Organic vs. Inorganic Coatings for Aerospace Applications: Making the Right Choice for Critical Components
May 7, 2025
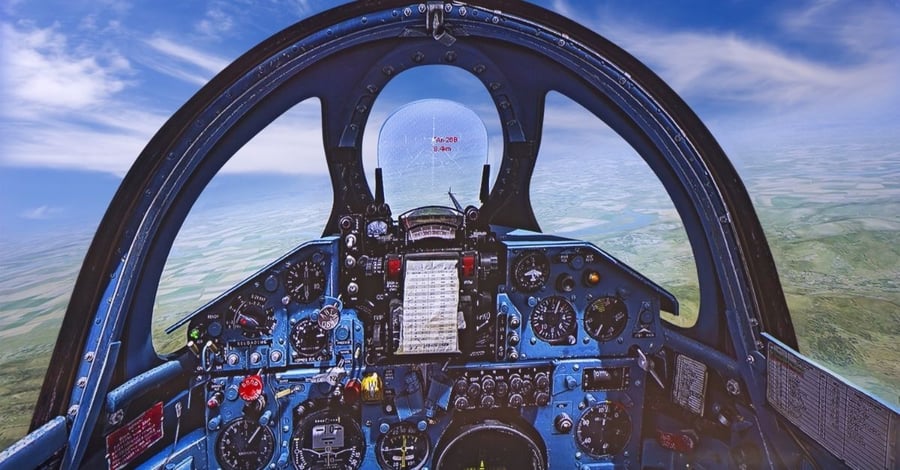
Manufactured with Speed and Precision
The manufacturing capabilities you need and the engineering support you want, all from a single partner.
Submit a DesignKey Points
- Aerospace coatings must withstand extreme conditions while providing protection against corrosion, erosion, thermal cycling, and other environmental stressors.
- Organic coatings offer excellent flexibility, impact resistance, and color options but typically have temperature limitations and shorter service lives.
- Inorganic coatings provide superior temperature resistance, hardness, and durability but may be more brittle and have limited color options.
- The cost equation differs significantly between coating types. Inorganic coatings often have lower material costs but higher labor costs.
- Selection criteria should include operating environment, substrate material, service life requirements, cost considerations, and application method requirements.
- The aerospace industry often employs a strategic combination of both coating types to maximize performance and protection across different aircraft components.
The High-Stakes World of Aerospace Coatings
In aerospace applications, coating selection is never simply about aesthetics. These specialized protective layers stand as the first line of defense against extreme conditions that would rapidly degrade unprotected components. From the scorching heat of engine compartments to the corrosive assault of high-altitude environments, aerospace coatings must perform flawlessly where failure is not an option.
Engineers designing components for aerospace applications face critical decisions when selecting protective coatings. The choice between organic and inorganic formulations carries significant implications for performance, durability, safety, and cost.
This technical deep-dive explores the fundamental differences between these coating types, their respective advantages and limitations, and the key considerations that should guide your selection process.
Read Our Comprehensive Guide to Optical and Thermal Coatings
Organic vs. Inorganic Coatings
Organic coatings, derived from carbon-based compounds like epoxies and polyurethanes, offer excellent flexibility, impact resistance, and color options at lower initial cost but face limitations in temperature resistance and service life. Inorganic coatings, based on metallic, ceramic, or mineral compounds, provide superior temperature resistance up to 2000°F, exceptional durability, and chemical stability at higher initial cost but may be more brittle and have more complex application requirements.
Understanding the Fundamental Differences
Organic and inorganic coatings represent two distinct approaches to surface protection, each with unique chemical compositions and performance characteristics. Understanding these differences provides the foundation for making informed engineering decisions.
Organic coatings derive from carbon-based compounds and typically include materials such as epoxies, polyurethanes, silicones, and acrylics. These coatings form through the polymerization of organic molecules, creating flexible, adherent films that bond to substrate materials.
Inorganic coatings, conversely, rely on metallic, ceramic, or mineral-based compounds such as chromates, phosphates, silicates, and ceramics. These coatings often form through chemical conversion, thermal processing, or deposition techniques, creating hard, dense protective layers.
The fundamental chemical differences between these coating types translate directly to their performance characteristics and cost structures in aerospace applications. Let's examine these differences in detail.
Performance Comparison: Organic vs. Inorganic Coatings
When evaluating coating options for aerospace applications, engineers must consider multiple performance criteria. The table below provides a side-by-side comparison of key performance attributes:
Performance Attribute | Organic Coatings | Inorganic Coatings |
Temperature Resistance | Limited (typically 177-204°C / 350-400°F max) | Superior (up to 1093°C / 2000°F for ceramics) |
Corrosion Protection | Good to excellent (barrier protection) | Excellent (barrier and sacrificial protection) |
Flexibility/Impact Resistance | Excellent | Limited (often brittle) |
Chemical Resistance | Varies by formulation | Generally excellent |
UV Resistance | Moderate (may degrade over time) | Excellent |
Abrasion Resistance | Moderate | Excellent |
Electrical Properties | Can be conductive or insulating | Can be conductive or insulating |
Weight | Generally lightweight | Can be heavier |
Service Life | Typically shorter | Generally longer |
Application Complexity | Often simpler | May require specialized equipment |
The performance characteristics outlined above translate directly to specific advantages, limitations, and cost implications for each coating type in aerospace applications.
Everything you need to know about optical and thermal coatings
Cost Comparison: Organic vs. Inorganic Coatings
Cost considerations play a critical role in coating selection, encompassing both initial application expenses and lifecycle costs. The table below outlines typical cost differences between organic and inorganic coating systems:
Cost Factor | Organic Coatings | Inorganic Coatings |
Material Costs | ||
Base Material | Typically higher cost per gallon | Typically lower cost per gallon |
Primer Requirements | Sometimes requires separate primer system, adding $30-100 per gallon | Some systems are self-priming, others require specialized primers at $100-300 per gallon |
Volume Efficiency | Higher solids content varieties provide better coverage per gallon | Often requires multiple layers to achieve desired thickness |
Waste Factor | 20-40% typical overspray/waste | 30-60% typical overspray/waste for thermal spray applications |
Application Costs | ||
Labor Requirements | Relatively straightforward application process | Requires specialized training, certification, and additional steps typically resulting in 1.5-2x the cost of applying organic components |
Curing/Processing Time | 1-24 hours typical cure time | May require extended processing (24-72+ hours for some ceramic systems) |
Surface Preparation | Standard cleaning and pretreatment | Often requires extensive surface preparation, including blasting |
Lifecycle Costs | ||
Durability | 2-7 years typical service life | 7-20+ years typical service life |
Repair/Maintenance | Relatively easy field repair | Often requires specialized repair procedures |
Removal/Replacement | Simpler chemical or mechanical removal | May require extensive mechanical methods |
The cost equation varies significantly based on specific application requirements, environmental conditions, and service life expectations. Initial cost advantages for organic systems may be offset by more frequent replacement requirements over the component's service life.
Organic Coatings: Advantages and Limitations
Organic coatings offer several distinct benefits that make them valuable for specific aerospace applications. These advantages must be weighed against their inherent limitations for informed decision-making.
Key Advantages of Organic Coatings
- Superior Flexibility and Impact Resistance: Organic coatings can flex with substrate materials during thermal cycling and withstand mechanical impacts without cracking or delaminating.
- Excellent Adhesion: Modern organic formulations achieve strong molecular bonding with properly prepared substrates, ensuring coating integrity even under stress.
- Wide Range of Application Methods: These coatings can be applied via spraying, dipping, brushing, or electrostatic processes, providing flexibility in manufacturing.
- Extensive Color Options: Organic coatings offer virtually unlimited color possibilities, important for identification, aesthetics, and solar reflectance management.
- Self-Healing Capabilities: Some advanced organic formulations incorporate self-healing mechanisms to address minor damage autonomously.
- Cost-Effective Initial Application: Lower equipment costs and simpler application processes typically result in 30-50% lower initial application costs compared to many inorganic systems.
The versatility and cost advantages of organic coatings make them particularly valuable for components exposed to varying mechanical stresses and impacts where regular inspection and maintenance are feasible.
Limitations of Organic Coatings
Despite their advantages, organic coatings face significant limitations in aerospace applications:
- Temperature Constraints: Most organic coatings degrade at temperatures above 177-204°C (350-400°F), making them unsuitable for high-temperature components.
- UV Vulnerability: Extended exposure to ultraviolet radiation can cause degradation, including chalking, fading, and reduced protective properties.
- Limited Service Life: Organic coatings typically require more frequent inspection and replacement than their inorganic counterparts, increasing lifecycle costs despite lower initial application expenses.
- Outgassing Concerns: Some organic formulations may release volatile organic compounds (VOCs) in vacuum environments, potentially contaminating sensitive instruments.
- Oxygen Sensitivity: Certain organic coatings may degrade more rapidly in oxygen-rich environments, particularly at elevated temperatures.
These limitations require careful consideration when specifying coatings for long-service aerospace applications or components exposed to extreme conditions.
Inorganic Coatings: Advantages and Limitations
Inorganic coatings provide performance characteristics that make them essential for demanding aerospace applications. Understanding their specific advantages and limitations is crucial for appropriate implementation.
Key Advantages of Inorganic Coatings
Inorganic coatings excel in extreme environments where organic alternatives would quickly fail:
- Exceptional Temperature Resistance:Ceramic-based inorganic coatings can withstand temperatures up to 1093°C (2000°F), making them ideal for engine components and thermal barriers.
- Superior Hardness and Wear Resistance: The crystalline or amorphous structures of inorganic coatings provide exceptional protection against erosion, abrasion, and wear.
- Extended Service Life: Many inorganic coatings provide decades of protection without significant degradation, reducing maintenance requirements and lifecycle costs despite higher initial investment.
- Excellent Chemical Stability: These coatings resist attack from fuels, hydraulic fluids, de-icing chemicals, and other aerospace chemicals.
- Zero Outgassing: Inorganic coatings are ideal for space applications where outgassing must be minimized or eliminated entirely.
The robustness of inorganic coatings makes them indispensable for components subjected to extreme thermal, chemical, or mechanical stresses, often providing better long-term value despite higher initial costs.
Limitations of Inorganic Coatings
Despite their impressive performance, inorganic coatings face several significant limitations:
- Inherent Brittleness: Most inorganic coatings lack the flexibility of organic alternatives, making them susceptible to cracking under impact or substrate flexing.
- Application Challenges: Many inorganic coatings require specialized application equipment and precise process control, increasing manufacturing complexity and initial costs by 50-200% compared to organic alternatives.
- Limited Color Options: The chemical nature of many inorganic coatings restricts available colors, sometimes limiting their use on external surfaces.
- Potential for Galvanic Corrosion: Some metallic inorganic coatings may create galvanic cells with substrate materials if not properly engineered.
- Higher Weight: Certain inorganic coatings add more weight per unit area than organic alternatives, a critical consideration in aerospace design.
- Higher Initial Cost: Materials and application expenses can be 2-5 times higher than comparable organic systems, though this may be offset by longer service life.
These limitations require careful engineering consideration when implementing inorganic coatings in aerospace applications.
Application-Specific Selection Criteria
Choosing between organic and inorganic coatings requires a systematic evaluation of multiple factors specific to the application at hand. Engineers should consider these critical selection criteria:
Environmental Exposure Factors
The operating environment dictates many coating requirements:
- Temperature Profile: Maximum and minimum temperatures, thermal cycling frequency, and rate of temperature change
- UV Exposure: Duration and intensity of ultraviolet radiation exposure
- Chemical Exposure: Contact with fuels, hydraulic fluids, de-icing chemicals, and atmospheric pollutants
- Moisture Conditions: Humidity levels, condensation cycles, and direct water exposure
- Altitude Considerations: Pressure differentials, ozone concentration, and radiation exposure
Environmental factors often establish the initial constraints that determine viable coating options.
Substrate Compatibility
The underlying material significantly influences coating selection:
- Thermal Expansion Coefficient: Must be compatible to prevent delamination during thermal cycling
- Surface Chemistry: Affects adhesion mechanisms and required surface preparation
- Electrical Properties: Important for managing static discharge and preventing galvanic corrosion
- Flexibility Requirements: Dictates needed coating flexibility, especially for composite structures
Successful coating systems begin with thorough substrate analysis and preparation protocols.
Cost-Benefit Analysis
A comprehensive cost evaluation should include:
- Initial Application Costs: Material costs, equipment requirements, labor, and processing time
- Expected Service Life: Projected durability under the specific operating conditions
- Maintenance Requirements: Frequency and complexity of inspection and repair procedures
- Replacement Costs: Expenses associated with removal and reapplication
- Operational Impact: Cost implications of component downtime during maintenance
The most economical solution often comes from balancing initial costs against total lifecycle expenses, particularly for components with extended service requirements.
Application Method Considerations
Manufacturing constraints impact coating feasibility:
- Component Geometry: Complex shapes may limit application methods
- Production Volume: May dictate economically viable application processes
- Cure Requirements: Temperature and time constraints of the manufacturing process
- Quality Control Access: Ability to inspect and verify coating integrity
Application method limitations can sometimes override performance considerations in practical implementation.
Real-World Applications: Strategic Selection Examples
In practice, aerospace engineers often make strategic coating selections based on component-specific requirements. These examples illustrate typical decision-making processes:
External Aircraft Surfaces
Common Selection: High-performance organic polyurethane topcoats over epoxy primers
Key Decision Factors:
- Need for flexibility on moving surfaces and during pressurization cycles
- Requirement for specific colors for thermal management and identification
- Exposure to UV radiation and varying weather conditions
- Moderate temperature requirements (typically -54°C to 82°C / -65°F to 180°F)
The flexibility, color options, adequate environmental protection, and moderate cost make organic systems the standard choice for external surfaces.
Engine Components
Common Selection: Ceramic thermal barrier coatings or other high-temperature inorganic systems
Key Decision Factors:
- Extreme temperature exposure (potentially exceeding 816°C / 1500°F)
- Thermal cycling stresses
- Exposure to combustion products and high-velocity particulates
- Critical safety implications of coating failure
Despite significantly higher initial costs (often 5-10 times more expensive than organic alternatives), the temperature requirements alone typically eliminate organic options for these applications. The extended service life and reduced maintenance requirements help offset the higher initial investment.
Landing Gear Components
Common Selection: Hard chrome plating or other wear-resistant inorganic coatings
Key Decision Factors:
- Extreme mechanical wear requirements
- Exposure to runway debris, brake dust, and hydraulic fluids
- Wide temperature variations and weather exposure
- Extended service life requirements
The combination of wear resistance and chemical exposure typically favors inorganic solutions for these critical components, with the higher initial costs justified by 3-5 times longer service intervals compared to organic alternatives.
Engineering the Right Solution with Modus Advanced
Selecting the optimal coating for aerospace applications requires balancing performance requirements, manufacturing constraints, cost considerations, and long-term reliability requirements. The choice between organic and inorganic coatings is rarely straightforward, often demanding custom solutions for specific applications.
When lives depend on your aerospace innovation, choose a partner who understands what's at stake. Because one day matters.
Contact our engineering team today to discuss your specific coating requirements and discover how our technical expertise can accelerate your path to an optimal solution.