The Top 4 EMI Shielding Gasket Manufacturing Processes
June 7, 2017
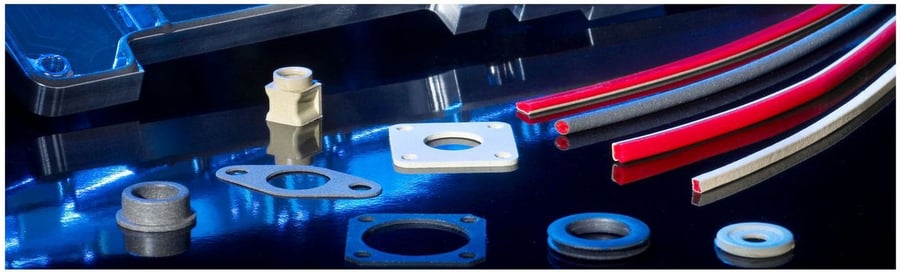
Manufactured with Speed and Precision
The manufacturing capabilities you need and the engineering support you want, all from a single partner.
Submit a DesignKey Points
- Die cutting offers precision, repeatability, and quick turnaround for EMI shielding gaskets with high shielding effectiveness and optional adhesive backing.
- Extruded EMI gaskets are ideal for flange and groove applications, with the benefit of efficient material usage through selective conductive layer placement.
- Custom molded EMI gaskets provide perfect 3D conformity to complex designs but require higher tooling costs and longer lead times.
- Form-in-Place (FIP) gaskets excel in complex electronic packaging with automated dispensing, reduced compression force, and elimination of manual placement.
- Working with an experienced gasket manufacturing partner helps engineers navigate material selection and manufacturing process options, ensuring the most reliable and cost-effective EMI shielding solution.
The purpose of EMI shielding gaskets are to protect and enhance the performance of electronic devices and equipment by creating a conductive path between two surfaces. The gaskets work to ensure the electrical conductivity required in your design is reliable and solid. Additionally, and maybe more important, they prevent the transmission of electromagnetic interference (EMI) disturbances which can disrupt or destroy electrical circuits. This article explores the top four EMI shielding gasket manufacturing methods.
The causes of EMI are numerous, but luckily so are your choices for EMI shielding materials and gasket fabrication methods. We're limiting the scope of our discussion in this article to enclosure gaskets typically used in all-metal housings. We will address EMI shielding gaskets used with plastic enclosures in a future blog.
While the all metal housing may offer the flexibility you need in your design, you will also want to consider the use of shielding silicones filled with metal-coated particles for EMI protection. These specialized elastomers can not only meet tough shielding requirements, but also provide environmental sealing as well. With early involvement of your gasket fabricator, gaskets can be manufactured to the exact shape and size needed for your design.
Four Forms of Gasket Fabrication
If your design supports the use of EMI silicones, you'll need to do more than choose the right EMI material. You'll also need to consider the relationship between form factors and gasket fabrication methods. Die cutting, spliced extrusion, custom molded rubber and Form-In-Place (FIP) each offer advantages, but which one of these four techniques is right for your application?
1. Die-Cutting
Your gasket manufacturer can die cut extremely precise gaskets out of EMI silicone. From 5 to 500,000 gaskets, once you have the exact specifications set, die cut ting is a great choice as a repeatable, quick solution with high shielding effectiveness.
Die cutting supports nested parts in addition to punched holes or slots with specific radii for fasteners required in your design. Die cut gaskets can also be supplied with a conductive pressure sensitive adhesive backing (PSA), eliminating the need for difficult to control liquid adhesives on the assembly line. Another benefit is the ability to kiss-cut which dramatically reduces the time it takes assembly personnel to peel the release liner off the PSA.
Probably the two biggest benefits to using die cut shielding gaskets are the worldwide availability and the shorter 2-4 week lead times. Die cut conductive silicone gaskets are easily procured from companies like Parker Chomerics, Laird and Nolato Silikonteknik. All three companies have manufacturing facilities or manufacturing partners in the USA, China, Malaysia, Europe and Mexico.
Visit our complete EMI shielding resource center.
2. Extruded EMI Shielding Gaskets
Image: Extruded EMI Shielding Gaskets (Courtesy of Nolato)
Extruded gaskets are ideal for flange and groove applications. There are a range of standard or semi-standard profiles available: solid O, hollow O, D, P, E, U, solid square, and hollow square available from the manufactures mentioned above. Both Laird and Nolato have helpful online tools available.
Image: Range of extruded gasket profiles (Courtesy of Nolato)
Should you find your project requires an unusual extruded gasket shape, your gasket manufacturer can work with you to customize a unique gasket shape which in some cases could also include innovative anti-stretch and press-fit features .
After extrusion and curing, the gaskets may be cut and spliced to your exact specifications creating full EMI rfi shielding enclosure seals. Splicing is typically done on a small molding press, but the extrusions can also be cold bonded or glued if needed.
The biggest benefit of using an extrusion is the efficient use of expensive rf shielding materials. EMI shielding extrusions can be made with a thin outer layer of conductive silicone, thereby significantly reducing the volume of silver or nickel graphite.
3. Molded EMI Shielding Gaskets
Instead of trying to make a die cut or extruded EMI gasket fit, why not create a custom molded EMI shielding gasket that perfectly conforms to your design requirements? Custom molding an EMI gasket material is an effective way to reduce cost by eliminating the center drop waste typically associated the die-cut process. Cost or budget is especially important when using electrically conductive silicone materials as those rfi shielding materials are more expensive than standard silicone gaskets.
Molded shielding gaskets can solve a number of issues die cut or extruded gaskets can't address. Probably the most obvious benefit to using a custom molded solution is the ability to conform to three dimensional designs not suitable for flat or extruded gaskets. As you can imagine, the flexibility in design comes at price. Make sure your budget allows for significant tooling costs as well as longer lead times.
Image: Molded EMI Shielding Gaskets (Courtesy of Nolato)
Another benefit to using a custom molded EMI shielding gasket is the speed and precision by which parts can be manufactured. The efficient molding process results in very little shielding material waste and can be automated in most cases, especially in volume applications.
4. Form-in-Place Gaskets (FIP)
Dispensed or Form-in-Place gaskets are another way to address EMI shielding. The FIP process dispenses a precise string of electrically conductive silicone directly onto the substrate. This type of gasket can result in 30% lower compression force, less material consumption, increased PCB area, in addition to excellent shielding properties.
When you consider the automated dispensing methods and efficient use of EMI material, Form-In-Place gaskets present an excellent solution for complex designs. Dispensing machines are programmed to place beads on thin gasket shelves thereby eliminating manual gasket placement and allowing for more compact designs.
A benefit of the FIP process is it easily accommodates densely populated electronic packaging where isolation and complex cross section patterns are required. Additional benefits include: superior flexibility for gap closure, there is no assembly needed, results in very little scrap material, and adhesive is not required.
Depending on volume, dispensed gasket solutions are available directly from Chomerics, Laird and Nolato worldwide. For smaller volumes or prototypes, all three manufacturers support specialized dispensing partners in a number of countries. To address consistency and quality concerns, Nolato even has a formal EMC Production Partner program .
One Solution
How can engineers possibly keep up with what's new in the industry? Well, that's where your gasket manufacturing partner comes into play. Process driven gasket manufacturers continually work with materials suppliers to be knowledgeable of the latest, greatest products on the market to meet the most innovative or difficult of designs.
Let their experienced team help guide you through your next project. They will help turn your "Idea into Ignition™" with the most reliable and appropriate shielding material needed for your EMI shielding project, and manufacture your seals using the most reliable, cost-effective manufacturing processes available. Let them take the risk out of the job of moving your project from the drawing or concept stage through full production.
Download the free Nolato Trishield product guide to discover everything you need to know about Nolato EMC & Thermal Solutions: