What is Galvanic Compatibility? Definition and FAQs
April 25, 2025
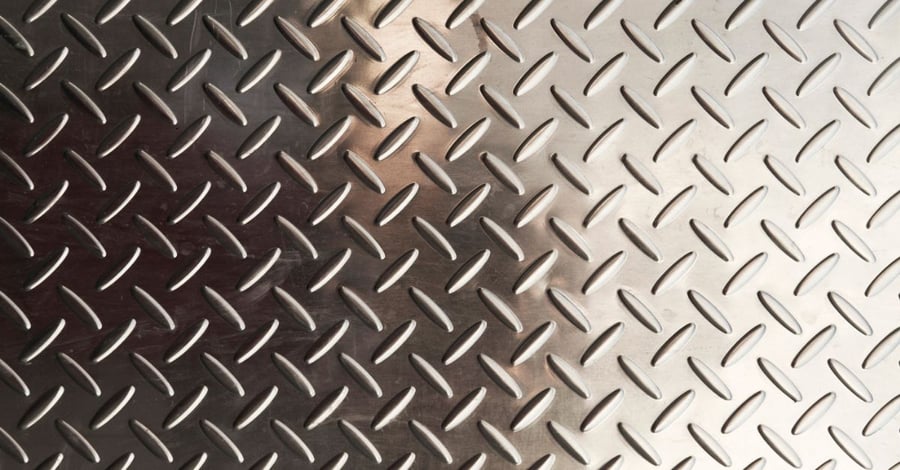
Manufactured with Speed and Precision
The manufacturing capabilities you need and the engineering support you want, all from a single partner.
Submit a DesignKey Points
- Galvanic compatibility refers to the electrochemical relationship between different metals and how they interact when in contact in the presence of an electrolyte.
- The galvanic series ranks metals based on their electrical potential, helping engineers predict which combinations are safe and which will lead to accelerated corrosion.
- Environmental factors like humidity, temperature, and salt exposure significantly impact galvanic corrosion rates.
- Proper material selection, isolation techniques, and protective coatings are essential strategies for preventing galvanic corrosion in engineered systems.
- Understanding galvanic compatibility is critical for aerospace, defense, and medical device applications where reliability and longevity are non-negotiable requirements.
Definition
What is Galvanic Compatibility?
Galvanic compatibility refers to how well different metals can coexist when in contact with each other without causing accelerated corrosion due to their relative positions on the galvanic series. Two metals are considered galvanically compatible when they have similar electrical potentials, minimizing the electrochemical reaction that would otherwise cause the more active metal to corrode rapidly when an electrolyte is present.
The Engineering Challenge of Mixed Metals
In the world of precision engineering, bringing different metals together creates both opportunities and challenges. Galvanic compatibility stands as one of the most fundamental considerations when designing components that must maintain structural integrity in demanding environments.
When two dissimilar metals make contact in the presence of an electrolyte, nature takes its course. Electrons flow from the more active (anodic) metal to the more noble (cathodic) metal, creating a microscopic battery. This natural phenomenon — while fascinating from a scientific perspective — leads to accelerated corrosion that can compromise critical systems in everything from medical implants to aircraft components.
For engineers working on advanced applications, understanding galvanic compatibility isn't just an academic exercise — it's an essential design requirement that directly impacts product reliability, safety margins, and operational lifespans.
Read the Guide: Better Understand EMI Shielding and How to Fit it into Your Design.
Defining Galvanic Compatibility
Galvanic compatibility refers to how well different metals work together without causing accelerated corrosion when in contact in the presence of an electrolyte. Two metals are considered galvanically compatible when they sit close together on the galvanic series, minimizing the potential difference that drives corrosion.
The fundamental principle behind galvanic compatibility stems from basic electrochemistry. When two dissimilar metals connect in an electrolyte (even something as simple as condensation or humidity), they form a galvanic cell — essentially a battery. The metal higher in the galvanic series becomes the anode and sacrificially corrodes at an accelerated rate to protect the more noble metal (cathode).
The greater the potential difference between metals, the faster the corrosion process. This electrochemical reaction transfers electrons from the more active metal to the more noble metal, gradually dissolving the anodic material over time.
Engineers measuring galvanic compatibility focus on three primary factors:
- The potential difference between metals (measured in volts)
- The relative surface area ratio between the metals
- The presence and conductivity of the electrolyte
A thorough understanding of these factors allows for informed material selection that balances performance requirements with corrosion resistance.
The Galvanic Table: Your Compatibility Roadmap
The galvanic series ranks metals and alloys according to their electrical potential in a specific environment, typically seawater. This hierarchical arrangement serves as a practical tool for engineers to evaluate galvanic compatibility between different materials.
Position | Metal/Alloy | Relative Nobility | Corrosion Tendency |
Most Anodic (Active) | Magnesium alloys | Very low | Highest |
Zinc | Low | High | |
Aluminum alloys | Low | High | |
Carbon steel | Moderate | Moderate | |
Cast iron | Moderate | Moderate | |
Lead | Moderate | Moderate | |
Tin | Moderate | Moderate | |
Nickel | Moderate to high | Low to moderate | |
Brass | Moderate to high | Low to moderate | |
Copper | High | Low | |
Bronze | High | Low | |
Stainless steel (passive) | Very high | Very low | |
Titanium | Very high | Very low | |
Most Cathodic (Noble) | Gold | Extremely high | Extremely low |
The practical application of this series is straightforward: metals closer together on the chart demonstrate better galvanic compatibility. For example, aluminum and zinc exhibit good compatibility, while aluminum paired with stainless steel creates a problematic galvanic couple with high corrosion risk.
It's important to remember that the galvanic series represents a continuum rather than discrete categories. The further apart two metals sit on this scale, the greater the potential difference and corrosion risk when they contact each other in the presence of an electrolyte.
Visit our Glossary for more definitions of key manufacturing terms.
Galvanic Compatibility Chart
Understanding galvanic compatibility becomes significantly easier with a visual reference. The following galvanic series chart illustrates which metals pose galvanic compatibility risks when paired together.
This visual representation helps engineers quickly identify potentially problematic metal combinations by showing their potential for galvanic corrosion when in contact with each other in the presence of an electrolyte.
Environmental Factors Affecting Galvanic Compatibility
While the galvanic series provides a baseline for material selection, real-world environments introduce additional variables that significantly impact galvanic compatibility. Understanding these environmental factors helps engineers anticipate and mitigate corrosion risks in specific applications.
Temperature plays a crucial role in galvanic corrosion rates. Higher temperatures generally accelerate electrochemical reactions, with corrosion rates approximately doubling with every 18°F (10°C) increase in temperature. This makes galvanic compatibility even more critical in high-temperature applications like engine components or heat exchangers.
Humidity and moisture exposure create the electrolytic environment necessary for galvanic corrosion to occur. Even in seemingly "dry" environments, morning dew or condensation can provide sufficient moisture to initiate the corrosion process between incompatible metals.
The specific electrolyte present significantly impacts corrosion severity. Saltwater represents one of the most aggressive electrolytes, making galvanic compatibility particularly important in marine, coastal, and road salt-exposed applications. The chloride ions in salt solutions increase electrolyte conductivity and can break down protective oxide layers, accelerating corrosion.
Atmospheric pollutants like sulfur dioxide and nitrogen oxides can form acids when dissolved in moisture, creating more conductive electrolytes that enhance galvanic corrosion. These considerations become especially important in industrial environments or locations with high pollution levels.
Environmental exposure duration and cycling also influence galvanic corrosion severity. Continuous exposure to moisture accelerates corrosion, while wet-dry cycling can concentrate electrolytes during evaporation phases, potentially creating more aggressive corrosion conditions.
Engineers must consider these environmental factors alongside the basic galvanic series when evaluating material compatibility for specific applications. The same metal pair that performs acceptably in a climate-controlled interior environment might fail rapidly when exposed to coastal humidity or industrial pollutants.
Common Galvanic Pairs and Their Compatibility
Understanding common metal combinations and their galvanic compatibility helps engineers make informed material selections. Here's an overview of frequently encountered galvanic pairs and their expected performance in typical environments.
Compatible Pairs (Low Risk)
These combinations typically exhibit good galvanic compatibility with minimal corrosion concerns:
- Stainless steel 300 series with stainless steel 400 series
- Copper with brass or bronze
- Nickel with copper alloys
- Zinc with aluminum alloys
- Gold with silver
Moderate Compatibility Pairs (Some Risk)
These combinations require careful evaluation and potentially some mitigation strategies:
- Stainless steel with nickel alloys
- Tin with copper
- Lead with copper alloys
- Aluminum with zinc
- Titanium with nickel alloys
These pairings demonstrate moderate potential differences that can cause accelerated corrosion under certain conditions, particularly in wet environments or with unfavorable surface area ratios.
Incompatible Pairs (High Risk)
These combinations should generally be avoided or require significant isolation measures:
- Aluminum with copper or copper alloys
- Carbon steel with stainless steel
- Zinc with copper or copper alloys
- Magnesium with practically any other metal
- Aluminum with stainless steel
These pairings show large potential differences on the galvanic series, creating aggressive corrosion cells that rapidly deteriorate the more anodic metal. In the presence of an electrolyte, these combinations can lead to premature component failure.
The real-world performance of these pairs depends heavily on environmental conditions. A theoretically "risky" combination might perform adequately in a dry, controlled environment, while even "compatible" pairs could experience issues in aggressive environments like saltwater exposure.
Engineering judgment must balance galvanic compatibility with other material selection criteria like strength, weight, cost, and thermal properties. When incompatible materials must be used together, appropriate isolation strategies become essential.
-- Article Continues Below --
Learn how Modus is redefining the traditional supplier relationship
Preventing Galvanic Corrosion in Engineered Systems
Engineers have developed numerous strategies to manage galvanic compatibility challenges while meeting performance requirements. These approaches range from material selection to isolation techniques and protective treatments.
Material Selection Strategies
The first line of defense against galvanic corrosion lies in thoughtful material selection:
- Choose metals with similar electrical potentials when possible
- Select corrosion-resistant alloys appropriate for the environment
- Consider non-metallic alternatives for joining dissimilar metals
- Design with the galvanic series in mind, especially for critical components
- Select materials that form stable, protective oxide layers
Proper material selection eliminates the fundamental conditions for galvanic corrosion, offering the most reliable long-term solution.
Isolation Techniques
When dissimilar metals must be used together, isolation prevents the physical or electrical contact necessary for galvanic corrosion:
- Insert non-conductive washers, bushings, or gaskets between different metals
- Use dielectric unions for pipe connections
- Apply non-conductive coatings at interface points
- Design with "bridge materials" that have intermediate galvanic potential
- Employ non-metallic fasteners where appropriate
Effective isolation breaks the electrical circuit required for galvanic corrosion, allowing incompatible metals to coexist in the same assembly.
Surface Treatments and Coatings
Protective coatings provide a physical barrier against the electrolyte environment:
- Apply sacrificial coatings like zinc to protect more noble base metals
- Use conversion coatings to create corrosion-resistant surfaces
- Specify anodizing for aluminum components
- Apply paint systems designed for galvanic protection
- Consider powder coating for comprehensive coverage
These treatments either isolate the metal from the environment or provide sacrificial protection that preserves the structural integrity of critical components.
Galvanic Compatibility Design Considerations
Thoughtful design can minimize galvanic corrosion even when using dissimilar metals:
- Design for drainage and ventilation to prevent electrolyte accumulation: Engineering components with proper drainage channels and ventilation prevents moisture, condensation, and other electrolytes from collecting at metal interfaces, effectively eliminating one of the three requirements for galvanic corrosion to occur.
- Maintain favorable area ratios (large anode to small cathode): Creating designs where the anodic (more active) metal has a larger surface area than the cathodic (more noble) metal distributes the galvanic current across a greater area, significantly reducing the corrosion rate at any single point.
- Specify thicker sections for components expected to experience galvanic attack: Adding extra material thickness to parts that will serve as anodes in unavoidable galvanic couples extends their functional lifespan by providing additional material that can be sacrificed before structural integrity is compromised.
- Create serviceable assemblies where sacrificial components can be replaced: Designing systems where parts expected to experience galvanic corrosion can be easily accessed and replaced during regular maintenance intervals allows for planned component renewal rather than unexpected system failure.
- Design with environmental exposure in mind: Accounting for the specific operating environment (including temperature fluctuations, humidity levels, salt exposure, and chemical presence) during the design phase ensures appropriate material selection and protection strategies tailored to real-world conditions.
These design strategies acknowledge the reality of galvanic relationships while minimizing their impact on system performance and longevity.
While no single approach works universally, combining these strategies creates robust galvanic compatibility management. Many aerospace and medical applications employ multiple layers of protection to ensure reliability in demanding environments.
Industry-Specific Galvanic Compatibility Considerations
Different industries face unique galvanic compatibility challenges based on their operating environments, performance requirements, and regulatory frameworks. Understanding these industry-specific considerations helps engineers develop appropriate solutions.
Aerospace and Defense Applications
Aerospace applications face extreme temperature variations, vibration, and potential exposure to both high-altitude conditions and saltwater environments. Galvanic compatibility requirements in this sector are particularly stringent because:
- Weight considerations often necessitate combinations of lightweight metals like aluminum and titanium with other materials
- Safety-critical systems cannot tolerate premature failure
- Service lifespans extend over decades in challenging environments
- Repair access is often limited or impossible during operation
Common aerospace galvanic compatibility challenges include aluminum-stainless steel interfaces in structural components, titanium-aluminum connections in engine components, and carbon fiber composite interfaces with metallic fasteners.
Aerospace standards like MIL-STD-889 specifically address galvanic compatibility requirements and provide guidance for material selection in defense applications. These standards recognize that galvanic compatibility directly impacts mission readiness and safety.
Medical Device Considerations
Medical devices present unique galvanic compatibility challenges, particularly for implantable devices that must function in the corrosive, warm, saline environment of the human body:
- Biocompatibility requirements limit material options
- Implantable devices must maintain integrity for years or decades
- Corrosion products must not cause adverse patient reactions
- Electrical functionality must remain stable despite potential galvanic effects
- Sterilization processes can affect surface properties related to galvanic compatibility
Titanium dominates implantable device construction due to its excellent biocompatibility and corrosion resistance, but interfaces with other materials like cobalt-chromium alloys, stainless steel, or nitinol must be carefully managed to prevent galvanic issues.
FDA regulations indirectly address galvanic compatibility through reliability and safety requirements, making this a critical consideration in medical device design and validation.
Industrial Equipment Applications
Industrial equipment often operates in challenging environments with exposure to chemicals, temperature extremes, and moisture. Galvanic compatibility considerations include:
- Extended service lifespans often measured in decades
- Exposure to process chemicals and cleaning agents
- Temperature cycling that can accelerate corrosion processes
- Vibration that can damage protective coatings
- Cost constraints that limit material options
Manufacturing equipment particularly benefits from thoughtful galvanic compatibility design to prevent unexpected failures and costly production downtime. The focus typically extends beyond simple corrosion prevention to maintaining precise dimensions and surface finishes critical to operation.
Understanding these industry-specific challenges allows engineers to develop appropriate galvanic compatibility strategies tailored to their particular applications and operating environments.
-- Article Continues Below --
Visit our complete EMI shielding resource center.
Frequently Asked Questions About Galvanic Compatibility
Engineers frequently ask these questions when addressing galvanic compatibility in their designs.
What is the primary mechanism behind galvanic corrosion?
Galvanic corrosion occurs through an electrochemical process where electrons flow from the more active (anodic) metal to the more noble (cathodic) metal through an electrical connection, while metal ions move through an electrolyte. This creates a complete circuit allowing corrosion to proceed at an accelerated rate.
The process requires three elements: two electrochemically dissimilar metals, an electrical connection between them, and an electrolyte bridging both metals. Remove any of these three elements, and galvanic corrosion stops.
How do I determine which metal will corrode in a galvanic couple?
The metal higher on the galvanic series (more anodic/active) will corrode preferentially when connected to a more noble metal. For example, in a zinc-copper connection, zinc will corrode sacrificially to protect the copper.
This predictable behavior allows engineers to implement sacrificial protection systems where a more active metal intentionally corrodes to preserve a more valuable or structural component.
Does the surface area ratio between metals matter for galvanic compatibility?
Yes, surface area ratio significantly impacts galvanic corrosion rates. A small anode connected to a large cathode creates a particularly dangerous situation, as the entire galvanic current concentrates on the small anodic area, accelerating corrosion dramatically.
The reverse situation — large anode connected to small cathode — distributes the galvanic current across a larger area, reducing the corrosion rate to more manageable levels. This principle informs design practices like using large sacrificial anodes to protect smaller cathodic structures.
How does distance between dissimilar metals affect galvanic compatibility?
Increasing the distance between dissimilar metals reduces galvanic corrosion by introducing electrical resistance into the system. The effect becomes particularly noticeable in electrolytes with lower conductivity, where the resistance of the electrolyte path significantly limits galvanic current.
This principle explains why galvanic corrosion typically concentrates near the junction between dissimilar metals rather than affecting the entire structure uniformly.
Can galvanic compatibility issues develop in supposedly "dry" environments?
Yes, even seemingly dry environments can provide sufficient moisture for galvanic corrosion through condensation, humidity, or occasional exposure to water. As little as 60% relative humidity can create an invisible moisture film capable of supporting galvanic corrosion.
This explains why galvanic compatibility remains important even for indoor applications, particularly in humid climates or applications with temperature fluctuations that might cause condensation.
Understanding these fundamental aspects of galvanic compatibility helps engineers develop more effective corrosion prevention strategies and make better material selection decisions across diverse applications.
The Engineering Advantage of Proper Material Selection
Addressing galvanic compatibility early in the design process delivers significant advantages throughout the product lifecycle. Engineers who successfully navigate these electrochemical relationships create more reliable, longer-lasting systems that perform consistently in demanding environments.
For aerospace and defense applications, proper galvanic compatibility management translates directly to improved operational readiness and reduced maintenance requirements. In medical devices, it ensures long-term functionality and patient safety. Across all industries, it prevents the premature failure and unexpected downtime that can damage reputations and bottom lines.
At Modus Advanced, our engineering team understands the critical importance of galvanic compatibility in precision-manufactured components. Our vertical integration capabilities allow us to control the entire manufacturing process, ensuring that material selection, surface treatment, and assembly techniques work together to prevent galvanic corrosion issues.
From initial design reviews to material selection guidance, we partner with your team to address galvanic compatibility challenges before they become field problems. Our AS9100 and ISO 9001 certified manufacturing processes deliver the consistency and quality that mission-critical applications demand.
Because when engineering life-changing innovations, one day matters — and so does each material choice that affects long-term reliability. Contact our engineering team today to discuss how we can help optimize your next design for galvanic compatibility and long-term performance.