutting is most often used for creating two dimensional gaskets out of thicker and/or harder materials.
However, depending upon the number of parts being produced, the material being used, the complexity of your design, and the speed at which you need the parts delivered, waterjet cutting is useful across a variety of situations.
In general waterjet cutting may be a good choice for the following situations:
- Thick and/or hard materials: Waterjet is the manufacturing method of choice for thick materials or very hard or high durometer materials as it can handle them better than other methods.
- Precise or smooth corners: Waterjet can provide the smoothest corners or edges of any manufacturing process.
- Large parts: Waterjet is a great fit for cutting very large format parts with high precision.
- Short lead times: If you need your parts faster than hard tooling solutions can turn them around, waterjet cutting may be the right fit.
- Material waste: Designs that nest well can provide less material waste than die cutting and may help reduce your material cost.
Material Considerations
One of the most important aspects of the DFM process is an understanding of the material you are looking to make your gasket with, and how it’s properties will affect tolerances and manufacturing process.
In general there is a misconception that tolerances for a specific design are determined primarily by the machines cutting or producing the gaskets. In reality, the ability for a manufacturer to meet tolerances on a specific gasket design depends far more heavily on the material itself than on the manufacturing process.
The interplay between the material itself and the method of gasket production is a very large part of the DFM process. Getting the right match between the two is a big part of the battle.
Density and thickness of the material being cut is often a large part of the determination for the gasket manufacturing process. And unfortunately, it isn’t as simple as just looking at the material properties themselves; it is actually more a factor of how the design of the gasket and the material properties will affect each other.
In general, waterjet cutting is the method of choice for materials that are generally thicker or where parts are larger and may not be suitable for die cutting or CNC cutting. It is also a great fit for exceptionally hard materials where other manufacturing processes will struggle.
Design and Quality Considerations
Up next in the list is the design of your part itself. Arguably this factor has the most sway over which manufacturing process will be the right fit.
When a design comes our way for DFM, the first thing we will look at is the tolerances listed in the design. Often a big part of the communication that happens with a customer during the DFM process is to understand if there is leeway on any of the tolerances listed (and in many cases there is).
Understanding what is a hard and fast requirement, and what can be adjusted helps us determine the right manufacturing process that will also help balance other important factors like cost and lead time.
Waterjet can be a fit for most various sizes and shapes of parts, but doesn’t work well for very small parts, as they may fall into the tank during production. It is a favorite for large format items that are too large for die cutting (about 30 inches or more).
From a quality perspective, waterjet cutting can help maintain straighter walls for thicker materials than other manufacturing methods, but keep in mind that even with a waterjet, you cannot have a perfectly straight wall because the water stream disperses and gets wider near the bottom.
Cost Considerations
The next consideration in what is beginning to feel a bit like a mile long list is your cost. Waterjet cutting has not traditionally been thought of as the “lowest cost” manufacturing process, but, depending on the situation it can be.
Part nesting: One such instance where waterjet cutting can reduce costs is through part nesting. If your part design can be nested in such a way that waterjet cutting allows us to produce more parts from the same size sheet of material, then it can reduce material costs significantly.
Layering: Waterjet cutting can provide the most layering benefits of any process. It is possible to layer multiple sheets of material on top of each other and cut multiple parts out at a time. Because a waterjet can handle a greater level of thickness overall, it can typically cut through more layers than a steel rule die.
Lead Time Considerations
Yet another item to consider is lead time. Waterjet cutting may be a great option if you need your part like yesterday.
It is much easier to turn around parts with short notice using digital cutting techniques, like waterjet, than those that require hard tooling, like die cutting.
In addition, because the waterjet has 8 unique heads that can all be cutting parts at the same time, it can handle a very large volume of parts with a single run. On top of that, using the layering and nesting techniques listed in the previous section, it can significantly help to bring down the total time to run a large volume of parts.
The Bottom Line
There is no easy way to say waterjet cutting is or isn’t a fit in general terms. It always comes down to a review of the interplay between your design, selected material, and production requirements.
Hopefully this article provided you with some clarity on what we consider DFM in order to determine if waterjet cutting might be a fit, but if you are looking to see if it works for a specific design, we highly recommend submitting your part design to us for a DFM review.