Gasket Material Guide: 27 Materials for Custom Gaskets and Their Purposes
January 13, 2021
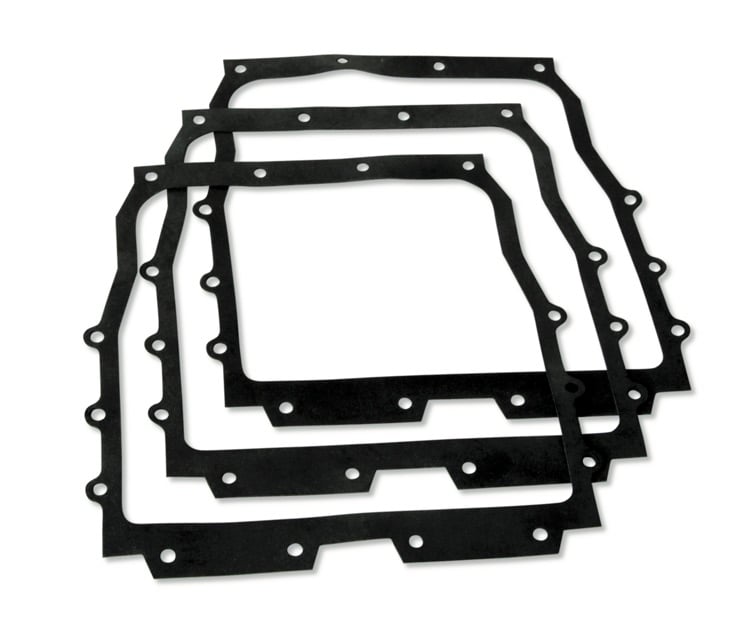
Manufactured with Speed and Precision
The manufacturing capabilities you need and the engineering support you want, all from a single partner.
Submit a DesignKey Points
- Selecting the right material for your custom gasket is critical to performance, with thousands of options available across several major categories: solid materials, sponge materials, foam materials, form-in-place materials, EMI shielding, and thermal interface materials.
- Solid materials offer superior durability and lifespan (up to 2x longer than sponge alternatives) but require stronger compression forces, materials like silicone excel in extreme temperatures while fluoroelastomers provide the highest performance across multiple properties.
- Sponge and foam materials are ideal for applications requiring lower compression forces, such as plastic housings or where warping is a concern, with silicone sponge offering the longest lifespan among sponge options.
- Form-in-place (FIP) gaskets solve manufacturing challenges for very small, intricate designs while reducing assembly costs, with material options ranging from standard silicone to specialized EMI shielding compounds.
- The right thermal interface material depends on your heat dissipation requirements, with options spanning from gap fillers to thermal tapes and pastes, each optimized for specific application conditions.
There are thousands of materials to choose from when building your custom gasket, each with different properties and tolerances to choose from.
Some of the most common categories of materials for making custom gaskets, and general guidelines for when they may be a fit are detailed below.
Please keep in mind that this article is meant to provide general guidance, and there are many materials with different properties and specifications to choose from within each category. Narrowing down to your final material is something best done with the help of an expert. This guide is designed to help you start the process of material selection, before diving into the nitty gritty details.
You can also use this table of contents to jump straight to the material you want to learn more about:
Table of Contents
Gasket Material Categories
Avoid frequent design mistakes in our free guide.
Solid Materials
Solids are often chosen based on a simple preference between solid and sponge materials. In general you can do most of the same things with solid and sponge materials but solid materials will give your gasket a longer life and more durability. Solids often extend the lifespan of the unit up to 2 times longer than a sponge material.
Additionally the compression force of a solid will always exceed that of a sponge. If your application has, or can handle strong compression forces, a solid material will be your best bet.
Solid materials can be formed into gaskets using die cutting, waterjet cutting, and CNC or digital cutting. In addition, solids materials can be molded into more three dimensional (rather than flat) gaskets if the situation calls for it.
Related: Is Waterjet Cutting the Right Fit for Your Custom Gasket?
Find out if waterjet cutting is the appropriate converting process for your gasket.
Learn MoreRelated: Is Die Cutting the Right Fit for Your Custom Gasket?
Find out if die cutting is the appropriate converting process for your gasket.
Learn MoreRelated: Is CNC or Digital Cutting the Right Fit for Your Custom Gasket?
Find out if CNC or digital cutting is the appropriate converting process for your gasket.
Learn MoreSilicone
Solid silicone is designed to be used in outdoor applications where physical properties are not critical but extreme temperature resistance is still needed. This may include situations where degradation may occur due to exposure to sunlight or ozone.
Fluorosilicone
Fluorosilicone sheeting is designed to be used in similar conditions to silicone, with additional chemical resistance. Both extreme temperature resistance, and its resistance to chemicals such as oils and fuels makes it an ideal material for fuel delivery applications in the aerospace, automotive and defense industries. Because of the additional chemical resistance you will find that fluorosilicone costs slightly more than silicone.
Neoprene
Neoprene is a more cost effective option than either silicone or fluorosilicone. It is recommended for applications that require resistance to liquids such as water, oil, and other solvents. It is also resilient with a high degree of elasticity. With greater elongation and tear strength than silicones formulated for general purposes, this material is resistant to abrasion and fatigue.
Nitrile
Nitrile is a material specifically developed for commercial or industrial applications where environmental extremes and wear is an important factor. Nitrile exhibits resistance to chemicals like fuels and oils. It is a tough, long lasting material.
There are FDA approved versions of nitrile materials available, making it a common choice for agricultural or food handling applications.
EPDM
Peroxide Cured EPDM (Ethylene-Propylene-Diene-Methylene) is used in a wide range of applications where a general-purpose rubber with excellent water, weather, UV and ozone resistance is required. The curing process of Peroxide Cured EPDM provides heat stability making it resistant to high temperatures and steam. This material may be less expensive than silicone in some applications. EPDM is not recommended for applications with exposure to oil.
Fluoroelastomer
The “higher end” choice for solid materials, Flouroelastomer is known for providing the best of everything. It provides resistance to extreme temperature ranges, shows strong resistance to chemicals and does well in most applications. As such, it is also the most expensive of all the solid materials. A common application where all of these properties are needed is in aerospace use cases.
Read Now: Guidance from start to finish on your custom gasket production.
Butyl
Butyl is a synthetic rubber that resists moisture and the passage of gasses well. In addition, it has strong resistance to oil and chemicals, making it a common choice for automotive and even medical applications.
Sponge Materials
Sponge materials are commonly chosen for applications when low compression forces are required. This may be the case if there is concern for warping or bowing of the housing during assembly, if plastic housing is required, or if there is concern for cracking at compression stops anywhere on the housing. In addition, sponge materials can make assembly much easier because there are far less compression forces needed.
In addition, sponge materials are sometimes selected over solids due to UL flame ratings. It is much easier to find silicone sponge materials with the UL94V-0 flame rating than it is for solid silicone.
Silicone Sponge
Soft Density Closed Cell Silicone Sponge is an excellent material for gasketing and padding applications that require a soft, compressible material. It is resistant to extreme temperatures, making it ideal for outdoor applications, and offers a good compression set. Also, its non-interconnected closed cells prevent water absorption.
Silicone sponge has the longest life out of all the sponge material options. Typically, Silicone Sponge is available in Soft, Medium, Firm and Extra-Firm Densities.
Neoprene Blend
A neoprene blend is an excellent choice for gasketing and sealing applications that require a soft and compliant material. It is considered a lower cost alternative to solid rubber and other sponge materials. It is commonly used in shock absorption applications, as a thermal barrier, for weather stripping, and as a common basic sealing solution for industrial applications.
Also, its non interconnected closed cells make it extremely impermeable to water absorption. This sponge rubber is typically available in five hardnesses: Soft, Medium, Medium-Firm, Firm and Extra-Firm.
EPDM Sponge
EPDM Sponge material has most of the same qualities as the neoprene blend above, but exhibits greater resistance to ozone, making it useful in applications where a sponge material is best-fit but ozone exposure is a concern. As such, it is slightly more expensive than neoprene blend.
Foam Materials
Similar to sponge materials, foam materials are used in applications where low compression force is required. In fact, they offer even lower compression forces than sponge materials. Additionally, foams are typically less expensive than either a solid or sponge.
In general, foams are used to provide a simple seal against primarily air and dust, but do not provide a true environmental seal. It is best fit if your application just needs a basic seal between two materials, and it is not fit for critical outdoor applications.
Silicone Foams
Cellular silicone foam features resistance to extreme temperatures and resilience required in many types of sealing, cushioning, insulation and vibration isolation applications. Typically silicone foam materials are available in six different varieties, ranging from ultra soft to extra firm.
Polyurethane Foams
Polyurethane foams offer a broad range of design solutions for gasketing, sealing, and energy absorption. They provide a balance of a lower cost option than silicone foams and have a very low compression set. Typically polyurethane foams can be formulated in a wide range of firmnesses and a variety of densities within each formulation.
Filter Foams
Filter foams are designed almost exclusively to filter out dust. They allow breathing, or the in and out flow of air but keep dust out. As such they are commonly used in electronic applications where dust can cause problems.
Polyolefin
Polyolefin is meant to be a low cost, or inexpensive material for making basic gaskets. For the most part, this material is selected when a space simply needs to be filled to ensure the two sides of a part aren’t touching each other.
Form in Place Materials
Form in place (FIP) materials are best fit when you have a very small gasket that would be difficult to die cut and then assemble in your production facility. Very small and thin gaskets are flimsy and difficult to manage, increasing the effort and time that must go into assembly. This is more and more common due to the smaller form factors and space constraints in today’s electronic assemblies.
As such, FIP gaskets are usually selected in an effort to reduce the cost of assembly in these instances. Because the gasket is dispensed directly on the unit, then cured, before being sent back to your production facility, it saves a step (and money) on the assembly process.
In addition, when using custom gaskets for EMI applications, choosing FIP as the method for production can limit waste, thus reducing cost on more expensive materials. Because of their typical size, FIP materials are commonly used to create an effective seal for electronic devices.
Visit our Complete Form-in-Place Gasket Resource Center
Silicone
Typically, a one-component silicone sealant and adhesive that cures when exposed to ambient humidity at room temperature. This material has excellent sealing properties with superior weather, ozone and compression set, as well as electrical insulation properties typical of silicone.
The paste-like consistency of this compound allows for application on vertical and overhead surfaces in addition to horizontal surfaces, at certain viscosities. The uncured body of this material is also sufficient to adhere small objects during the curing process. Silicone used for FIP, exhibits both low temperature flexibility and high temperature performance.
Because it is readily available, and has such a wide range of properties, silicone is the most commonly used material for FIP gasket production.
UV Materials
UV materials are typically used when production or lead time is an important factor. These materials don’t require the same amount of curing time after dispensing that silicone does, and as such can be turned around much faster. UV materials are typically selected in instances where high volume and production throughput are the most important considerations.
EMI FIP Materials
Probably the most common type of FIP Gaskets utilized are those with EMI materials. These materials meet all the requirements for EMI applications, but are useful when a small and precise gasket is required. EMI materials have the ability to shield between the two sides of the gasket and are very commonly seen in applications across a wide spectrum including test equipment, communications, satellites, and aerospace.
Deep Dive: 6 Tips for Designing a Form-in-Place EMI Gasket
Discover six proven engineering tips for designing form-in-place EMI gaskets that enhance electromagnetic shielding performance while reducing manufacturing complexity and production time.
Learn MoreRelated: The Benefits of Vertical Integration
Find out how vertical integration can improve part quality and reduce lead times.
Learn MoreEMI Shielding
EMI materials are used if shielding is required between two areas of a product or part.
Silicone Extrusions
Designers no longer need to choose between an environmental seal or EMI shielding gasket. Silicone extrusions merge both types of gaskets into a single product. This category of material features a thin electrically conductive shield co-extruded on a high performance silicone rubber base.
Silicone extrusions are typically selected when you have a groove you want to put a gasket into. In most cases you’ll be choosing between an extrusion or an FIP gasket, and your decision will be based on the size of the groove. If the groove is too small for an extrusion, FIP dispensing is likely the only option. In addition, extrusion provides a lower compression force, as it is a softer material than that used in FIP dispensing.
Visit Our Complete EMI Gasketing Resource Center
Silicone
Typically, silicone products made for EMI shielding are made conductive by putting a conductive filler in the material, often silver, aluminum, copper, or nickel. This type of material is highly flexible and can be made to fit a wide variety of sizes and designs. It usually doesn’t stand up to very harsh environmental conditions — like exposure to sunlight, caustic chemicals, fuels or oils — which can leave shielding and sealing capabilities impaired. As such, it is typically used primarily on print circuit boards (PCB) or as connector gaskets on ports in electronics.
Fluorosilicone
Conductive fluorosilicone materials use a fluorinated silicone elastomer base instead, to prevent degrading with contact to the above-mentioned chemicals or environmental factors. Fluorosilicone products are also made conductive by putting a conductive filler in the material, often silver, aluminum, copper, or nickel. Gaskets made with fluorosilicone have a strong resistance to the hydrocarbons found in many of the harsher environmental conditions.
Like silicone above, this material is commonly used in PCB applications, and is selected when a more chemically resistant material is required. If you are concerned that the gasket material will come into contact with acetones or detergents that may erode the material, fluorosilicone is the right fit. As such, it is also typically more expensive than silicone.
Nickel Taffeta Fabric / Foam
This material is best fit in areas where very low compression forces are required. It is most commonly used for servers and in cabinets where electronics are slotted in layers on top of each other. It is generally less expensive than other EMI materials.
Microwave Absorbing Materials
Dense rubber and foam based absorbers that are resistant to UV, ozone, extreme temperatures and flame. Typically these materials are thin, magnetically loaded sheet stock, having high loss at microwave frequencies, while maintaining the desirable characteristics of elastomeric binders. These materials are designed to help lower Q Factor in cavities and attenuate cavity oscillations.
These materials are technically not EMI materials themselves, but are often used in EMI applications. Instead, their job is to absorb frequencies emitted by electronic components, rather than “bouncing” them back like EMI materials.
DEEP DIVE: EMI SHIELDING MATERIAL GUIDE
Dig deeper into our complete guide on EMI shielding gasket materials.
Learn MoreRelated: 7 EMI Gasketing Design Considerations
We want to make the design process as easy as possible for you. That’s why the expert engineering team at Modus Advanced wrote this guide on EMI gasketing design considerations.
Learn MoreThermal Interface Materials
Thermal interface materials are used to dissipate heat in a part. The type of material you need will be based on the amount of power being output over a specific timeframe. From there you can select the right conductivity of the material to dissipate the required heat. The more heat you need to dissipate, the more expensive the material, so you’ll be looking to find the material that dissipates just the amount you need, and no more, to avoid excess cost.
Gap Fillers Silicone
This group of materials is typically used for custom gasket production for chips or PCB applications. You’ll want to use it where pieces of the housing mate and you have a gap that needs to be filled. Silicone is generally selected when there is a large gap here. The idea is that the gasket will transfer the heat to your aluminum metal housing which will then dissipate the heat.
Gap Fillers Acrylic
This class of materials offers the same benefits as Silicone gap fillers above, but has added properties that prevent outgassing. These acrylic pads have no siloxane VOC or oil bleeding, which are associated with silicone products and can often cause device failure. Silicone outgassing can cause contamination which may be a problem, particularly for hard drives in electronic applications. Acrylic Gap fillers would be best fit in these cases, as they don’t have any issues with outgassing.
Sil-Pad Materials
Sil-Pad materials (named for silicone pads) are used in applications where you’d choose a silicone gap filler but the gap is very thin. The pads offer the ability to fit into much smaller gaps, but offer the same material benefits.
Thermal Tape
Thermal tapes are best fit when you need to create a structural bond with your custom gasket. If you have two sides of a part that need to be stuck together and you want to dissipate heat, thermal tape is the way to go. These materials are commonly used to bond a heatsink to circuit boards and in electronic commodity production.
Thermal Paste
Unlike pre-formed gap filling materials, Thermal Pastes or Gels offer infinite thickness options and eliminate the need for specific pad thicknesses or die-cut shapes for individual applications.
Thermal pastes can be used in the place of gap fillers when very low compression forces are required. They will create virtually zero stress on components during the assembly process. There is definitely a give and take with this class of materials as they are very messy. Your application must be able to tolerate this, and you have to be ready to immediately assemble the rest of the part before the paste dries. This material is typically used as a cost-effective option in high volume applications where precision isn’t overly important.
The Bottom Line
Easily the most difficult part of designing a custom gasket is selecting the material that will meet all of your design requirements, but it is far from the only design consideration. Make sure you review the 8 key factors you should consider when designing your custom gasket to get it right the first time.