7 Critical Factors to Consider When Choosing Medical-Grade Seals
August 21, 2024
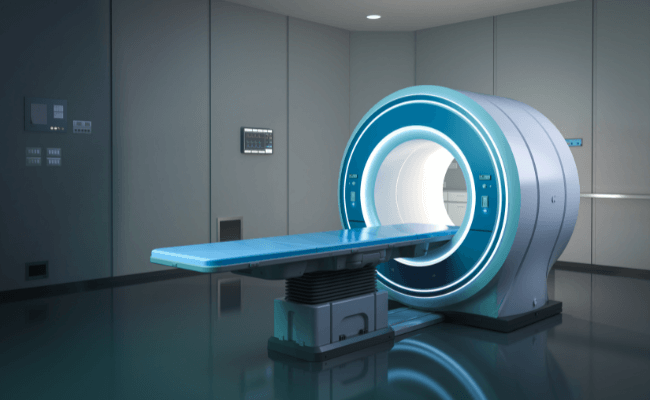
Manufactured with Speed and Precision
The manufacturing capabilities you need and the engineering support you want, all from a single partner.
Submit a DesignKey Points
- Material Compatibility and Sterilization Resistance are crucial for medical-grade seals, ensuring they withstand bodily fluids, medications, and sterilization processes without degrading, thus maintaining device safety and functionality.
- Durability, Precision, and Regulatory Compliance are essential factors in seal selection, guaranteeing long-term performance, dimensional stability, and adherence to stringent standards like FDA and ISO, which are vital for patient safety and device reliability.
- Customization and Quality Control are key to meeting unique device requirements, with tailored solutions and robust traceability ensuring optimal performance, regulatory compliance, and cost-effectiveness in medical device manufacturing.
In the high-precision world of medical device manufacturing, the devil's in the details - and those details often come down to components smaller than a dime. We're talking about medical-grade seals, the unsung heroes that keep your devices safe, effective, and reliable.
We're about to break down seven critical factors you need to consider when choosing medical-grade seals. Trust us, this isn't just another checklist - it's your roadmap to devices that don't just meet standards, but blow them out of the water.
So grab your coffee, settle in, and let's seal the deal on creating top-notch medical devices.
Get the complete guide to medically compliant seals for medical device manufacturers here!
1. Material Compatibility of Medical Seals with Bodily Fluids and Medications
When it comes to medical-grade seals, we're not just talking about keeping things tight - we're talking about keeping things safe. Let's dive into the first critical factor: material compatibility.
Importance of Biocompatibility
When it comes to medical grade seals, biocompatibility is non-negotiable. The materials used must be compatible with bodily fluids and medications to prevent adverse reactions. This is especially crucial in devices and equipment that come into direct contact with human tissue or fluids.
Resistance to Chemical Degradation
Medical devices often encounter a variety of chemicals, from bodily fluids to cleaning agents. The seals must resist chemical degradation to maintain their integrity and functionality. Materials like silicone, EPDM (ethylene propylene diene monomer), and PTFE (polytetrafluoroethylene) are commonly used due to their excellent chemical resistance.
Consideration of Potential Reactions with Living Tissue
The potential for materials to react with living tissue must be carefully evaluated. For instance, some materials may cause inflammation or other adverse reactions. Selecting materials and compounds that are proven to be safe for medical applications is essential.
Examples of Compatible Materials
- Silicone: Known for its flexibility and biocompatibility, silicone is widely used in medical seals.
- EPDM: Offers excellent resistance to heat, ozone, and weathering, making it suitable for various medical applications.
- PTFE: Known for its non-reactive properties and high resistance to chemicals and temperature extremes.
2. Sterilization Resistance
We've tackled compatibility, but let's face it - in the medical world, clean isn't just clean, it's sterile. And that's where our second critical factor comes into play: sterilization resistance.
Let's break down why this matters and how to ensure your seals can take the heat (or radiation, or chemicals).
Common Sterilization Methods
Medical devices must undergo a range of rigorous sterilization processes to ensure they are free from contaminants. Common sterilization methods include autoclaving, gamma radiation, and ethylene oxide (EtO) sterilization.
Impact of Sterilization on Seal Integrity
Different sterilization methods can affect seal materials in various ways. For example, autoclaving involves high temperatures and pressure, which can degrade some materials. Gamma radiation can cause changes in material properties over time.
Material Selection Based on Sterilization Requirements
Choosing materials that can withstand the specific sterilization methods used in your manufacturing and molding process is crucial. Silicone and PTFE, for example, are known for their ability to endure multiple sterilization cycles without significant degradation.
Importance of Maintaining Seal Performance After Repeated Sterilization Cycles
Medical devices often require repeated sterilization throughout their lifecycle. Ensuring that seals maintain their performance after multiple cycles is essential for device reliability and patient safety.
3. Durability and Longevity of Medical Grade Elastomers
When it comes to medical-grade seals, durability and longevity are crucial. These components must withstand repeated use, environmental stresses, and maintain their integrity over time. Medical-grade seals need to resist wear, compression set, and fatigue, with materials like silicone and EPDM known for their resilience. The seal's lifespan should align with the device's lifecycle, ensuring functionality and safety throughout its intended use.
In critical applications, long-term performance is paramount for patient safety and device reliability. Durability testing is essential to ensure seals can handle rigorous conditions and repeated use, revealing any potential weaknesses before market release. This focus on durability not only protects patients but also contributes to the overall reliability and cost-effectiveness of medical devices.
4. Precision and Dimensional Stability
Our fourth critical consideration is all about precision and dimensional stability. Think of it as the difference between a seal that fits like a glove and one that's as useful as a screen door on a submarine.
Importance of Maintaining Seal Dimensions Over Time
Precision and dimensional stability are crucial for ensuring a proper fit and function of the seal within the medical device. Any changes in dimensions can compromise the device's performance and safety.
Impact on Device Performance and Leak Prevention
Dimensional stability directly impacts the device's ability to prevent leaks and maintain a proper seal. Even minor deviations can lead to significant issues in medical applications.
Consideration of Temperature and Pressure Fluctuations
Medical devices often operate in environments with varying temperatures and pressures. The seal material must maintain its dimensions and properties under these conditions to ensure consistent performance.
Material Selection for Optimal Dimensional Stability
Materials like PTFE and certain high-performance elastomers are known for their excellent dimensional stability, making them ideal for medical seals.
5. Regulatory Compliance
Navigating the maze of standards and regulations might seem daunting, but it's essential for ensuring your devices are safe, effective, and market-ready.
Medical devices must comply with stringent regulatory standards such as FDA regulations, ISO 10993 for biocompatibility, and USP Class VI for material safety. Using certified materials and manufacturing processes ensures that the seals meet these regulatory requirements and are safe for medical use, including thorough documentation and traceability of materials and processes.
This level of documentation is crucial for addressing any issues that arise and ensuring regulatory compliance. Moreover, compliance must be maintained throughout the entire supply chain, from raw material suppliers to final product manufacturers.
Partnering with suppliers who understand and adhere to these regulatory requirements is essential for maintaining the integrity and reliability of your medical devices.
6. Customization Capabilities for Medical Applications
One size definitely doesn't fit all, especially in medical devices. Customization capabilities are crucial for designing seals that meet unique device requirements. Off-the-shelf solutions often fall short, making bespoke seals essential.
Addressing Unique Device Requirements
Customization allows for the creation of seals tailored to specific needs, ensuring optimal performance under pressure.
Importance of Working with Manufacturers Offering Custom Solutions
Partnering with manufacturers who provide custom solutions ensures seals are designed to your exact specifications, including material selection, dimensions, and performance characteristics.
Considerations for Prototyping and Scaling to Production
Custom seals often require prototyping to meet desired specs and performance criteria. Manufacturers capable of efficiently scaling from prototype to production are invaluable.
Balancing Customization with Cost-Effectiveness
While customization can increase costs, it's often necessary for optimal device performance. Balancing customization with cost-effectiveness ensures quality without breaking the budget.
7. Quality Control in Seal Design and Traceability
Let's talk about dotting our i's and crossing our t's. Our final critical factor is quality control and traceability - the unsung heroes of medical device manufacturing.
Rigorous quality control ensures your seals meet or exceed required standards. It's about catching issues before they become problems. Traceability is equally crucial, allowing you to track materials and processes from start to finish. This isn't just about compliance; it's about peace of mind.
Lot control and thorough documentation are non-negotiable. They ensure each batch of seals can be traced back to its origins, crucial for quality assurance and regulatory compliance.
Partnering with suppliers who have robust quality management systems is key. Look for those adhering to ISO 9001 and other relevant standards. Remember, your seal supplier isn't just a vendor - they're a critical partner in your success.
Elevating Your Medical Device Manufacturing with the Right Seals
We've just taken a whirlwind tour through the seven critical factors that can make or break your medical-grade seal selection. From material compatibility to quality control, we've covered the essentials that'll keep your devices performing at their peak and your regulatory compliance team sleeping soundly.
At Modus Advanced, we live and breathe this stuff. We're not just talking the talk—we're walking the walk with our vertically integrated manufacturing processes and our commitment to custom solutions that fit your needs like a glove.
So, the next time you're faced with a sealing challenge, don't sweat it. Armed with this knowledge and a partner like Modus, you're ready to take your medical devices from good to great, from prototype to production, and beyond. Contact us today.