Top EMI Shielding Materials for Defense Systems
March 27, 2025
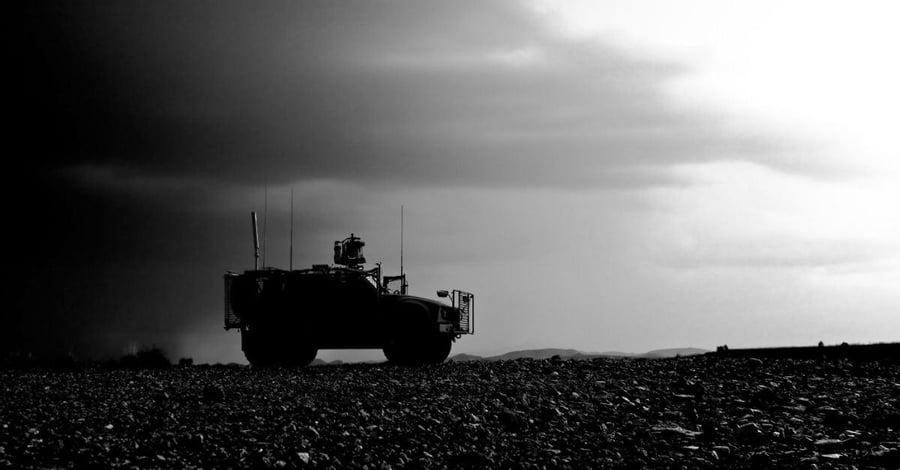
Manufactured with Speed and Precision
The manufacturing capabilities you need and the engineering support you want, all from a single partner.
Submit a DesignKey Points
- The proliferation of electromagnetic threats in modern warfare environments demands increasingly sophisticated EMI shielding solutions
- Material selection must address both broad-spectrum shielding effectiveness and compliance with rigorous military specifications
- Advanced composites and engineered materials are emerging as critical solutions for next-generation defense systems
- Proper material selection requires deep understanding of specific defense applications and their operating environments
- Comprehensive testing and validation according to military standards is essential for mission-critical systems
The increasing complexity of modern defense systems has created significant electromagnetic interference shielding challenges. Today's battlefield environments are saturated with electromagnetic signals from communication systems, radar installations, electronic warfare equipment, and countless other sources operating across an expanding frequency spectrum.
A single unprotected vulnerability in electromagnetic shielding can compromise mission-critical systems, potentially degrading radar accuracy, disrupting secure communications, or interfering with precision guidance systems.
This proliferation of electromagnetic threats, combined with the integration of increasingly sensitive electronic components in defense systems, makes shielding material selection for EMI shielding more critical than ever. Engineers must now consider materials that can provide protection across broader frequency ranges while meeting strict military specifications for durability, reliability, and performance in extreme environments.
It sounds like a daunting task, but we’re here to help. Read on.
Learn everything you need to know about EMI Shielding.
Shielding Material Performance Considerations
Modern defense systems operate across a vast range of frequencies, from low-frequency communications to high-frequency radar systems operating above 40 GHz. EMI shielding materials must demonstrate effectiveness across this entire spectrum while maintaining performance under extreme conditions.
Specific defense applications drive unique requirements. Radar systems, for instance, require materials that can provide up to 120 dB of shielding effectiveness at frequencies between 8-12 GHz, while electronic warfare systems may need protection across multiple bands simultaneously. The challenge intensifies when dealing with systems that both emit and receive signals, requiring careful management of internal and external EMI.
Military specifications add another layer of complexity. Materials must meet standards like MIL-STD-461G for EMI characteristics and MIL-STD-810H for environmental conditions. In many cases, they must also satisfy low observable requirements and maintain performance even after exposure to chemical, biological, or nuclear environments.
Common Base Materials
Defense applications require careful selection of base materials that satisfy both EMI shielding and military durability requirements. Each EMI Shielding material presents unique advantages for specific defense scenarios.
Aluminum, particularly in aerospace-grade alloys like 6061-T6, provides excellent shielding effectiveness of 80-120 dB while maintaining a crucial lightweight profile for airborne systems. Its corrosion resistance can be enhanced through chromate conversion coating or other MIL-SPEC surface treatments.
Stainless steel, particularly grades like 304 and 316, offers superior durability and corrosion resistance critical for naval defense applications. With typical shielding effectiveness ranging from 60-110 dB, it's particularly suited for shipboard radar systems and maritime communication equipment where salt spray exposure is constant.
Copper and its alloys, including beryllium copper and phosphor bronze, provide exceptional conductivity with shielding effectiveness often exceeding 100 dB. While weight and cost often limit their use, these materials prove invaluable in specialized applications like high-sensitivity SIGINT equipment or electronic warfare systems where maximum magnetic shielding is paramount.
Galvanic Compatibility Considerations for Defense Applications
When designing defense EMI shielding systems, engineers must carefully consider the galvanic compatibility between materials, particularly in maritime or high-humidity environments. Galvanic corrosion occurs when dissimilar metals come into contact in the presence of an electrolyte (such as saltwater spray), potentially compromising both structural integrity and shielding effectiveness over time.
The galvanic compatibility chart below ranks common metals and alloys used in defense EMI shielding by their galvanic potential, providing critical guidance for material selection in mission-critical systems:
Galvanic Compatibility Chart for EMI Shielding in Defense Applications
Metal/Alloy | Galvanic Index | Compatible With | Use Caution With | Avoid Contact With | Typical Shielding Applications |
Gold | 0.00 (Noble) | All metals in this chart | None | None | High-sensitivity SIGINT connectors, space applications |
Silver | 0.15 | Gold, Nickel, Stainless Steel | Beryllium Copper, Brass | Aluminum, Magnesium | Conductive filler in elastomers, high-frequency connectors |
Nickel | 0.30 | Gold, Silver, Stainless Steel | Copper, Brass | Aluminum, Magnesium | EMI gaskets, conductive coatings |
Stainless Steel (316, 304) | 0.50 | Gold, Silver, Nickel | Copper, Brass | Aluminum, Magnesium | Naval radar housings, maritime communications |
Beryllium Copper | 0.65 | Gold, Nickel | Silver, Copper | Aluminum, Magnesium | Spring fingers, EMI gaskets |
Copper | 0.72 | Gold, Nickel | Silver, Brass | Aluminum, Magnesium | RF cable shielding, ground planes |
Brass | 0.80 | Gold, Nickel | Silver, Copper | Aluminum, Magnesium | Connector shells, waveguides |
Tin | 0.94 | Gold through Brass | Aluminum | Magnesium | Plating for connectors, soldering |
Aluminum Alloys | 1.10 (Active) | Aluminum, Zinc | Tin, Stainless Steel (with barrier) | Gold, Silver, Copper, Nickel, Brass | Airborne system housings, lightweight enclosures |
Magnesium Alloys | 1.60 (Highly Active) | Magnesium, Zinc | Aluminum (with barrier) | All other metals in this chart | Ultra-lightweight drone components |
Implementation Notes for Defense Systems:
- Lower galvanic index numbers indicate more noble/cathodic metals (less likely to corrode)
- Higher galvanic index numbers indicate more active/anodic metals (more likely to corrode)
- For mission-critical systems, maintain galvanic index differences below 0.25 for direct metal-to-metal contact
- When dissimilar metals must be joined, implement appropriate finishes (per MIL-DTL-5541, MIL-C-81706) or isolating elements while maintaining EMI shielding continuity
- Maritime defense applications require additional protection measures for any metal combinations with index differences greater than 0.15
Implementing appropriate barriers between incompatible metals while maintaining electrical conductivity for EMI shielding presents a unique challenge in defense applications. Conductive elastomers with carefully selected fillers can serve dual purposes, providing both EMI shielding and acting as a galvanic barrier between dissimilar metals.
-- Article Continues Below --
Visit the full resource center here
Conductive Elastomers and Gaskets
The dynamic nature of defense systems, particularly in mobile platforms, requires a flexible EMI shielding solution that can maintain performance under constant movement and vibration.
Modern conductive elastomers must satisfy an array of military specifications while providing consistent shielding effectiveness. Options for EMI Materials include:
- Silver-aluminum filled silicones: Offering shielding effectiveness up to 120 dB, these materials excel in aerospace applications where galvanic corrosion resistance is crucial
- Nickel-graphite composites: Providing 60-100 dB shielding with excellent durability, these materials are ideal for ground-based systems and vehicles
- Fluorosilicone-based elastomers: Essential for applications exposed to jet fuel or hydraulic fluids, these materials maintain shielding effectiveness even after chemical exposure
- Hybrid materials: Combining multiple fillers to achieve optimal performance across specific frequency bands while maintaining environmental resistance
The compression set and durometer specifications become particularly critical in defense applications where exposure to extreme temperature cycles and high-vibration environments is common.
Advanced Composite Materials
The evolution of defense systems has driven rapid advancement in composite EMI shielding materials that can satisfy multiple requirements simultaneously.
Carbon fiber composites, when properly engineered, can provide structural strength while delivering 60-80 dB of shielding effectiveness. These materials are increasingly crucial in drone technology and unmanned systems where weight reduction is paramount.
Metal matrix composites (MMCs) represent a significant advancement for defense applications. Aluminum-based MMCs can provide enhanced shielding effectiveness up to 100 dB while offering superior heat dissipation - crucial for high-power radar and electronic warfare systems.
Nano-engineered materials, including graphene and carbon nanotube composites, are emerging as next-generation solutions. Early testing shows potential for achieving shielding effectiveness above 90 dB while adding minimal weight - particularly valuable for advanced missile systems and hypersonic applications.
Environmental Considerations
Defense systems must maintain EMI shielding integrity across environmental extremes that far exceed commercial requirements. Material selection must account for the full spectrum of military operational conditions.
Temperature requirements often range from -65°C to +165°C for aerospace applications, with rapid cycling that can stress material bonds and change conductivity characteristics. High-altitude applications must maintain shielding effectiveness in low-pressure environments, while desert operations require resistance to sand erosion and UV exposure.
Maritime defense applications present particularly challenging requirements. Materials must maintain specified shielding levels after 3,000+ hours of salt fog exposure per MIL-STD-810H Method 509.7. Additionally, they must resist degradation from aircraft fluids, hydraulic oils, and deicing solutions while preventing galvanic corrosion between dissimilar metals.
Testing and Validation
Defense EMI shielding materials require exhaustive testing beyond basic shielding effectiveness measurements. A comprehensive validation program typically includes:
- MIL-STD-461G compliance testing across all applicable frequency ranges
- Transfer impedance testing per ASTM D4935-10
- Shielding effectiveness verification through IEEE-STD-299
- Environmental cycling per MIL-STD-810H
- Accelerated aging studies simulating 20+ year service life
- Vibration and shock testing according to MIL-STD-167-1A
- Chemical resistance validation against MIL-PRF-131K
Real-world performance validation often requires custom test protocols that simulate specific operational conditions. For radar systems, this might include testing under high-power RF exposure, while SIGINT applications might require validation of shielding consistency across broader frequency ranges.
Implementation Best Practices
The effectiveness of EMI shielding materials in defense systems depends heavily on proper implementation that maintains performance under battlefield conditions.
Surface preparation must meet military specifications for conductivity and corrosion resistance. For example, aluminum surfaces typically require chromate conversion coating per MIL-DTL-5541F, while stainless steel might need passivation according to ASTM A967.
Installation procedures must account for:
- Proper compression of gasket materials (typically 15-45% depending on material)
- Fastener spacing to maintain consistent surface conductivity
- Prevention of galvanic corrosion at material interfaces
- Maintenance of shield integrity around necessary penetrations
- Verification of surface conductivity post-installation
Design Integration
Early integration of EMI shielding considerations in the design phase is crucial for defense systems. Modern battlefield electronics often operate at higher frequencies and power levels than ever before, making retrofit solutions increasingly challenging.
Multi-physics simulation tools have become essential for predicting EMI shielding performance during design. These tools can model complex interactions between thermal management, structural requirements, and EMI shielding effectiveness before prototyping begins.
Advanced computer modeling can predict potential EMI hotspots and identify areas where enhanced shielding may be required. This is particularly crucial for systems like phased array radars where multiple frequency bands must be managed simultaneously.
Quality Control Considerations
Quality control for defense EMI shielding materials requires unprecedented rigor. Each step must be documented and traceable to support mission assurance requirements.
Material qualification processes must include:
- Full chemical and physical property analysis of each production lot
- X-ray fluorescence testing to verify filler content in elastomers
- Surface resistivity mapping of conductive materials
- Detailed documentation of all processing parameters
- Regular audit of supplier quality systems
- Verification of material pedigree and country of origin per DFARS requirements
Final Thoughts
The selection and implementation of EMI shielding materials for defense systems requires deep understanding of both material properties and specific application requirements. Success depends on careful consideration of all operational parameters, from electromagnetic performance to environmental durability.
At Modus Advanced, our engineering team specializes in defense applications. Our AS9100 certification and ITAR compliance enable us to provide EMI shielding solutions that meet the most demanding defense requirements.
Contact our engineering team today to discuss your specific EMI shielding challenges and learn how we can help ensure your defense systems perform reliably in even the most challenging operational environments.