Understanding FDA, USP Class VI, and RoHS Compliance for Medical Gaskets
September 5, 2024
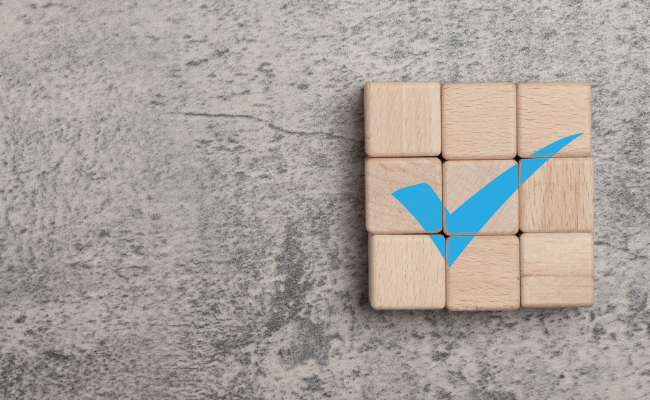
Manufactured with Speed and Precision
The manufacturing capabilities you need and the engineering support you want, all from a single partner.
Submit a DesignKey Points
- Material compatibility is crucial for medical-grade gaskets, ensuring they can withstand exposure to bodily fluids, medications, and sterilization processes without degrading or causing adverse reactions.
- Durability and dimensional stability are essential for long-term performance, as medical-grade gaskets must maintain their integrity and precise fit under various conditions to ensure device reliability and patient safety.
- Regulatory compliance and quality control are non-negotiable, with medical-grade gaskets needing to meet stringent standards like FDA regulations and ISO 10993 for biocompatibility, supported by robust traceability and documentation processes.
In medical device manufacturing, adhering to regulatory standards is crucial for ensuring patient safety and market success. For engineers and procurement managers, understanding FDA compliance, USP Class VI, and RoHS compliance is essential when selecting gaskets for medical devices.
As a trusted partner to many medical device manufacturers, we’re here to help. This comprehensive guide breaks down these important standards, their impact on gasket manufacturing, and provides detailed insights into testing procedures and material selection.
Get the complete guide to medically compliant seals for medical device manufacturers here!
FDA Compliance: Ensuring Safety in Medical Applications
The Food and Drug Administration (FDA) regulates medical devices, including gaskets. For manufacturers, meeting FDA CFR 177.2600 is vital. This regulation covers rubber materials used in medical applications.
Key Points of FDA CFR 177.2600:
- Material Composition: The regulation lists what ingredients can be used in rubber gaskets.
- Extraction Limits: This sets limits on how much material can leach out of the gasket over time.
- Testing Methods: The FDA requires specific tests to ensure compliance, including extraction tests with different solvents.
Using FDA-compliant gaskets is essential for medical device manufacturers to ensure long-term safety and reliability. Quality control measures are crucial in maintaining FDA compliance throughout the production process.
USP Class VI: The High Standard for Biocompatibility
First thing’s first: what is the USP? The United States Pharmacopeia (USP) is an independent, non-profit organization that establishes standards for the production of drugs, food ingredients, and dietary supplements for both humans and animals.
The USP focuses on ensuring purity, quality, strength, and consistency in biotechnology and pharmaceutical endeavors. The standards set by the USP are published in the USP-NF (United States Pharmacopeia-National Formulary), which combines the efforts of the USP and the National Formulary (NF).
The NF specifically lists formulas for commonly used pharmaceutical drugs within the United States. The USP-NF encompasses standards for a wide range of products, including medicines, dosage forms, drug substances, excipients, biologics, compounded preparations, medical devices, and dietary supplements. Importantly, these standards are enforceable by the U.S. Food and Drug Administration (FDA), playing a crucial role in ensuring the quality and safety of pharmaceutical and biotechnology products in the United States.
While FDA compliance covers many safety aspects, USP Class VI certification focuses on biocompatibility. This standard is one of the strictest in the medical device industry.
USP Class VI Testing Procedures:
- Systemic Injection Test: Assesses acute toxicity by injecting extracts of the material into mice and observing for systemic reactions over 72 hours.
- Intracutaneous Test: Evaluates local tissue reactions by injecting extracts into rabbit skin and monitoring for irritation over 72 hours.
- Implantation Test: Examines long-term tissue compatibility by implanting the material into rabbit muscle tissue and observing the reaction after 7 days.
Manufacturers must prepare samples according to USP guidelines and typically work with certified laboratories to conduct these tests. Results are evaluated against strict criteria to determine if the material passes USP Class VI requirements.
RoHS Compliance: Environmental Responsibility in Medical Manufacturing
The Restriction of Hazardous Substances (RoHS) Directive, initiated by the European Union (EU), now affects medical device manufacturers worldwide.
What is the RoHS Directive?
The RoHS Directive, also known as the EU RoHS Directive or the Hazardous Substances Directive, ensures that harmful substances are limited or removed from electrical and electronic equipment, including medical devices.
The RoHS Directive aims to reduce the environmental impact of electronic waste and protect human health. The European Union has set a global standard that many countries now follow, making RoHS compliance a crucial consideration for manufacturers.
Key aspects of RoHS compliance include:
- Restricted Substances: The directive limits the use of specific hazardous substances in electronic equipment.
- Compliance Documentation: Manufacturers must maintain records proving their products are RoHS compliant.
- CE Marking: RoHS compliant products sold in the EU must bear the CE mark.
It's worth noting that while similar, RoHS compliance and REACH compliance (another EU regulation) have distinct requirements. The REACH Regulation focuses on a broader range of chemicals and their use in various products.
Comparison Table: FDA, USP Class VI, and RoHS Requirements
Material Selection for Compliant Medical Gaskets
Choosing the right material is crucial for meeting compliance standards. Here's an overview of common materials used in medical gaskets:
- Silicone (Platinum-Cured):
- Compliance: Meets FDA, USP Class VI, and RoHS requirements
- Applications: Implantable devices, fluid handling systems
- EPDM (Ethylene Propylene Diene Monomer):
- Compliance: Can meet FDA and USP Class VI (specific grades)
- Applications: Sterilization equipment, water systems
- Fluoroelastomers (FKM):
- Compliance: Some grades meet FDA and USP Class VI
- Applications: Aggressive chemical environments, high-temperature applications
- PTFE (Polytetrafluoroethylene):
- Compliance: Meets FDA, USP Class VI, and RoHS
- Applications: Pharmaceutical processing, critical sealing applications
When selecting materials, consider specific application requirements, compliance needs (which standards must be met), and long-term performance.
Need more details on a particular material? We’ve got you covered – check out our material data sheets here.
The Importance of Multi-Standard Compliance
For medical device manufacturers, especially those serving global markets, meeting multiple compliance standards offers several benefits:
- Easier Regulatory Approval: Products with multi-compliant components often face fewer hurdles in the approval process.
- Simplified Supply Chain: Using gaskets that meet multiple standards can make inventory management easier.
- Enhanced Safety: Compliance with multiple strict standards often results in products that exceed minimum safety requirements.
- Market Flexibility: Multi-compliant components allow manufacturers to adapt products for different global markets, including those adhering to the RoHS Directive.
Future Trends in Compliant Medical Gasket Manufacturing
As medical technology advances, the importance of regulatory compliance in gasket manufacturing will grow. Emerging trends include:
- Biocompatibility for Long-Term Implants: As devices are designed for longer use within the body, gasket materials will need to meet stricter biocompatibility requirements.
- Nano-Material Considerations: The use of nanomaterials in medical devices may introduce new regulatory challenges, potentially affecting both RoHS compliance and biocompatibility standards.
- Global Standard Alignment: Efforts to align international standards may simplify compliance but could also introduce new requirements.
- Sustainability Focus: Future regulations may place greater emphasis on the environmental impact of medical devices and their components, potentially expanding the scope of the RoHS Directive.
Navigating Compliance for a Safer Future in Medical Gaskets
Understanding and implementing FDA, USP Class VI, and RoHS compliance is crucial for medical gasket manufacturers. At Modus Advanced, we specialize in guiding manufacturers through the complexities of these compliance requirements, ensuring that your medical gaskets are not only safe and effective but also positioned for success in global markets. Our expertise in material selection, rigorous testing procedures, and adherence to regulatory standards can help you navigate the challenges of compliance seamlessly.
Don’t leave your compliance to chance – partner with us to ensure your products meet the highest quality standards while enhancing your market competitiveness.
Contact Modus Advanced today to learn how we can support your journey toward achieving comprehensive compliance and driving innovation in your medical device solutions.