Conductive Elastomers: Advanced Solutions for Aerospace EMI Shielding
March 12, 2025
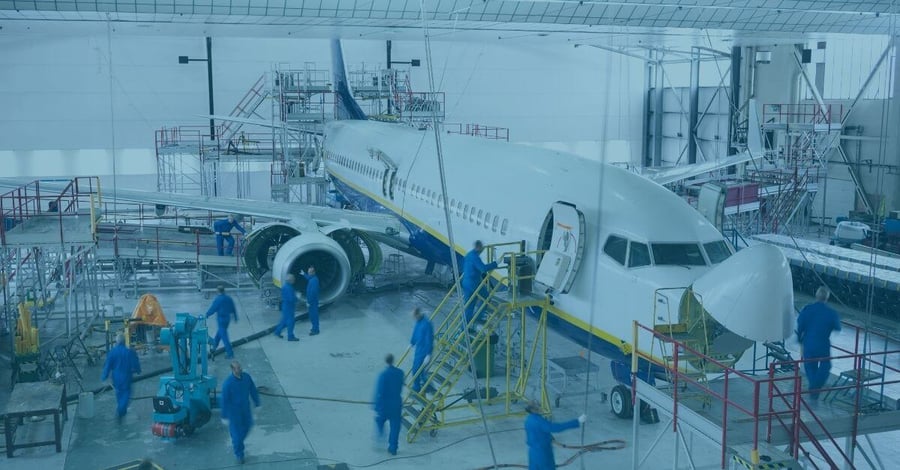
Manufactured with Speed and Precision
The manufacturing capabilities you need and the engineering support you want, all from a single partner.
Submit a DesignKey Points
- Conductive elastomers play a critical role in aerospace applications where EMI shielding is essential for mission-critical systems.
- Aerospace environments present unique challenges for conductive elastomers, including extreme temperature fluctuations, pressure differentials, and exposure to radiation.
- Material selection for aerospace conductive elastomers must balance electrical conductivity, environmental resistance, and mechanical properties.
- Working with a vertically integrated partner with AS9100 certification early in the design process can significantly improve performance outcomes and reduce development time.
In the demanding and unforgiving environment of aerospace, electromagnetic interference (EMI) presents a critical safety risk that engineers must address. Modern aircraft and spacecraft systems continue to evolve with increasing sophistication, packing more electronic components into tighter spaces.
This evolution has created an urgent need for effective EMI shielding solutions that can perform reliably under extreme conditions. Conductive elastomers have emerged as an advanced solution to this complex engineering challenge, offering the dual benefits of flexible environmental sealing and electrical conductivity essential for aerospace applications.
This article explores how conductive elastomers are transforming EMI shielding in aerospace, delivering the reliability required to protect mission-critical systems and ultimately safeguard lives in high-stakes environments.
-- Article Continues Below --
Learn everything you need to know about EMI Shielding.
What Makes Conductive Elastomers Unique for Aerospace Applications
Aerospace environments present some of the most challenging conditions for any material. Conductive elastomers used in these applications must perform reliably across extreme temperature ranges, withstand rapid pressure changes, resist various chemicals, and maintain their electrical and mechanical properties over an extended service life.
The unique advantages of conductive elastomers in aerospace applications include:
- Dual functionality: Simultaneously provides environmental sealing and EMI shielding, reducing part count and simplifying designs
- Conformability: Adapts to irregular surfaces and compensates for thermal expansion/contraction in metal housings
- Vibration damping: Absorbs shock and vibration that could otherwise damage sensitive electronic components
- Weight reduction: Offers lighter alternatives to all-metal EMI solutions, critically important for aerospace applications
- Reliability in extreme conditions: Maintains performance in the harsh conditions of aerospace environments
The combination of elasticity and conductivity makes these materials indispensable for modern aerospace designs where electronic systems must remain protected and functional in extremely demanding environments.
Critical Performance Factors for Aerospace Conductive Elastomers
When selecting a conductive elastomer for aerospace applications, several performance factors must be carefully evaluated to ensure the material will meet the stringent requirements of these mission-critical systems. The right material selection directly impacts system reliability and longevity in service.
Electrical Performance Requirements
The primary function of a conductive elastomer in aerospace applications is to provide effective EMI shielding. This electrical performance must be evaluated across several dimensions:
- Shielding effectiveness: Typically measured in decibels (dB) across specific frequency ranges relevant to aerospace applications (often 100 MHz to 40 GHz)
- Volume resistivity: Lower values (typically <0.1 ohm-cm) indicate better conductive performance
- Galvanic compatibility: Must be compatible with the housing materials to prevent corrosion
- Contact resistance: Should maintain low values under compression over time
- Attenuation performance: Must effectively reduce electromagnetic energy across the required frequency spectrum
The electrical characteristics must remain stable across the entire operating environment, making material selection particularly challenging for aerospace applications.
Environmental Resistance Factors
Aerospace conductive elastomers must withstand extreme environmental conditions while maintaining both their mechanical and electrical properties. These factors include:
- Temperature range: Typically from -65°C to +200°C for many aerospace applications
- Pressure differentials: Must maintain sealing during rapid pressure changes
- Radiation resistance: Particularly important for space applications
- Ozone resistance: Critical for high-altitude aircraft
- Fluid resistance: Must withstand exposure to aviation fuels, hydraulic fluids, and de-icing chemicals
- Salt spray resistance: Essential for maritime aerospace applications
- Humidity and moisture sealing: Must prevent moisture ingress that could compromise electronic systems
Environmental resistance factors often create trade-offs with other performance characteristics, requiring careful material selection.
Visit the full resource center here
Mechanical Performance Considerations
The mechanical properties of conductive elastomers are crucial for maintaining proper compression, sealing, and durability throughout the service life:
- Compression set: Should be minimized to maintain sealing force over time
- Compression force deflection: Must provide adequate sealing without requiring excessive closure forces
- Tear strength: Critical for installation and service durability
- Tensile strength: Must withstand installation stresses and service conditions
- Hardness: Typically measured in Shore A units, should be appropriate for the application
- Low outgassing: Essential for space applications where volatile compounds can contaminate sensitive optics or electronics
Material selection must balance these mechanical requirements with electrical and environmental performance.
Selecting the optimal conductive elastomer requires careful consideration of these interconnected performance factors to ensure reliable service in demanding aerospace environments.
Conductive Elastomer Material Options for Aerospace
The base elastomer and conductive filler combination significantly impacts performance characteristics and application suitability. Different aerospace applications may require specific material properties based on their operating environment and EMI shielding requirements.
Base Elastomer Selection
The base elastomer provides the mechanical properties and environmental resistance of the conductive material. Common options for aerospace applications include:
Base Elastomer | Temperature Range | Key Advantages | Typical Applications |
Silicone | -65°C to +200°C | Excellent temperature resistance, good compression set, UV resistant | General aerospace EMI shielding, cabin electronics |
Fluorosilicone | -55°C to +175°C | Excellent fuel and fluid resistance, good compression set | Fuel system electronics, engine compartment shielding |
EPDM | -45°C to +150°C | Weather resistant, excellent ozone resistance, cost-effective | External aircraft components, ground support equipment |
Fluorocarbon (Viton®) | -20°C to +200°C | Superior chemical resistance, excellent compression set at high temperatures | Engine and exhaust system electronics |
Each base material offers specific advantages for aerospace applications, with silicone and fluorosilicone being the most commonly specified due to their broad temperature ranges.
Conductive Filler Options
The conductive filler determines the electrical performance and often influences the cost of the material. Common fillers in aerospace applications include:
- Silver-Aluminum: Excellent conductivity, good galvanic compatibility with aluminum housings, moderate cost
- Silver-Copper: Very high conductivity, higher cost, potential galvanic issues with aluminum
- Silver-Nickel: Excellent conductivity and corrosion resistance, higher cost
- Nickel-Graphite: Good conductivity, excellent corrosion resistance, lower cost, compatible with aluminum housings
- Carbon: Lowest cost option, moderate conductivity, excellent chemical resistance
The filler selection must be compatible with the housing materials to prevent galvanic corrosion, particularly in the presence of moisture or other electrolytes common in aerospace environments.
Specialized Aerospace Formulations
Many suppliers offer specialized formulations specifically designed for aerospace applications with unique performance characteristics:
- Low outgassing formulations for space applications
- Highly conductive versions for sensitive equipment protection
- Flame-retardant grades meeting aerospace fire safety standards
- Hybrid filler systems optimizing performance across broader frequency ranges
- Custom durometer options for specific compression requirements
Working with a knowledgeable manufacturing partner who understands aerospace requirements is essential for selecting the optimal conductive elastomer formulation.
The right material choice represents a careful balance of performance requirements, environmental conditions, and cost considerations specific to each aerospace application.
Manufacturing Methods for Aerospace Conductive Elastomers
The manufacturing process selected for conductive elastomers can significantly impact performance, precision, and cost-effectiveness. Several manufacturing methods are commonly used for aerospace applications, each with distinct advantages for different design requirements.
Form-in-Place (FIP) Gaskets
Form-in-Place gasket technology is increasingly popular for complex aerospace applications with tight space constraints:
- Process: A conductive elastomer compound is dispensed directly onto the housing using CNC-controlled equipment
- Advantages: Minimal material waste, excellent for miniaturized components, no assembly required
- Typical applications: Small enclosures, board-level shielding, complex geometries
- Design considerations: Requires 0.4mm minimum wall width, typically 0.8-2.0mm gasket height
- Production volumes: Suitable for prototype through moderate production volumes
FIP gaskets offer excellent precision for the increasingly compact electronic systems in modern aerospace applications.
Die-Cut Gaskets
Die-cut gaskets from conductive elastomer sheets provide a cost-effective solution for many aerospace applications:
- Process: Sheet material is precision-cut using steel rule or chemically-etched dies
- Advantages: Cost-effective for larger parts, suitable for high-volume production
- Typical applications: Larger enclosures, access panels, connector interfaces
- Design considerations: Material thickness typically 0.5-3.0mm, requires careful handling during installation
- Production volumes: Most economical for medium to high volumes
Die-cut gaskets remain the most common manufacturing method for larger aerospace EMI shielding applications.
Molded Conductive Elastomers
For complex three-dimensional shapes or specialized profiles, molding offers unique capabilities:
- Process: Conductive compound is compression, transfer, or injection molded
- Advantages: Complex 3D geometries possible, excellent repeatability
- Typical applications: Connector interfaces, specialized shapes, high-performance requirements
- Design considerations: Higher tooling costs, excellent for complex geometries
- Production volumes: Most economical for higher volumes or complex designs
Molded conductive elastomers offer the highest level of design freedom but typically require higher production volumes to justify tooling investments.
Extruded Profiles
Extruded conductive elastomer profiles offer continuous lengths for larger applications:
- Process: Conductive compound is extruded through a die to create continuous profiles
- Advantages: Unlimited length, consistent cross-section, cost-effective
- Typical applications: Longer seams, door seals, access panels
- Design considerations: Limited to uniform cross-sections, may require splicing for closed shapes
- Production volumes: Economical even for lower volumes due to standardized tooling
Extruded profiles often provide the most cost-effective solution for longer straight runs in aerospace applications.
The selection of a manufacturing method should consider the specific design requirements, production volume, and performance needs of the aerospace application.
Working with a Manufacturing Partner on Aerospace Conductive Elastomers
Developing effective conductive elastomer solutions for aerospace applications requires specialized expertise in both material science and manufacturing processes. The right manufacturing partner can significantly reduce development time and improve performance outcomes.
Benefits of Early Design Collaboration
Involving a manufacturing partner early in the design process delivers substantial benefits:
- Identification of potential manufacturability issues before designs are finalized
- Material selection guidance based on specific application requirements
- Recommendations for design modifications to improve EMI performance
- Cost optimization through appropriate manufacturing method selection
- Reduction in development iterations and time-to-market
- Design guidance that balances electrical, mechanical, and environmental requirements
Early collaboration helps ensure designs are optimized for both performance and manufacturability from the start.
Critical Manufacturing Partner Qualifications for Aerospace
When selecting a manufacturing partner for aerospace conductive elastomers, several qualifications are essential:
- AS9100 certification: The aerospace industry standard for quality management
- ITAR registration: Required for many defense aerospace applications
- Material expertise: Deep understanding of conductive elastomer performance
- Engineering support: Access to engineers who understand aerospace requirements
- Production scalability: Capacity to move from prototype to production volumes
- Vertical integration: Multiple manufacturing processes under one roof to reduce lead times
- Quality systems: Robust quality controls with documented processes and traceability
A qualified manufacturing partner becomes an extension of your engineering team, providing valuable insights throughout the development process.
Advancing Aerospace Reliability with Conductive Elastomers
Conductive elastomers represent a sophisticated engineering solution to the complex EMI shielding challenges in modern aerospace systems. Their unique combination of electrical conductivity and mechanical flexibility makes them indispensable in applications where reliability directly impacts safety and mission success.
As aerospace systems become increasingly electronic and face growing EMI challenges, the role of conductive elastomers will continue to expand. Working with a knowledgeable manufacturing partner who understands both the material science and the rigorous demands of aerospace applications is essential for developing effective shielding solutions.
At Modus Advanced, we understand that in aerospace applications, one day matters. Our AS9100 certification, engineering expertise, and vertical integration capabilities position us as the obvious choice for aerospace engineers developing EMI shielding solutions where failure is not an option.
Contact our engineering team today to discuss your specific aerospace conductive elastomer requirements and discover how our expertise can accelerate your path to market with superior results.