EMI Shielding in Medical Devices: Selecting the Right CHO-FORM Form-in-Place Material
November 27, 2024
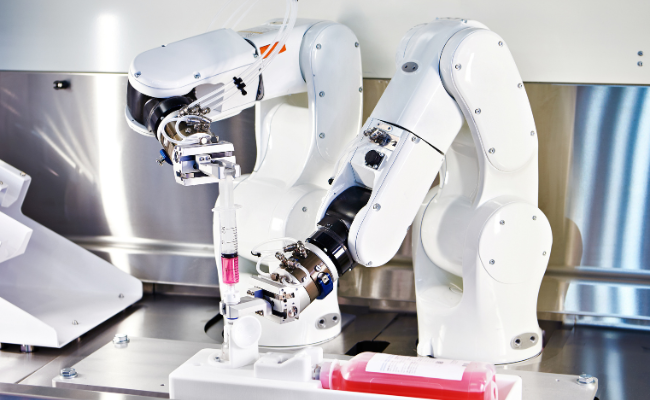
Manufactured with Speed and Precision
The manufacturing capabilities you need and the engineering support you want, all from a single partner.
Submit a DesignKey Points:
- Specialized EMI Shielding Solutions: CHO-FORM materials offer superior conductivity and shielding effectiveness for medical devices, with CHO-FORM 5526, 5513, and 5528 as top choices for optimal performance.
- Medical-Specific Challenges: EMI shielding in medical devices must address unique requirements including strict regulatory compliance, biocompatibility, sterilization compatibility, and high reliability standards.
- Comprehensive Quality Control: Implementing rigorous quality measures throughout the manufacturing process is crucial, including material controls, process validation, and regular testing to ensure consistent performance and regulatory compliance.
- Application-Specific Considerations: Different medical devices (imaging equipment, patient monitoring devices, surgical equipment, diagnostic devices) require tailored approaches to EMI shielding, considering factors like sterilization methods, cleaning protocols, and specific performance needs.
- Vertically Integrated Manufacturing: Partnering with experienced manufacturers like Modus Advanced provides access to ISO 9001 certified facilities, engineering expertise, and comprehensive technical support throughout the product lifecycle, ensuring optimal results in medical device EMI shielding applications.
In today's increasingly connected healthcare environment, effective EMI shielding is critical for ensuring medical device reliability and patient safety. The selection of appropriate materials and manufacturing processes can significantly impact device performance and regulatory compliance. This guide explores the optimal use of CHO-FORM materials in medical device applications.
Medical Device Industry Challenges
The medical device industry presents unique challenges that go beyond typical industrial applications. Understanding these specific requirements is essential for selecting and implementing EMI shielding solutions that meet both performance and regulatory demands.
Medical devices present unique challenges for EMI shielding:
- Strict regulatory compliance requirements
- Biocompatibility considerations
- Sterilization compatibility
- Cleaning and disinfection resistance
- High reliability requirements
- Precise electrical performance needs
Why CHO-FORM for Medical Devices?
CHO-FORM materials are particularly well-suited for medical device applications due to their excellent electrical properties, strong adhesion, and ability to be dispensed in small, precise beads. This makes them ideal for the increasingly compact and complex designs of modern medical equipment
Recommended CHO-FORM Materials
The selection of CHO-FORM materials for medical devices requires careful consideration of both performance requirements and healthcare-specific demands – this is where Modus shines. The recommendations from the Modus team are based on extensive experience in medical device applications and regulatory compliance requirements.
Ideal Choice: CHO-FORM 5526 (Ag Filled)
CHO-FORM 5526 has established itself as the preferred solution for medical device applications due to its outstanding electrical properties and processing characteristics. This material offers:
- Lowest volume resistivity (0.003 Ω-cm)
- Excellent shielding effectiveness (>90 dB)
- Soft and compliant (38 Shore A)
- Room temperature cure capability
- Clean processing characteristics
The reason this material isn’t often used is the price point. Most customers preferred to use one of the options laid out below as a more cost effective option that still meets the requirements they need.
Most Common Choice: CHO-FORM 5513 or 5528 (Ag/Cu Filled)
When applications demand enhanced mechanical durability while maintaining excellent electrical properties, CHO-FORM 5513 provides an excellent alternative solution:
- Superior electrical conductivity (0.004-0.005 Ω-cm)
- Excellent adhesion properties
- Better mechanical durability
- Thermal cure for fast processing
- Good overall performance balance
When applications demand superior EMI shielding in compact designs, CHO-FORM 5528 offers an excellent solution:
- Ideal for 5G telecommunication applications
- Small form factor for narrow walls and complex geometries
- Excellent environmental sealing and EMI shielding
- Reduces need for secondary gaskets, streamlining assembly
- Fast curing time and lightweight nature
- Suitable for uncontrolled environments
- Easy installation and intercompartmental isolation
Application-Specific Guidelines
Different medical devices present unique challenges that require careful consideration of material properties and design requirements.
Understanding these specific needs helps ensure optimal performance and regulatory compliance.
Medical Imaging Equipment
Modern imaging systems require exceptional EMI shielding to maintain image quality and system reliability. Key considerations for MRI, CT, and X-ray systems include:
- Choose CHO-FORM 5526, 5513, or 5528 for maximum shielding
- Consider housing design for proper grounding
- Implement rigorous quality control
- Validate sterilization compatibility
Patient Monitoring Devices
Monitoring devices must maintain reliable performance while ensuring patient safety. Important considerations include:
- Use CHO-FORM 5526, 5513, or 5528 for sensitive electronics
- Design for cleaning agent exposure
- Ensure consistent gasket compression
- Consider portable device requirements
Surgical Equipment
Surgical equipment faces unique challenges related to sterilization and reliability. Critical factors include:
- Material compatibility with sterilization
- Reliability under repeated cleaning
- Mechanical durability
- EMI protection for precision electronics
Diagnostic Devices
Diagnostic equipment requires careful attention to signal integrity and reliability. Key focus areas include:
- Signal integrity protection
- Environmental sealing
- Manufacturing repeatability
- Cost-effective production
Design Considerations for Medical Applications
Successful implementation of CHO-FORM materials in medical devices requires attention to various design aspects that impact performance, reliability, and regulatory compliance. The following guidelines help ensure optimal results.
1. Regulatory Compliance
Meeting regulatory requirements is fundamental to medical device success. Essential considerations include:
- Document material selection rationale
- Maintain traceability records
- Consider global regulations
- Plan for validation testing
2. Sterilization Compatibility
Sterilization requirements significantly impact material selection and design decisions. Key factors include:
- Validate steam autoclave exposure
- Test EtO sterilization effects
- Consider radiation sterilization
- Document all validation results
3. Cleaning and Disinfection
Long-term exposure to cleaning agents can affect material performance. Important considerations include:
- Test common cleaning agents
- Validate disinfection protocols
- Consider material degradation
- Document acceptable methods
4. Manufacturing Process
Consistent manufacturing processes are essential for regulatory compliance and reliable performance. Focus areas include:
- Implement cleanroom protocols
- Establish quality control measures
- Define acceptance criteria
- Maintain process documentation
Quality Control Requirements
Quality control in medical device manufacturing demands comprehensive documentation and consistent processes. A robust quality system should address the following areas:
1. Material Controls
Proper material management ensures consistency and traceability:
- Lot tracking
- Material certification
- Contamination prevention
- Storage controls
2. Process Validation
Validated processes are essential for regulatory compliance:
- Installation qualification
- Operational qualification
- Performance qualification
- Ongoing monitoring
3. Testing Requirements
Regular testing validates ongoing compliance with requirements:
- Electrical performance
- Physical properties
- Environmental exposure
- Aging effects
Case Study: Medical Imaging Equipment
Real-world applications provide valuable insights into successful implementation strategies. This case study examines how proper material selection and design practices led to successful outcomes in a demanding application.
A recent medical imaging system project faced several challenges:
- High shielding effectiveness requirements
- Steam sterilization compatibility needs
- Repeated cleaning resistance demands
- Long-term reliability requirements
Solution:
- Selected CHO-FORM 5526 for optimal performance
- Developed special cleaning validation protocol
- Implemented comprehensive quality system
- Established ongoing monitoring program
Results:
- Met all shielding requirements
- Passed sterilization validation
- Achieved cleaning compatibility
- Maintained consistent quality
Implementation Guidelines
Successful implementation requires attention to detail throughout the product lifecycle. These guidelines help ensure optimal results at each stage of development and production.
1. Planning Phase
Early planning and careful consideration of all requirements helps prevent issues during production:
- Define all requirements
- Consider regulatory needs
- Plan validation approach
- Document selection criteria
2. Development
Thorough development processes validate design decisions and manufacturing processes:
- Test material compatibility
- Validate processes
- Verify performance
- Document results
3. Production
Consistent production processes ensure reliable performance:
- Implement controls
- Monitor quality
- Maintain records
- Conduct regular reviews
Best Practices for Success
Following established best practices helps ensure consistent results and regulatory compliance. These guidelines address key aspects of medical device manufacturing.
Material Selection
Proper material selection is fundamental to long-term success:
- Choose highest purity materials
- Consider all processing requirements
- Validate compatibility
- Document decisions
Process Control
Consistent processes ensure reliable results:
- Implement cleanroom practices
- Control all variables
- Monitor critical parameters
- Maintain documentation
Quality Assurance
Comprehensive quality systems protect patient safety:
- Define acceptance criteria
- Implement testing programs
- Monitor performance
- Maintain records
Why Choose Modus Advanced for Medical Device Applications
Medical device manufacturing requires a partner who understands the importance of quality, cleanliness, and documentation. Modus Advanced's ISO 9001 certified facilities and experienced engineering team provide the expertise needed for successful medical device component manufacturing. Our focus on quality and process control makes us an ideal partner for medical device manufacturers.
Our vertically integrated manufacturing capabilities allow us to maintain strict control over quality and cleanliness throughout the production process. With over 10% of our staff being engineers, we provide extensive technical support during design and production phases. For medical device manufacturers, this means:
- Clean manufacturing environment
- Comprehensive documentation and traceability
- Expert DFM support from experienced engineers
- Consistent quality and process control
- Fast prototype and production capabilities
- ISO 9001 certified processes
We're ready when you are. Contact our team today to get started.