Emerging Trends in EMI Shielding for Space Applications
March 13, 2025
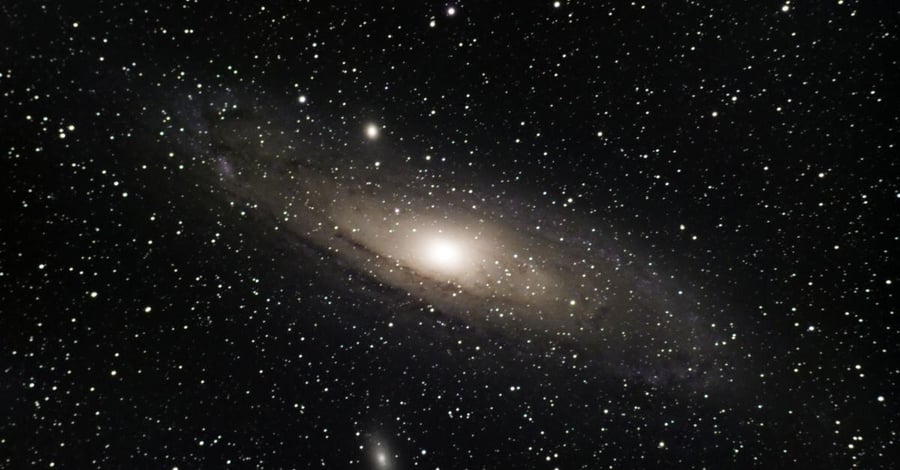
Manufactured with Speed and Precision
The manufacturing capabilities you need and the engineering support you want, all from a single partner.
Submit a DesignKey Points
- Space-grade EMI shielding materials are evolving to meet the increasing demands of modern spacecraft with higher emphasis on weight reduction, radiation resistance, and thermal management.
- New composite materials and multi-functional shielding solutions are transforming how engineers approach EMI protection in space environments.
- Miniaturization trends in satellite technology require more advanced and compact shielding solutions that don't compromise on performance.
- Space radiation effects pose unique challenges that require specialized EMI shielding materials with dual-purpose functionality.
- The growing commercial space sector is driving innovation in cost-effective yet reliable shielding solutions that can withstand the harsh conditions of space.
In the challenging environment of space, electromagnetic radiation permeates every cubic meter while temperature swings hundreds of degrees between sunlight and shadow. Here, protecting sensitive electronic components from interference becomes a matter of mission survival.
Modern spacecraft carry increasingly sophisticated electronics packed into tighter spaces, driving rapid evolution in space-grade EMI shielding materials in space. Engineers designing today's missions must implement innovative shielding solutions that can handle the triple threat of harsh radiation, extreme thermal cycling, and vacuum conditions while ensuring electromagnetic compatibility between densely-packed systems that simply cannot fail.
Let's explore the critical requirements and emerging innovations that are reshaping how aerospace engineers approach EMI protection in the unique challenges of the space environment.
-- Article Continues Below --
Learn everything you need to know about EMI Shielding.
The Evolving Landscape of Space-Grade EMI Shielding Materials
EMI shielding materials in space have undergone significant evolution in recent years, driven by the changing demands of modern spacecraft and satellite technology. The traditional approach of using heavy metal enclosures is being replaced by more sophisticated, multi-functional solutions that address multiple challenges simultaneously.
Space radiation, thermal cycling, vacuum conditions, and weight constraints all present unique challenges that terrestrial EMI shielding solutions simply cannot address effectively. Modern space-grade EMI shielding materials must perform reliably in these extreme conditions while meeting strict outgassing requirements and providing long-term stability over mission lifetimes that can span decades.
The integration of new space materials science advancements with traditional shielding approaches is creating a new generation of space-grade EMI shielding materials that offer superior performance-to-weight ratios. This evolution is essential as the space industry continues to push the boundaries of what's possible in orbit and beyond.
Critical Requirements for Space-Grade EMI Shielding Materials
When selecting EMI shielding for space mission applications, several critical requirements must be considered that go well beyond those for terrestrial applications. These specifications ensure that space-grade EMI shielding materials will perform reliably throughout the mission lifecycle.
The most essential requirements for space-grade EMI shielding materials include:
- Low outgassing properties (must meet ASTM E595 standards)
- Radiation resistance to withstand cosmic rays and solar radiation
- Thermal stability across extreme temperature ranges (-150°C to +150°C)
- Minimal weight contribution to overall spacecraft mass
- Long-term reliability without maintenance for mission durations
- Galvanic compatibility with spacecraft structures
- Vibration and shock resistance during launch and deployment
These requirements create a significant engineering challenge, as improving one characteristic often comes at the expense of another. The most successful space-grade EMI shielding materials achieve a careful balance across all these parameters, often through innovative new material combinations and manufacturing techniques.
Trend 1: Lightweight Composite Shielding Solutions
One of the most significant trends in space-grade EMI shielding materials is the move toward lightweight composite solutions that provide effective shielding without the mass penalty of traditional metal enclosures. Weight is a premium consideration in spacecraft design, with launch costs averaging $10,000 per pound to orbit.
Engineered composites combining carbon fibers, metallic nanoparticles, and specialized polymers are creating new possibilities for space-grade EMI shielding materials. These advanced composites can provide shielding effectiveness comparable to solid metal while weighing 40-60% less.
Carbon nanotube (CNT) reinforced polymers represent one of the most promising developments in this area, offering excellent conductivity and strength with minimal weight. When properly formulated, these materials can provide 60-80 dB of shielding across a wide frequency range while maintaining structural integrity in the space environment.
The integration of these composite materials into spacecraft design requires close collaboration between materials scientists and systems engineers to ensure optimal performance across all operating conditions. As manufacturing techniques improve, we can expect to see even lighter and more effective space-grade EMI shielding materials emerge.
Trend 2: Multi-Functional Shielding Materials
Modern spacecraft design increasingly favors multi-functional materials that can address multiple challenges simultaneously. This approach is particularly evident in the development of space-grade EMI shielding materials that offer additional protective properties beyond electromagnetic interference control.
Today's advanced space-grade EMI shielding materials often provide:
- Thermal management capabilities through integrated heat spreading
- Radiation shielding against charged particles and cosmic rays
- Micrometeoroid protection to prevent physical damage
- Structural support to enhance the mechanical properties of enclosures
- Static discharge mitigation to prevent charge buildup
This integration of functions creates a more efficient use of the limited mass and volume available in spacecraft. For example, aluminum-silicon carbide composites provide excellent EMI shielding while efficiently conducting heat away from sensitive components, eliminating the need for separate thermal management systems.
The development of these multi-functional space-grade EMI shielding materials represents a significant advance in spacecraft design philosophy, moving away from single-purpose components toward integrated solutions that maximize performance across multiple parameters.
Trend 3: Nanomaterial-Enhanced Shielding
Nanotechnology is revolutionizing space-grade EMI shielding materials by enabling unprecedented combinations of properties at the molecular level. These advanced materials leverage the unique characteristics of nanoscale structures to provide superior shielding with minimal mass.
Nanomaterial enhancements to traditional space-grade EMI shielding materials include:
- Metal nanowire networks that create conductive paths with minimal material
- Graphene and graphene oxide sheets providing atomically thin conductive layers
- Metallic nanoparticle fillers in specialized polymers for tunable conductivity
- Core-shell nanostructures that optimize both magnetic and electric field shielding
- Nanolaminates creating multiple reflection interfaces for improved attenuation
The addition of silver nanowires to conventional silicone EMI gaskets, for example, can increase shielding effectiveness by 15-20 dB while maintaining the gasket's flexibility and compression properties. Similarly, graphene-enhanced coatings can provide effective shielding at thicknesses measured in microns rather than millimeters.
These nanomaterial-enhanced space-grade EMI shielding materials are proving particularly valuable for protecting sensitive optical and quantum components that require exceptional shielding in extremely limited spaces. As manufacturing capabilities advance, we expect to see even more sophisticated nano-engineered shielding solutions entering the space market.
Visit the full resource center here
Trend 4: Adaptive and Tunable Shielding Systems
The next generation of space-grade EMI shielding materials includes adaptive systems that can respond dynamically to changing environmental conditions and electromagnetic threats. These intelligent shielding solutions represent a significant departure from traditional passive approaches.
Adaptive space-grade EMI shielding materials incorporate:
- Phase-change materials that modify their properties in response to temperature
- Metamaterials with tunable electromagnetic properties
- Electroactive polymers that change conductivity when voltage is applied
- Responsive nanocomposites that adapt to different frequency threats
- Self-healing materials that maintain shielding integrity after micrometeoroid impacts
These adaptive materials are particularly valuable for spacecraft operating in varied orbital environments or during long-duration missions where conditions change significantly over time. For example, shielding that can adjust its properties during solar storm events provides an extra margin of protection when it's most needed.
While still emerging, these adaptive space-grade EMI shielding materials show tremendous potential for enhancing the reliability and resilience of spacecraft electronics in unpredictable space environments. The integration of sensor networks with these materials creates truly intelligent shielding systems that optimize protection in real-time.
Trend 5: Specialized Coatings and Surface Treatments
Advanced coatings and surface treatments are transforming how space-grade EMI shielding materials are applied to spacecraft components. These specialized solutions can provide effective shielding without the bulk and weight of traditional approaches, particularly for complex geometries or retrofit applications.
Modern coating technologies for space-grade EMI shielding materials include:
- Atomic Layer Deposition (ALD) creating ultra-thin conductive films
- Magnetron sputtered metallic layers with precise thickness control
- Conductive ceramic sprays that withstand extreme temperatures
- Vacuum-deposited metal-matrix composites optimized for space environments
- Electroless plating techniques for complex three-dimensional surfaces
These coating approaches allow for the application of space-grade EMI shielding materials to surfaces and components that would be difficult or impossible to shield using traditional methods. For example, transparent conductive oxides can provide EMI shielding for optical windows and solar cells without significantly reducing light transmission.
The precision available with modern coating technologies enables engineers to apply exactly the right amount of shielding material exactly where it's needed, optimizing both performance and weight. This targeted approach is particularly valuable in weight-sensitive applications like cubesats and small satellites.
Trend 6: Radiation-Hardened EMI Shielding
The harsh radiation environment of space presents unique challenges for EMI shielding that terrestrial applications don't face. Modern space-grade EMI shielding materials are increasingly designed with radiation hardening in mind, creating dual-purpose protection against both electromagnetic interference and radiation effects.
Radiation-hardened space-grade EMI shielding materials typically incorporate:
- High-Z materials (like tungsten or tantalum) for stopping high-energy particles
- Boron compounds for neutron absorption
- Hydrogen-rich polymers for efficient proton stopping
- Graded-Z structures that optimize shielding across different radiation types
- Scintillation materials that convert harmful radiation to harmless light
This integration of radiation shielding with EMI protection addresses multiple threats simultaneously while reducing overall system mass. For example, tungsten-filled silicones can provide both excellent EMI shielding and protection against ionizing radiation, particularly valuable for missions beyond Earth's magnetosphere.
As spacecraft venture deeper into space and encounter more severe radiation environments, these specialized space-grade EMI shielding materials will become increasingly important for ensuring mission success and longevity.
Trend 7: Advanced Gasket and Seal Technologies
EMI gaskets and seals represent a critical vulnerability in spacecraft shielding systems, as they must maintain both electromagnetic and environmental sealing while accommodating thermal expansion, vibration, and mechanical stress. Advanced space-grade EMI shielding materials for gaskets are addressing these challenges through innovative compositions and designs.
Modern space-grade EMI shielding gaskets feature:
- Particle-filled silicones with specialized conductive fillers
- Knitted wire mesh in elastomeric carriers for superior compression recovery
- Form-in-place (FIP) gasket materials for complex geometries
- Wire-oriented elastomers with anisotropic conductivity
- Hybrid gasket designs combining multiple materials for optimized performance
These advanced gasket technologies ensure that the interfaces between spacecraft components – often the weakest points in EMI shielding systems – maintain their integrity throughout the mission lifecycle. Custom-engineered space-grade EMI shielding materials can be tailored to specific interface requirements, balancing conductivity, compression force, and environmental sealing.
The development of these specialized gasket solutions reflects the aerospace industry's recognition that system-level EMI protection is only as strong as its weakest link. By focusing on these critical interface components, engineers can significantly enhance overall shielding effectiveness without redesigning entire systems.
Material Comparison: Traditional vs. Emerging Space-Grade EMI Shielding Materials
Understanding the relative advantages of different space-grade EMI shielding materials helps engineers make informed decisions for specific applications. The following table compares traditional and emerging shielding options across key performance parameters:
Material Type | Shielding Effectiveness | Weight Impact | Radiation Resistance | Temperature Range | Manufacturing Complexity | Relative Cost |
Aluminum Sheet | 60-90 dB | High | Moderate | -150°C to +150°C | Low | Low |
Nickel-Graphite Silicone | 80-100 dB | Moderate | Moderate | -65°C to +125°C | Moderate | Moderate |
Carbon Fiber Composite | 40-70 dB | Very Low | Low | -100°C to +120°C | High | Moderate |
Metal-Plated Plastic | 60-80 dB | Low | Low | -50°C to +85°C | Moderate | Low |
Graphene-Enhanced Polymer | 70-90 dB | Very Low | Moderate | -80°C to +120°C | High | High |
MuMetal Foil | 90-110 dB | High | Low | -269°C to +400°C | Moderate | High |
Silver-Glass Silicone | 100-120 dB | Moderate | High | -65°C to +200°C | Moderate | Very High |
Nanowire Network | 60-80 dB | Minimal | Moderate | -100°C to +150°C | Very High | High |
This comparison highlights how newer space-grade EMI shielding materials often offer strategic advantages in specific parameters, though traditional materials still excel in certain applications. The selection process must carefully weigh these tradeoffs against mission requirements and constraints.
Modern spacecraft design typically employs a combination of these space-grade EMI shielding materials, with traditional options used where their specific properties are most valuable and newer materials applied where weight savings or specialized performance is critical. This hybrid approach optimizes overall system performance while managing costs and manufacturing complexity.
Challenges in Testing and Qualification
The qualification of space-grade EMI shielding materials for flight presents unique challenges that go beyond standard terrestrial testing protocols. Ensuring these materials will perform as expected throughout a mission requires specialized testing that replicates the unique conditions of space.
Critical testing challenges for space-grade EMI shielding materials include:
- Combined environmental testing (vacuum, temperature, radiation simultaneously)
- Accelerated aging to predict performance over mission lifetime
- Vibration and acoustic testing at launch loads
- Atomic oxygen exposure for LEO applications
- Thermal cycling across extreme temperature ranges
- Particle radiation exposure at mission-specific levels and types
These rigorous testing requirements ensure that space-grade EMI shielding materials will maintain their protective capabilities throughout the mission lifecycle. Testing protocols must be tailored to specific mission profiles, as the environmental challenges faced by a lunar lander differ significantly from those of a communications satellite in geostationary orbit.
The qualification process represents a significant investment for developers of new space-grade EMI shielding materials, but is essential for building confidence in their reliability for mission-critical applications. Standardized testing procedures help designers compare different shielding options on an equal basis.
The Impact of Commercial Space on Shielding Innovation
The rapid growth of commercial space ventures is significantly influencing the development of space-grade EMI shielding materials. The unique priorities and constraints of commercial operators are driving innovation in different directions compared to traditional government-led space programs.
Commercial space companies are pushing innovation in space-grade EMI shielding materials through:
- Higher production volumes enabling economies of scale for specialized materials
- Rapid iteration cycles allowing faster materials development and qualification
- Vertical integration of material development and application
- Risk-tolerant approaches that enable testing of novel solutions
- Cost-sensitive designs that emphasize performance-to-price ratio
This commercial influence has accelerated the development and adoption of advanced space-grade EMI shielding materials across the industry. For example, reusable launch vehicles have driven the development of shielding solutions that can withstand repeated thermal cycling and reentry stresses, while mega-constellation satellites have created demand for mass-producible, lightweight shielding systems.
The commercial sector's influence has lowered barriers to entry for innovative material suppliers and created new pathways for bringing advanced space-grade EMI shielding materials from laboratory concepts to flight-qualified products. This ecosystem is accelerating the pace of innovation and expanding the range of available shielding options for all space applications.
Practical Considerations for Aerospace Engineers
When you're tasked with selecting and implementing space-grade EMI shielding materials, the decisions you make directly impact mission success. At Modus, we've learned that practical considerations early in the design process can make the difference between a successful mission and a costly failure.
What’s the cost of poor quality, you ask? Learn more here.
Engineers working on aerospace applications face unique challenges that require specialized expertise and materials. Let's look at the crucial considerations that should guide your decision-making:
- Define EMI/EMC requirements thoroughly based on your system's specific sensitivities and the anticipated threat environment it will face
- Involve shielding experts early in your design process rather than treating it as an afterthought that needs to be addressed later
- Consider the complete lifecycle of your components, from pre-launch testing through deployment, operations, and end-of-life
- Test with flight-like hardware whenever possible, as engineering models may not accurately represent final EMI characteristics
- Build margin into your shielding designs to accommodate unknown variables and potential mission extensions
- Document all material properties and qualifications meticulously for future reference and validation
We've found that aerospace engineers who partner with manufacturing experts early in the design process consistently achieve better results. Working with a partner who understands the unique demands of space applications means you can identify opportunities to integrate shielding functions with structural, thermal, or radiation protection elements – potentially reducing overall system mass and complexity.
This systems engineering approach to EMI shielding yields significantly better results than treating shielding as an isolated subsystem bolted on at the end of the design process. When lives and missions depend on your components performing flawlessly in the harshest environment known to mankind, every detail matters.
Design Guidelines for Implementing Advanced Shielding
The difference between adequate EMI shielding and exceptional protection often comes down to implementation. Our engineering team has helped countless aerospace partners implement effective shielding solutions by following design guidelines that leverage each material's unique properties while accommodating their limitations.
When implementing space-grade EMI shielding materials, follow these critical design guidelines:
- Maintain electrical continuity across all shield interfaces and penetrations to prevent RF leakage
- Design gasket grooves appropriately for your specific gasket material's compression requirements and recovery characteristics
- Provide adequate grounding points that account for thermal expansion differentials in the harsh space environment
- Plan for outgassing directionality to prevent contamination of sensitive optical or electronic surfaces
- Ensure accessibility for verification testing of installed shielding components before final assembly
- Document all assumptions about shielding material performance for future reference and troubleshooting
We've seen how compartmentalization of sensitive electronics behind multiple shielding layers provides defense in depth, with each layer addressing specific frequency ranges or interference sources. This approach is particularly valuable for complex systems with multiple potential interference paths.
Essential Guide to EMI Shielding: Get it Here
EMI Shielding for Deep Space Missions
Deep space missions present the most extreme challenges for space-grade EMI shielding materials, with radiation levels, thermal conditions, and mission durations that push well beyond the requirements of Earth-orbiting spacecraft. These missions require specialized shielding approaches tailored to their unique operating environments.
Special considerations for deep space EMI shielding include:
- Enhanced radiation hardening for operation outside Earth's magnetosphere
- Extremely long service life requirements (often 10+ years)
- Operation at cryogenic temperatures for outer planet missions
- Extremely high temperatures for inner solar system exploration
- Limited communications bandwidth increasing autonomy requirements
- One-time deployment with no possibility for repair or adjustment
These extreme requirements drive the selection of space-grade EMI shielding materials toward the most robust and reliable options, often favoring flight-proven technologies over newer alternatives despite potential performance advantages. The risk calculation shifts significantly when a mission represents a once-in-a-generation opportunity.
The unique radiation spectrum encountered in deep space, particularly the high-energy galactic cosmic rays, may require shielding approaches that differ significantly from those used in Earth orbit. Combined EMI and radiation shielding becomes particularly valuable in these applications.
Industry Standards and Specifications
The selection and implementation of space-grade EMI shielding materials is guided by a comprehensive framework of industry standards and specifications. Understanding these requirements is essential for ensuring compliance and performance in space applications.
Key standards relevant to space-grade EMI shielding materials include:
- MIL-STD-461G: Requirements for the Control of Electromagnetic Interference
- ASTM E595: Standard Test Method for Total Mass Loss and Collected Volatile Condensable Materials
- NASA-STD-6016: Standard Materials and Processes Requirements for Spacecraft
- ECSS-E-ST-20-07C: Space Engineering: Electromagnetic Compatibility
- MIL-DTL-83528: General Specification for Gasketing Material, Conductive, Shielding Gasket, Electronic
- NASA-STD-4003: Electrical Bonding for NASA Launch Vehicles, Spacecraft, Payloads, and Flight Equipment
These standards provide the framework for qualifying space-grade EMI shielding materials and verifying their performance in specific applications. They establish minimum requirements for shielding effectiveness, material properties, and environmental compatibility that ensure reliability in the space environment.
Compliance with these standards typically requires extensive testing and documentation, particularly for novel space-grade EMI shielding materials that don't have established flight heritage. Working with materials and manufacturing partners who understand these requirements can significantly streamline the qualification process.
Choosing a Manufacturing Partner for EMI Shielding
Selecting the right manufacturing partner for space-grade EMI shielding materials is as important as choosing the right materials themselves. The complex nature of space-qualified materials and the stringent quality requirements demand specialized expertise and capabilities.
When evaluating manufacturing partners for space-grade EMI shielding materials, look for:
- Space heritage and flight-proven experience with similar applications
- Comprehensive quality systems with AS9100 certification
- Clean room manufacturing capabilities (when required)
- Materials engineering expertise specific to EMI shielding
- Established relationships with material suppliers
- Design for manufacturability support
- Strong documentation and traceability systems
The ideal partner brings both materials expertise and practical manufacturing knowledge to help optimize designs for both performance and producibility. Early involvement of manufacturing engineers can identify potential issues before they become costly problems during production.
Working with a vertically integrated partner who can handle multiple aspects of the manufacturing process – from material selection through final assembly and testing – reduces complexity and risk in the supply chain. This approach also typically leads to shorter lead times and better quality control across interfaces.
Partner with Modus Advanced for Space-Grade EMI Shielding Excellence
At Modus Advanced, we understand that when it comes to space applications, there's no room for compromise on quality or performance. Our team of specialized engineers works directly with aerospace customers to develop custom space-grade EMI shielding materials and solutions that meet the unique demands of the space environment.
Our vertical integration capabilities allow us to support your project from initial design concept through material selection, prototyping, testing, and production. With AS9100 and ISO 9001 certifications, ITAR compliance, and a commitment to meeting the most stringent outgassing and performance requirements, we provide the expertise and quality assurance that space missions demand.
We don't just manufacture parts – we help create technologies that protect sensitive systems in the harshest environment known to mankind. With our engineering-first approach and dedication to quality, Modus Advanced is your obvious choice for space-grade EMI shielding materials and solutions that perform when failure is not an option.
Contact our team today to discuss your specific space EMI shielding requirements and discover how our expertise can help ensure your mission's success.