What's My Solution: Thermal Pads or Thermal Form-In-Place?
February 9, 2017
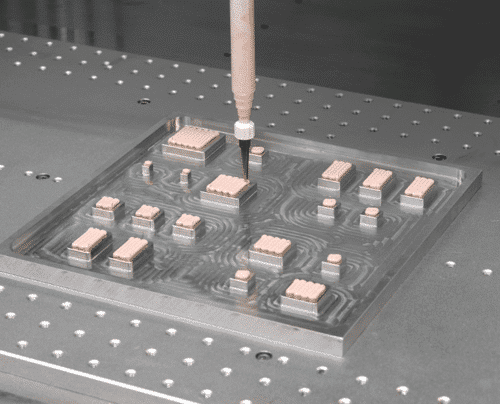
Manufactured with Speed and Precision
The manufacturing capabilities you need and the engineering support you want, all from a single partner.
Submit a DesignKey Points
- Selecting between thermal pads and form-in-place solutions requires considering factors like optimal supplier selection, material form (dispensed filler or discrete pad), and thermal conductivity requirements.
- Thermal fillers are typically more cost-efficient when you can set up inline dispensing operations in your manufacturing process, as they minimize material waste compared to cut pads.
Dispensing equipment for thermal fillers ranges from $15,000 for basic programmable options to $150,000+ for high-end systems, which can also be used for EMI shielding applications. - Thermal fillers provide better thermal performance than pads of similar conductivity because they wet adjoining surfaces more efficiently, reducing thermal contact resistance.
- Thermal pads offer superior portability, can be used without specialized equipment or training, and provide a wider selection of material variations to solve thermal management challenges.
- Consider annual volumes when deciding: higher volumes (hundreds of thousands+) make dispensing more economical, while lower volumes may favor thermal pads, especially if dispensing equipment budget isn't available.
As you’re probably aware, there are many different types of Thermal Interface Materials (TIMs) on the market. With so many variables, picking a thermal pad versus a form-in-place solution can be complex. Some of the variables include:
- Choosing the optimal supplier
- Form (dispensed filler or discrete pad)
- Thermal conductivity
When you add company specific performance requirements, selecting the right thermal pads or paste can be even more challenging.
Visit the Modus Form-in-Place Gasket Resource Center
First, we're going to tackle the thermal pad vs. paste debate with the hope of making the selection process a little easier. We will also very briefly touch on the various thermal conductivity options, as well as potential supplier selection, because both play an important part in the specification decision. We will get into a more in depth discussion of thermal conductivity and supplier selection in other blogs because they are both big topics.
For the purpose of this blog, we’ll use the term “thermal pad” to describe cut-to-size thermal interface materials. Keep in mind the industry is full of other terms such as thermal conductive pad, cpu thermal pad, thermal heat pads, not to mention specific brand name products such as The Bergquist Company’s (now part of Henkel) popular “Gap Pad” and Fujipoly’s “Sarcon Thermal Gap Filler Pads”.
Similarly, we’re going to use the term “thermal filler” to describe a dispensed thermally conductive gap filling material. Again, because there’s really no industry standard terminology, we’re using “thermal filler” in place of dispensed thermal paste, dispensed thermal pad and liquid gap filling materials.
Thermal Pad or Thermal Filler?
You're probably wondering, why is Modus Advanced, Inc. even discussing thermal pad or thermal filler options? We have customers who use both solutions to effectively transfer heat and have received plenty of feedback on using both solutions. We also die cut and CNC cut thermal pads as well as dispense everything from silicone to urethane materials. We’re discussing thermal management from a user perspective, not a material compounding perspective.
Ready to stop reading and get back to surfing YouTube for the latest drag racing times or bike tricks? Okay, a quick and simple way to make a decision is to figure out if your company or contract manufacturer is willing to set up to dispense thermal filler. If they’re willing to set up an inline dispensing operation and then ensure timely assembly of the components to the filler surface, then thermal filler is likely going to be the most cost efficient and highly recommended solution for you. So – if that’s all you need to know, feel free to jump back on YouTube, because you can now justify using the lower costs thermal filler solution in your assembly!
Thermal Filler - Dispensing Equipment
As mentioned above, thermal filler is typically recommended for onsite or inline dispensing applications. Thermal filler can be applied using off-the-shelf dispensing equipment. When shopping for dispensing equipment, you’re going to want lean towards programmable / automated dispensing options. We’ve seen decent robots from Nordson capable of dispensing thermal filler in the $15,000 range. If the budget is available and you’re looking for the ultimate in programming, motion control, and dispensing volume, high end dispensing equipment options from Datron and Rampf can run in the $150,000 plus range. Insiders tip – high end dispensing equipment can also be used to make high tolerance electrically conductive form-in-place gaskets (EMI shielding gaskets)! Just saying, from our experience, thermal interface materials and EMI shielding typically go hand in hand!
Read the Guide: Form in Place Gasket Guide
Thermal Filler – Set Up and Operator Training
We're not going to say learning to create uncomplicated programs on modern dispensing robots is easy, but it can certainly be learned in a matter of days or worst case weeks if your operator can only spend a couple hours per day on educating themselves. There are a variety of resources available to help operators get started, including onsite trainers, remote video (Skype et al.) and of course the trusty operator’s manual! Don’t let operator training influence your decision to purchase dispensing equipment. It’s not a long, drawn out process to learn to program basic movements and dispensing variables.
Thermal Filler – Advantages
As briefly discussed above, cost savings is probably the biggest advantage to using thermal filler vs. thermal pads. The easiest way to think about the cost advantage is being able to use a more optimized amount of dispensed thermal filler material needed to transfer heat. With the alternative thermal pad option, depending on the form factors, users may need to allow for varying amounts of drop or waste due to material yield issues in the cutting process. Obviously the less material waste, the lower cost for the solution.
A second advantage is the ability to quickly program different dispensing paths. If your application has more than one size and/or thickness of interface, you can dispense them all out of the same filler, instead of adding multiple TIM parts to the BOM, with the associated logistic and administrative costs.
Furthermore, if a revision change happens, there won’t be any tool or die costs associated with updating the thermal filler dispensing program. Changes to the dispensing parameters can also be done on demand, potentially reducing lead time for revision updates.
A third advantage, well worth bearing in mind, is that fillers generally tend to provide a better thermal performance than pads of similar conductivity. The reason for this is that as these materials are dispensed in a liquid state, they wet adjoining surfaces very efficiently, thus reducing the thermal contact resistances.
Thermal Filler – Disadvantages
The obvious disadvantage to thermal filler is the potential requirement of adding a new manufacturing process. Depending on the quality system your company or CM operates under, a new manufacturing process could be as simple as buying the equipment and installing it; or as difficult as researching, budgeting, testing, qualifying and finally, training multiple operators to program and monitor the robot!
A second and maybe less obvious disadvantage to thermal filler is the ratio of parts produced to set up time. Setting up a robot to dispense a few dozen or a couple of hundred parts will probably not be the most cost efficient option, considering it could take an hour or more to set up and test an existing program. A new program could take a day or more depending on the machine operator’s level of competence. This if course takes into account not only machine movement, but the volume of material being dispensed, and the time required to test the dispensed product.
A third consideration is also related to volume, and the use of two-part fillers in particular. These materials are mixed in a static mixer nozzle. If the material in the nozzle cures too much, the nozzle will need to be discarded, meaning that all the material that has gone into it will be lost. Depending on the pot life of the material used and the production down time between shifts, this may end up happening more or less often.
A further caveat to bear in mind concerns the dispensing equipment. Due to the nature of the thermally conductive particles, thermal filler compounds are highly abrasive. The pumps, valves and other components of the dispensing equipment absorb these demands, alleviating the reduction of rapid equipment wear out. Because of that, there are really only a handful of manufacturers that provide equipment suitable for thermal filler dispensing.
Case Study: Redefining the traditional supplier relationship.
Thermal Pads - Die Cutting Process
Thermal pads are typically cut from sheets based on customer requirements. Depending on the thermal interface material manufacturer, standard sheet sizes are typically less than 24” x 24”. Many material converters (companies like Modus™ who convert sheets to pads) use a die cutting process to manufacture thermal pads to customer specific requirements. While there are a variety of ways to cut thermal pads, the die cutting or stamping method can consistently produce excellent quality parts, meeting the toughest tolerance specifications, especially on thinner materials.
A die is required to manufacture thermal pads using this cutting method. Expect to pay somewhere in the neighborhood of $250 to $500 for a die cutting set up charge. What’s nice is, the die can be used to make tens of thousands of parts, or even hundreds of thousands of parts in some cases before it needs to be replaced.
Thermal Pads – Advantages
Probably the biggest advantage to using thermal pads are their portability. Die cut thermal pads can be shipped anywhere in the world and used in multiple locations on the factory floor without having to program robots or train technicians. Pads are cut in advanced and used on demand.
The pads also continue to be portable after being mounted in place. It is fully possible to mount pads; e.g., on a heat sink day one; and then ship these to an assembly plant to mount on the PCB two days later.
Another major advantage to using die cut thermal pads is the wide variety of materials available to overcome thermal management challenges. Today’s
thermal management consumer can literally pick from hundreds, if not thousands, of material variations from sources all over the world.
A word of caution, be sure to research material quality and supplier claims before picking a material! Many of the top thermal suppliers make test reports available to potential customers to help back up their claims.
Thermal Pads – Disadvantages
Probably the biggest disadvantage to using thermal pads is they could be more expensive than the thermal filler option. As previously discussed, thermal pads are cut from sheets. Depending on the pad and sheet size, you can typically expect a maximum sheet utilization of 90%. Of course, there are exceptions where “Mr. Super Die Cut Operator” will get a 95% yield, but don’t count on it!
Depending on the type of cutting operation, the form factor of the parts, and the flexibility of the sheet forming process, this can vary a lot more towards more efficient sheet utilization. With the rectangular parts usually used in the telecommunications industry, in addition to “Mr. Super Die Cut Operator”, you could actually see yield rates in the 95 – 100% range!
Full disclosure – depending on the shape of the part, yields of 80% are also very common. This means the customer is paying for not only the pads cut from the sheet, but also the 20% of the sheet being discarded. For lower volumes, the sheet yield may not be much of a consideration, but those with higher volumes should at least consider a dispensing option.
Your Best Option
Wouldn’t it be nice if there was an easy and obvious solution? A decent strategy for deciding between the two options might be to start with considering annual volumes. If you’re going to need hundreds of thousands or more, you should probably consider the dispensing option. If your usage will ramp over time and the budget isn’t currently in place to add a dispensing line, thermal pads might be the best option (or the obvious choice). You will definitely want to consider overall cost, material quality and your supply chain options as well when making the decision.
Effective heat transfer is vital to creating efficient and reliable products, so choosing the correct TIM is a key factor to a product’s success and longevity in the marketplace. Modus Advanced, Inc. offers a variety of TIM options through its WesTherm™ and Nolato Compatherm™ products.
Nolato's Compatherm® gap filleris a thermally conductive material developed to meet the growing demand for reliable, cost-effective TIMs. Ideal for applications requiring heat transfer from a PCB to a heat sink, these ultra-soft and pliable materials can drastically cut thermal resistance and greatly enhance cooling by filling air gaps and small irregularities. Available over a wide range of thicknesses, mechanical properties, liner solutions and thermal performances, this material can also be customized. Nolato's Compatherm® materials are available in both thermal pads and thermal filler.
Why Choose Modus Advanced for Your FIP Gasket Dispensing
At Modus Advanced, we've mastered the art and science of FIP gasket dispensing while offering a complete manufacturing ecosystem that accelerates your path to market. Our engineering-first approach means your critical components receive expert attention at every stage.
With Modus, you gain:
- Vertical integration that eliminates shipping between vendors and reduces lead times
- Concurrent manufacturing processes including machining, plating, and thermal material application
- Engineering expertise with over 10% of our staff being engineers who understand your technical challenges
- Enhanced quality control through a single quality system governing the entire process
- Simplified communication with one partner instead of multiple vendors
When one day matters—and we believe it does—our vertically integrated approach doesn't just save time; it helps your innovations reach the field faster, whether that's life-saving medical devices or mission-critical defense systems.
FIP Dispensing Services