Zirconium Oxide Yttria Stabilized: The Backbone of Advanced Aerospace Thermal Barriers
February 26, 2025
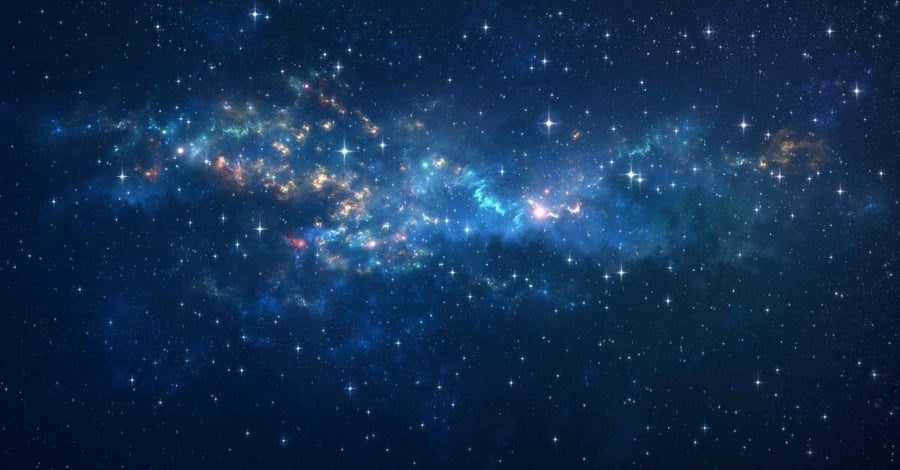
Manufactured with Speed and Precision
The manufacturing capabilities you need and the engineering support you want, all from a single partner.
Submit a DesignKey Points
- Zirconium oxide yttria stabilized (YSZ) is the industry standard for thermal barrier coatings in aerospace applications due to its exceptional thermal resistance and mechanical properties
- The material's unique crystalline structure, achieved through yttria stabilization, enables it to withstand extreme high temperature resistance cycling while maintaining structural integrity
- Recent advances in YSZ coating technologies have pushed the boundaries of aircraft engine efficiency and durability
- Understanding the properties and applications of YSZ is crucial for aerospace engineers working on next-generation propulsion systems
- Material selection and coating design require careful consideration of multiple factors to optimize performance
In the unforgiving environment of aerospace propulsion systems, every material choice can mean the difference between mission success and catastrophic failure. Among these critical materials, zirconium oxide yttria stabilized stands as a cornerstone of modern thermal barrier coating (TBC) systems, enabling aircraft engines to operate at higher temperatures and greater efficiencies than ever before.
This comprehensive exploration will launch into the fundamental properties, applications, and emerging trends in YSZ technology that aerospace engineers need to understand when designing next-generation thermal protection systems. Let’s get started.
Read Our Comprehensive Guide to Optical and Thermal Coatings
The Science Behind YSZ
At its core, YSZ's exceptional performance stems from its unique atomic structure and carefully controlled composition. Understanding these fundamental properties is essential for aerospace engineers working with these advanced materials.
Crystal Structure and Phase Stability
The addition of yttria to zirconium oxide creates a stable cubic crystal structure that prevents detrimental phase transformations during thermal cycling.
Key structural characteristics include:
- Cubic fluorite crystal structure at room temperature
- Oxygen vacancies that reduce thermal conductivity
- Enhanced phase stability up to 2680°C
- Controlled microstructure development during coating processes
The remarkable stability of YSZ in extreme conditions makes it an invaluable material for aerospace applications.
Chemical Composition and Properties
The precise composition of zirconium oxide yttria stabilized plays a vital role in determining its performance characteristics. Modern aerospace applications typically utilize specific formulations that have been optimized through decades of research and testing.
Standard composition features:
- ZrO2 with 6-8 wt% Y2O3 for optimal phase stability
- Controlled impurity levels below 0.1%
- Specific surface area ranging from 5-15 m²/g
- Particle size distribution optimized for coating application
These carefully controlled parameters ensure consistent performance in demanding aerospace environments.
Applications in Aerospace
The versatility of YSZ has made it indispensable across numerous aerospace applications, each with its own unique set of requirements and performance demands. Let's examine the key areas where this remarkable material has proven its worth.
Turbine Engine Components
Zirconium oxide yttria stabilized has revolutionized the design and performance of modern aircraft engines. Its implementation as a thermal barrier coating has enabled significant advances in operating temperatures and energy efficiency.
Primary applications include:
- High-pressure turbine blades and vanes
- Combustion chamber liners
- Afterburner components
- Exhaust system components
Each application requires careful consideration of coating thickness, microstructure, and bond coat selection.
Spacecraft Thermal Protection
Beyond aircraft engines, yttria stabilized zirconium oxide plays a crucial role in protecting spacecraft during atmospheric reentry. The material's exceptional thermal management properties make it ideal for managing the extreme heat generated during this critical phase.
Key spacecraft applications include:
- Heat shield components
- Propulsion system protection
- Thermal management systems
- Leading edge protection
These applications demonstrate the versatility of YSZ in aerospace thermal protection.
Performance Characteristics
The success of YSZ in aerospace applications relies on a specific combination of thermal and mechanical properties that make it uniquely suited for extreme environments. These characteristics must be thoroughly understood to optimize coating design and implementation.
Thermal Properties
The thermal performance of zirconium oxide yttria stabilized sets it apart from other ceramic materials used in aerospace applications. Its unique combination of properties makes it particularly well-suited for thermal barrier applications.
Critical thermal properties include:
- Low thermal conductivity (2.0-2.3 W/m·K at 1000°C)
- High thermal expansion coefficient matching superalloy substrates
- Excellent thermal shock resistance
- Stable performance up to 1200°C in service
These properties enable YSZ coatings to provide reliable thermal protection in demanding aerospace environments.
Mechanical Properties
While thermal performance is crucial, the mechanical properties of zirconium oxide yttria stabilized are equally important for ensuring coating durability and longevity.
Key mechanical characteristics include:
- High hardness (1200-1400 HV)
- Good erosion resistance
- Excellent strain tolerance
- Strong adhesion to bond coat layers
Understanding these properties is essential for proper coating design and implementation.
Everything you need to know about optical and thermal coatings
Manufacturing and Processing
The successful implementation of YSZ coatings depends heavily on precise manufacturing processes and rigorous quality control measures. These aspects are crucial for ensuring consistent performance in critical aerospace applications.
Coating Methods
The application of zirconium oxide yttria stabilized coatings requires sophisticated processing techniques to achieve optimal performance. Different methods offer varying advantages depending on the specific application requirements.
Common coating processes include:
- Air Plasma Spray (APS)
- Electron Beam Physical Vapor Deposition (EB-PVD)
- Solution Precursor Plasma Spray (SPPS)
- Suspension Plasma Spray (SPS)
Each method produces unique microstructures that influence coating performance.
Quality Control and Testing
Ensuring the consistent quality of thermal barrier coatings is paramount for aerospace applications. Rigorous testing and quality control measures are essential throughout the manufacturing process, regardless of the type of coating(s) you leverage for your projects.
Critical quality parameters include:
- Coating thickness uniformity
- Microstructure evaluation
- Phase composition analysis
- Bond high strength testing
- Thermal cycling performance
These parameters must be carefully monitored to ensure coating reliability.
Design Considerations
Creating effective thermal barrier systems requires careful attention to numerous design factors that influence overall performance and longevity. Engineers must take a holistic approach to system design to achieve optimal results, and that may mean reviewing material selections during a Design for Manufacturability (DfM) review with your manufacturing partner.
System Integration
Successfully implementing thermal barrier coatings requires careful consideration of the entire thermal protection system. Engineers must account for multiple factors when designing their solutions.
Key design factors include:
- Substrate material selection
- Bond coat compatibility
- Coating thickness optimization
- Edge effects and geometric considerations
These factors significantly influence overall system performance.
Performance Optimization
Optimizing thermal barrier coating performance requires balancing multiple competing factors. Engineers must consider trade-offs between different performance characteristics to achieve optimal results.
Important optimization parameters include:
- Coating density and porosity
- Microstructure control
- Deposition parameters
- Post-coating treatments
Careful attention to these parameters enables maximum coating performance.
From Materials Science to Mission Success
The critical role of zirconium oxide yttria stabilized in aerospace thermal protection systems cannot be overstated. However, as aerospace engineers continue to push the boundaries of aircraft and spacecraft performance, understanding and optimizing thermal barrier solutions becomes increasingly important.
Ultimately the goals of your project will determine which materials are the best fit for your needs. Our engineering team has extensive experience in materials selection and thermal management solutions for aerospace applications. We invite you to contact our engineers to discuss your specific thermal protection needs and explore innovative solutions for your next aerospace project.
Ready to discuss your thermal management challenges? Contact our engineering team today to leverage our expertise in aerospace materials and manufacturing solutions.