What is EMI Shielding and Why is it Important for Your Design?
January 21, 2021
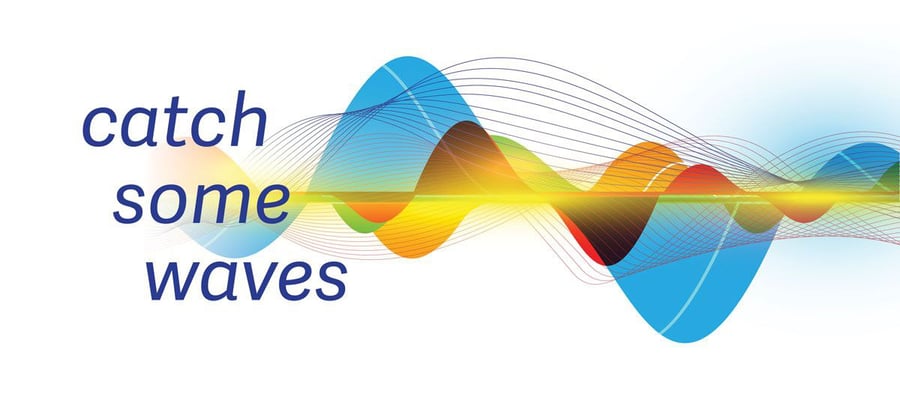
Manufactured with Speed and Precision
The manufacturing capabilities you need and the engineering support you want, all from a single partner.
Submit a DesignDefinition
What is EMI Shielding?
EMI Shielding in electronic devices and equipment is the use of manufacturing techniques and materials to protect signals from being disrupted by external electromagnetic signals as well as preventing generated signals from interfering with surrounding components.
EMI Shielding ServicesKey Points
- EMI shielding protects electronic signals from external electromagnetic interference and prevents generated signals from disrupting surrounding components.
- Electromagnetic interference poses serious risks in critical applications like medical devices, aerospace systems, and military equipment, potentially causing issues ranging from data loss to system failure.
- Common EMI sources include ambient electromagnetic energy, power quality problems, and application-specific factors in industries like transportation, healthcare, and defense.
- Modern EMI shielding materials have evolved from traditional metal sheets to include flexible options like particle-filled silicones, which combine metal's electrical properties with silicone's material advantages.
- Newer cost-effective materials like nickel-graphite silicones now perform at comparable shielding levels to silver-aluminum but at lower costs while meeting military specifications for shielding effectiveness.
Why is EMI Shielding Important?
Electromagnetic interference (EMI) can disrupt electronic devices, equipment, and systems that are used in critical applications. Examples include medical, military, and aerospace electronics; mass transit systems; industrial touch screens; and navigation and vehicular control systems - just to name a few.
The causes of electromagnetic interference are numerous, and include both man-made and natural sources. The results can range from temporary disturbances and data losses to system failure and even loss of life.
For engineers, it's important to recognize how electromagnetic energy (EME) in the application environment can cause interference and how an EMI shield works. Without this basic EMI awareness, you may design gaskets that lack adequate protection against electromagnetic fields in the radio frequency (RF) spectrum, the part of the electromagnetic spectrum with frequencies from 3 kHz to 300 GHz. RF waves form the basis of radio technology, but they can also transmit signals that interfere with wireless communications.
Sources of EMI
In general, EMI sources can be divided into two major categories: ambient EMI and power quality problems. Railroad and mass transit systems, medical equipment, and military applications also face their own specific challenges. Increasingly, intentional electromagnetic interference (IEMI) also represents a threat to non-military assets such as the power grid and other types of critical infrastructure.
Railroad and mass transit systems may experience EMI because of application-specific factors such as:
- Emissions from train control and propulsion systems
- High voltage contact switching
- Third rail shoes
- Train signaling and control systems
Medical equipment is susceptible to EMI, too. Application-specific sources include:
- Electrical and electronic equipment in surgical units
- Life support devices such as ventilators and infusion pumps
- Patient telemetry and assistance equipment
- X-ray machines for diagnostics and therapeutics
In addition to IEMI (colloquially called "electronic warfare"), military assets and critical infrastructure face EMI threats such as:
- High-altitude nuclear electromagnetic pulse (HNEMP)
- High-power microwave weapons
- E-bombs
- EMP cannons
Some of these threats are extreme, of course, but all engineers need to assess EMI risks in order to incorporate appropriate protection into their gasket designs.
Visit our complete EMI shielding resource center.
EMI Shielding Gaskets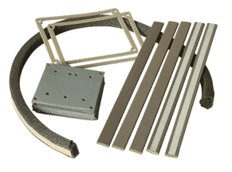
An EMI shielding gasket is a mechanical device that helps protect electronics from electromagnetic interference. Traditionally, EMI shielding has been fabricated from metal sheets and formed into shapes that fit electronic housings or enclosures. Aluminum, copper, and steel are strong and rigid, but thin metal sheets can deform under the pressures that are required for sealing. Once metal EMI shields are deformed, they tend to remain in that shape and may allow leakage to and from electronic circuits.
Today, EMI shielding materials include flexible metal screens, metal wires, and metal foams. Coatings made of metallic inks are also applied to the interiors of electronic enclosures to provide EMI shielding solution. Each of these shielding methods has its advantages, but particle-filled silicone combines the electrical properties of metal with the material properties of silicone rubber. For product designers who need to meet a variety of sealing and insulation challenges, silicone filled with metal or metal-coated particles is an excellent choice.
Learn how Modus is redefining the traditional supplier relationship.
For example, the EMI gaskets that are used in some ruggedized touchscreens are made of particle-filled silicones that attenuate EMI emissions, provide electrical conductivity , and ensure environmental sealing in conditions ranging from desert heat to arctic cold. These EMI shielding gaskets must cushion the device from mechanical shock and be soft enough to avoid interfering with the display's touch function. EMI shielding material costs and ease-of-fabrication are also important for gasket designers in many different industries.
Conductive Silicones
Particle-filled silicones are used in some demanding applications, but can these conductive elastomers really meet all of your application's requirements? Are EMI shielding gaskets made of these materials cost-effective, and do particle-filled elastomers support design for manufacturability? Silicone resists sunlight, water, and a wide range of temperatures, but loading them with a high percentage of metal particles can have negative tradeoffs.
That's why historically, some gasket designers rejected particle-filled silicones as too hard or too brittle. Other engineers have complained about part size limitations based on mold dimensions and long lead times for sheet materials. Some industry professionals also believe (incorrectly) that all particle-filled silicones are just too thick to support thinner electronic designs. The cost of older, particle-filled products also discouraged their use.
For years, the filler material of choice for shielding silicones was silver-aluminum. The U.S. military's development of the MIL-DTL-83528 specification played an important role in this particle's popularity. When silver began approaching $50 per Troy ounce in 2011, however, the fact that these elastomers were specified on thousands of gasket drawings and prints became problematic. EMI gaskets made of silicones filled were pure silver were even more expensive.
Today's electronic designers can specify alternative particle fills that cost less but still provide strong EMI shielding. In addition to silver and silver-aluminum, silver-copper and silver-glass are used. Today, cost-effective nickel-graphite silicones perform at the shielding level of silver-aluminum products. These nickel-graphite silicones meet the EMI shielding effectiveness requirements of MIL-DTL-83528, which sets a minimum shielding effectiveness of 100 dB at RF frequencies between 20 and 10,000 Hz.
Image: Graphic representation of electromagnetic interference
EMI Materials
Thanks to innovations in silicone compounding, particle-filled elastomers can meet demanding shielding requirements along with other project specifications. For example, because nickel-graphite silicones are available in 30, 40, and 45 durometer (Shore A), they're soft enough for enclosure gaskets. Other, higher-durometer shielding elastomers that use fluorosilicone as the base elastomer can resist fuels and chemicals. These fluorosilicone compounds come in 50, 60, and 80 durometers (Shore A) for applications that require EMI gaskets made of harder materials.
Unlike older shielding elastomers, newer shielding materials contain enough metal filler to ensure effective EMI shielding and electrical conductivity. Plus, these conductive silicones support reliable, cost-effective fabrication.
During gasket cutting , particle-filled silicones won't stretch or become deformed. Connector holes align properly, and the material's structural properties support greater tear resistance - an important consideration for thinner wall gaskets. Product designers can also specify the use of an adhesive backing for ease-of-installation. For shielding applications where Z-axis conductivity is required, particle-filled silicones can support the use of electrically-conductive adhesives for excellent shielding effectiveness.
Various higher-durometer, nickel-graphite silicones are available, but some EMI gasket applications require reinforcement for added strength. That's why EMI materials include products such as 65-durometer elastomer that's reinforced with an internal nickel-coated mesh.
Lower-durometer, nickel-graphite silicones can also be reinforced with an inner layer of conductive fabric for added conductivity and material strength, which helps to prevent brittleness and tearing during EMI gasket fabrication.
Related: EMI Shielding Materials Guide
Material selection is critical for EMI shielding gaskets, influencing performance and compatibility with design requirements during the design phase.
Read MoreRelated: MIL-SPEC EMI Shielding Materials Guide
Dig deeper into the specific material considerations for military-grade applications.
Learn MoreForm-in-Place Gaskets: Advanced EMI Shielding Solutions
Form-in-Place (FIP) gaskets represent one of the most precise and effective methods for applying EMI shielding in complex electronic designs. Unlike pre-cut gaskets or traditional EMI solutions, FIP gaskets are directly dispensed onto the housing as a liquid material that cures in place, creating a custom seal that perfectly conforms to the part's geometry.
For engineers working with intricate designs or miniaturized electronics, FIP gaskets offer several distinct advantages. The precision dispensing process allows for gasket beads as narrow as 0.3mm, making them ideal for densely packed electronics in aerospace systems and medical devices where space is at a premium. This level of precision simply isn't possible with die-cut or manually applied shielding solutions.
FIP gaskets excel in applications requiring both environmental sealing and EMI shielding performance. When dispensed with conductive materials like silver-filled or nickel-graphite silicones, these gaskets provide excellent electrical continuity across mating surfaces while maintaining the flexibility needed for multiple compression cycles. For medical and military applications where reliability is non-negotiable, the customizable nature of FIP gaskets ensures consistent performance even in demanding environmental conditions.
Modern CNC-controlled dispensing equipment ensures repeatable, consistent application across production runs, critical for maintaining quality control in high-reliability applications. By eliminating the material waste associated with die-cutting processes, FIP technology also offers a more cost-effective approach for low to medium volume production, especially for complex geometries where traditional gaskets would require multiple pieces.
When considering FIP gaskets for your EMI shielding needs, partner with a manufacturer experienced in both material selection and precision dispensing technologies. The effectiveness of FIP solutions depends heavily on proper material selection, bead profile design, and dispensing parameters, technical considerations that benefit from collaborative engineering support.
Frequently Asked Questions About EMI Shielding
What level of EMI shielding do I need for my application?
The required level of EMI shielding depends on your specific application and the regulatory standards you need to meet. Medical devices typically require shielding effectiveness between 60-80 dB, while military and aerospace applications often require 80-100+ dB of protection. Rather than overengineering, consult with an EMI specialist to determine the precise requirements for your specific design and environmental conditions.
Visit the EMI Gasketing Resource Center
How do I know if my product requires EMI shielding?
Your product likely needs EMI shielding if it: contains sensitive electronic components, operates in environments with high electromagnetic activity, must comply with EMC regulations, or could potentially interfere with other nearby devices. Early EMI testing during prototyping can help identify susceptibility issues before they become costly design problems.
What's the difference between EMI shielding and EMI filtering?
EMI shielding physically blocks electromagnetic radiation using conductive materials that reflect and absorb electromagnetic energy. EMI filtering, on the other hand, uses electronic components (capacitors, inductors, ferrites) to remove unwanted frequency components from power and signal lines. Many designs require both approaches for comprehensive EMI protection.
How does material thickness affect EMI shielding performance?
While thicker materials generally provide better shielding, the relationship isn't always linear. For conductive materials like metal, the skin depth (the depth at which radiation is attenuated by ~63%) varies with frequency. At higher frequencies, even thin materials can provide effective shielding. For particle-filled silicones, thickness affects both shielding effectiveness and compression forces needed for proper sealing.
Visit our Glossary for more definitions of key manufacturing terms.
Can I retrofit EMI shielding to an existing design?
Retrofitting EMI shielding is possible but often less effective and more costly than incorporating it during initial design. Options for retrofitting include conductive coatings, EMI gaskets at seams and apertures, cable shielding, and ferrite suppressors on cables. For critical applications, redesigning with integrated EMI protection is usually the more reliable approach.
How do environmental factors affect EMI shielding performance?
Environmental factors like temperature extremes, humidity, salt spray, and vibration can significantly impact EMI shielding performance over time. For instance, metal shields may corrode in high-humidity environments, reducing conductivity and shielding effectiveness. Particle-filled silicones offer excellent environmental resistance for applications facing these challenges, maintaining their properties across a wide temperature range (-65°C to +200°C).
What are the trade-offs between different EMI shielding materials?
Each EMI shielding material presents different trade-offs:
- Metal shields provide excellent shielding but may be rigid, heavy, and susceptible to corrosion
- Conductive fabrics offer flexibility but typically lower shielding effectiveness
- Particle-filled silicones balance good shielding with environmental sealing and flexibility, though they may be more expensive than basic metal solutions
- Conductive coatings are lightweight but may wear over time
The optimal material choice depends on your specific application requirements, including environmental conditions, mechanical constraints, and shielding targets.
How can I test the effectiveness of my EMI shielding?
EMI shielding effectiveness can be tested using specialized equipment in an anechoic chamber or TEM cell. Standard test methods include MIL-STD-285 and IEEE-STD-299 for enclosures and ASTM D4935 for materials. Working with a partner like Modus Advanced can help ensure your prototypes meet required specifications before moving to production.
How do gasket compression and mounting affect EMI shielding performance?
Proper gasket compression is critical for EMI shielding effectiveness. Insufficient compression creates gaps where EMI can leak, while excessive compression may damage the gasket or create permanent deformation. Most EMI gaskets require 10-30% compression for optimal performance. Mounting surfaces should be clean, conductive, and free of gaps larger than 1/20th of the wavelength of the highest frequency to be shielded.
Have More Questions About EMI Shielding?
Do you have questions about EMI sources, EMI shielding, or conductive silicones for elastomeric shielding gaskets? The Technical Team at Modus Advanced, Inc. is ready to help. For more information, please contact us.