Material Guide: AZ-1000-ECB Black Thermal Control, Electrically Conductive Coating
May 22, 2025
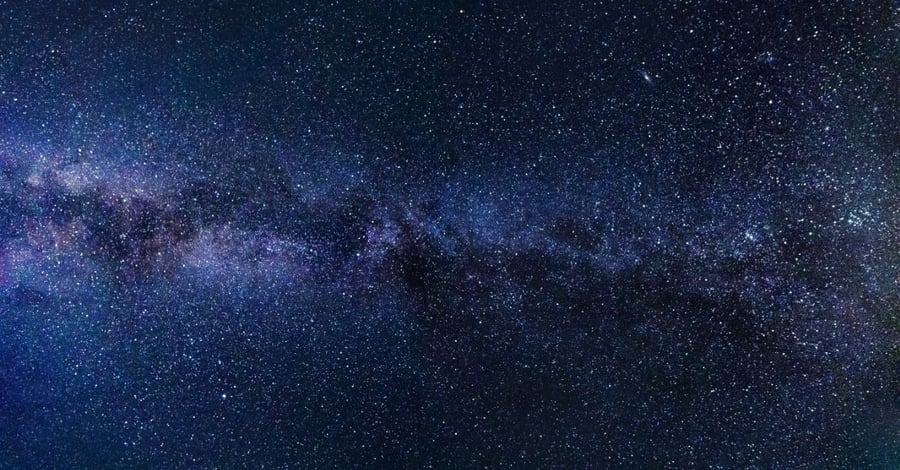
Manufactured with Speed and Precision
The manufacturing capabilities you need and the engineering support you want, all from a single partner.
Submit a DesignKey Points
- AZ-1000-ECB is an electrically conductive thermal control coating specifically designed for spacecraft and satellite applications where environmental resilience is critical
- This coating offers exceptional solar absorptance (0.97) and thermal emittance (0.89) properties while providing surface resistivity of 10²-10⁴ Ω/sq
- Space-proven through multiple missions including the Materials International Space Station Experiment (MISSE), where it maintained performance after 4 years in the space environment
- The operating temperature range of -180°C to 1100°C (-292°F to 2012°F) makes it suitable for extreme aerospace applications
- Key benefits include atomic oxygen protection, surface charge dissipation, and thermal control capabilities in a single coating
Introduction to Electrically Conductive Thermal Control Coatings
Electrically conductive thermal control coatings represent a critical component in aerospace engineering, particularly for spacecraft and satellites operating in the harsh conditions of space. These specialized materials must perform multiple functions simultaneously—managing thermal properties while providing electrical conductivity and protection against environmental degradation.
The AZ-1000-ECB black thermal control, electrically conductive coating stands out as an advanced solution developed specifically for these demanding applications. This high-performance material has been thoroughly tested not just in laboratories but in actual space environments through multiple missions, demonstrating its reliability in real-world applications.
Definition
What is AZ-1000-ECB?
AZ-1000-ECB is a high-performance, electrically conductive thermal control coating specifically designed for spacecraft and satellite surfaces exposed to harsh space environments. This specialized inorganic black coating offers exceptional solar absorptance (0.97) and thermal emittance (0.89) properties while providing electrical conductivity (10²-10⁴ Ω/sq), atomic oxygen protection, and surface charge dissipation in a single application.
Technical Specifications of AZ-1000-ECB
Before diving into applications and performance characteristics, engineers need to understand the fundamental specifications that define this electrically conductive thermal control coating. The following table outlines the key technical parameters of cured AZ-1000-ECB:
Parameter | Specification |
Surface Resistivity | 10²-10⁴ Ω/sq |
Thermal Emittance (ε_t) | 0.89 ± 0.02 |
Solar Absorptance (α_s) | 0.97 ± 0.02 at ≥ 1.5 mils thickness |
Operating Temperature Range | -180°C to 1100°C (-292°F to 2012°F) |
Appearance | Nonspecular black |
Nominal Dry Thickness | 2.5 ± 1.5 mils (over 85% of coated area) |
ASTM D3359A Adhesion Grade | Not less than 3A |
Full Cure Time | 7 days |
These specifications demonstrate the remarkable thermal and electrical properties that make this coating suitable for aerospace applications where performance is mission-critical.
Visit the Resource Center: AZ Technologies Coating Materials
Composition and Material Properties
The AZ-1000-ECB electrically conductive thermal control coating derives its performance characteristics from a specialized formulation of inorganic components. Understanding these components helps engineers appreciate how the coating achieves its unique combination of properties.
The primary components of AZ-1000-ECB include:
- Zinc oxide for enhanced electrical conductivity
- Potassium silicate as a binder system
- Distilled water as the carrier medium
This inorganic composition contributes to several advantages over organic-based alternatives:
- Superior resistance to atomic oxygen degradation
- Enhanced thermal stability across extreme temperatures
- Improved durability in vacuum environments
- Resistance to radiation damage
- Minimal outgassing in space applications
The specialized formulation creates an electrically conductive thermal control coating that maintains its properties under the extreme conditions faced by spacecraft and satellites, including rapid temperature cycling, vacuum exposure, and radiation bombardment.
Deep Dive: What is Thermal Emittance?
Discover the critical role thermal emittance plays in spacecraft temperature regulation in our comprehensive technical guide.
Learn MoreDeep Dive: What is Solar Reflectance?
Explore how solar reflectance impacts thermal management systems in aerospace applications in our detailed engineering analysis.
Learn MoreDeep Dive: What is Solar Absorptance?
Learn why precise solar absorptance values are essential for mission success in our expert breakdown of thermal control coatings.RetryClaude can make mistakes.
Learn MoreSpace-Proven Performance
When selecting an electrically conductive thermal control coating for mission-critical aerospace applications, flight heritage provides essential validation of performance claims. AZ-1000-ECB has been thoroughly tested in actual space environments through multiple missions.
The coating has been deployed on:
- Optical Properties Monitor (OPM)
- MIR MEEP POSA-I experiment
- Materials International Space Station Experiment (MISSE)
Particularly noteworthy is the MISSE testing, where the electrically conductive thermal control coating maintained its performance characteristics after four years of exposure to the space environment. This extensive in-space testing demonstrates the coating's ability to withstand:
- Atomic oxygen exposure
- UV radiation
- Micrometeoroid and debris impacts
- Extreme thermal cycling
- Vacuum conditions
These real-world validations provide engineers with confidence that the AZ-1000-ECB coating will perform as expected in their aerospace applications, particularly for long-duration missions where coating degradation could compromise system performance.
Application Process and Guidelines
Proper application is essential to achieve the specified performance characteristics of any electrically conductive thermal control coating. The application process for AZ-1000-ECB requires careful attention to surface preparation, application techniques, and curing conditions.
Surface Preparation
Before applying the AZ-1000-ECB electrically conductive thermal control coating, surfaces must be properly prepared:
- Clean the substrate thoroughly to remove all contaminants
- Ensure the surface is free from oils, greases, and particulates
- Apply appropriate primers if needed for specific substrate materials
- Maintain environmental controls during preparation and application
Application Methods
The coating can be applied using several techniques:
- Spray application for large or complex surfaces with HVLP (High Volume, Low Pressure) spray gun
- Brush application for touch-up or small areas
- Multiple thin coats are preferable to a single thick application
- Maintain recommended wet film thickness during application
Curing Requirements
To achieve optimal temperatures and performance, the electrically conductive thermal control coating requires proper curing:
- Allow for ambient temperature curing over 7 days for full properties
- Maintain appropriate environmental conditions during cure
- Protect from contamination during the curing process
- Verify coating thickness after cure using appropriate measurement techniques
Following these application guidelines ensures the AZ-1000-ECB electrically conductive thermal control coating will achieve its specified optical and electrical properties, maximizing performance in aerospace applications.
Read the guide: AZ Technology Coating Materials Guide
Why Partner with Modus Advanced for AZ-1000-ECB Application
The application process for AZ-1000-ECB requires precision and expertise to achieve optimal performance characteristics. Modus Advanced brings specialized engineering knowledge and vertically integrated manufacturing capabilities that ensure proper surface preparation, application technique, and quality control throughout the coating process.
Our team of engineers, making up over 10% of our staff, understands the critical nature of aerospace applications and follows rigorous procedures for surface cleaning, application method selection, and curing verification. We maintain strict environmental controls during preparation and application, verify coating thickness with precision instruments, and conduct comprehensive testing to ensure the electrically conductive thermal control coating meets all specified electrical and thermal properties.
When performance is mission-critical and lives depend on proper material application, our AS9100 and ISO 9001 certified processes provide the quality assurance aerospace engineers require. Partner with Modus Advanced to leverage our technical expertise in specialized coatings and reduce your time to market without compromising the integrity of your thermal management systems.
Coating ServicesKey Applications in Aerospace
The unique combination of thermal control and electrical conductivity makes AZ-1000-ECB suitable for numerous aerospace applications where traditional thermal control coatings would be insufficient. This electrically conductive thermal control coating addresses multiple engineering challenges simultaneously.
Primary applications include:
- External spacecraft surfaces requiring thermal management
- Satellite components needing electrostatic discharge protection
- Radiative surfaces for thermal control systems
- Structures exposed to atomic oxygen in low Earth orbit
- Components requiring both thermal control and electrical grounding
The coating is particularly valuable for:
- Communication satellites with sensitive electronics
- Earth observation platforms requiring precise thermal stability
- Space telescopes and optical systems
- Solar array supporting structures
- Spacecraft bus exteriors
By providing both thermal control and electrical conductivity, AZ-1000-ECB eliminates the need for separate surface treatments, reducing complexity and weight—critical considerations in aerospace design where every gram matters.
Performance Comparison with Alternative Solutions
When evaluating an electrically conductive thermal control coating for aerospace applications, engineers must consider how AZ-1000-ECB compares with alternative solutions. This analysis helps determine the most appropriate coating for specific mission requirements.
Thermal Performance Comparison
The following table compares AZ-1000-ECB with other common thermal control coatings:
Coating Type | Solar Absorptance (α_s) | Thermal Emittance (ε_t) | Electrical Conductivity | Space Environment Durability |
AZ-1000-ECB | 0.97 ± 0.02 | 0.89 ± 0.02 | 10²-10⁴ Ω/sq | Excellent |
Traditional Black Paint | 0.95-0.98 | 0.85-0.90 | Non-conductive | Poor-Fair |
Carbon-Loaded Polymers | 0.90-0.95 | 0.80-0.85 | 10⁵-10⁷ Ω/sq | Fair |
Anodized Aluminum (Black) | 0.88-0.92 | 0.80-0.85 | Non-conductive | Good |
This comparison demonstrates the unique position of the AZ-1000-ECB electrically conductive thermal control coating in providing high absorptance and emittance values while maintaining electrical conductivity and space environment durability.
Quality Control and Testing Methods
Maintaining consistent performance of electrically conductive thermal control coatings requires rigorous quality control procedures throughout the manufacturing and application process. For AZ-1000-ECB, several test methods ensure the coating meets its specified performance parameters.
Critical Property Testing
Quality control testing for AZ-1000-ECB includes:
- Surface resistivity verification using four-point probe measurements
- Solar absorptance testing using spectrophotometric analysis
- Thermal emittance evaluation using specialized infrared equipment
- Adhesion testing per ASTM D3359A standards
- Thickness measurements across coated surfaces
- Visual inspection for coating uniformity and appearance
Environmental Testing Protocols
To validate performance under operating conditions, the electrically conductive thermal control coating undergoes environmental testing:
- Thermal cycling between temperature extremes (-180°C to 1100°C / -292°F to 2012°F)
- Vacuum stability testing for outgassing characteristics
- UV radiation exposure testing
- Atomic oxygen resistance evaluation
- Mechanical vibration resistance
These testing protocols ensure the AZ-1000-ECB electrically conductive thermal control coating will perform as expected when deployed in space applications, providing engineers with confidence in the material's reliability.
Engineering Considerations and Implementation
When incorporating AZ-1000-ECB electrically conductive thermal control coating into aerospace designs, engineers should consider several factors to maximize performance and reliability. These considerations help ensure successful implementation across various mission profiles.
Design Integration Factors
Key design integration considerations include:
- Thermal expansion compatibility with substrate materials
- Electrical grounding requirements and integration
- Edge effects and coating continuity for electrical performance
- Inspection and verification methods for coated surfaces
- Repair procedures for damaged coatings
Mission-Specific Adaptation
The electrically conductive thermal control coating may require adaptation for specific mission parameters:
- Low Earth Orbit missions: Emphasis on atomic oxygen resistance
- Geosynchronous missions: Focus on radiation and charging mitigation
- Interplanetary missions: Consideration of high temperatures variations
- Long-duration missions: Stability of properties over extended periods
Understanding these engineering considerations allows for optimal integration of the AZ-1000-ECB electrically conductive thermal control coating into aerospace systems, maximizing performance benefits while minimizing potential issues.
Advancing Thermal Management in Space
The development of advanced electrically conductive thermal control coatings like AZ-1000-ECB represents a significant step forward in spacecraft thermal management technology. As space missions become more ambitious and long-duration, the demands on thermal control systems increase dramatically.
AZ-1000-ECB addresses multiple challenges that engineers face when designing spacecraft thermal management systems. The coating's combination of high solar absorptance, high thermal emittance, and electrical conductivity, all in a space-durable package, provides a versatile solution for complex thermal control challenges.
For engineers working on next-generation spacecraft and satellites, this electrically conductive thermal control coating offers a proven option that has demonstrated its performance in the ultimate test environment: space itself.
Partner with Modus Advanced for Your Critical Applications
At Modus Advanced, we understand that selecting the right materials for aerospace applications requires both technical expertise and application experience. Our engineering team specializes in helping partners identify and implement the optimal materials for their mission-critical systems, including electrically conductive thermal control coatings like AZ-1000-ECB.
Our vertical integration capabilities enable us to provide comprehensive support from material selection through application, quality control, and validation. For aerospace and defense applications where performance cannot be compromised, Modus Advanced delivers solutions that meet the highest standards of quality and reliability.
Contact our engineering team today to discuss how the AZ-1000-ECB electrically conductive thermal control coating might benefit your aerospace applications or to explore other advanced materials for your mission-critical systems. Because when lives depend on your innovation, one day matters.