EMI Shielding Materials Guide
March 8, 2021
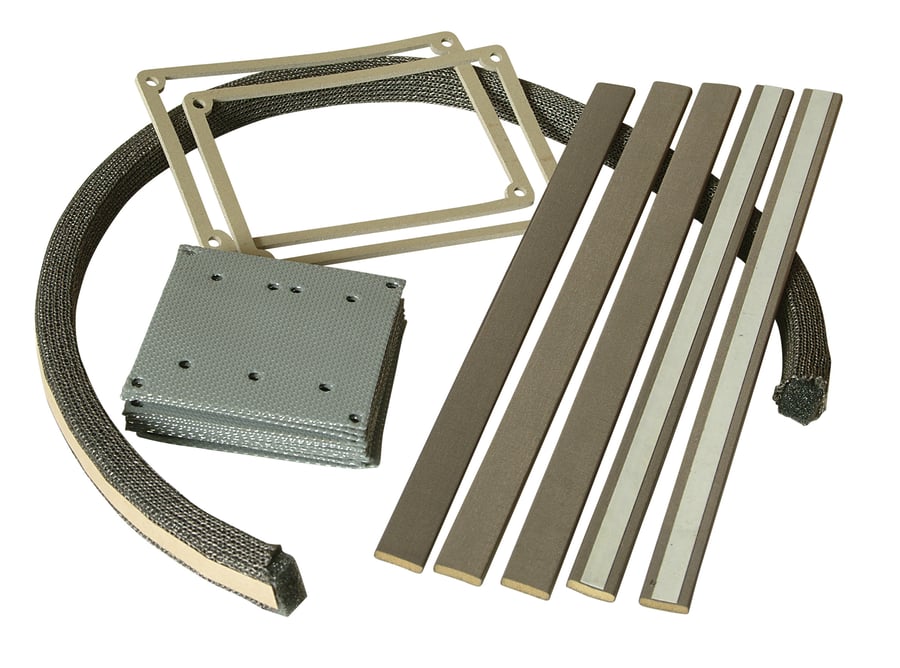
Manufactured with Speed and Precision
The manufacturing capabilities you need and the engineering support you want, all from a single partner.
Submit a DesignKey Points
- Material selection is critical for EMI shielding gaskets, influencing performance and compatibility with design requirements during the design phase.
- Filler choice significantly impacts cost and effectiveness; options include silver, nickel graphite, and others, each with unique properties and price points.
- Design considerations such as wall dimensions and compression stops are essential for ensuring consistent gasket application and optimal sealing performance.
Designing an Electromagnetic interference (EMI) shielding gasket is no easy task. You have plenty of requirements to keep in mind, and the materials you have to choose from have a very wide range of uses and costs. Selecting your material during the design phase is especially important to avoid any issues in which your design is not compatible with the ultimate material chosen to build your EMI shielding gasket.
Electromagnetic interference (EMI) and radio frequency interference (RFI) are significant concerns in many industries, necessitating effective EMI materials for shielding. These materials help prevent electromagnetic waves from interfering with sensitive electronic equipment.
Visit our complete EMI shielding resource center.
The most important questions you’ll need to ask yourself when selecting an EMI shielding material are:
Answering these questions during the design phase will help you select the right category of materials that will meet your EMI shielding requirements and allow you to incorporate important factors about that material into your design process.
There are many different EMI shielding materials to choose from when building your custom gasket, each with different properties and tolerances to choose from. These can include EMI silicone gaskets, molded EMI gaskets, and even cold bonded EMI gaskets or hot spliced EMI gaskets for specific applications.
Some of the most common categories of materials for making EMI shielding gaskets and general guidelines for when they may be a fit are detailed below.
Please keep in mind this article is meant to provide general guidance, and there are many materials with different properties and specifications to choose from within each category. Narrowing down to your final gasket material is something best done with the help of an expert. This guide is designed to help you start the process of EMI gasket material selection, before diving into the nitty gritty details.
The primary categories for EMI materials are:
In addition to these categories, some applications may require specialized solutions such as EMI filters or electrically conductive silicones to achieve optimal electromagnetic interference shielding.
EMI Shielding Gasket Design Questions
If you are in the design phase and still working on determining which EMI gasket material will work well with your design, and the other components in your design, then running through the following questions will be helpful for you.
What type of filler do I need?
Determining which metal filler you’ll want to use is a large part of the EMI gasket material selection process. Different fillers can have very big impacts on the overall material cost, and can be a huge factor in driving design decisions.
Your filler options will be different, depending on if you are looking at rubber-based materials or solids, form-in-place materials, foam materials, or fabric over foam solution. Some fillers will be available in each category and others will not, so make sure to take a look at each of the material categories listed later in this article to dive deeper into which fillers are available for each type.
In general, your filler options are:
- Silver
- Silver aluminum
- Silver nickel
- Silver copper
- Nickel graphite
The cost of the material you might need for your design is based heavily on which filler you need. Silver will be the most expensive and nickel graphite the least expensive. Which filler you require will be based on your application, other components in your design, and potential issues with galvanic compatibility.
Often, because of the large differences in price, your requirements for a filler may help determine the best manufacturing process to use to create your EMI shielding gasket. For instance, if you are using silver, material waste will be a huge concern because it will drive your cost per part up significantly if there are large amounts of highly expensive material that go unused.
Is galvanic compatibility a concern?
Galvanic corrosion happens when there is an exchange of electrons between two metals that have come into contact. Galvanic corrosion is accelerated when in the presence of electrolytes, but even dry air has moisture, which is enough to cause some level of corrosion. Your goal would be to select an EMI shielding material which will not cause galvanic corrosion when in contact with your housing.
If your gasket will be operating in an environment in which electrolytes will be present, you'll want to carefully select the filler you use to be compatible with any metal used on the housing of your part.
Typically the critical concern is galvanic corrosion between the part's substrate material, which comes into contact with the EMI gasket. The goal would be to select a filler material that does not corrode the metal of the housing.
Using a galvanic compatibility chart, like the one above allows you to select filler metals that will not cause corrosion in the housing.
If you are bonding to plastic housing, you can usually expect to coat the housing with metal, and thus will want to ensure there are no galvanic compatibility issues between the metal used in coating the housing and the filler you choose. In some cases, an RTV silicone adhesive might be used to bond the gasket to the housing.
What are your shielding effectiveness requirements?
An additional consideration is if you must adhere to shielding effectiveness requirements. Shielding effectiveness is a measure of how well a given part reflects or absorbs electromagnetic radiation.
Often in military applications, you will be required to meet MIL-STD-285, the military standard for electromagnetic shielding. This standard helps ensure that your EMI gasket design effectively prevents EMI leakage and provides adequate protection against electromagnetic interference (EMI).
When designing your EMI shielding solution, it's important to consider not only the gasket material but also other factors such as thermal insulation requirements and the overall effectiveness of your electromagnetic interference shielding strategy.
Designing an Electromagnetic interference (EMI) shielding gasket is no easy task. You have plenty of requirements to keep in mind, and the materials you have to choose from have a very wide range of uses and costs. Selecting your material during the design phase is especially important to avoid any issues in which your design is not compatible with the ultimate material chosen to build your EMI gasket.
The most important questions you’ll need to ask yourself when selecting an EMI shielding material are:
- What type of filler do I need?
- Is galvanic compatibility a concern?
- What are your shielding effectiveness requirements?
Answering these questions during the design phase will help you select the right category of materials that will meet your EMI shielding requirements and allow you to incorporate important factors about that material into your design process.
There are many different EMI shielding materials to choose from when building your custom gasket, each with different properties and tolerances to choose from.
Some of the most common categories of materials for making EMI gaskets and general guidelines for when they may be a fit are detailed below.
Please keep in mind this article is meant to provide general guidance, and there are many materials with different properties and specifications to choose from within each category. Narrowing down to your final gasket material is something best done with the help of an expert . This guide is designed to help you start the process of EMI gasket material selection, before diving into the nitty gritty details.
The primary categories for EMI materials are:
- Form-in-Place (FIP) (CNC Dispensed)
- Rubber-Based Sheet or Roll Materials
- Fabric Over Foam
- Beryllium Copper
Below you will find general information about each general category of EMI shielding material, when it might be a good fit, and some examples of material suppliers for reference.
Form-in-Place (FIP)
Choosing form-in-place (FIP) dispensing for your gasket is based upon the size, shape, and complexity of your gasket. Form in place (FIP) materials are best fit when you have a very small gasket that would be difficult to die cut and then assemble in your production facility. Very small and thin gaskets are flimsy and difficult to manage, increasing the effort and time that must go into assembly. This is more and more common due to the smaller form factors and space constraints in today’s electronic assemblies.
As such, FIP gaskets are usually selected in an effort to reduce the cost of assembly in these instances. Because the gasket is dispensed directly on the unit, then cured, before being sent back to your production facility, it saves a step (and money) on the assembly process.
In addition, when using custom gaskets for EMI applications, choosing FIP as the method for production can limit waste, thus reducing cost on more expensive materials. Because of their typical size, FIP materials are commonly used to create an effective seal for electronic devices.
The base of a FIP EMI gasket is typically silicone, and the most common types of fillers that are used on form-in-place EMI shielding gaskets are nickel graphite and silver nickel.
Your design has a significant impact on which materials you will want to ultimately select for your application. Understanding what your bead size is, the ratio of bead size height and width, the ledges you’ll be dispensing on, and the presence of loopholes or grooves will help determine which material can meet your requirements.
Another common design consideration is whether or not your EMI gasket must also provide an environmental seal. If so, you may consider dual dispensing two separate FIP gasket materials, because conductive particle filled FIP materials are harder set and don’t provide the best long term environmental seal.
FIP gaskets in particular, are not intended to provide an environmental seal and, due to their metal content, can be adversely affected if exposed to the environment. If environmental sealing needs to be accomplished to protect the gasket, this can be accomplished with the addition of another type of gasket.
Some examples of common FIP EMI shielding materials are:
Visit our Form-in-Place Gasket Resource Center
Rubber-Based Materials
For solid materials, you’ll be looking at most of the same categories of materials for the base of your EMI shielding gasket as you would any other solid rubber-based gasket:
- Silicone
- Fluorosilicone
- EPDM
In deciding which of the base materials is right for your needs, take a look at the solid materials section of this article which goes into the benefits and drawbacks of each.
Once you’ve selected your base material, you’ll be choosing a filler material. You’ll end up with a conductive particle filled elastomer made to very strict specifications based on your needs. The fillers you have to choose from on solid rubber-based electromagnetic interference gaskets are:
- Silver
- Silver aluminum
- Silver nickel
- Silver copper
- Nickel graphite
The base material and filler combination you select will depend on the requirements your application has for shielding effectiveness, environmental sealing, reliability and durability. Conductive particle filled elastomers usually come in two major category grades: commercial grade and military grade.
Commercial grade shielding products are typically lower in both performance and price, while military grade materials are built to meet the stringent EMI shielding requirements of the MIL-DTL specifications.
Some examples of materials across all grades and options are:
- JABAR Series 800 Conductive Particle Filled Elastomers
- SSP Electrically Conductive Shielding Compounds
Foam and Fabric Over Foam Solutions
When softer compression forces are required for your design, then foam-based EMI shielding materials may be a fit for your needs. You are much more limited in both material and conductive filler options in this category of materials.
Rather than being filled with particles, foam-based materials are typically made by taking a polyurethane foam and then spraying the foam with copper or nickel. This metal plating will fill the pores of the foam and make it conductive.
Some materials use a fabric or wire mesh wrapped over a low closure force urethane foam to achieve a similar effect. Fabric over foam solutions typically come in various cross sections (like D-shaped, O-shaped, or C-shaped), with hundreds of different profile offerings.
Keep in mind that EMI materials rarely provide a good seal, particularly against water, so design requirements are a key factor in determining if a foam-based EMI shielding material is even possible to use in your application.
An example of one of the most commonly used foam-based EMI shielding materials is the Parker Chomerics Soft-Shield material family.
Beryllium Copper
Beryllium Copper (BeCu) can be fabricated into specific shapes, the most common we see in EMI shielding applications being “fingers.” A high performance metal, BeCu provides shielding over a broad range of frequencies and is a good fit when your design requires repeated opening and closing of an enclosure providing an improved compression set.
An example of this material is the JABAR Series 350 Beryllium Copper Shielding group of materials.
The Bottom Line
Easily the most difficult part of designing an EMI shielding gasket is selecting the material that will meet all of your design requirements, but it is far from the only design consideration. Make sure you review the 8 key factors you should consider when designing your custom gasket to get it right the first time.