Electrically Conductive Jet Fuel Resistant Sealant: Advanced Form-in-Place Gasket Materials
March 26, 2025
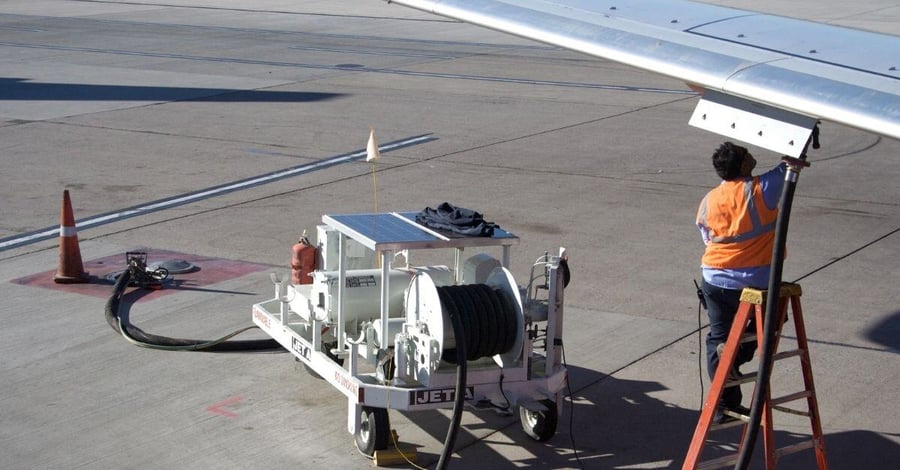
Manufactured with Speed and Precision
The manufacturing capabilities you need and the engineering support you want, all from a single partner.
Submit a DesignKey Points
- Aerospace and defense applications require specialized form-in-place (FIP) gasket materials that can withstand exposure to jet fuel while maintaining electrical conductivity
- The new jet fuel resistant sealant from Modus Advanced offers superior EMI/RFI shielding performance alongside chemical resistance to various aviation fuels
- Form-in-place dispensing provides precision application for complex geometries and small-scale components where traditional gaskets are impractical
- This specialized material can be applied to both metal and plastic housings using state-of-the-art dispensing equipment
- Engineers can reduce lead times and improve reliability by selecting the right jet fuel resistant sealant for critical aerospace components
- Working with a vertically integrated manufacturing partner ensures consistent quality and technical support throughout the design and production process
Introducing Arceo JFR-FIP: Modus’s Jet Fuel Resistant Form-in-Place Material
In the demanding world of aerospace and defense engineering, component reliability isn't just a matter of performance—it's often a matter of life and death. One of the most challenging aspects of designing systems for these applications is ensuring proper sealing and EMI/RFI shielding in environments where exposure to aviation fuels is a constant threat.
Standard sealing materials often degrade when exposed to these harsh chemicals, leading to premature failure and potentially catastrophic consequences. That's why Modus Advanced has developed a specialized jet fuel resistant sealant in our form-in-place gasket material lineup.
This advanced material represents a significant breakthrough for engineers tasked with designing and manufacturing critical aerospace components. By combining superior electrical conductivity with resistance to various types of jet fuel, this FIP gasket material addresses one of the most persistent challenges in aerospace design: maintaining shield integrity and environmental sealing in fuel-adjacent systems.
The need for specialized jet fuel resistant sealant becomes increasingly important as aerospace systems grow more compact and sophisticated, with electrical components often positioned in close proximity to fuel systems or in areas where fuel exposure is possible.
Everything you've ever wanted to know about FIP Gaskets - here!
Understanding Jet Fuel Resistant Sealant Requirements
Aerospace applications present unique challenges when it comes to gasket materials. The combination of extreme temperature fluctuations, pressure differentials, vibration, and chemical exposure creates an environment where standard sealing solutions often fail.
When designing components that may come into contact with aviation fuels, engineers need to account for the aggressive solvating properties of these chemicals that can degrade conventional elastomers and compromise both sealing and electrical performance.
A proper jet fuel resistant sealant must maintain its physical properties and electrical conductivity even after prolonged exposure to various types of jet fuel, including Jet A, JP-5, JP-8, JP-10, and specialized military formulations.
The material must resist swelling, shrinkage, and embrittlement while continuing to provide consistent electrical conductivity for EMI/RFI shielding. Additionally, it needs to adhere properly to substrate materials like aluminum, titanium, and composite structures commonly found in aerospace designs.
Materials that don't meet these stringent requirements can lead to a cascade of problems including shield effectiveness degradation, environmental seal failure, and ultimately system malfunction. The costs of such failures extend far beyond the component itself, potentially leading to system-wide issues, mission failure, or even safety incidents.
Evolution from Dual-Bead to Single Material Solutions
In the past, aerospace and defense manufacturers faced a challenging dilemma when designing electronics enclosures exposed to jet fuel environments. Traditional form-in-place gasket materials excelled at either EMI shielding or jet fuel resistance, but rarely both simultaneously. This limitation led to a common but cumbersome workaround: the dual-bead dispensing approach.
The dual-bead method involved applying two separate gasket beads to a single housing: an inner electrically conductive gasket for EMI shielding and an outer non-conductive but chemically resistant gasket to provide protection against jet fuel exposure. This approach, while functional, created several significant challenges for design engineers and manufacturing teams.
The housing required sufficient flange width to accommodate both gasket beads with adequate spacing between them. Each bead needed proper compression, requiring precise mechanical design of the mating surfaces. Additionally, the manufacturing process became more complex, with two separate dispensing operations and potential quality issues at the transition points between the two different materials.
For decades, this compromise solution was acceptable because aerospace electronics enclosures were relatively large, with ample flange width to accommodate dual gasket beads. However, the continuous miniaturization of avionics and other aerospace electronic systems has dramatically changed design requirements. Modern systems demand increasingly compact enclosures with minimal footprint, driven by:
- Aircraft weight reduction initiatives
- More sophisticated electronic systems requiring additional components in the same space
- Integration of multiple functions into single modules
- Unmanned aerial vehicle (UAV) designs with severe space constraints
- Embedded electronics in structural components with minimal allowance for sealing surfaces
As enclosure sizes have shrunk, the flange width available for gaskets has correspondingly decreased, often to dimensions that simply cannot accommodate dual-bead designs. In many contemporary applications, engineers are working with flanges barely 1-2mm wide—insufficient for even a single conventional gasket bead, let alone two separate beads with proper spacing.
This industry-wide miniaturization trend created an urgent need for a new approach: a single-bead jet fuel resistant sealant that could provide both excellent EMI shielding and withstand harsh chemical exposure. Our newly developed material addresses precisely this need, eliminating the compromise inherent in dual-bead designs while enabling the compact electronics packaging that modern aerospace applications demand.
By consolidating both functions into a single material that can be applied in one dispensing operation, our jet fuel resistant sealant not only solves the space constraint challenge but also simplifies the manufacturing process, reduces potential failure points, and decreases production time. This represents a significant advancement for aerospace design engineers who no longer need to make difficult trade-offs between space utilization, EMI protection, and chemical resistance when designing systems that may encounter jet fuel exposure.
Find the answer to all your FIP questions here.
Modus Advanced's Arceo FIP Jet Fuel Resistant Solution
Our new electrically conductive jet fuel resistant sealant represents the culmination of extensive materials research and testing. Designed specifically for aerospace and defense applications, this form-in-place gasket material delivers exceptional performance in both shielding effectiveness and chemical resistance. The material maintains its key properties even after extended exposure to various aviation fuels, ensuring long-term reliability in the most demanding applications.
The specialized formulation offers several key advantages over conventional gasket materials:
- Superior resistance to common aviation fuels including Jet A, JP-5, JP-8, and other military-grade fuels
- Excellent shielding effectiveness across a wide frequency range (>60 dB from 200 MHz to 10 GHz)
- Temperature stability from -65°F to +257°F (-54°C to +125°C)
- Low compression set for maintained sealing force over time
- Excellent adhesion to both metal and plastic substrates
- UL 94 V-0 flammability rating
- Salt fog resistance for maritime aerospace applications
This jet fuel resistant sealant can be precisely dispensed using our state-of-the-art automated equipment, allowing for application on complex geometries with exact bead placement. Our vertically integrated manufacturing process ensures consistent quality from initial design consultation through production, reducing potential points of failure in your supply chain.
Applications in Aerospace and Defense
The specialized properties of our jet fuel resistant sealant make it ideal for numerous critical aerospace and defense applications. Engineers working on these systems can benefit from a material that addresses both EMI/RFI shielding and environmental sealing requirements while maintaining performance in fuel-exposed environments.
Common applications for this specialized FIP gasket material include:
- Avionics enclosures in fuel-adjacent areas
- Fuel system monitoring equipment
- Wing-mounted electronic systems
- Engine control modules
- Fuel quantity measurement systems
- Communication equipment in fuel-exposed environments
- UAV/drone systems with integrated fuel tanks
- Flight control electronics
- Radar and sensor housings near fuel systems
In each of these applications, the dual functionality of the jet fuel resistant sealant eliminates the need for separate shielding and sealing solutions, reducing component complexity, weight, and potential points of failure. This integrated approach aligns with the aerospace industry's continuous drive toward more efficient, lightweight, and reliable systems.
Form-in-Place Dispensing Advantages
The precision application capabilities of form-in-place dispensing technology make it particularly well-suited for applying jet fuel resistant sealant in aerospace applications. Unlike pre-cut gaskets or O-rings that may require complex tooling and suffer from material waste, FIP technology allows for precise, automated dispensing directly onto component housings.
The advantages of FIP dispensing for jet fuel resistant applications include:
- Ability to create complex gasket geometries that follow intricate housing contours
- Precise control of gasket height, width, and cross-section
- Minimal material waste compared to die-cut methods
- Consistent bead dimensions across production runs
- Capability to dispense on narrow flanges (as small as 0.025" or 0.64mm)
- Excellent repeatability through automated CNC dispensing
- Ability to create custom profiles for specific compression requirements
- Reduced inventory costs (no need to stock multiple pre-formed gaskets)
Our state-of-the-art dispensing equipment can apply this specialized jet fuel resistant sealant to both metal housings (aluminum, titanium, steel) and specially prepared plastic substrates. The precision of the dispensing process ensures consistent material application, which is critical for maintaining both shielding effectiveness and resistance to jet fuel exposure across production volumes.
Design Considerations for Jet Fuel Environments
When designing components that will incorporate our jet fuel resistant sealant, several important factors should be considered to maximize performance and reliability. Taking these design elements into account early in the development process can help avoid costly redesigns and ensure optimal functionality in the final product.
Key design considerations include:
- Provide adequate flange width for proper gasket compression and sealing
- Include compression stops to prevent gasket over-compression
- Consider galvanic compatibility between housing materials and the conductive fillers in the sealant
- Ensure proper grounding for optimal EMI/RFI shielding performance
- Account for temperature cycling and its effect on gasket compression
- Design housing features to direct fuel flow away from gasket areas when possible
- Consider the effects of vibration on long-term gasket performance
- Incorporate appropriate surface preparation requirements in manufacturing documentation
Involving our engineering team early in your design process allows us to provide specific recommendations tailored to your application. Our expertise with jet fuel resistant sealant applications can help identify potential issues before they become costly problems, ensuring your component performs as expected in real-world conditions.
Why Choose Modus Advanced for Your Jet Fuel Resistant Sealing Needs
When selecting a partner for critical aerospace and defense components requiring jet fuel resistant sealant, Modus Advanced offers distinct advantages that enhance both quality and efficiency. Our vertically integrated capabilities allow us to handle multiple manufacturing processes under one roof, reducing lead times and quality risks associated with transferring components between vendors.
Our team includes highly qualified engineers who understand the unique challenges of aerospace applications. Over 10% of our staff are engineers who can provide valuable technical input during the design and manufacturing process. This engineering-first approach ensures that your components are not just manufactured to specification, but optimized for performance in real-world conditions where jet fuel exposure is a concern.
Additionally, our quality systems are aligned with the rigorous standards of the aerospace and defense industries:
- AS9100 Certification
- ISO 9001 Certification
- ITAR Compliance
- CMMC Compliance
- MIL-SPEC Materials Expertise
By partnering with Modus Advanced for your jet fuel resistant sealant applications, you gain access to both cutting-edge materials and the manufacturing expertise to apply them correctly. This combination helps ensure that your components perform reliably in the field, where failure is not an option.
Final Thoughts
In the high-stakes world of aerospace and defense engineering, component reliability is paramount. Our advanced jet fuel resistant sealant offers a superior solution for applications where both EMI/RFI shielding and resistance to aviation fuels are critical requirements. By combining these properties in a form-in-place material that can be precisely dispensed onto complex component geometries, we've created a solution that addresses one of the most persistent challenges in aerospace design.
Whether you're developing new systems or improving existing ones, selecting the right materials for gaskets and seals in fuel-adjacent environments can make the difference between component success and failure. Our specialized jet fuel resistant sealant, backed by Modus Advanced's engineering expertise and vertically integrated manufacturing capabilities, provides the performance and reliability your critical applications demand.
Partner with us to enhance your aerospace and defense components with advanced materials that stand up to the most demanding environments. Because when lives depend on your innovation, one day matters—and so does every material choice you make.