Everything You Need to Know About Thermal Protection Systems for Space Vehicles
April 9, 2025
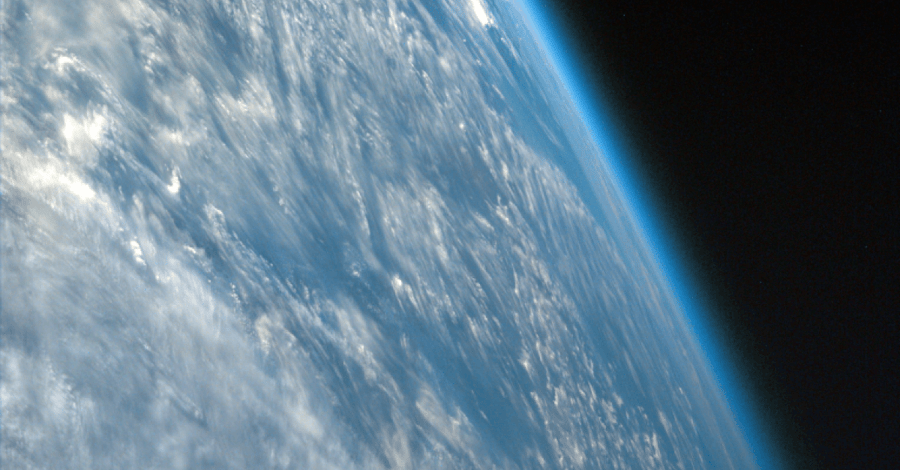
Manufactured with Speed and Precision
The manufacturing capabilities you need and the engineering support you want, all from a single partner.
Submit a DesignKey Points
- Thermal protection system requirements vary significantly based on mission profile and vehicle design
- Material selection is critical for ensuring spacecraft survival during atmospheric entry
- Different types of thermal protection systems serve distinct purposes in spacecraft design
- Testing and validation of thermal protection systems require specialized facilities and protocols
- Maintenance and inspection procedures are crucial for reusable thermal protection systems
Understanding thermal protection systems enables aerospace engineers to make informed decisions that protect billion-dollar missions and, more importantly, human lives during the most dangerous phases of spaceflight.
Read all our EMI Shielding resources in one spot.
Types of Thermal Protection Systems
The field of thermal protection systems has evolved significantly since the early days of spaceflight. Today's engineers have multiple options at their disposal, each suited to different mission requirements. Understanding the nuances of each system type is crucial for making informed design decisions.
Ablative Systems
Ablative thermal protection systems represent the most proven technology for extreme heat protection. These systems work through controlled material degradation, where the outer layer sacrifices itself to carry away heat energy. The degradation process creates a char layer that provides additional thermal protection while the gas products create a boundary layer that blocks incoming heat.
Key applications for ablative systems include:
Mission Type | Temperature Range | Example Vehicles |
Lunar Return | 4,000-5,000°F | Apollo, Orion |
Mars Entry | 3,500-4,500°F | |
LEO Return | 3,000-4,000°F | Dragon Capsule |
Modern ablative materials like PICA (Phenolic Impregnated Carbon Ablator) offer significant advantages over traditional carbon phenolic, including:
- 1/5 the density of traditional ablators
- Improved manufacturing consistency
- Better thermal shock resistance
- More predictable ablation characteristics
Reusable Ceramic Systems
Reusable ceramic thermal protection systems revolutionized spacecraft design with the Space Shuttle program. These systems utilize high-temperature ceramics that can withstand repeated thermal cycling without degradation.
The primary categories of reusable ceramic systems include:
Type | Material | Max Temp | Primary Use |
RCC (Reinforced Carbon-Carbon) | Carbon fiber in carbon matrix | 4,000°F | Leading edges |
HRSI (High-temperature Reusable Surface Insulation) | Silica tiles | 2,300°F | Large surface areas |
LRSI (Low-temperature Reusable Surface Insulation) | Silica tiles | 1,500°F | Lower heat zones |
Manufacturing considerations for reusable systems demand exceptional precision:
- Surface coating uniformity affects thermal properties
- Attachment systems must accommodate thermal expansion
- Gap fillers require precise sizing and installation
- Quality control standards exceed typical aerospace requirements
Learn more about our Design for Manufacturability (DfM) review process here.
Flexible Insulation Systems
Flexible insulation systems provide thermal protection for areas experiencing moderate heating rates. These systems offer significant advantages in terms of installation and maintenance while providing adequate thermal protection for many applications.
Advanced flexible systems incorporate multiple layers:
- Outer ceramic fabric layer for thermal resistance
- Insulation layers (multiple)
- Inner gas barrier
- Attachment system
Table of applications and capabilities:
System Type | Temperature Limit | Key Benefits | Primary Applications |
AFRSI | 1,500°F | Easy installation | Large surface areas |
FRSI | 700°F | Lightweight | Low-heat regions |
Multi-layer | 2,000°F | Customizable | Complex geometries |
Let's examine the comparative properties of each system type:
System Type | Temperature Range | Reusability | Weight | Cost | Maintenance |
Ablative | > 3,000°F | Single Use | High | Moderate | Minimal |
Reusable Ceramic | 1,000-3,000°F | Multiple | Moderate | High | Extensive |
Flexible Insulation | < 1,000°F | Multiple | Low | Low | Moderate |
Material Properties and Applications
Different thermal protection system materials offer unique advantages for specific applications. Here's a comprehensive breakdown:
Material Category | Primary Applications | Temperature Limit | Key Advantages | Limitations |
Carbon-Phenolic | Atmospheric Entry | 6,000°F | Highest temperature resistance | Single use |
Reinforced Carbon-Carbon | Leading Edges | 4,000°F | Reusable, good strength | Oxidation sensitive |
Ceramic Tiles | Large Surface Areas | 2,500°F | Lightweight, reusable | Brittle |
Flexible Blankets | Lower-temp Zones | 1,500°F | Easy installation | Limited temp range |
Manufacturing Considerations
The manufacturing process for thermal protection systems demands exceptional precision, rigorous quality control, and specialized facilities. Success requires careful attention to environmental conditions, process parameters, and material handling throughout the entire manufacturing cycle.
Environmental Controls
Manufacturing facilities must maintain strict environmental parameters:
Parameter | Requirement | Impact on Process |
Temperature | 70°F ±5°F | Material cure rates |
Humidity | 45% ±5% | Material properties |
Cleanliness | Class 100,000 | Contamination prevention |
Air Flow | HEPA filtered | Particle control |
Material Preparation Process
Raw material preparation represents a critical first step in thermal protection system manufacturing. Each material type requires specific handling procedures:
Ablative Materials:
- Precursor material conditioning (24-48 hours)
- Precise weighing and mixing of components
- Controlled temperature processing
- Vacuum degassing
- Pre-form creation
Ceramic Systems:
- Powder characterization
- Slurry preparation
- pH and viscosity control
- Binder addition
- Aging process
Flexible Systems:
- Fiber preparation
- Coating application
- Layer assembly
- Vacuum processing
- Pre-installation conditioning
Component Formation
The formation of thermal protection system components requires specialized equipment and precise process control:
Process Step | Critical Parameters | Quality Checks |
Molding | Temperature, pressure, time | Density, void content |
Machining | Tool wear, speed, feed | Dimensional, surface finish |
Coating | Thickness, uniformity | Coverage, adhesion |
Curing | Time-temperature profile | Hardness, shrinkage |
Advanced Manufacturing Technologies
Modern thermal protection system manufacturing increasingly incorporates advanced technologies:
Automated Systems:
- 5-axis CNC machining for complex geometries
- Robotic coating application
- Automated inspection systems
- Digital process monitoring
Process Control:
- Real-time parameter monitoring
- Statistical process control
- Automated environmental logging
- Digital twin modeling
System Integration
The integration phase requires careful attention to interfaces and attachments:
Integration Step | Key Considerations | Validation Methods |
Surface Preparation | Cleanliness, roughness | Visual, profilometry |
Adhesive Application | Coverage, thickness | Ultrasonic testing |
Component Placement | Alignment, gaps | Laser scanning |
Cure Monitoring | Temperature profile | Thermocouple data |
Quality Assurance
Manufacturing quality assurance involves multiple inspection points:
Pre-Process Verification:
- Material certification review
- Equipment calibration check
- Environmental parameter verification
- Personnel qualification confirmation
In-Process Controls:
- Real-time parameter monitoring
- Statistical process control
- Non-conformance management
- Documentation requirements
Final Validation:
- Non-destructive testing
- Dimensional verification
- Performance testing
- System-level validation
Read more: What’s the Cost of Poor Quality?
Documentation Requirements
Manufacturing documentation must meet stringent aerospace standards:
Document Type | Content | Purpose |
Process Records | Parameters, times | Traceability |
Inspection Reports | Measurements, results | Verification |
Non-conformance Reports | Issues, resolutions | Quality control |
Certification Packages | Test results, approvals | Compliance |
Understanding and controlling these manufacturing considerations ensures consistent production of high-quality thermal protection systems that meet the demanding requirements of space applications.
Working with Modus Advanced
At Modus Advanced, we understand the critical nature of thermal protection systems in aerospace applications. Our vertically integrated manufacturing capabilities include:
Capability | Description | Benefit |
Engineering Support | >10% engineering staff | Expert design guidance |
Quality Systems | Aerospace-grade quality | |
Manufacturing | Multiple processes in-house | Faster turnaround |
Testing | Comprehensive facilities | Validated performance |
Design Your Next-Generation Thermal Shield
Thermal protection system design and implementation remain critical challenges in spacecraft development. Success requires careful material selection, thoughtful system integration, and rigorous testing. With proper attention to these factors and partnership with experienced manufacturers like Modus Advanced, engineers can develop thermal protection systems that ensure mission success in the harshest environments of space exploration.
Ready to discuss your thermal protection system needs? Contact our engineering team today.