Optimizing for Application of Thermal Control Coatings for Spacecraft: Design Guidance for Engineers
February 10, 2025
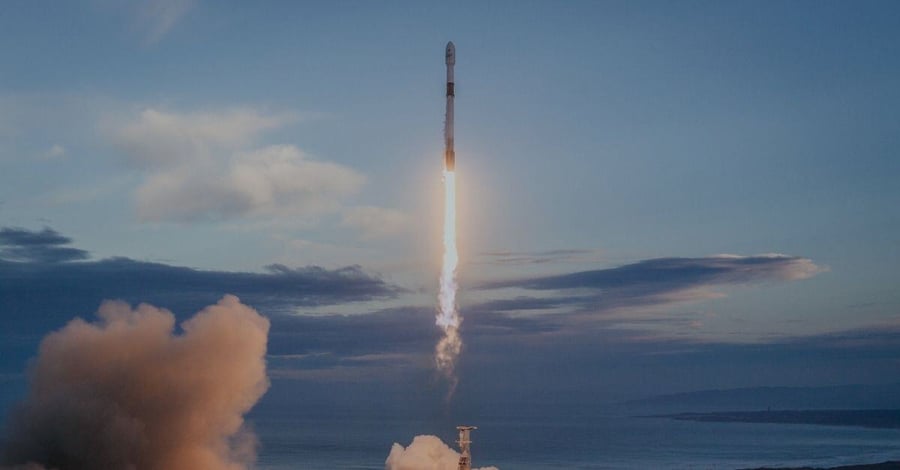
Manufactured with Speed and Precision
The manufacturing capabilities you need and the engineering support you want, all from a single partner.
Submit a DesignKey Points
- Design decisions significantly impact the performance of thermal control coatings that manage solar reflectance, absorptance, and emittance in space environments
- Critical design considerations ensure optimal coating application while maintaining precise thermal properties
- Understanding the relationship between part geometry and coating performance helps balance thermal requirements with manufacturing feasibility
- Early collaboration with manufacturing partners can identify design modifications that improve coating outcomes while maintaining thermal control properties
When designing components for space applications, thermal control coatings play a crucial role in managing heat in the harsh environment of space. These specialized coatings, characterized by their solar reflectance, solar absorptance, and thermal emittance properties, help protect spacecraft components from extreme temperature variations.
While engineers often focus on the thermal requirements of their designs, understanding how design choices impact coating application and performance can mean the difference between a component that maintains optimal thermal properties in orbit and one that fails prematurely.
Critical Surface Identification
Before diving into specific design guidance, it's essential to identify which surfaces require thermal control coatings based on their exposure to solar radiation and the desired thermal properties.
Surfaces typically requiring thermal control coating include:
- Areas exposed to direct solar radiation: These surfaces require coatings to protect components from extreme temperature fluctuations caused by direct sun exposure in space, where temperatures can swing hundreds of degrees between sunlight and shadow.
- Surfaces requiring specific solar reflectance properties: These areas need coatings with precise reflectance values to either deflect solar energy away from sensitive components or help maintain specific operating temperatures for optimal performance.
- Regions needing precise thermal emittance control: These surfaces require coatings to regulate how much heat the component releases into space, helping maintain critical operating temperatures for electronics and other temperature-sensitive systems.
- External surfaces managing heat dissipation: These areas need coatings to help radiate excess heat into space since traditional convection cooling doesn't work in the vacuum environment, making radiation the only way to shed heat from spacecraft components.
Surfaces that often should remain uncoated include:
- Mating surfaces and fastener interfaces: Coating in these areas could break down during assembly or operation, creating debris and potentially compromising the mechanical integrity of fastened connections or affecting the designed torque specifications.
- Internal surfaces not exposed to solar radiation: Adding unnecessary coating to these surfaces provides no thermal benefit while adding weight to the spacecraft - a critical consideration since every ounce costs significantly more to launch into space.
- Areas where coating debris could create foreign object damage (FOD): Since many thermal control coatings like AZ-93 are ceramic-based, any coating damage could create particles (FOD) that become dangerous projectiles in zero gravity, potentially damaging sensitive equipment or mechanisms.
- Surfaces involved in thermal conduction between components: Coatings can act as thermal insulators, so applying them to surfaces meant for thermal conduction between components could disrupt designed heat transfer paths and compromise the overall thermal management system.
Spacecraft thermal control coating plays a pivotal role in managing the delicate balance between heat absorption and dissipation on a spacecraft surface. The effectiveness of a thermal coating depends not only on its material properties but also on how it interacts with the spacecraft's geometry. Surfaces with high solar absorption must be carefully coated to prevent overheating, while others with lower absorption are optimized to reflect solar energy. Ensuring the uniform application of coatings across spacecraft surfaces is critical to maintaining consistent thermal properties, especially in regions exposed to direct sunlight or harsh temperature fluctuations. Thoughtful design and precise application help maximize the coating's performance in regulating heat transfer in space's extreme environment.
Design for Coating Performance
The success of thermal control coatings in space applications hinges on much more than just the coating material properties themselves. The underlying geometry of your part plays a crucial role in how effectively these coatings can perform their critical function of managing solar reflectance, absorptance, and emittance.
While a coating like AZ-93 might have excellent thermal properties on paper, its real-world performance in space depends heavily on how well it can be applied to your component's surfaces. This means design decisions you make early in development can either enhance or compromise your coating's ability to protect your component from the extreme thermal environment of space.
Consider these factors when designing for optimal thermal performance:
- Maintain consistent surface geometry to ensure uniform coating thickness
- Account for how surface features might affect solar reflectance properties
- Design surfaces to achieve desired emittance properties across different viewing angles
- Consider how thermal cycling might affect coating adhesion in different areas
The more thoughtfully designed your surfaces are, the more reliable your thermal control properties will be in space applications.
Masking Considerations
The precision required for thermal control coatings in space applications creates a unique manufacturing challenge: how to protect surfaces that must remain uncoated while ensuring optimal coating performance on critical surfaces. This isn't as simple as just taping off certain areas.
The masking process for space components requires careful consideration because it directly impacts both manufacturing efficiency and coating performance. Improper masking can lead to coating irregularities that affect thermal properties, create potential contamination risks, or add unnecessary manufacturing complexity and cost to your component.
Masking is often necessary to protect surfaces that must remain uncoated, but excessive masking requirements can affect both manufacturing efficiency and thermal performance.
Key masking design considerations include:
- Create clear boundaries between surfaces requiring different thermal properties
- Design adequate space around features requiring masking to maintain coating precision
- Consider incorporating masking features that don't compromise thermal performance
- Minimize complex geometries that could create thermal control inconsistencies
Thoughtful masking design can help achieve precise thermal properties while reducing manufacturing complexity.
Read how this DoD contractor improved product quality by partnering with Modus Advanced.
Material Transitions and Edges
One of the most challenging aspects of thermal control coating design lies in managing the transitions between coated and uncoated surfaces. These interfaces are potential weak points where coating failures often begin, and in space applications, even a small coating failure can cascade into significant thermal management issues.
The geometry of these transitions affects not just manufacturing feasibility but also the long-term reliability of your thermal control system, particularly when subjected to the extreme temperature cycles experienced in orbit.
The interface between coated and uncoated surfaces requires careful consideration to maintain thermal control properties while ensuring coating integrity.
Design recommendations for thermal control transitions:
- Provide clear demarcation lines where different thermal properties are required
- Avoid sharp edges where coating thickness could affect thermal performance
- Consider incorporating small steps or channels to create natural coating boundaries
- Design gradual transitions where possible to maintain consistent thermal properties
Proper attention to these transitions during design can prevent coating failures and maintain consistent thermal performance in space.
Working with Your Manufacturing Partner
The complexity of thermal control coatings for space applications makes early collaboration with your manufacturing partner not just beneficial, but essential for project success. Having manufactured numerous components for space applications, we've seen firsthand how small design decisions can have major implications for coating application and performance.
The insights gained from this practical manufacturing experience often reveal opportunities to optimize designs in ways that aren't obvious from a purely theoretical engineering perspective. This is particularly true for complex geometries where coating application challenges might not be apparent until you understand the practical limitations of the coating process.
Early collaboration with your manufacturing partner can help optimize your design for both thermal performance and manufacturing feasibility. Benefits of early manufacturing involvement:
- Validation of coating specifications for thermal control requirements
- Guidance on geometry optimization for consistent coating application
- Understanding of process limitations that could affect thermal properties
- Cost-saving design modifications while maintaining thermal performance
Remember that manufacturers with space component experience understand the critical nature of thermal control coatings and can provide valuable insight into design improvements.
Final Thoughts
Designing components for optimal thermal control in space requires careful consideration of both coating performance and manufacturing feasibility. By incorporating these design considerations early in your development process and working closely with experienced manufacturing partners, you can create components that maintain precise thermal properties while remaining efficiently manufacturable.
The Modus Advanced engineering team has extensive experience in manufacturing thermal control coated components for space applications. Our AS9100 certification and ITAR compliance, combined with our vertically integrated manufacturing capabilities, make us an ideal partner for optimizing your designs for thermal performance in space. Contact our engineering team today to discuss your specific thermal control requirements.