5 Manufacturing Methods for Shielding RF Signals
May 11, 2022
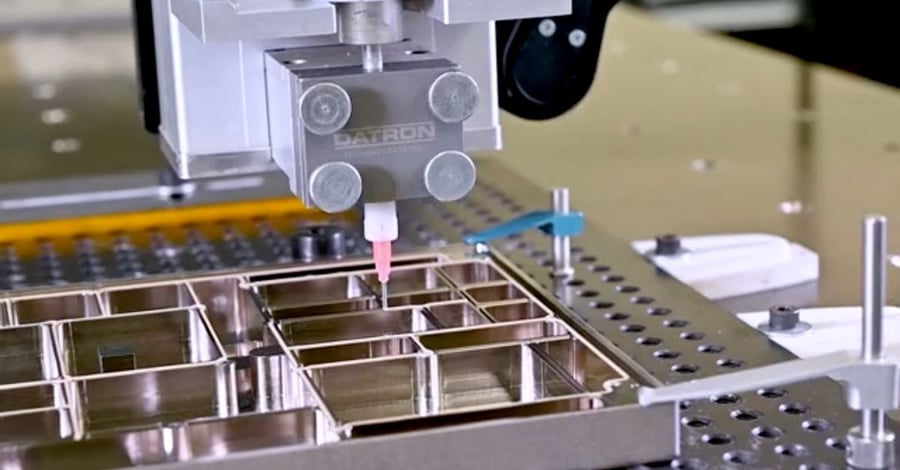
Manufactured with Speed and Precision
The manufacturing capabilities you need and the engineering support you want, all from a single partner.
Submit a DesignKey Points
- There’s more than one way to manufacture a radio frequency (RF) shield.
- While the manufacturing methods used for your RF shield will depend on the design, CNC milling and form-in-place gasket dispensing are the most likely candidates.
- An experienced manufacturing partner can advise you on the best manufacturing method for your unique RF shield design.
Frank’s machine shop around the corner will probably tell you there’s only one way to manufacture an RF shield, and the shop that just got a die cutter is likely going to tell you there’s only one way to manufacture an RF-shielding gasket.
The truth, however, is that there are several ways to manufacture an RF shield. The manufacturing method ultimately used for your RF shield should depend on the unique details of your design, your project scope and budget and the RF shield’s intended application, among other factors.
In this post, the Modus Advanced team will walk you through the five most common manufacturing methods for shielding RF signals, including the metal housing and gaskets that may be parts of the whole. Read on to learn more.
When you’re manufacturing something to resist radio frequency interference (RFI), there is no substitute for quality or expertise. Quality makes sure the end product is effective, and the expertise makes sure manufacturing goes smoothly and stays within budget and on deadline. To work with a partner who brings both to the table, reach out to Modus.
RF Shielding: Everything You Need to Know
CNC Milling
Computer numerical control (CNC) milling is, by far, the most common manufacturing method to create the metal housing for RF shields. The basic process for CNC milling an RF shield’s metal housing looks like this:
- A CNC machinist programs a computer-assisted cutting device (called a mill) to cut a stock piece of metal material into the shape specified in the part’s specs.
- The device removes material from the stock piece until it is formed perfectly into the intended shape of the metal housing.
It’s a relatively fast process that can reduce lead times, so it’s a great manufacturing method for RF shield project teams who are on tight deadlines. Meanwhile, the CNC mills don’t require expensive and time-consuming hard tooling.
CNC Cutting
A CNC lathe works in much the same way as a CNC mill. The device is programmed beforehand and removes material from a stock piece to form the metal housing.
The key difference here is that a CNC lathe is best used on thinner and flatter materials, as well as those that have small tolerances and tight turns. That may be perfect for manufacturing smaller RF shields or even gaskets that are applied to them.
Form-in-Place Gasket Dispensing
You won’t be able to make your metal housing with FIP gasket dispensing, but when it comes time to add gaskets to your machined metal housing, FIP can save time and headaches.
Using a computer-controlled bead, an FIP gasket dispenser places a liquefied RF-shielding gasket material directly onto the metal housing. From there, the material dries and cures to the housing, forming a precise gasket.
This process creates almost no material waste and is ideal for extremely intricate or small gaskets — precisely the kind often used on small RF shields.
Waterjet Cutting
A waterjet cutting machine uses a tiny stream of water under extremely high pressure to cut through all kinds of materials — from metals to elastomers — with precision. Before leaving the cutting head, the jet passes through a chamber that draws in an abrasive material like sand, which gives the water jet its cutting power.
Waterjet cutting isn’t the most common manufacturing method for shielding RF signals by any means, but it can be quite effective and useful under certain contexts. For example, waterjet cutting works particularly well when you need to cut through thermal or microwave-sensitive materials, such as those used on RF absorbers (a common component of RF shields).
Die Cutting
Die cutting is sometimes involved in the manufacturing of RF-shielding gaskets to be used in and on RF shields. In this method, soft materials pass through and over a metal die that cuts them into the necessary shapes.
This RF gasket manufacturing method is relatively fast compared to other methods, but that speed comes with a bit more material waste than other gasket manufacturing methods, such as FIP.
Modus: An RF Shield Manufacturer with Wide-Ranging Capabilities
Modus Advanced is capable of all of the above manufacturing methods. In fact, we employ each of these, among others, for customers across a wide variety of industries, ranging from defense and aerospace to telecommunications and consumer electronics.
For every job we do, we act as consultants — not just vendors. Our staff manufacturing engineers assess each RF shield design for functionality, feasibility and manufacturability, and we advise on those factors to help you perfect your design.
The results of this approach have been fantastic: happy customers, world-class RF shields and a bright future for the Modus team. Want to be a part of that bright future? Reach out to us today. Give us a call at 925-960-8700 or contact our team online.
Why Choose Modus for Your RF Shielding Needs?
When your critical applications require reliable RF shielding, partnering with a manufacturing expert can make the difference between a device that performs flawlessly and one that fails in the field. Modus Advanced combines engineering expertise with vertical integration to deliver RF shields that meet the most demanding requirements in aerospace, defense, and medical device applications.
- Engineering-First Approach: With over 10% of our staff being engineers, we provide expert design feedback that improves manufacturability and performance
- Vertical Integration: From machining to FIP gasket dispensing, plating, and assembly, all under one roof, reducing lead times and risk
- Quality Systems: AS9100 and ISO 9001 certified processes ensure consistent, high-quality RF shields that perform when lives depend on them
- Prototype to Production Partner: Support throughout your entire product lifecycle, from rapid prototype turnaround in days to efficient scaling for ongoing production volumes with consistent quality and performance
- Materials Expertise: Access to the full spectrum of RF shielding materials with guidance on selecting the optimal solution for your specific application
Partner with Modus Advanced to accelerate your path to market with RF shields manufactured to the highest standards of quality and precision; because when one day matters, having the right manufacturing partner is the obvious choice.
RF Shield Manufacturing