The Interplay Between Solar Reflectance and Thermal Emittance
January 30, 2025
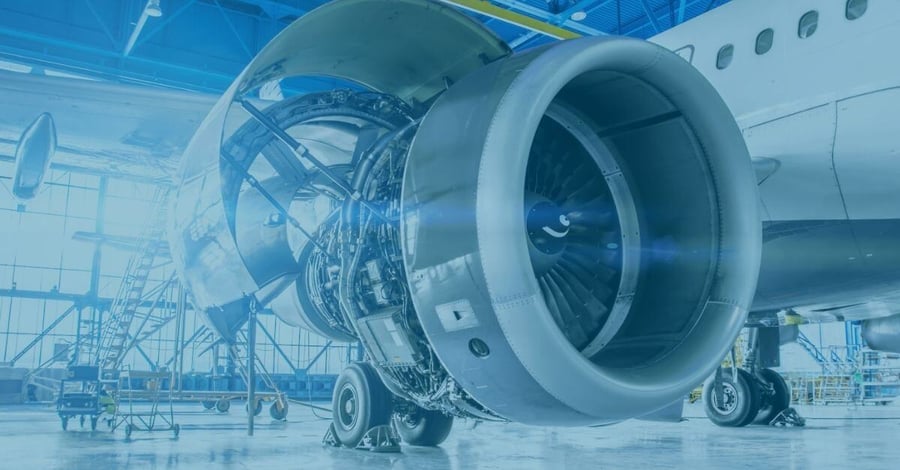
Manufactured with Speed and Precision
The manufacturing capabilities you need and the engineering support you want, all from a single partner.
Submit a DesignSolar Reflectance and Thermal Emittance
Solar reflectance and thermal emittance work together like a choreographed balancing act: while solar reflectance determines how much solar energy a surface will absorb (with higher reflectance meaning less energy absorbed), thermal emittance controls how effectively that surface can radiate heat away into space. The ratio between these two properties ultimately determines a material's equilibrium temperature in space - for example, a surface with high solar reflectance but low thermal emittance might still overheat because it can't efficiently release the small amount of heat it does absorb, while a surface with lower solar reflectance but very high thermal emittance might maintain an acceptable temperature by quickly radiating away the heat it absorbs.
Key Points
- Solar reflectance and thermal emittance are critical properties that affect spacecraft thermal management and performance, influencing solar heat absorption, heat transfer, surface temperature, and infrared heat dissipation.
- These properties have a complex interplay that engineers must carefully balance in aerospace applications
- Surface coatings and materials can be strategically chosen to optimize both properties
- Understanding how environmental factors impact these properties is crucial for maintaining consistent surface temperature and ensuring long-term mission success.
- Testing and measurement standards exist to properly characterize these properties
Critical Considerations for Aerospace Applications
In the unforgiving environment of space, proper thermal management can mean the difference between mission success and catastrophic failure. Two of the most critical properties that aerospace engineers must understand and control are solar reflectance and thermal emittance.
These properties work in concert to determine how spacecraft interact with solar radiation and manage their thermal loads.
Understanding the Fundamentals
Before diving into the complex relationship between solar reflectance and thermal emittance, it's essential to understand what each property represents and how they function independently.
Solar reflectance measures a material's ability to reflect solar radiation across the solar spectrum. A higher solar reflectance means less solar energy is absorbed by the material. This property is particularly crucial for spacecraft surfaces that face direct solar radiation.
Thermal emittance indicates how effectively a surface can emit thermal energy as infrared radiation. Materials with high thermal emittance are better at radiating heat away from themselves. This becomes especially important in space, where radiation is the only mechanism available for heat dissipation.
The Critical Interplay
The relationship between solar reflectance and thermal emittance creates a delicate balance that aerospace engineers must carefully manage. Here's how these properties interact:
- A high solar reflectance reduces heat absorption from solar radiation
- High thermal emittance allows better heat dissipation through radiation
- The ratio between these properties affects equilibrium temperature
- Environmental degradation can impact both properties differently
- Material selection must optimize both properties for specific mission requirements
Solar Reflectance and Heat Absorption
A high solar reflectance acts as your first line of defense in thermal management by reducing the initial heat absorption from solar radiation. Like a mirror deflecting light, a surface with high solar reflectance bounces more solar energy back into space before it can be converted to heat within the material, significantly reducing the thermal load that needs to be managed.
Thermal Emittance and Cooling
High thermal emittance serves as the cooling system, determining how effectively a material can radiate absorbed heat back into space. Think of it as opening a pressure release valve - the higher the thermal emittance, the wider that valve opens, allowing more heat to escape through infrared radiation, which is particularly crucial in the vacuum of space where convection and conduction aren't available for cooling.
Material Equilibrium
The ratio between solar reflectance and thermal emittance is what ultimately determines a material's equilibrium temperature in space. This relationship is similar to balancing water in a sink - solar reflectance controls how fast water flows in through the faucet, while thermal emittance controls how quickly it drains out, and together they determine the steady-state water level (or in this case, temperature).
Environmental Degradation
Environmental degradation can wreak havoc on this delicate balance because space conditions affect reflectance and emittance properties through different mechanisms. For instance, UV radiation might primarily degrade a coating's solar reflectance while atomic oxygen exposure could more severely impact its thermal emittance, creating a shifting thermal management challenge over time.
Material Selection
Material selection becomes a complex optimization problem where engineers must balance both properties not just for day-one performance but for the entire mission lifetime. This often means choosing materials that might not have the absolute best initial properties but maintain a more stable ratio of solar reflectance and thermal emittance throughout years of space exposure, ensuring consistent thermal management across the mission duration.
Understanding this interplay is crucial because spacecraft thermal control often requires different combinations of these properties for different surfaces and mission phases.
Factors Affecting Performance
Multiple factors can influence both solar reflectance and thermal emittance in aerospace applications. These variables must be carefully considered during design and material selection.
Surface Properties:
- Surface roughness affects both properties: Surface roughness creates microscopic variations in the material surface that can either enhance or inhibit both solar reflectance and thermal emittance by changing how radiation interacts with the surface at different wavelengths.
- Oxidation can alter surface characteristics over time: Oxidation gradually changes a material's surface chemistry and optical properties, potentially creating oxide layers that can significantly alter both the solar reflectance and thermal emittance characteristics from their initial design specifications.
- Contamination from outgassing or external sources: Contamination, whether from spacecraft outgassing or external debris, can create thin films or deposits on surfaces that interfere with both properties, often reducing solar reflectance while simultaneously altering the surface's ability to emit thermal radiation.
- Micrometeoroid impacts can degrade surface properties: Micrometeoroid impacts create localized damage zones that can drastically change surface properties by generating craters, fractures, and altered surface morphology, leading to decreased performance in both solar reflectance and thermal emittance in the affected areas.
Environmental Conditions:
- Atomic oxygen exposure in low Earth orbit: Atomic oxygen exposure in low Earth orbit aggressively erodes exposed surfaces through chemical reactions, particularly affecting polymeric materials and coatings that are critical for maintaining specific solar reflectance and thermal emittance properties.
- UV radiation effects over time: UV radiation gradually breaks down chemical bonds in materials and coatings over time, leading to color changes and degradation that can significantly alter both the solar reflectance and thermal emittance properties of exposed surfaces.
- Thermal cycling impacts: Thermal cycling causes repeated expansion and contraction of materials as spacecraft move between sunlight and shadow, potentially leading to coating delamination, surface cracking, or material fatigue that affects thermal control properties.
- Space debris considerations: Space debris poses an ongoing risk of surface damage through impacts and material deposits, which can create localized hot spots or cold spots by changing the solar reflectance and thermal emittance properties in affected areas.
Read how this DoD contractor improved product quality by partnering with Modus Advanced.
The Role of Coatings
Surface coatings play a vital role in controlling solar reflectance and thermal emittance for aerospace applications. Modern coating technologies offer engineers precise control over these properties.
Common Coating Types:
White Thermal Control Coatings
White thermal control coatings use ceramic or zinc oxide particles to achieve both high solar reflectance (typically 0.8-0.9) and high thermal emittance (0.8-0.9), making them excellent for general temperature control in space applications where heat rejection is crucial.
Optical Solar Reflectors
Optical solar reflectors, typically consisting of silver or aluminum backing with specialized glass or quartz covers, provide extremely high solar reflectance (>0.9) while maintaining high thermal emittance (>0.8), offering superior thermal control but at higher cost and complexity.
Metallic Surfaces and Films
Metallic surfaces and films offer very high solar reflectance (0.9-0.95) but relatively low thermal emittance (0.02-0.1), making them ideal for applications where heat retention is desired or where selective radiative properties are needed.
Specialized Polymer Coatings
Specialized polymer coatings can be formulated to provide moderate solar reflectance (0.4-0.7) with high thermal emittance (0.8-0.9), offering good all-around performance with the added benefits of flexibility and easier application.
Multi-layer Insulation Systems
Multi-layer insulation systems use alternating layers of reflective metallic films and insulating spacers to provide extremely high solar reflectance while allowing engineers to tune thermal emittance through layer design and spacing.
Each coating type offers different combinations of solar reflectance and thermal emittance properties that can be matched to specific mission requirements. The selection process must consider not just initial properties but also degradation rates in the space environment.
Testing and Measurement
Accurate measurement of solar reflectance and thermal emittance is essential for aerospace applications. Testing must account for the space environment's unique challenges.
Standard Test Methods:
- ASTM E903 for solar reflectance
- ASTM C1371 for thermal emittance
- Accelerated environmental testing
- Space environment simulation
- Long-term degradation studies
These measurements help engineers validate material selections and predict long-term performance.
Why Choose Modus Advanced
At Modus Advanced, we understand the critical nature of thermal management in aerospace applications. Our team of engineers works closely with aerospace partners to ensure proper material selection and testing for optimal solar reflectance and thermal emittance properties.
Our AS9100 certification and ITAR compliance demonstrate our commitment to aerospace quality standards. With over 10% of our staff being engineers, we provide technical expertise throughout the entire development process.
Partner with us to ensure your aerospace innovations meet their thermal management requirements. Because when mission success depends on precise thermal control, one day matters.