Thermal Management Solutions: 5 Keys to Thermal Dissipation Using Thermal Interface Material
December 5, 2016
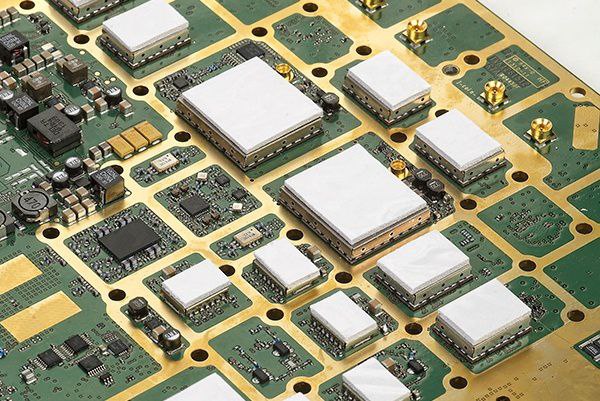
Manufactured with Speed and Precision
The manufacturing capabilities you need and the engineering support you want, all from a single partner.
Submit a DesignElectronic components produce heat when they operate. How these products manage their heat-generating and cooling systems determines how functional and reliable they are. Thermal management solutions and the resulting thermal dissipation greatly contributes to the performance and longevity of various products, especially electronic devices.
Since electronics generate power, fluctuations in temperatures can occur. When temperatures get too high, there needs to be a way to wick the heat away from the components to a heat-dissipating mechanism, such as a liquid cooling plate, chassis, or traditional heat sink. For instance, if a Printed Circuit Board (PCB) does not have a way to transfer heat, the reliability and longevity of its components will be adversely affected. In extreme cases, they can even melt or become damaged. Thermal Interface Materials (TIMs) are used to as a thermal management solution to transfer heat away from the heat source and onwards in the cooling chain.
Selecting the appropriate form and thermal conductivity of TIM is key to achieving optimal cooling in today's high-performance electronic enclosures. TIM solutions may be dispensed via automated equipment directly onto one of the surfaces as a paste, or be supplied as fully cured, pre-cut pads. The dispensed version is especially effective for intricate designs and can greatly reduce costs and lead times but does require the purchase of dispensing equipment and programming.
The pliability or softness of thermal materials can drastically cut thermal resistance and greatly enhance cooling by filling the gaps and small irregularities inevitably present between flat surfaces. Thermal interface materials are purposely made to conduct heat, usually by adding conductive gap filler to soft silicone to increase heat transfer. As a result, TIMs offer at least two orders of magnitude better thermal conductivity than the pockets of still air which would otherwise fill these irregularities.
Dispensed thermal interface material offer the following features:
- Available in cartridges
- Easily conforms to uneven and rough surfaces
- Thermal conductivity range 2-5 W/(m•K)
- Low contact resistance
- Soft – high deflection at low pressure
Die cut thermal pads offer the following features:
- Available in pre-cut custom die-cut parts or sheets (converted or unconverted)
- Highly conformable to uneven and rough surfaces
- Thermal conductivity range 1 – 12 W/(m•K)
- Thickness range 0.25 – 5 mm
- Soft – high deflection at low pressure
Five fundamentals of effective thermal dissipation are as follows:
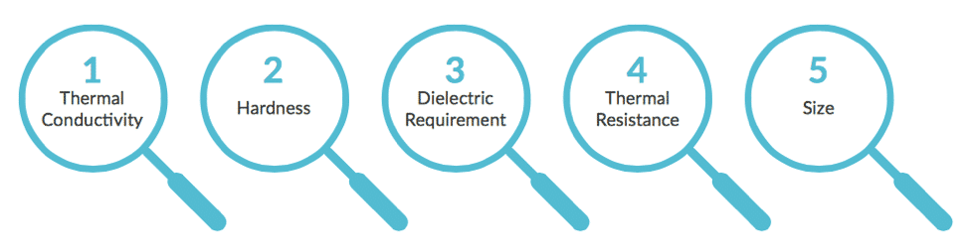
1. Thermal Conductivity
The rate at which heat passes through a material is its thermal conductivity. We typically talk about the conductivity of thermal management material in terms of the unit "Watts per meter Kelvin". This is expressed as W/(m • K).
This unit of measurement represents the amount of heat energy that can be transferred through a material per unit area per unit temperature difference. In other words, it tells us how well a material conducts heat. The higher the thermal conductivity, the more heat a material can transfer.
TIMs are specifically designed for thermal management to transfer excess heat while exhibiting a compression force characteristic that accommodates both the component that is creating the heat as well as the chassis or heat sink being used to dissipate the heat.
Thermal conductivity can be measured using equipment such as the Hot Disk 500S. This instrument uses a sensor that applies a constant power and simultaneously measures the temperature of the probe.
2. Hardness
Material hardness is measured using a Durometer that determines the resistance of a material to indentation.
The Durometer scale is used to measure material hardness by measuring the resistance of a material to indentation. The higher the Durometer number, the harder the material. For example, a material with a Durometer hardness of 70 is harder than a material with a Durometer hardness of 50.
Compression force has a relation to material hardness. It is preferable to choose a TIM with a low compression force requirement so electronic components are not damaged. Increasing the compression force effectively reduces thermal resistance. Have you ever gripped the handle of a warm kitchen pan? The tighter you grip the handle, the more heat you feel on your hand. Relaxing your grip on the handle increases thermal resistance, thus transferring less heat from the handle to your hand.
Image: Relative Durometer Scale
Another example of compression force can also be shown through the common heat sink that is used on the tab of a semiconductor device, such as a TO-220 package. For the TO-220 package, the metal tab on the package is compressed to the metal heat sink through torque using a nut tightened on a bolt. In situations that require the tab to be isolated, a TIM and nonconductive bolt are used. The amount of area that is compressed; the maximum force, which is speed dependent; and the relaxation of material (applied force is reduced over time) are considerations when determining compression variables.
Compression force considerations as it relates to thermal management:
- Amount of area that is compressed (example 1x1 cm, 2x2 cm)
- Maximum force (dependent on speed)
- Relaxation of material (applied force is reduced over time)
There isn't always a linear relation between hardness and compression force. Compression is a more important parameter in thermal conductivity applications. Note that compression force versus deflection is dependent on the sample thickness.
3. Dielectric Requirement
Dielectric breakdown voltage is the electric potential where a non-conducting material becomes conductive.
Dielectric breakdown voltage is important for thermal interface materials because it tells us how much voltage a material can withstand before it breaks down and becomes conductive. This is important because thermal interface materials are often used in applications where they are exposed to high voltages. If the dielectric breakdown voltage of a thermal interface material is too low, it could break down and cause a short circuit.
Dielectric testing consists of placing electrodes on both sides of a TIM and applying an increasing amount of voltage until a current begins to flow.
- Common test equipment measures up to 10 kV.
- Normally, the TIM should be electrically isolating, but dielectric breakdown voltage depends on the application.
- We typically talk about the conductivity of TIMs in terms of Watts per Meter Kelvin [W/(m•K)]. Dielectric breakdown voltage is typically between 1kV/mm and 20kV/mm. A dielectric breakdown less than 8kV/mm is usually adequate for most applications.
4. Thermal Resistance
The thermal conductivity of a material is not affected by the thickness of the product. However, the overall thermal resistance of a product is affected by the TIM thickness.
Thermal resistance is calculated using the following formula:
R = L / (kA)
where:
R is thermal resistance (in K/W)
L is thickness of the material (in meters)
k is thermal conductivity of the material (in W/(m•K))
A is area of the material (in square meters)
The resistance is a function of the material's high thermal conductivity, the contact area, and the TIM thickness, added to the contact resistances, which in turn are a function of how well the thermal interface materials conform to and wets the surfaces it attaches to. It is therefore best to have the shortest distance between the heat source and heat radiator, while having the TIM cover the maximum area of the heat source.
It is also important to maintain low enough thermal interface resistance to keep the component temperature below the threshold temperature.
5. Size
Thermal pads are typically cut to the dimensions of the product package that requires heat sinking. By making the pad as large as the package, the maximum surface area is achieved, thus creating the lowest possible thermal interface resistance in terms of the package plane. The typical die-cut pad thickness ranges are usually between 0.25-5 mm.
Success in Thermal Management
Although great gains are being made to reduce the amount of heat that is produced by electronics, effective heat dissipation is still vital to a product's success. Therefore, it is important to consider material composition, high thermal conductivity, hardness, dielectric requirement, thermal resistance, and size when selecting a thermal interface material.
These attributes will enhance your thermal dissipation efforts by seamlessly becoming part of the cooling chain. Choosing the appropriate TIM will also ultimately create efficient and reliable products with fewer product returns and potential additional costs.
Our experts can help you find the right fit for your next project – give us a call today.