RF Shield Design Guide
April 14, 2022
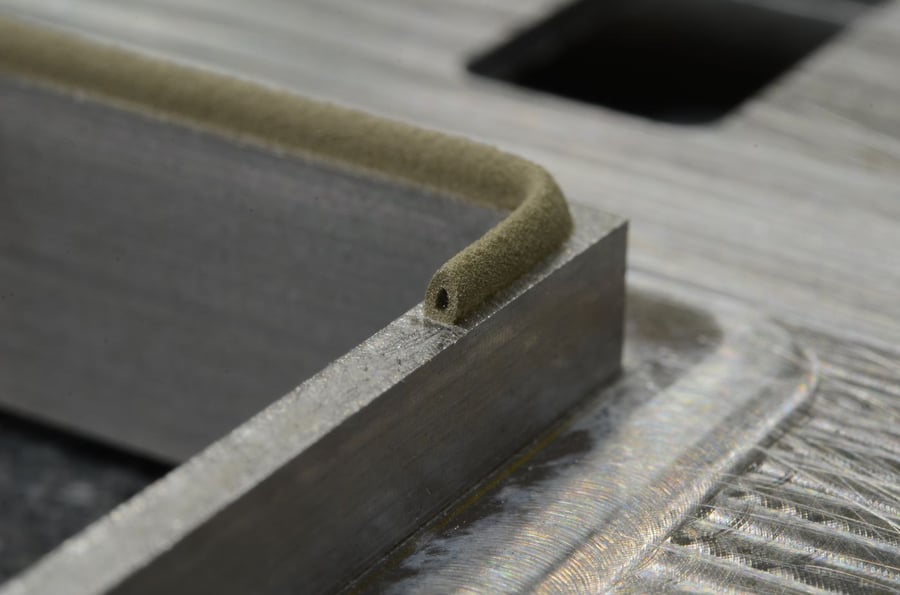
Manufactured with Speed and Precision
The manufacturing capabilities you need and the engineering support you want, all from a single partner.
Submit a DesignKey Points
- The ability to design an effective RF shield is important in a wide variety of industries and applications.
- Avoiding several common missteps can make the design and manufacturing process go much more smoothly.
- Seeking feedback from experienced manufacturing engineers can be an enormous help.
Radio frequency (RF) interference isn’t going away any time soon. It’s only getting more common, which means that designing effective RF shields is only going to become more important in more applications over time.
You are probably already there. If you’re reading this, you’re looking for an RF shield design guide. And the team at Modus Advanced is uniquely qualified to help you. That’s because we have partnered with countless designers and engineers in diverse and numerous industries to manufacture RF shields in every shape and size. We routinely offer feedback on RF shield designs that improves the manufacturing process and functionality of the end device.
As we have obtained all of that experience, we have learned a few key RF shield design tips, which we share with you below. Read on to learn more.
Designing an effective RF shield isn’t easy, and designing one that’s actually easy and cost-effective to manufacture is even harder. We can help. With our SigShield process and Design for Manufacturability (DFM) review, we’ll help you perfect your design and manufacture the perfect part. Contact us.
Read Everything You Need To Know About RF Shielding
Choose the Right RF Shield Manufacturing Method
The first and most important tip in this RF shield design guide is foundational. It’s about the manufacturing method you choose. In our experience, computer numerical control (CNC) milling works for most RF shields. We use a vertical milling center to get the job done in the vast majority of RF shield manufacturing jobs.
Why? Because CNC milling doesn’t require any hard tooling, it’s low on material waste and it can shorten lead times during critical phases, such as prototyping. It’s also accurate and perfect for small or large parts, both of which can describe RF shields in certain contexts.
However, there are other methods of production, and the manufacturing of gaskets to consider, but for the majority of RF shield designs, the CNC milling of metal housing is usually where the most questions arise.
Keep Inside Corner Radii Large
As you’re designing your machined housing for an RF shield, remember to keep the radii of your inside corners relatively large. Here’s why that’s important: Sharp inside corner radii can necessitate specialized tools and methods, such as electrical discharge machining (EDM).
A larger inside corner radius, on the other hand, allows faster and lower-cost tools with larger diameters to do the job. And that reduces your costs and your lead times.
Opt for Shallow Pockets
Another key RF shield design consideration is the depth of your pockets. If your pockets are too deep, you will need a longer tool to machine the part. That means you may get into specialized territory, which can drive your costs through the roof. It’s rarely impossible to manufacture a pocket of great depth, but it is quite often more expensive.
Thicken the Floor for Easier Manufacturing
How thick is the floor of your design? This is another RF shield design consideration that isn’t going to make your design impossible to manufacture, but it can certainly affect your lead times and costs. In general, the thicker the floor, the easier it is to manufacture the RF shield. A thinner floor is possible, but it requires a much more hands-on manufacturing run.

Read our Complete Guide to RF Shielding
Remember Your Scale
For all of the RF shield design tips we’ve covered so far, we have discussed the effect each consideration can have on lead times. As you decide how to approach each of the above considerations, you need to also keep in mind your scale. In other words, how many of these RF shields are you going to need to make?
Is it just a handful? Or are you thinking about mass production? Simplified designs that are faster to manufacture are much friendlier to mass production, while you can get a lot more complicated in your design if you’re just doing a proof-of-concept part or one-off design.
Seek Manufacturing Feedback
Engineers know their stuff. But do they know everything about all kinds of other fields? Absolutely not. And that’s OK, but it can cause problems in the manufacturing process sometimes. That’s because designing for functionality and designing for manufacturability are not always one and the same.
That simple fact explains why it is so important to work with a manufacturing partner who can offer expert feedback on the manufacturability of your RF shield. And it’s why we keep so many engineers on staff here at Modus.
Work with Modus
Here is one of the most important RF shield design tips: Work with Modus Advanced. Why? Because we have unmatched experience and a team full of engineers who know RF shield manufacturing inside and out. Through our complimentary DFM process, we’ll offer actionable feedback that will improve your device. And then we’ll manufacture your RF shield to your exact specifications.
Ready to get this RF shield designed and done with? We’re ready to make that happen for you. To start working with Modus, reach out to us online or give us a call at 925-960-8700.
Why Choose Modus for Your RF Shielding Needs?
When your critical applications require reliable RF shielding, partnering with a manufacturing expert can make the difference between a device that performs flawlessly and one that fails in the field. Modus Advanced combines engineering expertise with vertical integration to deliver RF shields that meet the most demanding requirements in aerospace, defense, and medical device applications.
- Engineering-First Approach: With over 10% of our staff being engineers, we provide expert design feedback that improves manufacturability and performance
- Vertical Integration: From machining to FIP gasket dispensing, plating, and assembly, all under one roof, reducing lead times and risk
- Quality Systems: AS9100 and ISO 9001 certified processes ensure consistent, high-quality RF shields that perform when lives depend on them
- Prototype to Production Partner: Support throughout your entire product lifecycle, from rapid prototype turnaround in days to efficient scaling for ongoing production volumes with consistent quality and performance
- Materials Expertise: Access to the full spectrum of RF shielding materials with guidance on selecting the optimal solution for your specific application
Partner with Modus Advanced to accelerate your path to market with RF shields manufactured to the highest standards of quality and precision; because when one day matters, having the right manufacturing partner is the obvious choice.
RF Shield Manufacturing