Don't Miss Out.... On-Site Thermal Interface Materials Lunch-and-Learn
February 20, 2017
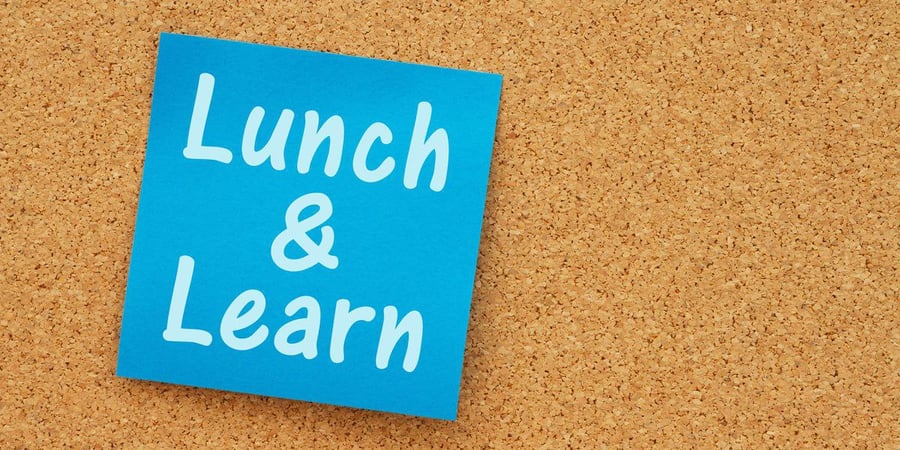
Manufactured with Speed and Precision
The manufacturing capabilities you need and the engineering support you want, all from a single partner.
Submit a Design- Facing thermal challenges in your current design?
- Interested in learning about industry leading thermal interface materials?
- Want to influence new thermal interface material product development?
- Need non-biased, outside perspective from a thermal technical expert?
Our lunch-and-learns are typically catered to company-specific thermal challenges or other issues involving areas of optimal design for thermal success. Maybe a brief thermal basics or thermal 101 is in order, or perhaps you wish to bring your product to the LNL and have our thermal expert analyze the current solution and consult on other thermal solution alternatives.
The point is, you are in control and ultimately dictate the exchange of information based on your applicable thermal challenges. This is not a marketing/sales presentation. In fact, other materials and solutions outside of our portfolio will be discussed if these solutions prove to lead to an optimal thermal solution!
Typical LNL format:
- Prior to the LNL, a selection of topics will be emailed to the group’s organizer.
- Once feedback is received, our thermal expert will tailor the information toward your specific requests/needs.
- Samples, materials, specific case studies and technical solutions will be available.
- Main drivers of discussion will be toward meeting specific expectations.
- This is not a sales presentation.
- Catered lunch will be provided by Modus Advanced, Inc. and Nolato.
Who should attend?
Previous LNLs have been attended by a variety of project stakeholders ranging from commodity managers, mechanical design team members, thermal engineers, manufacturing engineers, quality personnel, PCB engineers/board layout and project managers.
Benefits from attending:
- Learn from examining some of the most typical thermal challenges.
- Case studies can be presented and solution/cost benefits examined.
- Have open, two-way communication addressing your specific thermal challenges:
- How would we approach your thermal problem?
- We will examine your current design for optimal thermal performance.
- What is currently working – what can be improved – what is still missing?
- ROI – lunch and thermal expertise is provided free of charge – no travel cost – no cost to attend.
- Engage with a team of thermal experts and production partners who can support your thermal interface material requirements from concept to compliance on a global scale.
- Connect with industry experts who can provide applicable resources.
- Learn why the need for thermal interface materials is expanding.
- Gain an understanding of what exactly heat is and what are the mechanisms of transfer.
- Explore Thermal 101:
- Cool: Remove, Spread & Dissipate
- Shield: Divert, Disperse, Screen & Insulate
- Cover the basics of heat pipes, heat spreaders, heat sinks & fans.
Example of a Thermal Challenge & Solution Lunch-and-Learn Session
Customer is designing a consumer device and needs to cool a 10x10mm component with 1.2W power loss against a 100x50x4mm copper plate, which also is one of the device’s outer enclosure walls.
Normal ambient temperature for the application is specified as 25°C, and the customer is concerned that the case temperature of the component does not exceed 80°C.
Calculations show considering its orientation in the gravity field, and taking natural convection as well as radiation into account, the plate has a heat transfer coefficient of 5W/(m2·K).
Anticipated volumes are 100,000 pcs/month for 18 months.
The customer was considering a competing 3W/(m·K) thermal pad, at a cost of $0.020/pc. The nominal thickness of the material is 1mm, and the nominal bond-line thickness is 0.65mm.
Customer asked us to evaluate the parameters using 3 of our thermal pad materials as well as the initial competing material and provide a recommendation. The following materials were used in the calculations:
Nolato Compatherm® Pad 9411 – 1 W/(m·K)
Nolato Compatherm® Pad 9451 – 5W/(m·K)
Nolato Compatherm® Pad 9472 – 7W/(m·K)
Based on the input from the customer, we know the cross section area of both the conductor (copper plate) Ahs = 100x50mm = 0.1 x 0.05 m
as well as the cross of the component (CPU) ACPU = 10x10mm = 0.01 x 0.01 m
We also know the heat transfer coefficient is h = 5 W/(m2·K)
The bond-line thickness L = 0.65mm = 0.00065 m
Thermal Power (Q) is 1.2W (power loss)
An ambient temp tamb = 25 °C and a max temp tmax = 80 °C
Using formulae for thermal resistance, we then could calculate the resistance of the heat sink as well as plug in our 1, 5, and 7W/m·k) materials into the equation and compare cost vs. benefit of each material.
Heat sink: R = 1 / (5 x 0.1x0.05) = 40 K/W
Thermal Interface Materials Comparisons:
TIM 0: k = 3 W/(mK)(customer initial choice)
R = 0.00065 / (3 x 0.01x0.01) = 2.2 K/W
Δt = 1.2 x (40 + 2.2) = 51 °C
t = 25 + 51 = 76 °C
9411: k = 1.3 W/(mK)
R = 0.00065 / (1.3 x 0.01x0.01) = 5 K/W
Δt = 1.2 x (40 + 5) = 54 °C
t = 25 + 54 = 79 °C
9451: k = 5 W/(mK)
R = 0.00065 / (5 x 0.01x0.01) = 1.3 K/W
Δt = 1.2 x (40 + 1.3) = 50 °C
t = 25 + 50 = 75 °C
9472: k = 7 W/(mK)
R = 0.00065 / (7 x 0.01x0.01) = 0.93 K/W
Δt = 1.2 x (40 + 0.93) = 49 °C
t = 25 + 49 = 74 °C
We see the customer’s initial choice of using a 3W thermal pad as well as the other thermal pads used in the calculations will all ensure the case temperature of the component does not exceed 80°C. So, from a performance standpoint, any one of the thermals pads will work. If we now consider the cost parameter, we know the customer had a price of $0.20/pc for the initial 3W thermal pad. Below are the prices for the Nolato Compatherm® thermal pad:
9411 – 1 W/(mK) @ $0.016/pc
9451 – 5W/(mK) @ $0.049/pc
9472 – 7W/(mK) @ $0.054/pc
For this application, we see from the calculations that the customer can use a 1.3 W/(mK) thermal pad at a price of $0.016/pc.
Other factors, within various designs, are also examined and considered such as using a higher wattage thermal pad. This can reduce the length of the proposed heat-sink saving cost by eliminating extensive machining and cost of the heat-sink extrusion by 30%. Likewise, using a higher wattage pad enables a customer to reduce the number of cooling fans by half. In conclusion, all facets of the design are considered as well as how each component influences other areas of the thermal solution.
So, don’t waste your time attending our thermal interface lunch-and-learn unless you are…….
Case Study technical information provided by:
Jussi Myllyluoma,
Head of Product Line,
Thermal Senior Specialist at Nolato Silikonteknik AB.