Cutting-Edge Aerospace Ceramic Composites: Yttria and Alternatives
February 26, 2025
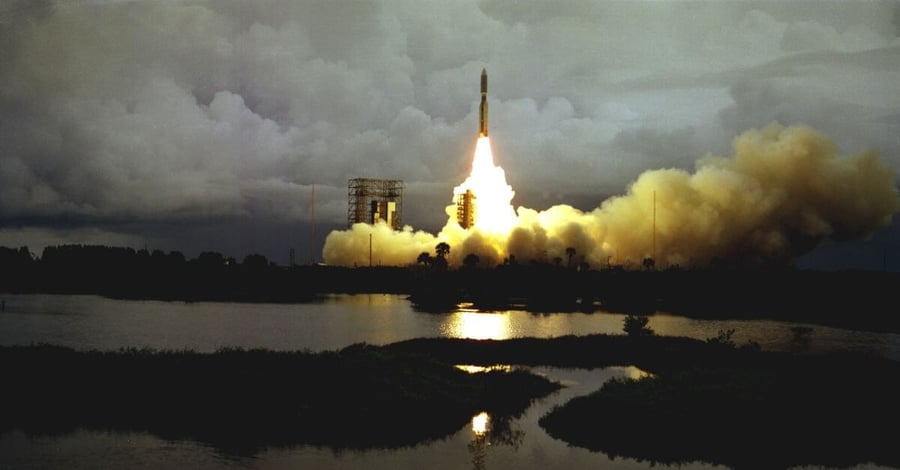
Manufactured with Speed and Precision
The manufacturing capabilities you need and the engineering support you want, all from a single partner.
Submit a DesignKey Points
- In the extreme conditions of space, yttria-based materials provide critical thermal and structural performance that can mean the difference between mission success and catastrophic failure
- While well-established in thermal barrier coatings, yttria's full potential in aerospace applications extends far beyond traditional uses
- Space-qualified alternatives to yttria offer unique advantages for specific mission requirements, particularly in thermal control and electrostatic dissipation
- Material selection for space-bound components demands careful consideration of environmental factors, manufacturing capabilities, and long-term performance
- Engineering teams must understand both yttria and its alternatives to make informed decisions that ensure mission success
When a spacecraft undergoes atmospheric reentry at temperatures exceeding 1,600°C, or when a satellite's thermal control system faces decades of solar radiation, material selection becomes a matter of mission survival. In this unforgiving realm of aerospace engineering, yttria (Y₂O₃) has emerged as a cornerstone material, enabling innovations that were once thought impossible.
Yet despite its crucial role in modern aerospace applications, from thermal barrier coatings on propulsion systems to advanced ceramic composites in structural components, many engineers aren't fully aware of yttria's capabilities – or the growing range of space-qualified alternatives available for specific mission requirements. Understanding these options can mean the difference between a material that merely survives and one that excels in the harshest environments known to engineering.
Read Our Comprehensive Guide to Optical and Thermal Coatings
The Science Behind Yttria's Excellence
Before diving into applications, we need to understand what makes yttria such a powerful material in aerospace applications. Yttria (Y₂O₃) brings several unique properties that make it indispensable in high-performance ceramic composites.
Chemical Structure and Properties
Yttria's exceptional performance stems from its fundamental atomic structure and chemical properties. As a rare earth oxide, it demonstrates remarkable stability under extreme conditions.
Properties that make yttria particularly valuable include:
- High melting point (2425°C)
- Excellent thermal stability
- Superior mechanical high strength
- Exceptional chemical resistance
- Low thermal expansion coefficient
- High thermal shock resistance
These characteristics make yttria an ideal candidate for aerospace applications where material reliability is paramount.
Thermal Performance
In aerospace applications, thermal management can mean the difference between mission success and catastrophic failure. Yttria excels in this critical area.
Key thermal properties include:
- Exceptional heat resistance
- Low thermal conductivity
- Stable performance across wide temperature ranges
- Minimal thermal expansion
- Resistance to thermal cycling fatigue
This combination of properties helps explain why yttria-containing composites are increasingly common in thermal barrier coatings for aerospace components.
Applications in Modern Aerospace
Understanding where and how yttria provides value in aerospace applications helps engineers make informed decisions about material selection. Let's explore some key applications where yttria proves invaluable.
Thermal Barrier Coatings
Yttria-stabilized zirconia (YSZ) has become the industry standard for thermal barrier coatings in aerospace applications. This vital role protects underlying components from extreme temperatures.
Common applications include:
- Turbine blade coatings
- Combustion chamber linings
- Exhaust system components
- Heat shield materials
- Propulsion system elements
The success of these applications relies heavily on yttria's unique properties and its ability to enhance the performance of ceramic composites.
Structural Components
Beyond coatings, yttria plays a crucial role in structural ceramic composites where high strength and reliability are paramount.
Key structural applications include:
- High-temperature fasteners
- Bearing components
- Sensor housings
- Electromagnetic windows
- Structural reinforcements
These applications leverage yttria's mechanical properties while taking advantage of its thermal stability.
Alternative Materials and Solutions
While yttria offers exceptional performance, aerospace engineers have access to a range of specialized coating alternatives that have proven their reliability in space applications. Understanding these alternatives, particularly their thermal control and electrostatic dissipative properties, ensures optimal material selection for specific mission requirements.
Not sure where to start? Our team of experts are ready to help. Contact our engineering team today.
Space-Qualified Thermal Control Coatings
Space-proven thermal control coatings offer reliable alternatives to yttria-based solutions, particularly for exterior spacecraft applications. These materials have undergone extensive testing and real-world validation on platforms including the International Space Station, MIR space station, and various satellite systems.
White thermal control coatings include:
- AZ-93: An inorganic white coating with low solar absorption (0.15±0.02) and high thermal emittance (0.91±0.02)
- AZW/LA-II: Superior solar reflection properties with absorption of 0.09±0.02
- AZ-2100-IECW: Combines thermal control with electrostatic dissipative properties
- AZ-400-LSW: Organic-based coating suitable for specific thermal management applications
Black thermal control options include:
- ML-210-IB: High absorption (0.98±0.02) inorganic coating
- AZ-1000-ECB: Electrically conductive black coating with superior thermal properties
- MLS-85-SB: Organic-based coating for specialized applications
Each of these alternatives has been space-qualified and offers:
- Low outgassing properties essential for space applications
- Proven stability in the space environment
- Compliance with toxicity requirements
- Meeting stringent flammability standards
- Documented performance in long-duration space exposure
Specialized Coating Systems
Modern aerospace applications often require specialized coating systems that can be tailored to specific mission requirements. These systems offer precise control over critical properties including solar absorption, thermal emittance, and electrical conductivity.
Key coating system categories include:
- Thermal Control Coatings (TCC): Precisely engineered for thermal management
- Electrostatic Dissipative (ESD) Coatings: Managing static charge in space
- High Temperature Low Emittance Coatings: Such as AZ-3700-LSW for specialized applications
- Color Coatings for Navigation and Identification: Including mission-specific markers and logos
- Hybrid Systems: Combining multiple properties like thermal control and conductivity
These systems can be further customized with properties such as:
- Solar absorptance (α_s) from 0.09 to 0.98
- Thermal emittance (ε_t) from 0.25 to 0.91
- Sheet resistance ranging from 102 to 109 Ω/sq
- Custom colors for specific mission requirements
The key is selecting the right combination for your specific application requirements.
Everything you need to know about optical and thermal coatings
Design Considerations
Successful implementation of yttria-based materials requires careful consideration of various design factors. Understanding these considerations helps ensure optimal performance.
Environmental Factors
Aerospace components face extreme environmental conditions that must be considered during material selection.
Critical environmental considerations include:
- Temperature extremes
- Pressure variations
- Chemical exposure
- Radiation exposure
- Thermal cycling
These factors significantly impact material performance and longevity.
Manufacturing Considerations
The practicality of manufacturing with yttria-based materials must be carefully evaluated during the design phase.
Key manufacturing considerations include:
- Processing temperature requirements
- Forming methods
- Sintering conditions
- Surface preparation needs
- Quality control measures
Working with an experienced manufacturing partner, such as Modus Advanced, can help navigate these considerations effectively.
Maximizing Performance Through Material Expertise
Contact our engineering team today to discuss your specific application requirements and explore how our expertise in advanced ceramic material can support your aerospace innovations. Because when it comes to aerospace applications, one day matters – and so does choosing the right manufacturing partner.
Our team of engineers can help you:
- Evaluate material options for your specific application
- Optimize design for manufacturability
- Ensure quality control throughout production
- Accelerate time to market
- Maintain the highest standards of precision and reliability
Ready to explore how yttria-based materials can enhance your aerospace components? Contact our engineering team today to start the conversation about your next project.
