Enhancing Durability in High-Temperature Aerospace Applications
March 26, 2025
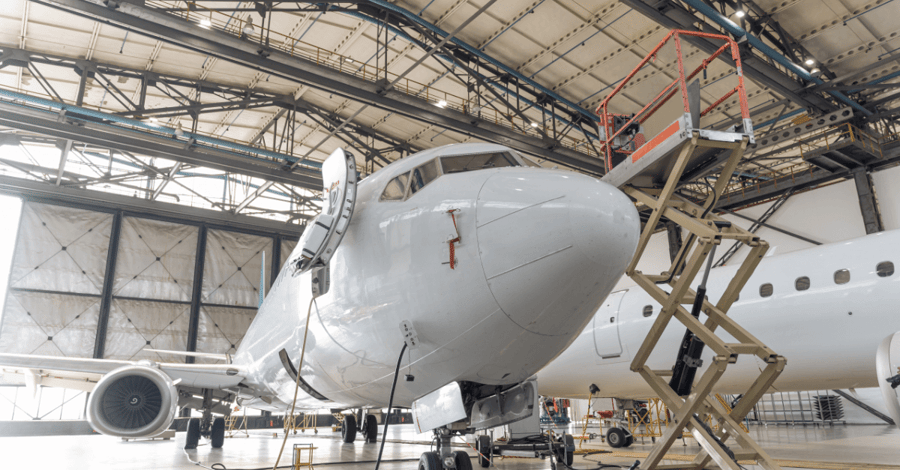
Manufactured with Speed and Precision
The manufacturing capabilities you need and the engineering support you want, all from a single partner.
Submit a DesignKey Points
- High-temperature durability represents one of the most critical challenges in aerospace engineering, where component failure could lead to catastrophic results
- Material selection, coating technologies, and design considerations must work in harmony to protect components in extreme thermal environments
- Comprehensive testing and validation processes are essential for ensuring long-term reliability in mission-critical applications
- Modern manufacturing techniques, when properly leveraged, can significantly improve component durability while reducing production time
- Strategic supplier partnerships are vital for achieving optimal durability outcomes, particularly when working with advanced materials and processes
When lives depend on your aerospace innovations, every decision about materials, coatings, and manufacturing processes takes on heightened importance. Let's explore the comprehensive approach needed to enhance durability in these demanding applications.
Read Our Comprehensive Guide to Optical and Thermal Coatings
Understanding the Stakes
The aerospace industry operates in an environment where failure isn't an option. Every component must perform reliably under extreme conditions, often experiencing temperature cycles from -65°F to well over 2000°F.
Aircraft engines, rocket propulsion systems, and hypersonic vehicles all rely on components that must maintain their structural integrity and performance characteristics despite these brutal conditions.
Critical Failure Points
Before we can enhance durability, we must understand where and why components typically fail in high-temperature and harsh aerospace applications. The primary failure modes in high-temperature aerospace applications can be categorized into several key areas:
Failure Mode | Description | Primary Impact Areas |
Damage from repeated heating/cooling cycles | Turbine blades, combustion chambers | |
Oxidation/Corrosion | Chemical degradation at high temperatures | Exhaust systems, heat exchangers |
Mechanical Wear | Surface degradation accelerated by heat | Bearings, actuators, sliding surfaces |
Creep Deformation | Progressive deformation under sustained loads | Structural components, fasteners |
Thermal Shock | Rapid temperature change damage | Leading edges, thermal protection systems |
Understanding these failure modes is essential for developing effective durability solutions that protect mission-critical components.
Material Selection Strategies
Choosing the right materials forms the foundation of durability enhancement in high-temperature aerospace applications. The selection process must balance multiple competing factors including temperature resistance, strength-to-weight ratio, and cost-effectiveness.
High-Temperature Superalloys
Modern aerospace applications rely heavily on superalloys engineered specifically for extreme environments. Nickel-based superalloys remain the gold standard for their exceptional strength retention at high temperatures, particularly in jet engine components where temperatures can exceed 2000°F. Cobalt-based alloys excel in wear-resistant applications, while titanium aluminides offer an excellent balance of strength and weight savings.
The following table outlines key superalloy characteristics for aerospace applications:
Alloy Type | Temperature Range | Key Properties | Typical Applications |
Nickel-based | Up to 2200°F | High strength, oxidation resistance | Turbine blades, combustors |
Cobalt-based | Up to 2000°F | Wear resistance, thermal fatigue resistance | Vanes, shrouds |
Titanium Aluminides | Up to 1500°F | Low density, high specific strength | Compressor blades, structural components |
Refractory Metals | Up to 3000°F | Ultra-high temperature capability | Rocket nozzles, heat shields |
Advanced Composites
Composite materials have revolutionized aerospace design by offering unique combinations of properties unattainable with traditional materials. Ceramic matrix composites (CMCs) stand out for their ability to maintain strength at temperatures where metals begin to fail. These materials can operate at temperatures up to 2700°F while providing significant weight savings.
Carbon-carbon composites push the temperature envelope even further, remaining stable at temperatures exceeding 3000°F in non-oxidizing environments. These materials find critical applications in rocket nozzles and hypersonic vehicle leading edges where extreme heat resistance is paramount.
Advanced Coating Technologies
Protective coatings serve as the first line of defense in high-temperature aerospace applications. A well-designed coating system can dramatically extend component life while improving overall system reliability. Modern coating technologies have evolved to provide multi-functional protection against thermal, mechanical, and chemical degradation.
Thermal Barrier Coatings
Thermal barrier coating systems represent one of the most significant advances in high-temperature component protection. These sophisticated multi-layer systems typically consist of:
- A ceramic top coat that provides primary thermal insulation
- A thermally grown oxide layer that develops during service
- A metallic bond coat that ensures adhesion and oxidation resistance
- The substrate material being protected
The performance characteristics of common TBC systems are outlined below:
Coating System | Temperature Reduction | Key Benefits | Limitations |
150-200°F | Proven reliability, good strain tolerance | Limited to 2400°F max | |
Low-k YSZ | 200-250°F | Enhanced insulation | Higher cost |
Gadolinium Zirconate | 200-300°F | Superior CMAS resistance | Lower toughness |
Multi-layer Systems | 250-350°F | Optimized performance | Complex application |
Surface Engineering
Beyond traditional coatings, advanced surface engineering techniques provide additional options for enhancing component durability. These processes modify the surface structure and composition of materials to achieve specific performance characteristics.
Plasma nitriding, for instance, creates a hardened surface layer that significantly improves wear resistance while maintaining core material properties. This process proves particularly effective for components subject to both high temperatures and mechanical wear.
Design Considerations for Durability
Enhancing durability begins at the design phase. Engineers must consider how design choices impact component longevity in high-temperature environments. This requires a holistic approach that accounts for thermal management, structural optimization, and manufacturing constraints.
Learn more about our Design for Manufacturability (DfM) process here.
Thermal Management
Effective thermal management represents a cornerstone of durable high-temperature design. This encompasses several key strategies:
Internal Cooling Networks: Modern aerospace components often incorporate sophisticated internal cooling passages. These networks must be carefully designed to provide uniform temperature distribution while maintaining structural integrity. Advanced manufacturing techniques, particularly additive manufacturing, have revolutionized the ability to create complex cooling geometries that were previously impossible to manufacture.
Thermal Barriers: Strategic placement of thermal barriers and heat shields requires careful analysis of heat flow paths and thermal gradients. The goal is to protect critical components while managing overall system thermal efficiency.
Active Cooling Systems: In extreme applications, active cooling systems may be necessary. These systems must be integrated into the component design from the beginning, with careful consideration of fluid dynamics, heat transfer, and system reliability.
Structural Optimization
Structural design for high-temperature applications must account for both thermal and mechanical loads. Key considerations include:
Thermal Expansion: Components must accommodate thermal expansion without developing excessive stresses. This often requires careful attention to mounting arrangements and clearances.
Stress Distribution: Design features should promote uniform stress distribution and avoid concentrations that could lead to premature failure. This becomes particularly important in areas subject to thermal cycling.
Fail-Safe Features: Critical components should incorporate redundancy or fail-safe features where possible to prevent catastrophic failure modes.
Everything you need to know about optical and thermal coatings
Manufacturing Considerations
The manufacturing process significantly impacts component durability in high-temperature applications. Modern manufacturing techniques offer new possibilities for enhancing durability, but they must be carefully selected and controlled to ensure consistent quality.
Process Selection Matrix
Manufacturing Process | Advantages | Best Applications | Quality Considerations |
Additive Manufacturing | Complex geometries, internal features | Cooling systems, structural components | Powder quality, process parameters |
Excellent surface finish, tight tolerances | Critical mating surfaces, seals | Tool selection, cutting parameters | |
Advanced Joining | Join dissimilar materials, complex assemblies | Multi-material components | Joint preparation, process control |
Near-net-shape Processing | Reduced residual stress, material efficiency | Large components, superalloys | Temperature control, cooling rates |
Partnership Approach to Enhancing Durability in Aerospace Applications
Enhancing durability in high-temperature aerospace applications requires a comprehensive approach that considers materials, coatings, design, manufacturing, and testing. Success depends on making informed choices at every step of the process and working with partners who understand what's at stake.
The right manufacturing partner becomes an extension of your engineering team, helping ensure success from design through production. At Modus Advanced, we combine deep engineering expertise with advanced manufacturing capabilities to help you create components that perform reliably in the most demanding aerospace applications.
Contact our team of engineers today to discuss your high-temperature durability challenges.