3 Reasons to Use Nickel-Graphite Silicones for EMI Shielding Gaskets
June 27, 2017
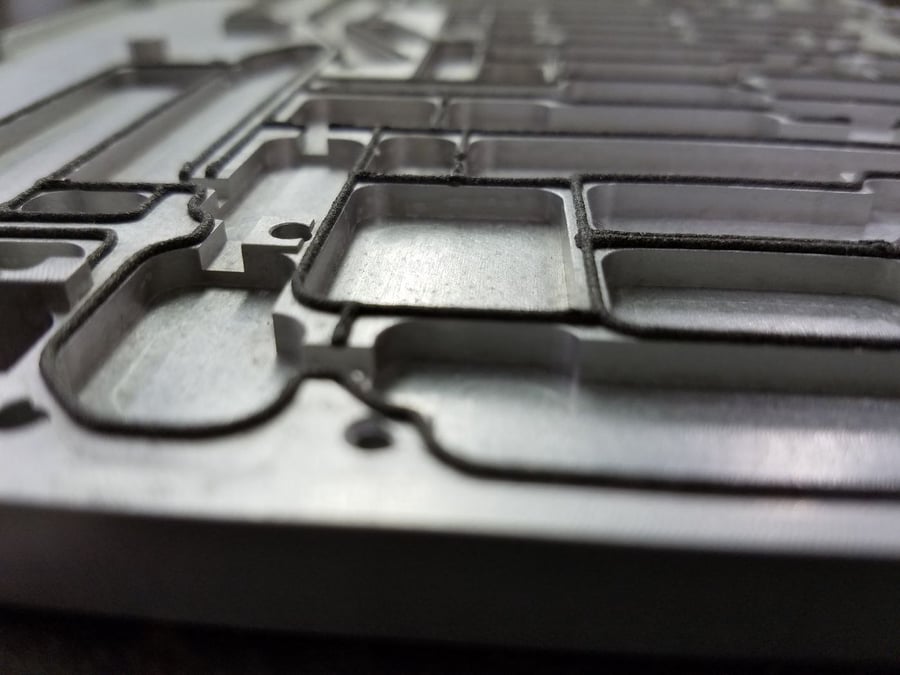
Manufactured with Speed and Precision
The manufacturing capabilities you need and the engineering support you want, all from a single partner.
Submit a DesignKey Points
- Nickel-graphite silicones offer significant cost advantages over silver-filled elastomers for EMI shielding gaskets, providing price stability that helps protect project budgets from precious metal price fluctuations.
- While silver provides the highest electrical conductivity, nickel-graphite silicones deliver sufficient shielding effectiveness (exceeding 100 dB) for many applications without the premium cost.
- Beyond cost and performance benefits, nickel-graphite silicones provide excellent material properties, including lower durometer options (30-45 Shore A) for better compressibility and superior corrosion resistance in high-humidity environments.
- Engineers can achieve optimal balance between cost, shielding performance, and material properties by selecting nickel-graphite silicones that match their specific application requirements rather than overspecifying with more expensive silver-based options.
Nickel-graphite silicones are cost-effective compounds that combine the advantages of silicone rubber with the electrical properties of nickel. They are fabricated into gaskets and installed between metal surfaces to provide limited environmental sealing, excellent electrical conductivity, and resistance against electromagnetic interference (EMI). Nickel-graphite silicones aren’t the only shielding elastomers for EMI gaskets, but they offer advantages over silicones that are filled with silver or silver-coated particles.
To determine whether nickel-graphite silicones are right for your sealing and shielding application, it’s important to evaluate all of your business and technical requirements.
Typically, there are three main factors to consider:
- Gasket Cost
- Shielding Performance
- Material Properties
Let’s take a look at each.
Gasket Cost
For years, silver-aluminum was the filler material of choice for EMI shielding gaskets. The U.S. military’s development of the MIL-DTL-83528 specification played an important role in this particle’s popularity. When silver began approaching $50 per Troy ounce in 2011, however, the fact that silver-aluminum silicones were specified on thousands of gasket drawings became problematic.
Today, engineers and sourcing managers can specify shielding silicones with a variety of particle fills. Nickel-graphite silicones cost significantly less than elastomers that contain silver or silver-aluminum particles. Nickel-graphite silicones also cost less than elastomers that are filled with silver-coated copper or glass particles.
Nickel-graphite silicones offer greater price stability than silver or silver-filled elastomers. Because silver is a precious metal, price fluctuations can be significant. If the price of silver skyrockets during a product’s life cycle, gasket pricing at end of the program may be significantly higher. This can lead to cost overruns and affect your ability to win future projects.
Shielding Performance
Choosing a less expensive shielding silicone can reduce project costs, but engineers need to ensure that EMI gaskets meet shielding requirements. Silver has the highest electrical conductivity of all metals and is extremely reliable as a shielding material. Yet not all applications require silver’s extreme conductivity. Some applications don’t even require the conductivity that’s associated with silver-coated particles.
The table below shows the relationship between filler type, electrical conductivity, and typical volume resistivity (VR) as measured in ohms per centimeter. Direct methods for measuring shielding effectiveness can be expensive and complex, so VR is a commonly-used method for the indirect measurement of EMI shielding effectiveness.
Table 2: Performance Comparisons
The next table contains results from a third-party test report for a nickel-graphite silicone. Note that all of the shielding effectiveness levels exceed 100 dB, which is the minimum standard in the MIL-DTL-83528 specification.
Table 3: Shielding Effectiveness Test Results
EMI gasket costs and shielding performance are critical, but engineers also need particle-filled silicones with material properties that support environmental sealing, manufacturability, and corrosion resistance.
Learn how Modus is redefining the traditional supplier relationship
Material Properties
Nickel-graphite silicones are available as lower-durometer (softer) materials with good tensile strength, elongation, and tear resistance. Durometer, a measure of hardness or softness, is an especially important property because it effects compressibility. If an EMI shielding gasket is too hard, sealing pressures can cause permanent deformation. The “leaks” that result can admit currents that disrupt electrical and electronic devices.
Softer nickel-graphite silicones are available in 30, 40, and 45 durometer (Shore A). Nickel-graphite silicones, in 65-durometer, can contain an inner layer of conductive fabric for applications where brittleness or tearing is a problem. When fluorosilicone is used as the base elastomer, both material hardness and chemical resistance increase.
Silicone rubber supports compressibility, environmental sealing, and manufacturability, but the metals in shielding silicones are still subject to corrosion. In environments with high relative humidity, moisture, or water, corrosion can cause the deterioration of metal and reduce the effectiveness of an EMI shield. Examples include medical electronics where EMI shielding products are subject to repeated cleaning, and marine applications where salt spray or salt fog are factors.
Galvanic coupling, a type of corrosion, occurs when two dissimilar metals come into electrical contact in the presence of an electrolyte (such as water). The natural oxidation characteristics of each metal are enhanced, and the metal that’s more easily oxidized experiences a higher corrosion rate than normal. For this reason, silicones with silver-aluminum particles can be problematic in corrosive environments. By contrast, nickel-graphite silicones provide corrosion resistance because they contain particles with a metal (nickel) and a non-metallic (graphite) material.
Nickel-graphite silicones can also pass the ASTM B 117 Salt Spray Test, an important measure of suitability for marine environments. This test, which is performed inside an automated salt spray chamber, clamps the EMI gasket between bare aluminum electrodes in order to simulate real-world conditions.
Visit our complete EMI shielding resource center.
Final Thoughts
Engineers and sourcing managers can select particle-filled silicones for conductive gasket applications that require environmental sealing, electrical conductivity, and protection against electromagnetic interference (EMI). Silver is the most electrically-conductivity metal, but it’s also relatively expensive – and may offer more shielding performance than you really need.
Nickel-graphite silicones provide a cost-effective alternative, but you’ll need to balance gasket costs not just against shielding, but against material properties such as compressibility, manufacturability, and corrosion resistance. By analyzing all your business and technical requirements, you can select the right EMI gasket material.
Our 4 step Idea to Igniton™ process allows Modus to strategically plan, manufacture and deliver exactly what you need, while staying agile enough to ship over 99% of orders on time. Learn more by viewing our infographic below!