High Temperature Gasket: Durability and Performance in Extreme Military Environments
April 24, 2025
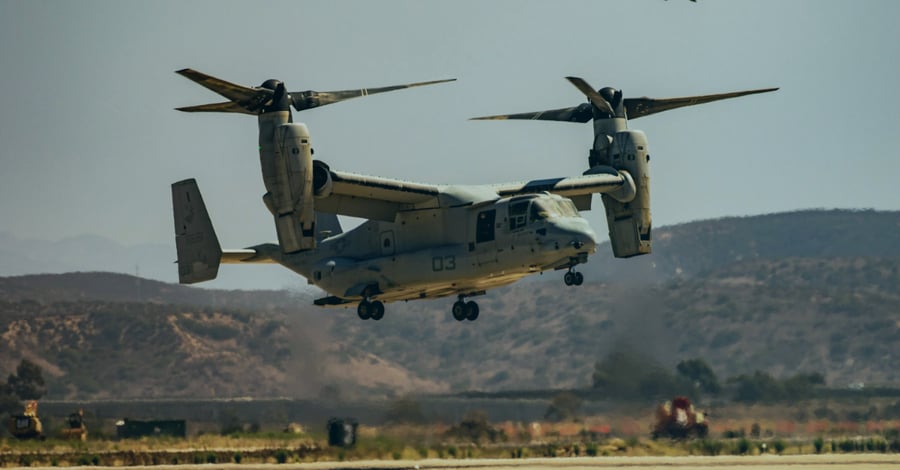
Manufactured with Speed and Precision
The manufacturing capabilities you need and the engineering support you want, all from a single partner.
Submit a DesignKey Points
- RF gaskets in military applications face extreme temperature ranges from -65°F to over 500°F, requiring specialized high temperature gasket materials for optimal performance
- Material selection criteria include thermal stability, electromagnetic shielding effectiveness, corrosion resistance, and compression force requirements
- Silicone-based elastomers with silver, nickel, and graphite fillers provide excellent high temperature gasket performance up to 500°F
- Form-in-place gasket technology offers advantages for complex military electronics with tight spaces and intricate geometries
- Vertically integrated manufacturing processes significantly reduce lead times and quality issues for mission-critical defense applications
RF gaskets might seem like a small component in complex military systems, but their reliability under extreme conditions directly impacts mission success. These specialized gaskets play a critical role in protecting sensitive electronics from electromagnetic interference (EMI) while maintaining environmental seals in some of the world's most demanding operational conditions.
Military environments push components to their absolute limits, with temperature ranges spanning from the frigid -65°F of high-altitude operations to the scorching 500°F+ encountered in engine compartments and weapons systems. High temperature gaskets for military applications must meet crucial specifications that ensure communications remain secure, guidance systems stay functional, and mission-critical equipment operates flawlessly when lives depend on it.
Read the Guide: Engineer's Complete Guide to EMI Shielding in Aerospace & Defense Applications
Critical Military Environmental Challenges for RF Gaskets
Military equipment faces environmental extremes that commercial products rarely encounter. Each environment presents unique challenges for designing high temperature gaskets and material selection.
Desert operations expose equipment to temperature swings exceeding 100°F within a 24-hour period, combined with abrasive sand that can compromise gasket seals. High temperature gasket materials must maintain their sealing properties despite these thermal cycles and particulate intrusion.
Naval environments combine humidity, salt spray, and constant vibration, creating an ideal environment for galvanic corrosion between dissimilar metals. RF gaskets in these applications require excellent corrosion resistance while maintaining electrical conductivity.
Aerospace applications introduce another level of complexity with rapid pressure changes, extreme cold at altitude, and the potential for ozone exposure. High temperature gasket solutions for these applications must perform across broader temperature ranges without losing compression set or shielding effectiveness.
The combination of these environments with strict electromagnetic compatibility requirements makes military-grade RF gaskets a specialized engineering challenge requiring advanced materials and manufacturing processes.
Material Performance Considerations for Military RF Gaskets
When selecting high temperature gasket materials for military applications, engineers must consider multiple performance factors simultaneously. The table below outlines critical performance requirements and their importance:
Performance Factor | Importance in Military Applications | Key Considerations |
Temperature Range | Critical for operational reliability | Must maintain properties from -65°F to 500°F+ |
EMI Shielding | Essential for communications security | 60-100+ dB attenuation across specified frequency ranges |
Environmental Sealing | Prevents system failure | IP67/IP68 ratings for water and dust intrusion |
Corrosion Resistance | Extends operational life | Galvanic compatibility with housing materials |
Compression Set | Maintains sealing under vibration | <30% ideal for long-term performance |
Chemical Resistance | Protects against fuels/oils | Resistance to JP-8, hydraulic fluids, lubricants |
Balancing these requirements often involves trade-offs. For instance, high temperature gaskets with optimal EMI shielding might require higher compression forces, potentially limiting its use in lightweight components with thin walls.
High Temperature Gasket Materials for Military Applications
Material selection directly impacts RF gasket performance in extreme environments. The most common high temperature gasket materials for military applications include:
Silicone-Based Elastomers with Conductive Fillers
Here's a table created from the information about silicone-based elastomers with conductive fillers:
Filler Type | Temperature Rating | Shielding Effectiveness | Key Advantages | Best Applications | Example Materials |
Silver-Aluminum | Up to 500°F | Exceeding 80 dB | Minimal compression set, excellent high-temperature performance | High-temperature military environments requiring reliable shielding | Parker Chomerics CHOFORM 5575 |
Nickel-Graphite | Up to 400°F | Good | Economical, excellent aluminum compatibility, corrosion resistant | Aerospace applications where galvanic corrosion is a concern | Parker Chomerics CHOFORM® |
Silver-Copper | Up to 450°F | Highest | Maximum EMI protection | Applications requiring maximum shielding with limited salt spray exposure | Parker Chomerics CHO-SEAL® |
Silicone remains the foundation for many high temperature gasket applications due to its inherent temperature stability. For military applications, these elastomers are enhanced with various conductive fillers to provide EMI shielding while maintaining their environmental sealing properties.
Silver-aluminum filled silicones offer exceptional high temperature gasket performance, maintaining conductivity up to 500°F with minimal compression set issues. Materials like Laird's SNL70-HXP and Nolato's specific formulations provide excellent shielding effectiveness exceeding 100 dB across a wide frequency range.
Nickel-graphite filled silicones provide a more economical alternative with excellent aluminum compatibility, particularly important for aerospace applications where galvanic corrosion is a concern. These high temperature gasket materials maintain their properties up to 400°F in continuous operation.
Silver-copper filled options offer the highest shielding effectiveness, though with greater susceptibility to environmental corrosion. They excel in applications where maximum EMI protection is required and exposure to salt spray is limited.
Each of these materials offers distinct advantages depending on the specific application requirements and environmental exposures.
Fluorosilicone Compounds
Fluorosilicone compounds represent a specialized high temperature gasket solution for military applications with exposure to jet fuels, hydraulic fluids, and other harsh chemicals. These materials can withstand temperatures up to 400°F while providing excellent resistance to aviation fluids.
Their primary advantage lies in maintaining seal integrity when exposed to chemicals that would degrade standard silicones. This makes them ideal for applications in aircraft engine compartments, fuel systems, and other areas where fluid exposure is likely.
Advanced Elastomer Composites
For the most demanding applications, advanced elastomer composites combine multiple materials to achieve extraordinary performance. These specialized high temperature gasket materials can maintain their properties at extremes approaching 600°F while providing excellent compression set resistance.
These advanced materials often incorporate fluoropolymers and specialized silicones with proprietary filler systems to achieve their exceptional performance. The trade-off comes in higher material costs and more demanding manufacturing processes.
Manufacturing Techniques for Military-Grade RF Gaskets
The manufacturing process significantly impacts RF gasket performance in extreme environments. Military applications often require precision manufacturing to ensure consistent performance across production batches.
Form-in-Place (FIP) Gasket Technology
Form-in-place technology offers significant advantages for complex military electronics where space constraints and intricate geometries are common. This process dispenses a conductive elastomer directly onto the housing, creating a precisely positioned high temperature gasket that conforms exactly to the surface.
FIP gaskets can be dispensed on walls as narrow as 0.025" (0.76 mm), allowing for maximum use of available space in compact military electronics. This precision becomes particularly valuable in applications like radar systems, secure communications equipment, and electronic warfare modules where every millimeter matters.
The process allows for consistent gasket height control, typically ranging from 0.8mm to 2.0mm depending on the specific application requirements. This precision ensures reliable compression and EMI shielding performance even under extreme conditions.
For military applications, materials like Parker Chomerics CHOFORM® provide excellent high temperature gasket performance while offering the design flexibility of the FIP process. These materials maintain their conductivity and compression set resistance even after thermal cycling.
Die-Cut Gaskets
Die-cutting remains an efficient production method for less complex geometries and higher volume applications. This traditional approach provides excellent consistency across production batches, ensuring reliable performance in the field.
For high temperature gasket applications, precision die-cutting allows for tight tolerance control, typically ±0.005" for critical dimensions. This precision ensures consistent compression and reliable EMI shielding performance.
The die-cutting process works particularly well with silicone sheet materials that have been loaded with conductive fillers. Materials like silicone-impregnated wire mesh, conductive fabric over foam, and solid conductive elastomers can all be precisely converted through die-cutting processes.
Design Considerations for Extreme Environment Applications
Successful implementation of high temperature gasket solutions requires careful design consideration beyond just material selection. Several critical factors directly impact long-term reliability in military applications:
Compression Force Management
Proper compression force management prevents gasket damage while ensuring effective sealing and shielding. Military designs often incorporate:
- Mechanical compression stops to prevent gasket over-compression during assembly
- Careful fastener spacing to ensure uniform compression across the gasket
- Design features that account for thermal expansion differences between housing materials and gaskets
Most high temperature gasket materials designed for military applications require 10-50% compression for optimal performance.
Galvanic Compatibility
The combination of dissimilar metals in the presence of moisture can accelerate corrosion, potentially compromising both the gasket and the housing. This consideration is particularly important for naval and coastal deployments.
When selecting a high temperature gasket with conductive fillers, engineers must consider the galvanic potential between the filler materials and the housing metals. Nickel-graphite fillers offer excellent compatibility with aluminum housings, while silver fillers may require additional protective measures in certain environments.
Environmental Sealing Integration
Many military applications require both EMI shielding and environmental sealing from the same gasket. This dual functionality demands careful design:
- Proper groove dimensions to ensure adequate material for compression
- Consideration of fluid ingress paths under various pressure differentials
- Integration with overall system IP rating requirements
For high temperature gasket applications requiring both functions, form-in-place technology often provides the most reliable solution by creating a continuous seal that follows complex geometries precisely.
Testing and Validation for Military RF Gaskets
Military applications demand rigorous testing to validate performance under extreme conditions. Standard testing protocols for high temperature gasket solutions include:
Thermal Cycling
Repeated cycling between temperature extremes (typically -65°F to 500°F for many applications) reveals how the gasket will perform over time. Key measurements include:
- Changes in compression set after thermal cycling
- Shielding effectiveness before and after thermal stress
- Visual inspection for cracking, separation from substrates, or other physical degradation
This testing is particularly important for high temperature gasket materials used in aerospace applications where rapid temperature changes are common.
Vibration and Shock Testing
Military equipment faces extreme mechanical stresses during operation. Vibration testing (often to MIL-STD-810 specifications) ensures the gasket maintains its sealing and shielding functions despite these challenges.
Long-term vibration testing, combined with thermal cycling, provides the most realistic assessment of how the high temperature gasket will perform over the life of the equipment.
Salt Spray and Humidity Testing
For naval and coastal deployments, resistance to corrosion is critical. Salt spray testing according to ASTM B117 evaluates how the gasket and its interface with the housing will withstand prolonged exposure to corrosive environments.
These tests highlight potential galvanic issues between gasket fillers and housing materials that might not be apparent under normal conditions but could lead to premature failure in the field.
The Modus Advanced Advantage for Military RF Gaskets
At Modus Advanced, we understand that high temperature gasket solutions for military applications require specialized materials and processes. Our approach combines engineering expertise, vertical integration, and quality focus to deliver RF gasket solutions that perform under the most extreme conditions.
Our engineering team, which makes up more than 10% of our staff, specializes in designing RF shielding solutions for extreme environments. This expertise allows us to recommend the optimal high temperature gasket material and manufacturing process for your specific application requirements.
Our vertically integrated manufacturing approach eliminates the traditional multi-vendor process that can introduce quality issues and extend lead times. By handling metal machining, FIP gasket dispensing, and quality validation under one roof, we reduce risks and accelerate production schedules.
Our quality systems, including AS9100, ISO 9001 certifications, and ITAR compliance, ensure that every high temperature gasket solution meets the stringent requirements of military applications. We maintain a 99.5% quality rate goal across all our manufacturing processes.
Engineered Solutions for Mission Success
RF gaskets in extreme military environments require specialized engineering attention and material selection. The high temperature gasket solutions described in this article represent just a portion of the available options for meeting these challenging requirements.
Working with an experienced manufacturing partner who understands both the technical requirements and the mission-critical nature of these components can make the difference between system success and failure in the field. For military applications where performance means protecting lives and ensuring mission success, having the right partner matters as much as having the right materials.
When your project requires a high temperature gasket solution that performs reliably in the world's most challenging environments, partner with Modus Advanced. Our engineering-first approach and vertically integrated manufacturing ensure your RF gaskets will perform when it matters most. Contact our engineering team today to discuss your specific requirements.