Material Offsets for EMI Shielding Form-in-Place Materials
October 30, 2024
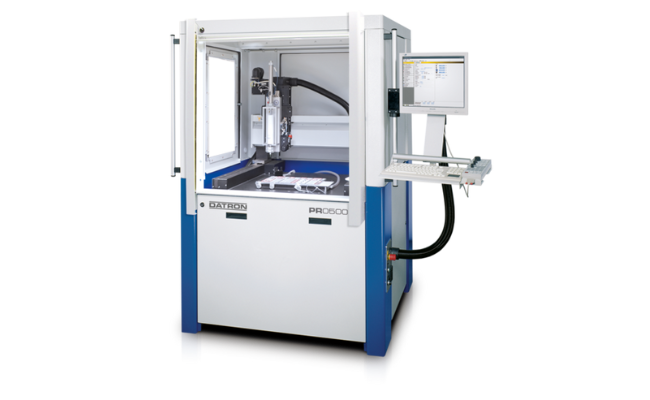
Manufactured with Speed and Precision
The manufacturing capabilities you need and the engineering support you want, all from a single partner.
Submit a DesignKey Points
- Chomerics offers a range of EMI shielding FIP materials that can serve as alternatives to many Tennmax, Laird, and other FIP products.
- When selecting an alternative, it's important to consider specific project requirements such as shielding vs. grounding needs and corrosion resistance.
- Environmental regulations, such as the EPA's efforts to reduce PFAS usage, are driving the development of new, compliant materials.
- Supply chain risk reduction, domestic sourcing requirements, and vendor flexibility are common reasons for seeking material alternatives.
We commonly get requests from customers for material offsets and alternatives to ensure they have de-risked their supply chain, or to find a suitable additional partner for dispensing and converting materials.
We’ve created this article to help answer the most common questions we get about material offsets. We hope that this makes it easier for engineers to get their questions answered on making trade-offs and decisions around which materials are the best fit for their project, supply chain risk tolerance, and vendor requirements.
Get the Parker Chomerics EMI Shielding Material Guide here!
Why Find Alternative EMI Shielding Form-in-Place (FIP) Materials?
Choosing offsets for Form-in-Place materials is as much of an art as it is a science. Our team typically works with customers to identify their primary need or the defining characteristic of the material that is most important to their part or project, and then work from there to find a range of other materials that will work to serve the same needs in its place.
The reasons our team is often asked for material offsets for Form-in-Place materials include:
- Supply Chain Risk Reduction: Often customers using a proprietary material are often nervous about the risk that material poses to their supply chain. They can only get the material through one source, and are stuck with whatever supply chain issues may arise for that single source.
- Domestic Supply Chain Goals: Additionally, defense and aerospace customers are often sensitive to where that supply chain originates from. If a material is produced in a foreign country, for example, it can possibly close doors on high-value contracts.
- Vendor Performance and Choices: Another reason customers ask for material offsets, particularly for single source proprietary materials, is that it gives them options for vendors who can fulfill their needs. This way, they can flexibly move between vendors depending on satisfaction with communication, lead times, and quality as needed.
Below you’ll find a list of the most common FIP materials our team has been asked to provide offsets for along with details as to how the offset was determined. As previously mentioned, offsets are often specific to the needs of a project, so if you have any questions about a specific project you are working on, don’t hesitate to reach out to our team for guidance.
Tennmax Alternative
Tennmax Alternatives for EMI Shielding FIP Materials
- Get a list of product-by-product offsets, along with reasoning for each, for each Tennmax form-in-place gasket material.
- Review a summarized table of all potential Tennmax form-in-place material alternatives.
For this particular material supplier, the defining characteristic most customers are after is the ability to dispense a very small bead. Our team has found particular success with small bead application using a set of Chomerics materials.
Depending on the use case, there are a couple of questions to ask yourself about your specific project to arrive at the best Chomerics material to use as a potential offset:
- Does your application require shielding or grounding?
- Is corrosion resistance important for your project?
If you require both shielding capabilities and corrosion resistance, you’ll want to look at Chomerics CHOFORM 5575 or CHOFORM 5538.
If you require grounding and do not need corrosion resistance, you’ll want to look at CHOFORM 5513 or 5528.
Learn how we've used Chomerics materials to achieve small bead sizes for our customers.
Tennmax F5304 Alternatives
For this particular material, the defining characteristic most customers are after is the hardness of the material. The Chomerics material that best offsets this need is CHOFORM 5550.
Tennmax F5314 Alternatives
The primary characteristic of this is the softness and use case at higher frequencies. While a much less common request, the most comparative offset for this material is CHOFORM 5550 or 5538.
Tennmax F5221 Alternatives
The defining characteristic most customers need out of this material is the grounding capabilities, so you’ll want to find the replacement with the lowest resistance. In this case CHOFORM 5513 or 5528 are the best alternatives.
Tennmax F5321 Alternatives
Because this material is for use on plastics, you’ll want to match the ability to produce a small bead with a Chomerics material that is not cured using thermal methods. In this case, you’ll still have two questions to ask yourself about the project:
- Does your application require shielding or grounding?
- Is corrosion resistance important for your project?
If you require both shielding capabilities and corrosion resistance, you’ll want to look at Chomerics CHOFORM 5575.
If you require grounding and do not need corrosion resistance, you’ll want to look at CHOFORM 5528.
Tennmax F5521 Alternatives
The defining characteristic of this material is that has strong corrosion resistance. Good offsets for this need from Chomerics include CHOFORM 5575 and 5550.
Tennmax F5381 and F5382 Alternatives
The defining characteristics of these materials is that they are solvent resistant. The problem with these materials is that they use flourosilicone to achieve the desired capabilities.
The EPA is currently working to remove and reduce the usage of this material and others in the category. Your goal should be to find a solvent resistant material that meets PFAS requirements.
Modus is currently working on a proprietary material to do just that. If you are interested in learning more, please don’t hesitate to reach out to our team for more information.
Tennmax F9304 Alternatives
The defining characteristic of this material is its hardness. Good Chomerics offsets to this material are CHOFORM 5550 and 5575.
Visit the Modus Form-in-Place Gasket Resource Center
Tennmax Offsets: Material Alternatives Summary
Find a summary of potential material offsets for all Tennmax materials in the table below.
Tennmax Material | Key Characteristics | Recommended Chomerics Alternatives |
---|---|---|
General Tennmax FIP | Small bead dispensing capability | Depends on specific needs (see below) |
If shielding + corrosion resistance needed: | CHOFORM 5575, CHOFORM 5538 | |
If grounding only (no corrosion resistance): | CHOFORM 5513, CHOFORM 5528 | |
F5304 | Higher hardness | CHOFORM 5550 |
F5314 | Softness, higher frequency applications | CHOFORM 5550, CHOFORM 5538 |
F5221 | Grounding capabilities (lowest resistance) | CHOFORM 5513, CHOFORM 5528 |
F5321 | For use on plastics, small bead, non-thermal cure | Depends on specific needs |
If shielding + corrosion resistance needed: | CHOFORM 5575 | |
If grounding only (no corrosion resistance): | CHOFORM 5528 | |
F5521 | Strong corrosion resistance | CHOFORM 5575, CHOFORM 5550 |
F5381, F5382 | Solvent resistant (contains fluorosilicone) | Modus proprietary material in development (PFAS compliant) |
F9304 | Hardness | CHOFORM 5550, CHOFORM 5575 |
Laird Alternative
Laird Alternatives for EMI Shielding FIP Materials
- Get a list of product-by-product offsets, along with reasoning for each, for each Laird form-in-place gasket material.
- Review a summarized table of all potential Laird form-in-place material alternatives.
Laird Technologies is a well-known manufacturer of EMI shielding materials, including form-in-place (FIP) gaskets. However, there are alternative products available from other manufacturers that offer similar properties and performance.
Laird SNC45-HXP Alternatives
The defining characteristic of this material is the non-conductive filler combined with a low hardness. Chomerics’ CHOFORM 5550 is a suitable offset for this material.
Laird SNC70-HXP and SNC70-RXP Alternatives
The defining characteristic of this material is the nickel/graphite filler combined with its shielding capability. Chomerics’ CHOFORM 5550 is a suitable offset for this material as well.
Laird SNL60-RXP Alternatives
The defining characteristic of this material is the Silver/Aluminium filler combined the room temperature curing mechanism. Chomerics’ CHOFORM 5575 is a suitable offset for this material with similar properties and curing capabilities.
Laird SNK55-RXP Alternatives
The defining characteristic of this material is the silver/copper filler combined with its rapid curing capabilities. Chomerics’ CHOFORM 5528 is a suitable offset for this material.
Laird SNN60-RXP Alternatives
The defining characteristic of this material is its shielding effectiveness and corrosion resistance. Chomerics’ CHOFORM 5575 is a suitable offset for this material.
Laird Offsets: Material Alternatives Summary
Find a summary of potential material offsets for all Laird materials in the table below.
Laird Material | Key Characteristics | Recommended Chomerics Alternative |
---|---|---|
SNC45-HXP | Non-conductive filler, low hardness | CHOFORM 5550 |
SNC70-HXP, SNC70-RXP | Nickel/graphite filler, shielding capability | CHOFORM 5550 |
SNL60-RXP | Silver/Aluminum filler, room temperature curing | CHOFORM 5575 |
SNK55-RXP | Silver/copper filler, rapid curing | CHOFORM 5528 |
SNN60-RXP | High shielding effectiveness, corrosion resistance | CHOFORM 5575 |
Final Thoughts
Selecting the right EMI shielding Form-in-Place (FIP) material is crucial for ensuring both performance and supply chain stability. This article has outlined various alternatives for popular Tennmax and Laird FIP materials, focusing on key characteristics such as bead size, hardness, corrosion resistance, and shielding effectiveness.
Remember that while this guide provides general recommendations, each project may have unique requirements. It's always advisable to consult with EMI shielding experts when making final material selections. Our team at Modus is ready to assist you in finding the best FIP material solution for your specific needs, including our work on developing new, environmentally friendly alternatives.
By understanding these material offsets and alternatives, engineers can make informed decisions that balance performance, supply chain resilience, and regulatory compliance in their EMI shielding projects.
Why Choose Modus Advanced for Your FIP Gasket Dispensing?
At Modus Advanced, we've mastered the art and science of FIP gasket dispensing while offering a complete manufacturing ecosystem that accelerates your path to market. Our engineering-first approach means your critical components receive expert attention at every stage.
With Modus, you gain:
- Vertical integration that eliminates shipping between vendors and reduces lead times
- Concurrent manufacturing processes including machining, plating, and thermal material application
- Engineering expertise with over 10% of our staff being engineers who understand your technical challenges
- Enhanced quality control through a single quality system governing the entire process
- Simplified communication with one partner instead of multiple vendors
When one day matters—and we believe it does—our vertically integrated approach doesn't just save time; it helps your innovations reach the field faster, whether that's life-saving medical devices or mission-critical defense systems.
FIP Dispensing ServicesStill have questions? We're here to help – contact our team today.