What is GD&T: Complete Definition and Engineering FAQs
June 30, 2025
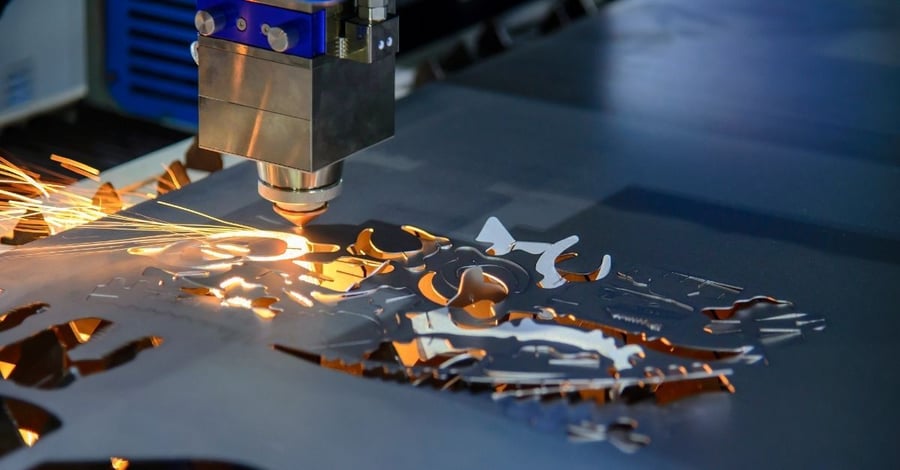
Manufactured with Speed and Precision
The manufacturing capabilities you need and the engineering support you want, all from a single partner.
Submit a DesignKey Points
- Geometric Dimensioning and Tolerancing (GD&T) is a standardized symbolic language that defines exact part geometry using universal symbols and reference frames established by ASME Y14.5 and ISO standards
- GD&T controls five main characteristics: form, orientation, location, profile, and runout to ensure parts function correctly in assemblies while reducing manufacturing costs
- Datum reference frames establish coordinate systems that allow consistent measurement and manufacturing across different facilities and equipment
- Proper GD&T implementation reduces manufacturing costs by 20-50% by specifying only necessary precision while preventing tolerance stack-up issues
- Overly tight tolerances without GD&T justification can increase machining time by 200-400% and significantly extend lead times
- Understanding GD&T fundamentals helps engineers create manufacturable designs that meet functional requirements without unnecessary expense
Definition
What is GD&T?
Geometric Dimensioning and Tolerancing (GD&T) is a symbolic language system that transforms vague dimensional drawings into precise manufacturing instructions, ensuring parts function correctly while minimizing production costs.
Engineers designing precision components face a critical challenge: how do you communicate exact geometric requirements to manufacturers while ensuring parts function correctly in assemblies? The answer lies in mastering Geometric Dimensioning and Tolerancing (GD&T), a standardized symbolic language that transforms vague dimensional drawings into precise manufacturing instructions.
GD&T serves as the universal translator between design intent and manufacturing reality. When properly applied, it eliminates guesswork, reduces manufacturing costs, and ensures consistent part quality across different production facilities worldwide.
Understanding GD&T Fundamentals
Geometric Dimensioning and Tolerancing (GD&T) is a system of symbols, rules, and definitions used to define the exact geometry of parts and assemblies. This system goes beyond basic dimensional tolerancing by controlling how features relate to each other in three-dimensional space.
Get a PDF of this wall chart from gdandtbasics.com.
Unlike traditional coordinate tolerancing that only controls size and location, GD&T addresses five fundamental geometric characteristics that determine how parts function in real-world applications. The system uses datum reference frames — essentially coordinate systems established by physical features on the part — to create consistent measurement standards that manufacturers can replicate regardless of their location or equipment.
The American Society of Mechanical Engineers (ASME) Y14.5 standard governs GD&T implementation in the United States, while ISO 1101 provides international guidelines. Both standards ensure that engineers and manufacturers speak the same geometric language worldwide.
View the full glossary of terms
Why Use GD&T? Key Benefits for Engineers
GD&T implementation provides substantial benefits across the entire product development lifecycle:
Manufacturing Benefits:
- Reduces tolerance stack-up issues that cause assembly problems
- Provides 57% larger tolerance zones compared to coordinate tolerancing
- Enables bonus tolerance through Material Condition Modifiers
- Streamlines inspection processes and reduces measurement complexity
Cost Benefits:
- Eliminates unnecessary precision that increases machining costs
- Reduces rework and scrap rates through clearer specifications
- Minimizes tolerance disputes between design and manufacturing teams
- Optimizes manufacturing processes by focusing on functional requirements
Quality Benefits:
- Ensures consistent part quality across different suppliers
- Provides clear acceptance criteria for inspection
- Reduces interpretation errors in manufacturing
- Enables statistical process control implementation
The Five Pillars of GD&T Control
GD&T organizes geometric controls into five distinct categories, each addressing specific aspects of part geometry and function. Understanding these categories helps engineers select appropriate controls for their design requirements.
Control Category | Primary Function | Key Symbols | Typical Applications |
Form | Controls shape of individual features | ⎯ (Straightness), ⬜ (Flatness), ○ (Circularity), ⌭ (Cylindricity) | Surface finish requirements, basic feature shape |
Orientation | Controls angular relationships | ∥ (Parallelism), ⊥ (Perpendicularity), ∠ (Angularity) | Mating surfaces, assembly alignment |
Location | Controls feature positioning | ⊕ (Position), ◎ (Concentricity), ≡ (Symmetry) | Hole patterns, critical dimensions |
Profile | Controls complex surface shapes | ⌒ (Profile of Line), ⌓ (Profile of Surface) | Curved surfaces, complex geometries |
Runout | Controls rotational variation | ↗ (Circular Runout), ↗↗ (Total Runout) | Rotating assemblies, dynamic parts |
Form Controls: Foundation of Geometric Accuracy
Form controls define the shape of individual features without reference to other features or datums. These controls ensure that surfaces and features maintain their intended geometry within specified limits.
Key form controls include:
- Straightness — Controls how much a line element can deviate from perfectly straight
- Flatness — Ensures surfaces remain within two parallel planes
- Circularity — Maintains round features within acceptable roundness limits
- Cylindricity — Controls cylindrical features more comprehensively than circularity
Form controls typically require the tightest manufacturing precision since they establish the foundation for all other geometric relationships. Engineers should apply form controls strategically to avoid unnecessary manufacturing costs.
Orientation Controls: Managing Angular Relationships
Orientation controls define how features relate angularly to datum reference frames. These controls ensure that features maintain proper angular relationships regardless of their exact location.
Critical orientation applications:
- Assembly interfaces — Where parts must mate at specific angles
- Machining setups — Ensuring proper tool access and orientation
- Functional surfaces — Where angular relationships affect performance
- Secondary operations — Maintaining orientation through multiple machining steps
Orientation controls are essential for ensuring proper fit and function in assemblies where angular relationships affect performance, particularly in aerospace and medical device applications.
Location Controls: Optimizing Feature Positioning
Location controls govern where features are positioned relative to datum reference frames. These controls are critical for ensuring parts mate correctly in assemblies.
Position tolerance offers several advantages:
- Tolerance zone flexibility — Circular zones often provide more usable tolerance than rectangular coordinate tolerances
- MMC benefits — Additional tolerance becomes available as feature sizes vary from Maximum Material Condition
- Assembly optimization — Direct control of mating feature relationships
- Manufacturing efficiency — Reduces inspection complexity compared to coordinate tolerancing
Location controls often work in conjunction with Material Condition Modifiers to optimize manufacturing tolerance while maintaining functional requirements.
Material Condition Modifiers: Maximizing Manufacturing Flexibility
GD&T incorporates Material Condition Modifiers that allow geometric tolerances to change based on actual feature sizes. This concept provides significant manufacturing benefits while maintaining functional requirements.
Modifier | Symbol | Definition | Manufacturing Benefit |
Maximum Material Condition (MMC) | Ⓜ | Smallest holes, largest pins | Bonus tolerance as features deviate from MMC |
Least Material Condition (LMC) | Ⓛ | Largest holes, smallest pins | Ensures minimum material for strength |
Regardless of Feature Size (RFS) | None | Constant tolerance regardless of size | Consistent geometric control |
MMC Application Benefits:
- Cost reduction — Manufacturers gain flexibility without compromising function
- Faster production — Looser effective tolerances reduce machining time
- Higher yields — More parts pass inspection due to bonus tolerance
- Assembly assurance — Parts always fit together when properly applied
When MMC is applied to position tolerances, manufacturers gain bonus tolerance as feature sizes deviate from MMC toward LMC. A hole that measures larger than its minimum size allows the positional tolerance to increase proportionally, providing manufacturing flexibility without compromising function.
Datum Reference Frames: Establishing Measurement Consistency
Datum reference frames form the foundation of all GD&T measurements by establishing coordinate systems based on actual part features. These reference frames ensure that all measurements relate to the same geometric foundation, regardless of where or how the part is manufactured.
Datum Hierarchy and Function:
Datum Level | Degrees of Freedom Removed | Typical Feature Type | Manufacturing Consideration |
Primary | 3 (one plane) | Large, stable surface | Must be accessible for setup |
Secondary | 2 (perpendicular plane) | Edge or surface | Should be machinable reference |
Tertiary | 1 (final constraint) | Point or small surface | Often determines part orientation |
Datum Selection Criteria:
- Functional importance — Choose features that matter for part function
- Manufacturing accessibility — Ensure datums can be easily contacted during setup
- Measurement stability — Select features that provide consistent reference points
- Size and stability — Larger features typically provide better datum references
Poor datum structure can create measurement errors that compound across large parts, particularly when tight tolerances are applied to features far from their controlling datums.
Common GD&T Implementation Challenges and Solutions
Engineers frequently encounter specific challenges when implementing GD&T in their designs. Understanding these pitfalls helps create more manufacturable designs while maintaining functional requirements.
Manufacturing Impact Factors
Challenge Area | Impact on Lead Time | Impact on Cost | Prevention Strategy |
Over-tight tolerances | +200-400% machining time | Significant increase | Specify functional requirements only |
Poor datum structure | Extended setup/inspection | Measurement complexity | Choose stable, accessible datums |
Unnecessary precision | Multiple machining passes | Tool wear, cycle time | Match tolerance to function |
Complex inspection | CMM programming time | Equipment/labor costs | Simplify geometric controls |
Tolerance Stack-Up Solutions
Traditional coordinate tolerancing often creates tolerance stack-up problems where individual part tolerances combine to create assembly issues. GD&T addresses this challenge through several mechanisms:
Stack-up elimination strategies:
- Direct feature control — Position tolerances control mating features directly
- MMC application — Ensures parts always fit regardless of exact locations
- Composite tolerances — Separate pattern and individual feature requirements
- Profile applications — Control complex surfaces without coordinate dependencies
Software Default Traps
Engineers sometimes specify tighter tolerances than functionally necessary, particularly when using default CAD software values. One manufacturing expert noted that software defaults often assume cut taps for threaded holes, specifying drill sizes that may not match the manufacturer's preferred roll tap processes.
Common software-related issues:
- Thread specification defaults — May not match manufacturer's preferred tap type
- Standard tolerance blocks — Often tighter than necessary for function
- Geometric tolerance symbols — Default values may exceed manufacturing capabilities
- Drawing annotation styles — May create inspection complexity
The solution involves specifying functional requirements — thread class, position, and orientation — while allowing manufacturers flexibility in achieving those requirements through their preferred processes.
Manufacturing Impact: Lead Times and Costs
GD&T implementation directly affects manufacturing lead times and costs through several mechanisms that engineers should understand when creating designs.
Machining Considerations
Tolerance Range | Machining Impact | Typical Lead Time Effect | Special Requirements |
Standard (±0.005") | Normal operations | Baseline | Standard tooling |
Precision (±0.001") | Multiple passes | +50-100% | Temperature control |
Ultra-precision (±0.0004") | Specialized processes | +200-500% | Stress relief, environmental control |
Critical manufacturing factors:
- Tool selection — Tighter tolerances require specialized cutting tools
- Setup complexity — Precise geometric controls extend machine setup time
- Environmental control — Very tight tolerances may require temperature-controlled environments
- Multiple operations — Achieving precision often requires additional machining passes
One manufacturing engineer mentioned working on a part requiring four-tenths flatness tolerance — an extremely demanding specification that requires specialized processes and environmental controls far beyond typical manufacturing standards.
Inspection Requirements
GD&T specifications directly determine inspection complexity and duration. Understanding these relationships helps engineers balance functional requirements with manufacturing economics.
Inspection complexity levels:
- Basic dimensional — Calipers, micrometers (minutes per part)
- Geometric tolerances — CMM programming and measurement (hours per part)
- Complex profiles — Advanced CMM programming and surface scanning (extended time)
- 100% inspection — Every part measured rather than statistical sampling
Some customers specify 100% inspection requirements rather than statistical sampling plans, dramatically increasing inspection time and costs. Understanding these implications helps engineers balance functional requirements with manufacturing economics.
Visit the full resource center
Industry-Specific GD&T Applications
Different industries apply GD&T with varying emphasis and requirements based on their specific functional needs and regulatory environments.
Industry | Primary GD&T Focus | Typical Tolerances | Special Considerations |
Aerospace/Defense | Weight optimization, precision | ±0.0005" to ±0.002" | Material certificates, traceability |
Medical Devices | Repeatability, biocompatibility | ±0.001" to ±0.005" | FDA validation, enhanced documentation |
Automotive | High-volume production | ±0.002" to ±0.010" | Statistical process control |
Industrial Equipment | Durability, serviceability | ±0.005" to ±0.020" | Cost optimization |
Aerospace and defense applications typically demand the tightest geometric controls due to weight constraints and performance requirements. Space applications often push machining and measurement capabilities to their limits, requiring geometric tolerances that approach the boundaries of manufacturing technology.
Medical device applications focus heavily on repeatability and traceability, often requiring enhanced inspection protocols and documentation systems. These requirements affect manufacturing lead times more through inspection burden than manufacturing complexity.
Industrial applications typically balance functional requirements with manufacturing economics, applying GD&T strategically to control only the geometric characteristics that affect performance.
Best Practices for Effective GD&T Implementation
Successful GD&T implementation requires understanding both the technical aspects of the system and its practical manufacturing implications.
Design Phase Recommendations
Datum selection guidelines:
- Primary datums — Choose large, stable surfaces accessible for measurement and setup
- Functional relevance — Base datums on features that matter for part operation
- Manufacturing reality — Ensure datums can be easily contacted during production
- Consistency — Use the same datum structure across related parts when possible
Tolerance specification strategy:
- Functional analysis — Determine what geometric characteristics actually affect performance
- Manufacturing consultation — Engage manufacturing partners during design phase
- Material condition optimization — Apply MMC wherever functional requirements permit
- Inspection planning — Consider measurement complexity when specifying controls
Documentation Requirements
Essential drawing elements:
- Clear datum identification — Unambiguous datum feature symbols and callouts
- Complete tolerance specifications — All necessary geometric controls clearly defined
- Material condition symbols — Proper application of MMC, LMC, or RFS as appropriate
- Notes and specifications — Additional requirements not covered by GD&T symbols
Drawing clarity checklist:
- CAD vs. drawing precedence — Clearly specify which takes precedence when discrepancies exist
- Thread specifications — Define functional requirements rather than manufacturing methods
- Surface finish requirements — Coordinate with GD&T controls and manufacturing processes
- Special processes — Identify any required secondary operations or treatments
Advanced GD&T Concepts
Understanding advanced GD&T concepts enables engineers to handle complex design challenges while maintaining manufacturability.
Composite Tolerances
Composite tolerances separate pattern requirements from individual feature requirements, providing manufacturing flexibility while maintaining functional assembly requirements.
Applications include:
- Bolt hole patterns — Control pattern location separately from individual hole positions
- Feature arrays — Manage overall pattern while allowing local variation
- Assembly interfaces — Ensure pattern fits while optimizing individual features
Profile Applications
Profile controls offer excellent solutions for complex geometries that cannot be adequately controlled through traditional form, orientation, and location controls.
Profile advantages:
- Complex surfaces — Single control defines entire surface geometry
- Flexible application — Can function as form, orientation, or location control
- Manufacturing efficiency — Often easier to measure than multiple discrete controls
- Design intent clarity — Directly controls the actual designed surface
Frequently Asked Questions About GD&T
What does GD&T stand for?
GD&T stands for Geometric Dimensioning and Tolerancing, a symbolic language system used to define and communicate engineering tolerances on technical drawings and 3D models.
What is the difference between GD&T and traditional tolerancing?
Traditional tolerancing uses coordinate measurements and plus/minus tolerances, while GD&T uses geometric controls that often provide larger, more usable tolerance zones and better control of part functionality.
What are the main GD&T standards?
The primary GD&T standards are ASME Y14.5 (used in North America) and ISO 1101 (used internationally). ASME Y14.5-2018 is the current version in the United States.
When should engineers use GD&T?
GD&T should be used when parts must fit together in assemblies, when geometric relationships affect function, or when traditional coordinate tolerancing creates unnecessarily tight or unclear requirements.
What are the five types of GD&T controls?
The five types are: Form (straightness, flatness, circularity, cylindricity), Orientation (parallelism, perpendicularity, angularity), Location (position, concentricity, symmetry), Profile (profile of line, profile of surface), and Runout (circular runout, total runout).
How does GD&T reduce manufacturing costs?
GD&T reduces costs by providing larger tolerance zones, eliminating unnecessary precision, preventing tolerance stack-up issues, and allowing manufacturers to use optimal processes while meeting functional requirements.
What is Maximum Material Condition (MMC)?
MMC is a material condition modifier that provides bonus tolerance as feature sizes deviate from their worst-case condition, allowing manufacturers more flexibility while ensuring parts always assemble correctly.
How do I choose the right datums?
Choose datums based on functional requirements, manufacturing accessibility, measurement stability, and assembly considerations. Primary datums should be large, stable surfaces that relate to how the part functions.
Mastering the Language of Precision Manufacturing
GD&T represents far more than a collection of symbols and rules — it provides a systematic approach to communicating design intent while optimizing manufacturing processes. Engineers who master GD&T fundamentals can create designs that meet functional requirements while minimizing manufacturing costs and lead times.
The key to effective GD&T implementation lies in understanding that geometric controls should reflect functional requirements rather than arbitrary precision standards. When properly applied, GD&T transforms engineering drawings from simple dimensional specifications into comprehensive manufacturing instructions that ensure consistent, economical production of high-quality components.
Engineers who embrace GD&T as a design tool rather than merely a documentation requirement will find themselves better equipped to navigate the complex relationship between design intent and manufacturing reality, ultimately creating better products in less time and at lower cost.
Ready to optimize your manufacturing processes with proper GD&T implementation? Partner with manufacturing experts who understand both the theoretical foundations and practical applications of geometric dimensioning and tolerancing to ensure your designs achieve their full potential.