10 Questions to Ask Yourself When Choosing a Material for Your Custom Gasket
January 18, 2021
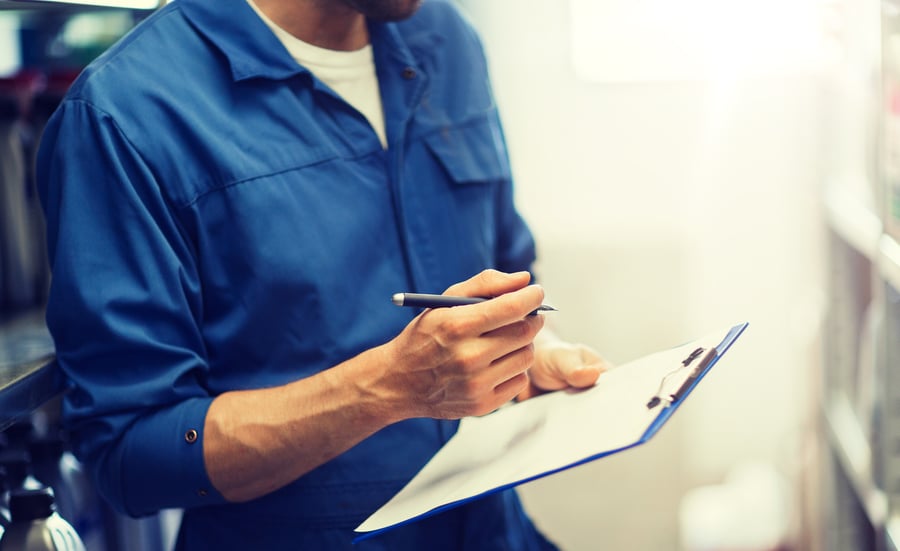
Manufactured with Speed and Precision
The manufacturing capabilities you need and the engineering support you want, all from a single partner.
Submit a DesignThe process of choosing a material for your custom gasket is intricately woven into your design process. Material informs design as much as design informs material, so deciding on both of these items together will help you land on just the right material for your needs.
-- Article Continues Below --
Avoid frequent design mistakes in our free guide.
We’ve found, in our years of helping customers choose the perfect material for their custom gasket, that there are 10 very important questions you should be asking yourself when choosing a material that will help you get it right the first time:
- Will the gasket be used in an indoor or outdoor application?
- What temperature range must your gasket operate in?
- What does your industry require?
- How hard or soft does your gasket material need to be?
- Do you need a three-dimensional or flat gasket?
- How will your custom gasket be assembled?
- What will your housing be made out of?
- What chemicals will the gasket be exposed to?
- How small is the gasket?
- Is outgassing a concern?
Please keep in mind this article is meant to provide general guidance, and there are many materials with different properties and specifications to choose from within each general material category. Narrowing down to your final material is something best done with the help of an expert. This guide is designed to help you start the process of material selection, before diving into the nitty gritty details.
Will the gasket be used in an indoor or outdoor application?
Usually, the first question to ask is where your custom gasket will be used. Indoor applications will have an entirely different starting set of materials to consider than outdoor applications.
If your gasket will be used outdoors, you’ll likely need a larger supported temperature range, a material that can withstand the elements, and has resistance to ozone or sunlight. A good general rule of thumb is the more a gasket can withstand, the higher the material cost.
Indoor applications can generally get away with lower cost materials than outdoor applications.
Some materials that are a good fit for outdoor applications include:
- Most solid gasket materials
- Silicone or EPDM sponge materials
- Some silicone and polyurethane foams
- Silicone Form-in-Place (FIP) materials
Another consideration that falls into this category is if the gasket will be enclosed or exposed when used in an outdoor environment. If it will be enclosed, and there will be protection from chemicals and ozone, you will obviously have a larger variety of materials that may fit your needs.
What temperature range must your gasket operate in?
This question tends to work hand in hand with the previous one. Generally speaking, outdoor applications will require a higher range of temperatures to which the gasket must be resistant.
Start by narrowing down the highest and lowest temperatures your gasket will be subject to and layout the full range. You’ll want to find a material that can operate across the entire range, rather than just ideal conditions. As you might expect, the larger the range of temperatures supported by a material, the higher the cost.
Selecting the right material in this case is a balancing act between making sure your gasket can operate across exactly the range it needs while reducing the material cost.
Some materials that are resistant to extreme temperatures include:
- Most solid gasket materials, Silicone and Fluoroeleastomer(FKM)
- Some silicone sponge materials
- Silicone FIP materials
What does your industry require?
Depending upon your industry, there may be very specific material requirements you need to be aware of. Some examples include:
- Materials used in military applications will have to meet MIL SPEC requirements
- Materials used in medical applications may require the use of FDA, CFR 177.2600, USP Class VI compliant materials that are either non-toxic or have skin compatibility
- Food handling or agricultural applications may require FDA compatible materials should food or liquid come into contact with your custom gasket
- Rail and mass transit applications often require specific UL or flame ratings
Make sure you’ve considered all of the requirements that apply to your application and be sure you select a material that meets those requirements before getting too deep into the design process.
Read Now: Guidance from start to finish on your custom gasket production.
How hard or soft does your gasket material need to be?
Balancing the hardness of your material with the lifespan will be the biggest challenge in this instance. In general, the softer a material, the shorter the expected lifespan will be.
Softer gaskets are important in instances where there are larger gaps, uneven gaps, or you are concerned with damaging the materials the gasket is touching. Harder gaskets are best for instances where compression forces will be high, and a longer lifespan is important.
Durometer is the measurement of hardness in a material and provides a quantitative indication of how resistant said material is to permanent deformation or indentation. Make sure you’ve considered the durometer range needed for your design and find a material that meets those specifications.
Compression force deflection is another measurement that will be important in material hardness. It is defined as the force required to reduce material thickness by 25%. Softer materials require on the order of 2 psi to reduce thickness by 25% whereas harder materials require upwards of 17 psi.
Some materials that are good for softer gaskets include:
Some materials that are good for harder gaskets include:
Do you need a three-dimensional or flat gasket?
If your gasket needs to be three-dimensional you’ll be looking at custom molded silicone or rubber to meet your needs.
Flat gaskets on the other hand have a wide variety of materials you can choose from depending upon your answers to some of the other questions in this list.
How will your custom gasket be assembled?
An important consideration that is often overlooked in the design process is how the assembly process will need to work. It is very easy to design in a vacuum and ultimately lose sight of factors that may make it easier or harder to add your gasket to your assembly process in the long term.
Some of the more obvious considerations that usually are considered in design are the requirement of adhesive backing and the compression forces being applied to the gasket. Both of these will limit your available choices of gasket materials depending upon your needs.
Some of the considerations that are often overlooked include:
- How long will the assembly process take and/or cost? Often smaller, thinner gaskets are hard to work within the assembly and increase production time. In this case, FIP materials may be a better choice to improve production time and reduce labor costs.
- How hard do you want the assembly to be? In general, the softer the gasket material, the easier assembly will be in the end, as lower compression force will be required to get it into place.
- Will everything be assembled right away? Sometimes assembly processes are broken into smaller chunks, but choosing to use a material like thermal paste adds the requirement that everything must be immediately assembled before the paste dries.
Just make sure you’ve considered your assembly process before ultimately deciding upon the best fit material to ensure you don’t have to come back and redesign later.
What will your housing be made out of?
While you are obviously considering the material of your gasket itself, it is also important to keep in mind the materials for your housing.
Knowing how hard the housing materials are will help you decide on a gasket material that will work well in the environment you are placing it. For instance, in cases where a plastic housing is used, you have to be careful to select a gasket material (e.g. a sponge material) that won’t cause cracking at your compression stops.
What chemicals will the gasket be exposed to?
You will want to ensure you are aware of the range of chemicals your gasket may come into contact with. This will probably be one of the most important considerations that will significantly narrow your choices should you expect any harsh chemicals to be present.
Some custom gasket materials that are resistant to a variety of chemicals include:
How small is the gasket?
The size of your gasket will help you determine if it is the best fit for form-in-place (FIP) dispensing or not. Narrow, small or flimsy gaskets are often much easier to dispense via FIP than trying to cut and assemble them by hand.
Is outgassing a concern?
This consideration is typically only a real problem in custom gaskets used in hard drives, where outgassing may cause contamination of the drive. In this case, you’ll need to use a material other than silicone to get rid of outgassing.
The Bottom Line
Ultimately, selecting the right gasket material is as much of a science as it is an art. It is about knowing the right questions to ask to help you balance cost, lifespan and the needs of your design. Want help from an expert? We’ve got plenty that are ready to help consult you on choosing the best materials for your needs.