AZW/LA-II White Thermal Control and Electrostatic Dissipative (ESD) Paint: Material Guide for Aerospace Applications
May 1, 2025
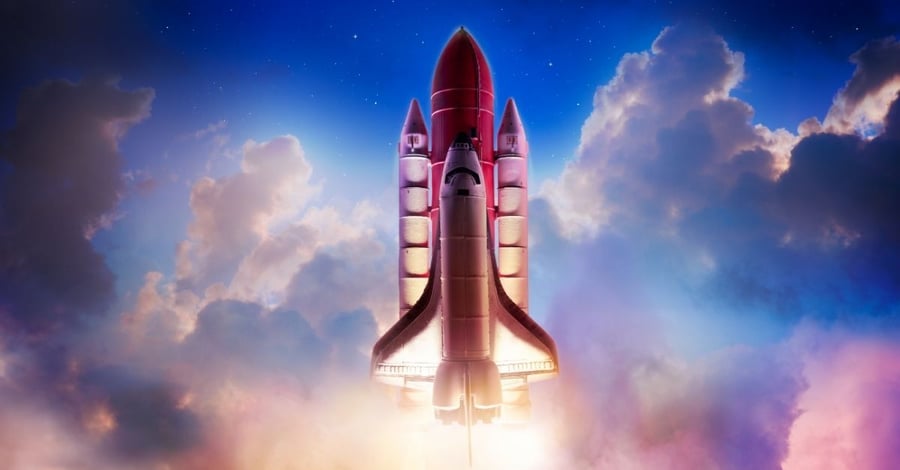
Manufactured with Speed and Precision
The manufacturing capabilities you need and the engineering support you want, all from a single partner.
Submit a DesignKey Points
- AZW/LA-II is an inorganic white thermal control ESD paint specifically engineered for spacecraft and satellite surfaces exposed to harsh space environments
- The coating provides superior thermal protection with extremely low solar absorptance (0.09 ± 0.02) and high thermal emittance (0.91 ± 0.02)
- This ESD paint has demonstrated exceptional stability, with less than 4% deterioration in solar absorptance after exposure to atomic oxygen and UV radiation
- After 4 years in orbit on the Materials International Space Station Experiment (MISSE), AZW/LA-II showed only 0.03 overall degradation in solar absorptance
- The ceramic-forming thermal control ESD paint operates in extreme temperature ranges from -292°F to 2552°F
- Application requirements and handling specifications demand precise engineering parameters for optimal performance
Engineered for the Harshest Environment: Space
When your hardware must perform in the most extreme environment known to humanity, the selection of thermal control coatings becomes a mission-critical decision. AZW/LA-II represents cutting-edge thermal control ESD paint technology specifically formulated for spacecraft and satellite applications where even minor thermal management failures could result in catastrophic mission outcomes.
This advanced thermal control ESD paint creates a nonspecular white coating that delivers remarkable thermal protection properties. The esd coating allows only 7-11% of solar radiation reaching the spacecraft's external surface to be absorbed into internal systems, while simultaneously emitting 89-93% of internally generated heat out to the vacuum of space.
For mission planners and spacecraft designers, these performance metrics translate directly to more stable internal temperatures, extended component lifespans, and reduced thermal management complexity.
Read the guide: AZ Technology Coating Materials Guide
Technical Performance Specifications
The technical specifications for AZW/LA-II thermal control ESD paint provide critical data points for engineers evaluating esd protection options for spacecraft applications. Understanding these parameters is essential for proper implementation in your designs.
Parameter | Specification | Engineering Significance |
Solar Absorptance (α_s) | 0.09 ± 0.02 at ≥ 10.0 mils thickness | Extremely low absorption of solar radiation reduces heat transfer to spacecraft interior |
Thermal Emittance (ε_t) | 0.91 ± 0.02 | Exceptional ability to radiate internal heat to space |
Use Temperature Range | -292°F to 2552°F (-180°C to 1400°C) | Functions across extreme temperature variations encountered in space |
Nominal Dry Thickness | 7 to 13 mils (over 85% of coated area) | Optimal thickness for performance balance |
ASTM D3359A Adhesion Grade | Not less than 3A | Provides necessary adhesion reliability in vacuum conditions |
Full Cure Time | 7-14 days | Critical scheduling consideration for integration workflows |
Appearance | Nonspecular white | Reduces glare while maintaining thermal properties |
These specifications demonstrate why AZW/LA-II stands out as a premier thermal control ESD paint for mission-critical space applications. The combination of extremely low solar absorptance with high thermal emittance creates an ideal thermal management profile for spacecraft external surfaces.
Composition and Stability Mechanisms
The exceptional performance of AZW/LA-II thermal control ESD paint stems from its carefully engineered composition. Engineers selecting this electrostatic dissipative coating should understand the fundamental mechanisms behind its stability in space environments.
AZW/LA-II incorporates a specialized formulation that includes:
- Stabilized pigment system that resists degradation
- Silicate binder that transitions to ceramic-like properties when cured
- Inorganic composition that resists breakdown from radiation exposure
- Chemical structure resistant to atomic oxygen attack
This formulation creates a thermal control ESD paint that maintains its performance characteristics despite exposure to the combined effects of vacuum, temperature cycling, radiation, and atomic oxygen. The ceramic-like nature of the cured coating provides a stability profile unavailable in organic-based alternatives.
For aerospace engineers, this stability translates to predictable thermal management characteristics throughout the mission lifetime – a critical factor in long-duration space applications where coating degradation could compromise thermal balance.
Visit the Resource Center: AZ Technologies Coating Materials
Space-Proven Performance Data
The theoretical performance of a thermal control ESD paint means little without verification in actual space conditions. AZW/LA-II has undergone rigorous testing both in simulated environments and in actual orbital exposure.
NASA testing exposed AZW/LA-II to:
- Atomic oxygen (AO) fluence of 7.4 x 10²⁰ atoms/cm²
- Ultraviolet (UV) radiation of approximately 832 equivalent solar hours
The results from this testing demonstrate the exceptional stability of this thermal control ESD paint. After exposure, the coating showed:
- Less than 4% deterioration in solar absorptance (α_s)
- Less than 1% change in thermal emittance (ε_t)
Even more compelling is the real-world orbital performance data. AZW/LA-II was flown on the Materials International Space Station Experiment (MISSE) and subsequently returned for analysis after 4 years in the space environment. Post-flight measurements revealed only a 0.03 overall degradation in solar absorptance compared to pre-flight values.
This minimal degradation in the harsh LEO environment makes AZW/LA-II thermal control ESD paint an ideal choice for missions requiring long-term thermal stability. Engineers can incorporate these degradation rates into thermal models with high confidence.
Application Guidelines for Aerospace Integration
Applying AZW/LA-II thermal control ESD paint requires adherence to specific protocols to ensure optimal performance. The application process directly impacts the coating's thermal properties and longevity, making specialized application expertise a critical factor in mission success.
Key application considerations include:
- Surface preparation must achieve appropriate cleanliness and roughness profiles
- Application temperature and humidity must be controlled within specified ranges
- Thickness control is critical - performance specifications require 7-13 mils dry film thickness
- Cure time of 7-14 days must be incorporated into integration scheduling
- Quality verification testing should include thickness measurements and adhesion testing
- Handling protocols must prevent contamination of the cured surface
Proper application of this thermal control ESD paint ensures that the theoretical performance characteristics translate to actual on-orbit performance. Application defects can create thermal anomalies that may compromise the spacecraft's thermal balance.
Why Partner with Modus Advanced for Coating Application
While the technical specifications of AZW/LA-II are impressive, achieving these performance parameters requires precision application that few manufacturers can deliver consistently. Modus Advanced brings several critical advantages to the application of specialized thermal control ESD paint:
- Engineering-first approach with over 10% of staff being degreed engineers who understand the science behind thermal control coatings
- AS9100 and ISO 9001 certified quality management systems that ensure consistent application meeting aerospace standards
- Vertical integration capabilities that reduce handling between manufacturing steps, minimizing contamination risks
- Climate-controlled application environments that maintain optimal temperature and humidity throughout the coating process
- Advanced measurement technologies that verify coating thickness to ensure performance specifications are met
- ITAR compliance and CMMC security standards that protect your sensitive aerospace designs
- Expertise in working with mission-critical sensitive components where coating failure could jeopardize astronaut safety or mission success
The application of AZW/LA-II is not simply a manufacturing step but a critical engineering process that requires specialized expertise. Modus Advanced's focus on aerospace and defense applications has built a team that understands the stakes involved when applying thermal control ESD paint to sensitive electronic components that will operate in the unforgiving environment of space.
Engineers should develop detailed application specifications in consultation with Modus Advanced's ESD coating specialists to ensure proper integration of AZW/LA-II into the manufacturing workflow. This attention to application details pays dividends in predictable thermal performance throughout the mission.
Read the guide: Optical and Thermal Coatings in Aerospace
Comparative Analysis: AZW/LA-II vs. Alternative Coatings
When selecting a thermal control ESD paint for spacecraft applications, engineers often evaluate multiple options. While AZW/LA-II represents a premium solution with exceptional performance characteristics, understanding how it compares to alternatives aids in making appropriate design decisions.
AZW/LA-II compared to other common spacecraft coatings:
- More expensive than AZ-93 but offers superior solar absorptance
- Provides better long-term stability than organic-based white paints
- Higher temperature resistance than many alternative coatings
- Superior atomic oxygen resistance compared to silicone-based options
- Better maintained optical properties than Teflon-based materials after UV exposure
This comparative assessment allows engineers to make cost-benefit analyses based on mission requirements. For applications where thermal stability is mission-critical, the premium performance of AZW/LA-II thermal control ESD paint often justifies the higher cost. For shorter-duration missions or less thermally sensitive applications, alternative coatings may provide sufficient performance at lower cost.
The decision matrix should consider mission duration, orbit characteristics, thermal sensitivity, and budget constraints when selecting between AZW/LA-II and alternative thermal control options.
Integration with Spacecraft Thermal Management Systems
AZW/LA-II thermal control ESD paint functions as one component in a comprehensive spacecraft thermal management strategy. Understanding how this coating interacts with other thermal control elements allows engineers to optimize overall system performance.
Thermal control ESD paint like AZW/LA-II typically integrates with:
- Multi-layer insulation (MLI) at transition boundaries
- Radiator surfaces for enhanced emission efficiency
- Active thermal control components like heat pipes or fluid loops
- Instrument thermal isolation systems
- Specialized thermal control surfaces for solar arrays and antennas
The exceptional α/ε ratio of AZW/LA-II creates unique opportunities for passive thermal management. When strategically applied to external surfaces, this thermal control ESD paint can reduce the complexity and power requirements of active thermal control systems.
Engineers should model the complete thermal system with accurate AZW/LA-II properties to optimize the overall thermal management approach. The coating's stable optical properties allow for more precise thermal predictions throughout the mission lifetime.
Engineering Considerations for Mission Success
Selecting and implementing AZW/LA-II thermal control ESD paint requires attention to several critical engineering factors that directly impact mission success. These considerations extend beyond basic material properties to encompass the entire mission lifecycle.
Mission planners and spacecraft engineers should evaluate:
- Thermal cycling impacts on coating adhesion and performance
- Long-term stability requirements based on mission duration
- Atomic oxygen exposure based on orbital parameters
- UV radiation exposure based on attitude and orbit
- Integration with other spacecraft materials to prevent compatibility issues
- Ground handling and pre-launch protection requirements
- Potential contamination sources during integration
Addressing these engineering considerations early in the design process ensures that AZW/LA-II will perform as expected throughout the mission. The exceptional stability of this thermal control ESD paint provides engineers with confidence that initial thermal models will remain valid throughout the spacecraft's operational life.
When Lives and Missions Depend on Thermal Control
The selection of appropriate thermal control ESD paint may seem like a minor detail in the complex process of spacecraft design, but thermal management failures have contributed to numerous mission anomalies and failures. When astronaut safety or mission-critical payloads are at stake, the proven performance of AZW/LA-II provides essential reliability.
For crewed missions, maintaining habitable temperatures is not merely a performance issue but a safety-critical requirement. For scientific missions, instrument thermal stability often directly impacts data quality. For commercial missions, thermal management affects service life and return on investment.
AZW/LA-II thermal control ESD paint has demonstrated its reliability in the harshest environment imaginable. Its exceptional performance characteristics make it an ideal choice for applications where failure is not an option and thermal management is mission-critical.
Partner with Modus Advanced to explore how AZW/LA-II and other advanced materials can enhance the reliability and performance of your aerospace systems. Our engineering team understands the critical nature of materials selection in aerospace applications and can help guide your design decisions for optimal mission outcomes.