RF Gasket Maintenance and Replacement in Long-Term Defense Contracts
April 24, 2025
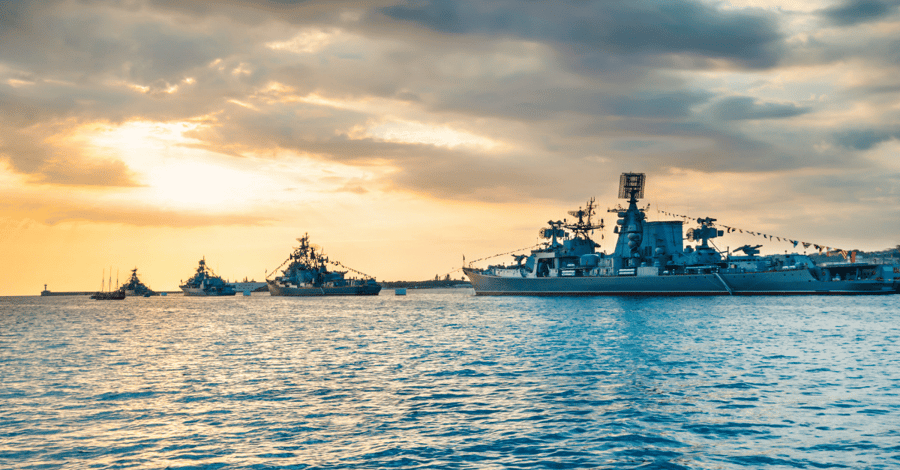
Manufactured with Speed and Precision
The manufacturing capabilities you need and the engineering support you want, all from a single partner.
Submit a DesignKey Points
- Military gasket maintenance is critical for ensuring continued performance of defense equipment over extended contract periods
- Environmental factors can accelerate RF gasket material degradation, requiring proactive inspection protocols
- Replacement schedules should account for both standard lifecycle expectations and observed performance degradation
- Material selection for replacement gaskets must consider compatibility with existing housing materials and environment-specific requirements
- Proper documentation of maintenance and replacement is essential for contract compliance and quality assurance
RF gaskets play a critical role in defense systems, providing electromagnetic shielding that protects sensitive components from interference. For long-term defense contracts, the maintenance and timely replacement of these specialized military specification gaskets directly impact operational readiness and system reliability.
When defense systems operate in harsh environments for extended periods, proper gasket maintenance becomes essential. A single point of gasket failure can compromise an entire system's electromagnetic integrity, potentially rendering mission-critical equipment inoperable at the worst possible moment.
Environmental Factors Affecting Military Gasket Lifecycle
Environmental conditions significantly impact the performance and longevity of RF gaskets in defense applications. Understanding these factors helps in developing appropriate maintenance and replacement protocols.
Temperature variations stress gasket materials through repeated expansion and contraction. Most military gasket types have specified operating temperature ranges, typically between -65°F and 400°F for silicone-based options. Exceeding these ranges accelerates degradation and reduces effective lifespan.
Humidity and saltwater exposure present particular challenges for naval and coastal defense installations. The combination of salt and moisture creates highly corrosive conditions that can compromise gasket integrity and conductive properties.
Vibration from equipment operation or transport can gradually deform gaskets, creating gaps in the shielding barrier. This is especially relevant for deployable systems that experience frequent relocation and varying operational conditions.
The table below summarizes common environmental factors and their effects on military gasket performance:
Environmental Factor | Potential Effects | Vulnerable Gasket Types |
High Temperature (>300°F) | Material hardening, reduced compression recovery | Silicone elastomers with silver-aluminum fillers |
Cold Climate (<-40°F) | Brittleness, cracking when compressed | Certain fluorosilicone formulations |
Salt Fog/Marine | Galvanic corrosion of conductive elements | Silver-copper filled materials |
UV Exposure | Surface degradation, reduced elasticity | Most silicone-based gaskets without UV inhibitors |
Vibration | Compression set, material fatigue | Form-in-place (FIP) gaskets with improper adhesion |
Chemical Exposure | Material breakdown, loss of conductivity | Varies by specific chemical exposure |
Understanding these interactions allows engineers to develop proactive maintenance schedules rather than waiting for system failure.
Inspection Protocols for RF Gaskets
Regular inspection of RF gaskets in defense equipment is essential for maintaining electromagnetic shielding integrity. Implementing structured protocols ensures consistent evaluation across systems and operators.
A comprehensive military gasket inspection should include the following elements:
- Visual examination for physical damage (cuts, tears, compression set)
- Conductivity testing at multiple points along gasket paths
- Assessment of compression characteristics and recovery
- Verification of proper adhesion to mounting surfaces
- Evaluation of environmental contamination (salt, dust, chemicals)
- Documentation of findings with dated images for historical reference
Frequency of inspection should be determined by operational environment and criticality. For example, systems deployed in marine environments typically require quarterly inspections, while those in controlled indoor settings might be examined semi-annually.
Specialized tools improve inspection accuracy beyond visual assessment. Shielding effectiveness testers can identify degradation before it's visually apparent, and durometer readings help quantify hardening of elastomeric materials.
Proper documentation is as important as the inspection itself. Each military gasket inspection should generate records that become part of the equipment's maintenance history, supporting trend analysis and predictive maintenance planning.
Replacement Decision Factors
Knowing when to replace RF gaskets in defense systems requires balancing multiple factors. This decision process should be systematic rather than reactive.
The decision to replace a military gasket should consider:
- Age of installation relative to manufacturer's specified lifetime
- Measured decline in shielding effectiveness
- Observable physical degradation
- Changes in mission parameters or environmental conditions
- Availability of improved gasket technologies
- Scheduled maintenance windows to minimize operational downtime
For critical systems, replacement decisions shouldn't rely solely on visual inspection. Quantitative measurements of compression set, conductivity, and shielding effectiveness provide objective data for informed decision-making.
The table below offers general guidelines for replacement intervals based on environment and gasket type:
Environment | Conductive Elastomer Gaskets | Form-in-Place Gaskets | Metallic Fingerstock |
Controlled Indoor | 5-7 years | 4-6 years | 7-10 years |
Field Deployment | 3-5 years | 2-4 years | 5-7 years |
Maritime/High Humidity | 2-3 years | 1-2 years | 3-5 years |
Extreme Temperature | 2-3 years | 1-2 years | 4-5 years |
These timeframes should be adjusted based on specific military gasket materials, system criticality, and observed performance metrics. Preventive replacement often proves more cost-effective than addressing failures after they occur.
Material Selection for Replacement Gaskets
Selecting the appropriate replacement material is crucial for maintaining or enhancing system performance. Military gasket replacement provides an opportunity to upgrade materials based on observed performance in specific environments.
When selecting replacement gaskets, consider these factors:
- Compatibility with existing housing materials to prevent galvanic corrosion
- Shielding performance across the specific frequency range of concern
- Temperature range expected during operation and storage
- Chemical resistance relevant to the operational environment
- Compression force limitations of the enclosure design
- Long-term availability for future replacement cycles
Advancements in gasket technology may allow for upgrades during replacement. Newer military gasket formulations often offer improved durability, wider temperature ranges, and enhanced shielding effectiveness compared to older materials.
Material selection should be documented as part of the maintenance record, especially when changing from the original specification. This documentation supports future maintenance decisions and helps identify performance trends.
Learn everything you need to know about RF Shielding here.
Installation Best Practices
Proper installation of replacement RF gaskets is as important as selecting the right material. Even the highest quality military gasket will fail prematurely if installed incorrectly.
Follow these installation best practices:
- Thoroughly clean mounting surfaces to remove all traces of old adhesive and contamination
- Verify dimensional compatibility between replacement gaskets and mounting surfaces
- Apply appropriate primers when recommended by gasket manufacturers
- Maintain consistent compression across the entire gasket path
- Observe cure times completely before returning equipment to service
- Verify shielding effectiveness after installation and before system deployment
For form-in-place gaskets, proper dispensing equipment calibration is essential. Variations in bead height or width can significantly impact both compression characteristics and shielding performance.
Installation technicians should be specifically trained in RF gasket replacement techniques. The specialized nature of military gasket installation warrants dedicated training rather than treating it as a general maintenance task.
Documentation and Compliance
Thorough documentation of gasket maintenance and replacement is essential for defense contract compliance. Military standards often require detailed maintenance records for all EMI/RFI shielding components.
Effective documentation should include:
- Original installation specifications and materials
- Scheduled and unscheduled inspection results
- Replacement dates and materials used
- Shielding effectiveness measurements before and after replacement
- Personnel involved in maintenance actions
- Environmental conditions during inspection and replacement
- Photographic evidence of condition and installation quality
This documentation serves multiple purposes beyond compliance. It establishes performance baselines, enables trend analysis, and supports continuous improvement in maintenance practices.
Strategic Gasket Management for Mission-Critical Systems
Effective military gasket maintenance and replacement strategies are essential for ensuring the continued performance of defense systems under long-term contracts. Engineers can maximize operational reliability while minimizing downtime through the implementation of structured inspection protocols, data-driven replacement decisions, and appropriate material selection. These proactive measures directly contribute to mission readiness and extended system lifecycle in demanding defense applications.
At Modus Advanced, we understand that one day matters when it comes to defense systems reliability. Our engineering team works with defense contractors to develop comprehensive gasket maintenance strategies that extend system life and ensure mission readiness. With AS9100 certification, ITAR compliance, and a team where over 10% of our staff are engineers, we're positioned to support your most critical military gasket requirements.