Extrusions vs. Form-in-Place Gaskets
May 17, 2021
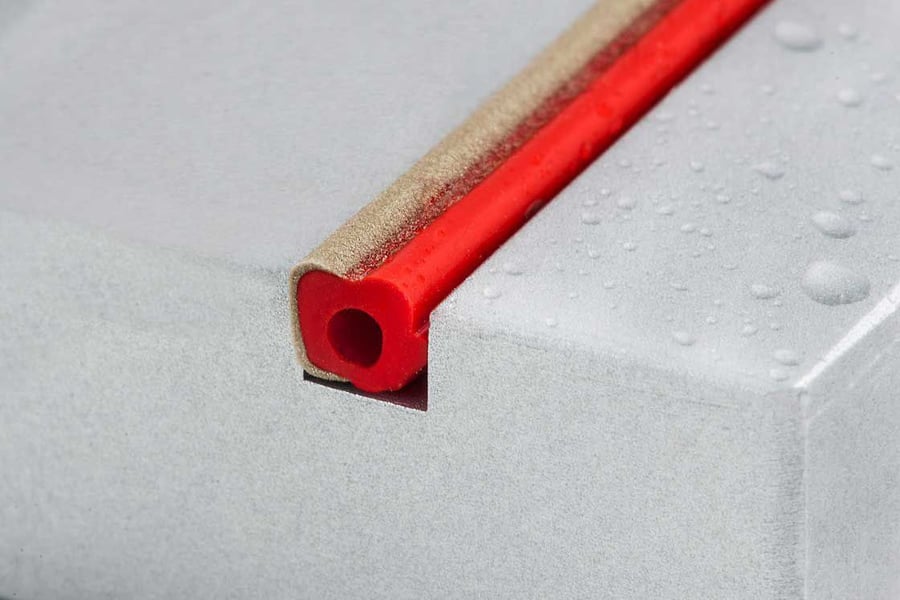
Manufactured with Speed and Precision
The manufacturing capabilities you need and the engineering support you want, all from a single partner.
Submit a DesignKey Points
- Choosing between extrusions and form-in-place (FIP) gaskets depends on specific design requirements and applications rather than having a one-size-fits-all solution.
- Reworkability is a major factor; extrusions work better for systems needing to be repeatedly opened and resealed, while FIP gaskets are ideal for permanent or rarely reopened assemblies.
- FIP gaskets excel at handling intricate gasket paths and complex designs where manual installation of extrusions would be challenging and time-consuming.
- Material requirements matter; some extrusions can provide both EMI shielding and environmental sealing, while FIP gaskets typically specialize in one or the other.
- Total cost considerations should include not just material costs but also assembly labor implications, as FIP gaskets reduce assembly steps despite potentially higher initial material costs.
Our engineering team is regularly asked for guidance in determining if an extrusion or a form-in-place (FIP) gasket is a better fit for a particular design. While each design is unique, and it is nearly impossible to answer definitively without looking at a design which will be the better fit, we figured that we could at least pull together our collective knowledge and provide guidance on what considerations might lead down one path or the other.
Visit the Modus Form-in-Place Gasket Resource Center
So this article is meant to help provide some insight into the thought process we put behind helping make this determination on a design by design basis. It is by no means exhaustive, and if you have questions about a specific design, then by all means submit your design and let our engineering team help you make a determination!
Differences Between Extrusions and FIP Gaskets
We’d be remiss if we didn’t provide a brief overview of both extrusions and FIP gaskets before jumping into all the considerations that make one a better fit than the other.
Extrusions
An extrusion is a flexible gasket that has an internal profile in a specific shape meant to fit the design. Some examples showing different internal profile shapes of extrusions are shown below:
In order to build a gasket that fits the requirements of a design, the extrusion must first be created by feeding it through a die (almost like creating a piece of spaghetti), and then cutting it to the appropriate length as required in the design.
Once the extrusion has been made, the two ends must be bonded together to create a closed system, and then fit into the design.
Form-in-Place Gaskets
A form-in-place gasket is created by dispensing a liquid gasket onto a metal or plastic part before assembly. Because it is dispensed as a liquid, it fits precisely to the part’s form, regardless of housing imperfections. This results in a reliable seal and durable finished product.
FIP gaskets are dispensed using CNC machines. The process is so precise that surfaces less than one millimeter wide can still receive FIP gasket application.
Considerations When Selecting Extrusions vs. FIP Gaskets
Below we walk through the most important considerations you should weigh when choosing between an extrusion or form-in-place gasket for your design.
The Gasket Application
The first thing you’ll want to consider is the application of the gasket itself. This breaks down into two categories:
- What are the reworkability requirements of the gasket?
- What do you need the gasket to do?
Reworkability
On one end of the spectrum, you’ll have gaskets that will be sealed into a design once and then never need the system opened again.
On the flip side, there are instances where housing may need to be opened or closed many times, essentially unsealing and resealing the system. In these cases, the gasket needs to provide a reliable seal every time the system is closed.
In systems where reworkability requirements are high (e.g. the system will need to be sealed and unsealed multiple times), extrusions are often the better fit.
Extrusions can more easily rebound in these situations, and it is much easier to replace an extrusion should the repeated sealing and unsealing cause it to fail to produce the necessary seal after wear and tear. An extrusion can be replaced without having to replace any other portion of the housing or part relatively easily and inexpensively.
By contrast, FIP gaskets will take a compression set when the gasket is first sealed in the housing. The longer the system is closed, the less likely a FIP gasket will be to “rebound” upon opening. In addition, because the gasket is adhered to the surface of the housing, replacing it would require sending the part out to a FIP dispenser to replace if needed.
In systems where reworkability isn’t really required (e.g. the system will not need to be unsealed and resealed frequently), form-in-place gaskets become a much more viable option.
Gasket Requirements
Another very important factor in determining if FIP or extrusions will be a fit for your need is the simple question of what your gasket needs to do.
Is your gasket simply providing an environmental seal? Does it need to provide EMI shielding or protection? Or does it need to do both?
In general, materials that need to both provide EMI shielding protection and an environmental seal will do an “ok” job at both, but not necessarily a great job at either. This makes it very important for you to determine which of the two goals is more important (e.g. the gasket needs to provide a moderate environmental seal but must do a great job shielding against EMI).
Materials for form-in-place gaskets can typically provide either EMI shielding protection or an environmental seal, but not both. Depending on your design, it may be possible to dispense two beads (one with an EMI shielding material composition and one meant for an environmental seal), but cases where this is possible are relatively rare.
Some extrusions are built to serve both EMI shielding and environmental sealing requirements, and maybe a good fit if you find yourself needing both.
Ideally, your gasket will only need to be serving one goal, rather than two, which allows you to build a gasket that does a great job of meeting that need. In this case, either a FIP gasket or extrusion is possible, and it will be significantly more effective at meeting that single goal.
Case Study: Redefining the traditional supplier relationship.
Intricacy or Complexity of the Gasket
The next consideration in the list is the complexity of the gasket path. The more intricate or complex the gasket path, the harder it will be to use an extrusion.
Take this part for instance:
The very narrow size of the gasket, the length of the full gasket path, and the sheer numbers of twists and turns in the housing would make this particular gasket a huge pain to achieve with anything other than a form-in-place gasket.
Having a tech assemble an extrusion into this housing manually would be very time consuming, and potentially end up with part failures if it wasn’t done exactly right. In addition, if the part were turned upside down, an extrusion could easily fall out, requiring re-assembly. A form-in-place gasket is actually adhered to the surface of the part, meaning it won’t move from its placement once cured.
So, in general, very small and complex gaskets are best fit to FIP. It is easier to achieve the final product and can significantly reduce labor costs.
Assembly Requirements
Depending upon the volume of parts you are producing, you may also want to weigh the considerations of assembly.
For small or complex gaskets, the previous section breaks down, in detail, the assembly issues that may be caused by using an extrusion.
For parts that are larger and less complex, this question just becomes one of weighing what is most important. Some factors to consider include:
- Extrusions can be assembled by an in-house team.
- Form-in-place gaskets must be dispensed by someone who has the appropriate dispensing equipment (and you’ll definitely want to keep in mind that having an expert here is critical, as there is a pretty steep learning curve involved).
- Extrusions typically take longer to install than form-in-place gaskets take to be dispensed and cured.
In this instance, you’ll want to consider how your own labor will be affected by your choice, what it will ultimately do to product lead times, and how these factors are affected by the volume of parts you are producing.
Production Costs
The last part of the equation, which is tied inextricably with the previous factor, is cost.
It is actually kind of tough to directly compare the material costs between FIP gaskets and extrusions because the effects each has on the assembly process means there are far reaching implications for total part costs.
The initial material cost is just the beginning of the conversation. One factor that makes this relatively confusing is that when comparing quotes between the two products. A quote for extrusion will just be simple material cost. A quote for an FIP gasket will actually include both material cost and the cost to dispense the material onto the part.
So, on the surface it may look like FIP is the more expensive option. But what is important to keep in mind is that FIP reduces your assembly costs overall, as it takes care of one step in assembly for you.
Thus, when deciding which is the more economical option, you’ll need to consider your own labor costs into the equation. If you have exceptionally low labor costs, extrusion might be the winner. If your labor costs are high or assembly would be very difficult, FIP will probably be your winner.
Why Choose Modus Advanced for Your FIP Gasket Dispensing?
At Modus Advanced, we've mastered the art and science of FIP gasket dispensing while offering a complete manufacturing ecosystem that accelerates your path to market. Our engineering-first approach means your critical components receive expert attention at every stage.
With Modus, you gain:
- Vertical integration that eliminates shipping between vendors and reduces lead times
- Concurrent manufacturing processes including machining, plating, and thermal material application
- Engineering expertise with over 10% of our staff being engineers who understand your technical challenges
- Enhanced quality control through a single quality system governing the entire process
- Simplified communication with one partner instead of multiple vendors
When one day matters—and we believe it does—our vertically integrated approach doesn't just save time; it helps your innovations reach the field faster, whether that's life-saving medical devices or mission-critical defense systems.
FIP Dispensing ServicesThe Bottom Line
Ultimately choosing between extrusions and FIP comes down to a part-by-part discussion. It isn’t always a simple answer, and your choice affects far more than the part itself. It also has further-reaching implications in your assembly process and, ultimately, in your part cost and speed to market. Visit our Glossary for more definitions of key manufacturing terms.