Form in Place EMI Gaskets: Precision Shielding for Complex Geometries
April 4, 2025
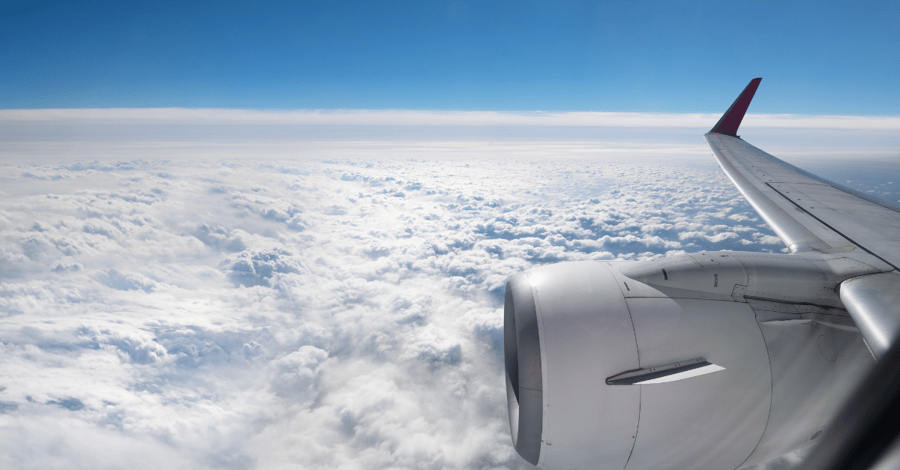
Manufactured with Speed and Precision
The manufacturing capabilities you need and the engineering support you want, all from a single partner.
Submit a DesignKey Points
Before diving into the details, let's examine the core attributes that make form-in-place EMI gaskets a game-changer for complex geometries:
- Customizable application: Precise dispensing for intricate shapes
- Material versatility: Various conductive materials available
- Excellent compression set resistance: Maintains seal integrity over time
- Minimal waste: Reduces material costs and environmental impact
- Seamless integration: Ideal for tight spaces and complex assemblies
In the high-stakes world of aerospace and defense manufacturing, electromagnetic interference (EMI) shielding isn't just a technical requirement — it's a mission-critical necessity. As DoD contractors and OEMs push the boundaries of electronic system miniaturization and complexity, the limitations of conventional EMI shielding methods become increasingly apparent.
The evolution of electronic systems in aerospace and defense applications has created unprecedented challenges in EMI protection. Form-in-place (FIP) EMI gaskets represent a sophisticated solution to these challenges, offering precision shielding for even the most demanding applications.
Learn everything you need to know about EMI Shielding.
Understanding Form in Place EMI Gasket Technology
Form in place EMI gaskets represent a significant leap forward in shielding technology. Unlike pre-formed gaskets, FIP gaskets are dispensed directly onto the substrate as a viscous material that cures in place. This process allows for unparalleled precision and adaptability in shielding applications.
The basic principle behind FIP EMI gaskets involves the controlled dispensing of a conductive elastomer material along a predetermined path. This material, typically a silicone-based compound filled with conductive particles, creates a continuous, customized seal that conforms perfectly to the substrate's surface.
The Dispensing Process
The precision dispensing of form-in-place EMI gaskets requires careful control of multiple variables to ensure consistent results.
Key process parameters include:
- Material viscosity and flow rate
- Dispensing pressure and speed
- Needle size and type
- Environmental conditions during cure
- Substrate temperature and preparation
These parameters work together to create gaskets that meet exact specifications while maintaining their protective properties. Understanding these fundamentals sets the stage for proper material selection, which is crucial for optimal performance.
Material Selection and Properties
The selection of appropriate materials is fundamental to achieving optimal EMI shielding performance. Engineers must carefully balance electrical conductivity, mechanical properties, and environmental resistance when choosing materials for their specific application.
Conductive Fillers
The choice of conductive filler significantly impacts the gasket's shielding effectiveness and galvanic compatibility.
Common filler options include:
- Silver-plated copper
- Silver-plated aluminum
- Silver-plated nickel
- Nickel-graphite
- Pure silver
Each filler type offers distinct advantages depending on the application requirements and environmental conditions. The selection of the proper filler material directly influences both performance and cost considerations.
Base Elastomers
The elastomeric base material provides the gasket's mechanical properties and environmental resistance.
Critical properties to consider include:
- Compression set resistance
- Temperature stability
- Chemical resistance
- Adhesion characteristics
- Cure mechanism
With materials properly selected, attention must turn to the crucial aspects of design implementation.
Design Considerations
Creating effective form-in-place EMI gaskets requires a thorough understanding of both design principles and manufacturing constraints. A successful design must account for everything from basic geometric requirements to long-term performance specifications in challenging environments.
Geometric Constraints
Understanding geometric limitations is crucial for optimal gasket performance.
Essential geometric considerations include:
- Minimum wall width requirements
- Height-to-width ratios
- Corner radius specifications
- Surface finish requirements
- Compression stop design
These design elements directly impact the gasket's ability to maintain consistent contact and provide effective shielding.
Performance Requirements
Engineers must clearly define performance requirements to ensure the gasket meets application needs.
Key specifications include:
- Shielding effectiveness across frequency ranges
- Compression force requirements
- Environmental exposure conditions
- Durability requirements
- Service life expectations
Once these technical foundations are established, we can examine how these capabilities translate into real-world applications.
Applications in Mission-Critical Systems
Protecting sensitive electronics from electromagnetic interference has become more crucial than ever. Form-in-place EMI gaskets provide reliable shielding solutions across a wide range of critical applications where failure is not an option.
Aerospace and Defense Applications
The aerospace and defense sectors require particularly robust EMI shielding solutions.
Critical applications include:
- Mission-critical communications
- Avionics systems
- Electronic warfare equipment
- Secure communication devices
- Flight control systems
- Radar systems
- Navigation equipment
- Satellite components
The demands of these applications drive continuous innovation in FIP gasket technology and implementation.
Medical Device Applications
Medical equipment often requires precise EMI shielding to ensure proper operation and patient safety.
Typical applications include:
- Diagnostic equipment
- Patient monitoring systems
- Surgical equipment
- Imaging systems
- Life support devices
The success of FIP gaskets in these critical applications has led to significant benefits for manufacturers in these sectors.
Benefits for DoD Contractors and OEMs
The implementation of form in place EMI gaskets offers distinct advantages for Department of Defense contractors and Original Equipment Manufacturers working on mission-critical systems.
Accelerated Production Timeline
By eliminating the need for custom-molded gaskets, FIP technology dramatically shortens production timelines. Modern dispensing systems, combined with in-house manufacturing capabilities, enable rapid prototyping and seamless transition to full-scale production.
Enhanced Quality and Consistency
Form-in-place EMI gaskets deliver superior quality through automated dispensing processes, ensuring consistent shielding performance across production runs. This reliability is paramount for mission-critical defense and aerospace applications where failure is not an option.
Cost-Effective Scaling
The transition from prototype to production becomes significantly more efficient with FIP gasket technology.
Key cost benefits include:
- Minimal tooling costs with no molds required
- Reduced inventory through on-demand production
- Design flexibility without retooling expenses
- Lower material waste
- Simplified assembly processes
These advantages make FIP gaskets particularly attractive for programs that may require design iterations or varying production volumes. To fully realize these benefits, proper manufacturing integration is essential.
Visit the full resource center here
Manufacturing Integration and Capabilities
The true power of FIP gasket technology emerges when integrated with other advanced manufacturing capabilities.
CNC Machining Integration
The combination of precision CNC machining with FIP gasket dispensing creates seamless, ready-to-assemble components. This integration ensures:
- Perfect fit between housing and gasket
- Optimal surface preparation
- Consistent gasket compression
- Reduced assembly time
- Enhanced quality control
Surface Treatment Integration
Comprehensive EMI solutions often benefit from multiple shielding approaches. The ability to apply conductive coatings to machined parts before dispensing FIP gaskets creates a multi-layered shielding strategy that maximizes protection.
Manufacturing Partner Selection
Selecting the right manufacturing partner for form-in-place EMI gaskets requires careful evaluation of several critical factors. A qualified partner should maintain ITAR registration and compliance, along with AS9100 certification, demonstrating their commitment to aerospace and defense standards. Experience with DoD contractors is particularly valuable, as these partners understand the unique requirements and security protocols essential for defense applications.
Beyond certifications, evaluate the partner's facility security measures and vertical integration capabilities. Technical expertise and comprehensive quality certifications provide the foundation for reliable production, while robust manufacturing capabilities and responsive support services ensure long-term success.
Quality Assurance
Quality control in form-in-place EMI gasket production demands a sophisticated, multi-layered approach. Advanced manufacturing facilities employ real-time vision systems for inspection and automated validation of the dispensing process. Environmental monitoring during cure cycles, combined with comprehensive testing documentation, ensures consistent results across production runs.
Successful quality assurance programs incorporate full material traceability, precise dimensional verification, and thorough adhesion testing. Regular conductivity testing validates the gasket's shielding effectiveness. Together, these measures create a robust quality system that maintains consistent performance throughout the production lifecycle.
Collaboration Process
The path to successful form-in-place EMI gasket implementation begins with early collaboration between design engineers and manufacturing partners. Effective partnerships start during the initial design phase, where technical consultation can prevent costly modifications later in the process. As the project progresses, close collaboration ensures proper process development and quality planning.
Ongoing support throughout the product lifecycle helps address challenges as they arise and enables continuous improvement of both design and manufacturing processes. This collaborative approach, combined with rigorous quality assurance and careful partner selection, creates the foundation for successful EMI shielding implementation.
Modus Advanced Solutions
At Modus Advanced, we've invested in state-of-the-art equipment and processes to deliver superior FIP EMI gasket solutions. Our specialized dispensing systems offer:
- Precision control: +/- 0.1mm accuracy in bead placement
- Flexibility: Capable of dispensing various bead profiles and sizes
- Speed: High-speed dispensing for efficient production
- Quality assurance: Integrated systems for quality control
Materials for Optimal Shielding Performance
We utilize a range of advanced materials to meet diverse shielding requirements:
- Silicone-based elastomers: Excellent temperature resistance and durability
- Fluorosilicone options: Enhanced resistance to fuels and solvents
- Particle-filled compounds: Silver, nickel, or graphite for tailored conductivity
- Custom formulations: Engineered for specific environmental challenges
Vertically Integrated Approach
At Modus Advanced, our vertically integrated manufacturing process represents a significant advantage in form-in-place EMI gasket production. Rather than relying on multiple vendors for different aspects of production, we handle every step of the manufacturing process under one roof. This comprehensive approach ensures seamless coordination and superior quality control throughout the entire production cycle.
Our single-point-of-contact system streamlines project management and communication, eliminating the complexity of coordinating with multiple suppliers for machining, plating, gasket dispensing, and quality control. This simplified communication structure reduces misunderstandings and ensures all requirements are accurately implemented across every manufacturing stage.
Traditional manufacturing often involves shipping parts between multiple vendors, with each transfer adding delays to production timelines. Our integrated approach eliminates these delays and associated costs, allowing concurrent processing of different manufacturing steps. This efficiency is especially valuable for prototype development and quick-turn production requirements.
The Future of EMI Shielding: Precision, Performance, and Partnership
As electronic systems continue to advance in complexity and miniaturization, the role of form-in-place EMI gaskets becomes increasingly critical. These sophisticated shielding solutions represent not just a current solution, but a pathway to future innovations in aerospace, defense, and medical device applications.
Success in implementing form in place EMI gaskets depends on the careful orchestration of material science, design expertise, and precise manufacturing processes. Working with an experienced partner who understands both the technical demands and mission-critical nature of these applications is essential. The right manufacturing partner brings together advanced capabilities, rigorous quality systems, and robust security protocols to ensure consistent, reliable results.
At Modus Advanced, our engineering team combines deep technical expertise with a thorough understanding of aerospace and defense requirements. Through our vertically integrated processes and comprehensive quality systems, we help accelerate the development and production of mission-critical components where failure is not an option.
Contact our team to explore how we can support your next EMI shielding project and help bring your innovations to life sooner.