FIP Gaskets for Medical Device Sealing and Environmental Protection
August 14, 2024
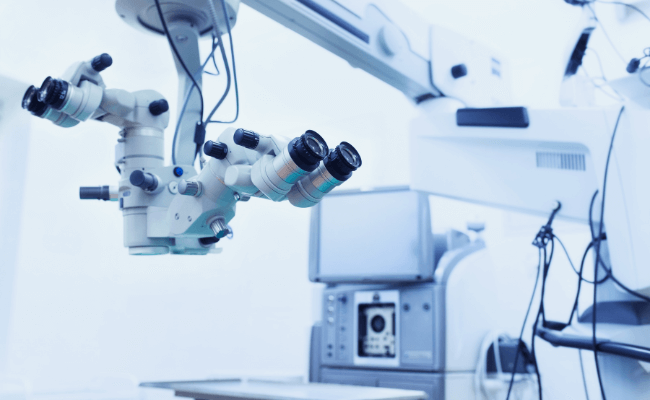
Manufactured with Speed and Precision
The manufacturing capabilities you need and the engineering support you want, all from a single partner.
Submit a DesignKey Points
- FIP gaskets offer a custom fit for medical devices, ensuring precise sealing that conforms to device contours, eliminating gaps, and preventing leaks, which is crucial for maintaining device integrity and patient safety.
- Enhanced durability and chemical resistance make FIP gaskets ideal for harsh medical environments, as they withstand extreme temperatures and chemicals, ensuring long-term reliability and reducing the need for frequent replacements.
- Partnering with Modus Advanced streamlines the manufacturing process, reducing lead times and costs while maintaining high-quality standards, enabling rapid development from prototype to production for medical device manufacturers.
When it comes to medical device manufacturing, precision isn't just a goal – it's a lifeline. The performance of medical devices directly impacts patient safety, making the role of seals crucial.
Among the various sealing solutions, Form-in-Place (FIP) gaskets stand out as a versatile option, especially when it comes to static seals. In this article, we’ll explore the importance of FIP gaskets, the various types of seals used in medical devices, and why partnering with Modus Advanced can elevate your manufacturing process.
Read the complete guide to medically compliant seals for medical device manufacturers!
The Critical Role of Medical Seals
Medical seals are the unsung heroes of medical devices, ensuring that everything from pumps to implants functions seamlessly. Their primary roles include:
- Preventing Leaks: Seals maintain the integrity of fluid systems, crucial for devices like IV pumps and blood separators. A static seal ensures that internal pressure is contained, preventing leaks that could compromise device functionality.
- Controlling Fluid Flow: Accurate medication delivery relies on seals that regulate the flow of fluids. In static sealing situations, the seal material must be chosen carefully to ensure chemical compatibility and maintain precise control.
- Protecting Internal Components: Seals guard against contamination, ensuring that sensitive internal parts remain safe from external environmental factors. This protection is vital for maintaining the longevity and reliability of medical devices.
Understanding Different Types of Seals for Medical Devices
When it comes to medical devices, not all seals are created equal. Here’s a breakdown of the most common types:
1. Static Seals
Static seals are designed for applications where there is no relative motion between the sealing surfaces. These seals are essential in devices such as:
- Pumps
- Blood Separators
- Oxygen Concentrators
Their primary function is to maintain a barrier between stationary surfaces, preventing leaks and ensuring device reliability. O-rings are a popular choice for static seals due to their effectiveness and cost-efficiency. Static axial seals, where sealing occurs parallel to the seal centerline, and static radial seals, which involve inner and outer surfaces, are common static sealing applications.
In static sealing, the mating surfaces must be precisely aligned to ensure a proper seal. The seal surfaces play a critical role in maintaining the integrity of the device, preventing any breach that could lead to contamination or malfunction.
2. Reciprocating Seals
Unlike static seals, reciprocating seals are used in applications with linear motion. These seals are found in:
- Endoscopes
- Trocar Seals
The design of reciprocating seals must accommodate the complexities of instrument manipulation, ensuring that they function smoothly while maintaining a secure seal. Dynamic seals, which are often used in conjunction with reciprocating seals, must handle the relative motion between components, requiring careful consideration of the seal material and design.
3. Hermetic Seals
Hermetic seals create a fully enclosed barrier, making them essential for medical implants. These seals prevent corrosion and protect sensitive components from contamination, ensuring the longevity and reliability of implants. The ability to maintain a hermetic seal is crucial in environments where even the slightest breach could lead to significant consequences.
4. Seals for Surgical Instruments
Surgical instruments face unique challenges, including exposure to harsh chemicals and sterilization processes. Silicone O-rings are often used in these applications because of their:
- Biocompatibility: Safe for use in medical applications.
- Temperature Resistance: Able to withstand extreme conditions.
These properties make silicone O-rings ideal for maintaining the integrity of surgical instruments. In addition to O-rings, square rings are sometimes used for their ability to provide a more robust seal in certain applications, offering enhanced resistance to wear and tear.
5. Seals for IV Pumps and Dispensers
In IV pumps and dispensers, the role of seals is critical. They ensure precise control of fluid flow, which is vital for accurate medication administration. A reliable seal prevents leaks and maintains the correct dosage, directly impacting patient care. Static sealing applications in these devices require a careful balance of seal material and design to ensure that the inner and outer surfaces are adequately protected.
The Advantages of Form-in-Place Gaskets
FIP gaskets offer several compelling benefits that make them an ideal choice for medical device applications:
1. Custom Fit for Every Application
FIP gaskets are tailored to meet the specific requirements of each device. The in-place curing process allows the gasket to conform perfectly to the device’s contours, eliminating gaps and potential leakage points. This custom fit ensures that the sealing surfaces are fully engaged, providing a reliable barrier against contamination.
2. Enhanced Durability
FIP gaskets are designed to withstand harsh environments, exhibiting exceptional resistance to chemicals and temperature extremes. Their durability ensures long-term reliability, reducing the need for frequent replacements. This resistance to high temperature and chemical compatibility makes FIP gaskets a preferred choice in static sealing applications.
3. Streamlined Manufacturing Process
Using FIP gaskets can significantly reduce lead times and costs associated with manufacturing. Their efficiency in custom and prototype applications allows for rapid development and deployment of new medical devices. By reducing the complexity of the manufacturing process, FIP gaskets enable manufacturers to bring products to market faster without sacrificing quality.
Partnering with Modus Advanced
Choosing the right sealing solution is crucial for the success of any medical device. This is where Modus Advanced shines. We are committed to quality and employ rigorous quality control measures to ensure the performance and reliability of our products. Our focus on expertise and innovation keeps us at the forefront of technological advancements, enabling us to provide cutting-edge solutions tailored to your needs.
At Modus, we don't just provide sealing solutions; we offer a partnership that transforms your manufacturing process. Our team is dedicated to being a trusted partner in the medical device industry, offering tailored sealing solutions that enhance device performance and patient safety.
Our rapid prototyping and quick-turn capabilities ensure that you stay ahead of the curve, bringing life-changing products to market sooner. And with fewer vendors to juggle, you enjoy reduced risks and enhanced security standards, all under one roof. Whether you're dealing with static sealing situations or dynamic seals, we have the expertise to guide you through the process.
So, why settle for ordinary when you can have exceptional? Contact Modus Advanced today and let us be the catalyst that propels your medical device manufacturing to new heights. With our cutting-edge solutions and unwavering commitment to quality, the sky's the limit.