The High Cost of Using Renewable Resources to Manufacture Custom Rubber Products
August 15, 2017
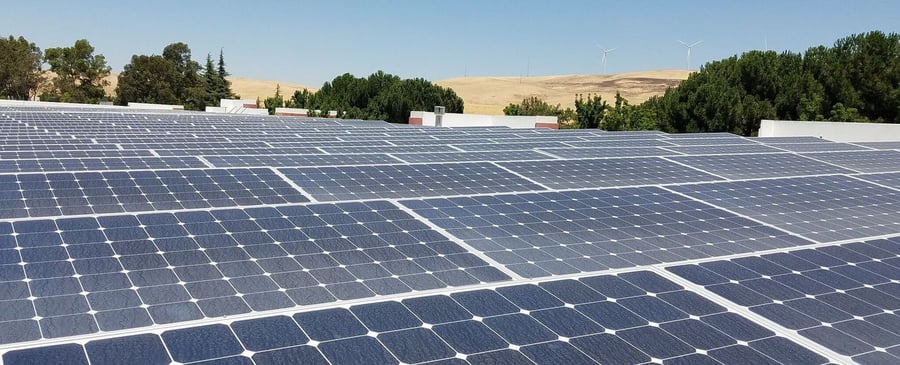
Manufactured with Speed and Precision
The manufacturing capabilities you need and the engineering support you want, all from a single partner.
Submit a DesignSustainability, renewable resources and environmental awareness aren’t just buzzwords to toss up on a website. Today, the world is more aware than ever of the effects of human activity on our planet. With humans speeding climate change up to 170 times faster than natural forces, organizations have a responsibility to find ways to be more sustainable, even if there’s a cost associated with it.
In the past, manufacturing was a notorious culprit of industrial pollution. Now, with so many new sustainable technologies out there, industry has an opportunity to shrink its footprint and invest in the future. Of course, the short-term setup costs can be intimidating. But in the long run, investments in green manufacturing technologies can save money and keep our planet healthy. A win-win!
Want more insight into cutting costs during die cut gasket manufacturing? Download our latest guide and avoid the 5 common gasket design oversights:
At Modus Advanced, Inc., we believe everyone has a right to drink clean water and breathe fresh air. With this guiding principle, we budgeted for and invested in sustainable manufacturing practices such as:
- A closed loop water recycling / purifying system to ensure industrial waste from our waterjet doesn’t get flushed into our waterways
- A solar powered manufacturing plant to reduce our dependence on fossil fuel energy and reduce operation costs
- A remote workforce to help limit employee commutes and reduce carbon emissions
- A company-subsidized Vanpool to further limit carbon emissions
Let’s take a look at how these practices can benefit the environment as well as impact your budget.
Waste Water Discharge to Sewer Avoided via Closed-loop Water Recycling
The 100-horsepower pump on our water jet is powerful enough to cut 8 inch thick aluminum, yet can also be tuned to cut foam with extreme precision. The Flow Mach 4 Waterjet is a cutting edge machine tool used to create custom components for our customers. The waterjet system cycles city water through multiple filters before using the water as part of the process to cut rubber, foam, carbon fiber, glass, steel and other materials into intricate shapes.
Image: Flow Waterjet Cutting Maching
Waterjets cut material through a process of controlled erosion. The concept is like turning on your garden hose and using it on its most focused setting. Dirt and grass eventually give way to the stream of water. The same holds true for the cutting process on a waterjet, except the stream is obviously much more focused than a garden hose!
Controlled erosion means particles of raw material are being removed from the sheet of rubber or other material to make parts. Where do the small particles go? Most of the waste drops to the bottom of the waterjet tank, but a small number of dissolved solids make their way into the stream of water and exit the tank. The process was designed this way. It’s not possible to push an endless stream of water into the waterjet tank! The water coming into the system must go somewhere!
The waste water stream is where the owner of the waterjet needs to decide. Will the water be treated before it hits the city sewer? If the waste water is sent down the sewer without being treated, there’s a potential for harmful materials making their way into an unprepared city system.
Check out the image below to see what a normal waterjet pump system looks like.
Image: Waterjet pump system (Source: Flow International Corporation)
On the other hand, a closed loop water recycling system filters dissolved solids from the cutting process, filters the water and feeds clean water back into the waterjet for further cutting. The closed loop system eliminates our local city requirement to test spent water for potentially hazardous dissolved solids before going down the drain.
Image: Closed Loop Water Recycling System (Source: Ebbco Inc.)
Strangely (from a containment perspective), the city only wanted us to test our water after the cutting process. By that time dissolved solids would have made their way down the drain. This means if we were ever to unknowingly release hazardous waste water into the sewer, we would have found out after we did so! Then what?
Was there a cost to set up a closed loop system? Absolutely! We spent north of $30,000 on the system and about $5,000 on distributing electrical to the system. Not only was there an upfront cost for the system, but properly disposing of the filter media costs us another $800 to $1000 per month. Was there a monetary cost and does it affect our pricing strategy, you bet. We can also sleep at night knowing we made the decision to act in the interest of the environment.
Solar Panels: An Investment in Sustainability
The amount of solar energy hitting the earth equates to more than 10,000 times the world's total energy use. Harnessing this energy more efficiently year over year has led to an extraordinary growth of the solar industry. As technology develops and demand increases, the economic advantage of solar power are becoming obvious and more attainable by homeowners and businesses. Federal tax credits, significant utility cost reduction, protection against fluctuating electricity rates, and a low maintenance energy system are just a few benefits to the commercial sector investing in solar power.
The decision to install solar panels was tough at first – we knew the upfront costs would be more than $350,000. But, we realized we were playing the long game, both with our company and our planet. Then it just made sense. The results have been astounding. In the past 3.5 years, our panels have generated 512 MWh of energy. The graphic below shows the impact the system has had on our carbon footprint so far.
Image: Capture of the environmental benefits gained from the use of renewable energy
What is the long game anyway? From a business perspective, it’s the realization Modus Advanced, Inc. could very well be producing custom rubber parts 20 years from now. With a life expectancy of 25 years, our solar powered factory will have an enormous impact on the environment moving forward. Facts from the Solar Energy Industries Association® show that we are not alone in this movement.
- Solar panels owned by businesses produce enough energy to power 193,000 homes
- Corporations in the U.S. offset approximately 1.1 million metric tons of CO2 emissions
- Top U.S. businesses have increased their solar capacity by 240% since 2012
Image: Solar panels installed on the roof of Modus Advanced's facility Image: Solar power monitoring system
The installation was quite expensive even with the significant tax credit from the State, but once we complete the payments, our operating costs will be significantly lower. For those who’re interested, our payments on the system are about $7500 per month. We’re essentially paying an extra $2000 to $3000 per month for solar. The cost burden has forced us to find creative ways to operate leaner and do more with less. In fact, that brings us to our next method of environmental cost control.
Remote Workforce and Vanpooling: More Satisfied Employees, Smaller Footprint
While a lot of the work we do requires hands-on expertise in the factory, we also have a sizeable number of employees who can do their job from anywhere. When our remote employees do come in to the office, the in-house hours are planned and coordinated for maximum effect. Extensive use of video chat when not in the office has helped maintain working relationships and improve communications with remote team members. Not only does our remote workforce eliminate unnecessary commutes, but research has shown an array of other benefits.
Image Source: Control
Working from home has been shown to increase worker productivity, lower stress, reduce employee turnover, and lead to greater engagement. Organizations that offer work from home options reduce their carbon footprint, cut costs, and make their employees happier.
In fact, 43% of Americans said they spent at least some time working remotely in 2016. With this growing trend becoming a major attraction to desirable talent, it’s in every company’s best interest to consider how working from home could benefit their organization.
As mentioned, a lot of our employees need to come to the office every day to get their jobs done. That’s why we invest in a company-subsidized vanpool to facilitate ridesharing to our site. Instead of each of our employees driving their own car to work, they can enjoy a chauffeured ride. And on that ride, they can enjoy the knowledge that they’re saving money on gas and insurance while reducing their carbon footprint.
Image Source: MTA
So why does all this matter to OEM customers?
In our evolving global market, engineers need to find ways to make their products both competitive and sustainable to produce. Raw materials and the energy to convert them into something useful are not as abundant as they once were. Modus is spending over $10,000 month on eco-friendly initiatives because we choose to consider the environment.
Dedicating an organization to sustainability and environmental cost control is a lot like packing. At first glance, everything in the bag seems essential. Of course, you’ll need your binoculars on your trip, right? But, when you really consider the value and burden of each item in the pack, you can find ways to remove unnecessary weight and lighten your load. At Modus, we’ve been doing the same thing. We closely examine our processes, the machines we use, and the resources we consume to see if there are ways we can be more efficient. The above examples stand as a testament to that scrutiny. As we continually investigate cost reduction opportunities, we remain confident knowing that our initiatives will not be at the expense of the environment because we have committed to a greener approach.
When a company decides to make the change towards environmental responsibility, the International Organization for Standardization provides a set of standards to follow to ensure operations and business development goals are in line with the criteria required for an effective environmental strategy. ISO 14001 environmental management system may be utilized in its entirety or in pieces across any industry to measure and achieve environmental objectives.
Knowing this, engineers should strategize on ways to implement environmental cost control into their organizations, designs, and production processes. Doing so not only helps our planet and reduces operation costs over time, but it also attracts and retains a happy, dedicated workforce.