5 Considerations for Selecting a Conductive Elastomer
March 8, 2023
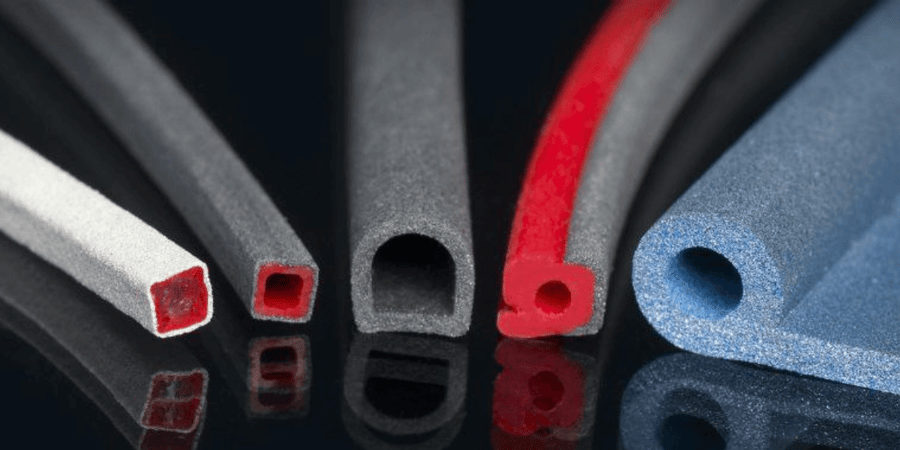
Manufactured with Speed and Precision
The manufacturing capabilities you need and the engineering support you want, all from a single partner.
Submit a DesignKey Points
- Electrically conductive elastomers combine the properties of rubber-like elasticity and electrical conductivity and are useful for applications in electronics, such as EMI shielding, grounding, and electrical contact.
- The performance of conductive elastomer materials depends on several material properties.
- Factors such as chemical resistance, temperature range, compression set, and conductivity should be considered. Additionally, conductive elastomers can be affected by acids, bases, solvents, and oils, which can degrade or dissolve the material.
If you're in the defense, medical device, or emerging technology industry categories designing custom gaskets likely isn’t new to you.
What may be new or worth brushing up on, however, are the five critical things to consider when selecting a conductive elastomer. We've got you covered!
Dig in to learn some of the key considerations for selecting the right conductive elastomer for your next big project, especially when electromagnetic interference and environmental sealing are crucial factors.
Not sure where to start? You need a trusted manufacturing partner that has been there, done that – that’s Modus Advanced. Contact our expert team of materials engineers for design guidance today.
What is a Conductive Elastomer?
A conductive elastomer is the best of both worlds. It combines the properties of rubber-like elasticity and conductivity. It is usually made by mixing an elastomer matrix, such as solid silicone or fluorosilicone, with a filler of conductive particles, such as silver, nickel, or carbon.
The material produced is then able to provide mechanical flexibility and conductivity to meet the needs of your application, including EMI shielding and radio frequency interference protection.
Conductive gaskets are often used as seals and connectors in electronic devices to prevent electromagnetic interference (EMI) from leaking out of enclosures and to ensure reliable electrical contact.
There are a lot of things to consider when designing an effective conductive gasket so our expert team of engineers has narrowed it down to 5 main pillars for consideration. Let's dig in.
1. Material Properties and Performance
The performance of conductive elastomers depends on several material properties that affect their ability to conduct electricity and provide reliable EMI shielding in electronic devices.
- Electrical conductivity: The amount and type of conductive fillers used in the material will dictate the conductivity of your elastomer. Materials with a higher concentration of highly conductive fillers will have better conductivity and shielding performance.
- Compression set: Maintaining shape and compression force over the lifespan of the device is critical to ensure EMI shielding effectiveness.
- Hardness: A conductive elastomer that is too hard will not be able to form a reliable seal between two mating surfaces properly, leading to an ineffective device. A material that is too soft may also cause issues by not being firm enough to create the proper seal required.
- Tear and tensile strength: These properties determine the ability of the material to resist tearing or breaking under stress, such as during installation or use.
- Environmental resistance: Electrically conductive elastomers may be exposed to various environmental factors such as temperature, moisture, chemicals, and UV radiation.
Material properties of conductive elastomers must be carefully selected and optimized to provide the required electrical conductivity, EMI shielding effectiveness, and mechanical durability for your specific application.
2. Compression Force and Resilience
Compression force and resilience of conductive elastomers are influenced by several factors related to the material composition, filler content, temperature, and aging. Understanding these factors is important in selecting the appropriate conductive elastomer for specific applications that require EMI shielding or excellent environmental sealing properties.
The compression force and resilience of conductive elastomers are affected by several factors, including:
- Material composition: The specific elastomer composition, such as the type of polymer and filler materials used, can affect the compression force and resilience of the material. For example, silicone elastomers tend to have lower compression forces and higher resilience compared to fluorosilicone elastomers.
- Filler content: The filler content of the conductive elastomer can also affect the compression force and resilience of the material.
- Temperature: The temperature of the conductive elastomer can also affect its compression force and resilience.
- Aging: The aging of the conductive elastomer can also affect its compression force and resilience over time. Exposure to environmental factors, such as heat, light, and chemicals, can cause the material to degrade and lose its mechanical properties.
Visit our full resource center
3. Chemical Compatibility
When selecting conductive elastomers for applications that involve exposure to chemicals or corrosive substances, several factors should be considered:
- Resistance to Chemicals: Consider the resistance of the conductive elastomer to the specific chemicals or corrosive substances that it will be exposed to.
- Temperature range: High temperatures can accelerate chemical reactions and reduce the material's performance over time.
- Compression set: Exposure to these substances can affect the material's mechanical properties and EMI shielding effectiveness.
- Electrical conductivity: Exposure to certain chemicals or corrosive substances can affect its ability to conduct electricity.
- Application requirements: The specific application requirements are the foundation for the design.
Conductive elastomers can be affected by a variety of chemicals, depending on the specific elastomer composition and the nature of the chemical exposure. Some common chemicals that can affect the performance of conductive elastomers include:
- Acids: Strong acids, such as sulfuric acid and hydrochloric acid, can degrade many types of elastomers, including silicone, fluorosilicone, and EPDM.
- Bases: Strong bases, such as sodium hydroxide and potassium hydroxide, can also degrade many types of elastomers, including silicone, fluorosilicone, and EPDM.
- Solvents: Many solvents, such as acetone, ethanol, and toluene, can dissolve or soften elastomers, ..
- Oils: Exposure to certain oils, such as mineral oil and hydraulic oil, can cause swelling and deterioration of elastomers, leading to loss of mechanical properties and EMI shielding effectiveness.
- UV radiation: Exposure to UV radiation can cause degradation of many types of elastomers.
It is important to consider the specific chemical exposure conditions when selecting a conductive elastomer for an application. This is critical in the medical device industry where devices are subject to being wiped down or cleaned frequently with abrasive chemicals.
Selecting the appropriate conductive elastomer for chemical or corrosive environments requires careful consideration of the specific chemicals or corrosive substances, temperature range, compression set, electrical conductivity, and application requirements of the specific application.
4. Temperature Range
As we've seen so far, temperature is a large piece of the puzzle in choosing a conductive elastomer. For applications that involve exposure to high or low temperatures, several factors should be considered:
- Temperature range: For high-temperature applications, materials such as silicone or fluorosilicone may be suitable, while for low-temperature applications, materials such as fluorocarbon elastomers may be appropriate.
- Thermal conductivity: The thermal conductivity of the conductive elastomer can affect the ability of the material to dissipate heat.
- Compression set: With temperature in mind, the material's ability to maintain its shape and compression force is critical to providing an effective EMI shield.
- Aging characteristics: Exposure to extreme temperatures can accelerate aging and reduce the material's performance over time.
- Chemical resistance: The resistance of the conductive elastomer to chemical exposure at high or low temperatures should be considered, as exposure to chemicals can affect the material's electrical conductivity and mechanical properties.
5. Cost and Availability
At the end of the day, you need a conductive elastomer that fits your application and budget. Luckily there are thousands of materials to choose from to fit your needs.
Once you’ve reviewed materials that make the first cut, cost and availability help whittle down the selections a little further. Here are a few of the key considerations:
- Material cost: Cost is impacted by material composition, manufacturing process, and availability.
- Tooling cost: Tooling costs can significantly increase the cost of the project.
- Volume requirements: Higher volumes may require more cost-effective materials or specialized production processes to achieve cost savings.
- Lead times: Availability or production constraints, like supply chain challenges, can impact lead times.
- Supplier reliability: Is your vendor reliable? Ensuring that they can stock the materials you need and when you need them is part of the puzzle.
Conductive Gaskets with Speed and Precision – the Modus Way
When you’re designing a conductive gasket, you are designing for a reliable seal and perfect performance – anything less could be disastrous. The materials you choose should suit the needs of your project perfectly, and balance performance with cost-effectiveness using the five considerations we’ve listed above.
We’ve covered a lot here, there’s no denying that. We hope that this has provided enough information on selecting a conductive elastomer that you’re ready to take the next step in the design cycle.
We’re ready and able to help. Contact us today and work with our expert engineering team to get your custom conductive gasket crafted with speed and precision.