EMI Shielding Gasket: The Best Application for Compression Molding
July 11, 2017
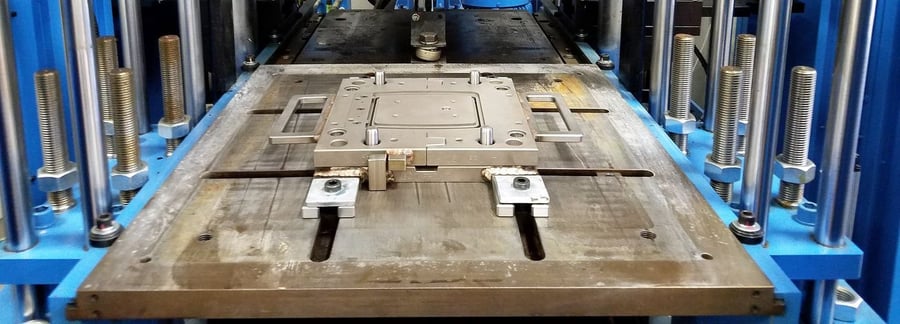
Manufactured with Speed and Precision
The manufacturing capabilities you need and the engineering support you want, all from a single partner.
Submit a DesignKey Points
- Compression molding is often the most cost-effective manufacturing method for EMI shielding gaskets, especially when using expensive conductive materials like silver-filled silicones.
- While other methods like die cutting, water jet cutting, and digital cutting are suitable for prototyping and lower volumes, compression molding minimizes material waste, a crucial factor when working with costly conductive materials.
- Compression molding excels at producing complex three-dimensional EMI gasket shapes with tight tolerances, while reducing the closure force required for metal-filled silicone materials.
- Molded EMI gaskets are particularly valuable for aerospace, defense, and other industries requiring high electrical conductivity levels only achievable with premium materials like silver-filled compounds.
- The initial investment in compression molding tooling may be higher than other methods, but the per-unit cost savings from minimal material waste makes it economical for higher volume production.
EMI gaskets can be fabricated through a variety of methods. The most common techniques tend to be die cutting and compression molding. Some excellent shielding gaskets, such as EMI O-rings, can be cut by hand and then cold-spliced or vulcanized. Water jet cutting and digital or die-less cutting are also used in EMI gasket fabrication. These methods are good choices for prototyping and lower-volume production because there’s no custom tooling.
No matter which gasket fabrication method is used, engineers want to maximize material yields and minimize tooling costs. They also need to select a manufacturing method that can meet application-specific requirements for a connector gasket shape, size, and production quantities.
Molding is just one of many options for EMI shielding gaskets, but is it the right choice for what you need?
How Molding Works
There are many different molding techniques, but compression molding is probably the most commonly used method for molding an EMI shielding gasket. Compression molding is a production process that uses heat and pressure to shape a pliable raw material into a finished product.
Typically, the mold is made of steel or aluminum and contains machined cavities. The uncured conductive silicone or raw material is inserted in the mold cavities in a putty-like state, and after 7-10 minutes cures to a finished rubber like material. The shape and size of the molding cavity determines the final form of the EMI gasket material. Compression molding supports the manufacture of small parts as well as larger EMI gaskets in addition to accommodating precise gasket details for intricate and complex gasket designs.
After the EMI silicone is cured, the mold is opened and the parts are removed from the mold. Compression molding wastes little material, and this manufacturing method is suitable for mass production.
Why Material Waste Matters
With particle filled, conductive silicones, material waste matters because these elastomeric compounds can be expensive. Shielding silicones that contain silver or silver-coated particles are also subject to price fluctuations in the precious metals market. Nickel-graphite silicones cost less, but successful companies are always looking for ways to avoid waste that inevitably increases costs.
Not every RFI shielding application supports a non-silver substitution, however. In the defense and aerospace industries especially, an EMI gasket may require a level of electrical conductivity that only silver can provide. Therefore, in order to remain competitive when using these expensive materials, defense contractors, aerospace companies, and other buyers of EMI shielding gaskets are very conscious of shielding material waste. For companies in these and other industries, molding can be the most cost-effective gasket fabrication technique.
Visit our complete EMI shielding resource center.
Where Molded EMI Gaskets Add Value
Depending on your production quantities, molded EMI gaskets can provide a significant per-unit cost savings over manufacturing methods such as die cutting. A metal mold may cost more than a die, but there’s less material waste. Die cut parts can be nested to maximize material yields, but there’s still unused material between parts. Additionally, there is always leftover material around a sheet’s edges.
Image: EMI Shielding Gasket Mold
Per-gasket costs are important, but designers can’t afford a manufacturing method that won’t meet application requirements for shape and complexity. Sometimes, bezel gaskets are molded to avoid wasting sheet material in the middle of these “picture frame” parts. Bezel gaskets support compression molding, but these flat gaskets aren’t especially complex. For three-dimensional (3D) shapes and intricate parts, compression molding is also an excellent choice, and sometimes the only choice.
Image: Compression Mold Press
Compression molding can produce 3D EMI gaskets with tight tolerances. Importantly, these custom conductive shapes can reduce the amount of closure force that’s required for metal-filled materials such as silver, silver-aluminum, or nickel-graphite silicones. Other gasket fabrication methods have their advantages, but engineers and sourcing managers who compare their gasket design requirements to the advantages of using a molding process may decide that compression molded EMI gaskets are their best choice.
For more information about molded EMI gaskets, contact Modus Advanced.
Our 4 step Idea to Igniton™ process allows Modus to strategically plan, manufacture and deliver exactly what you need, while staying agile enough to ship over 99% of orders on time. Learn more by viewing our infographic below!