LORD 100 Series Plate Form Mounts: Engineering Guide for Aerospace & Defense Applications
November 6, 2024
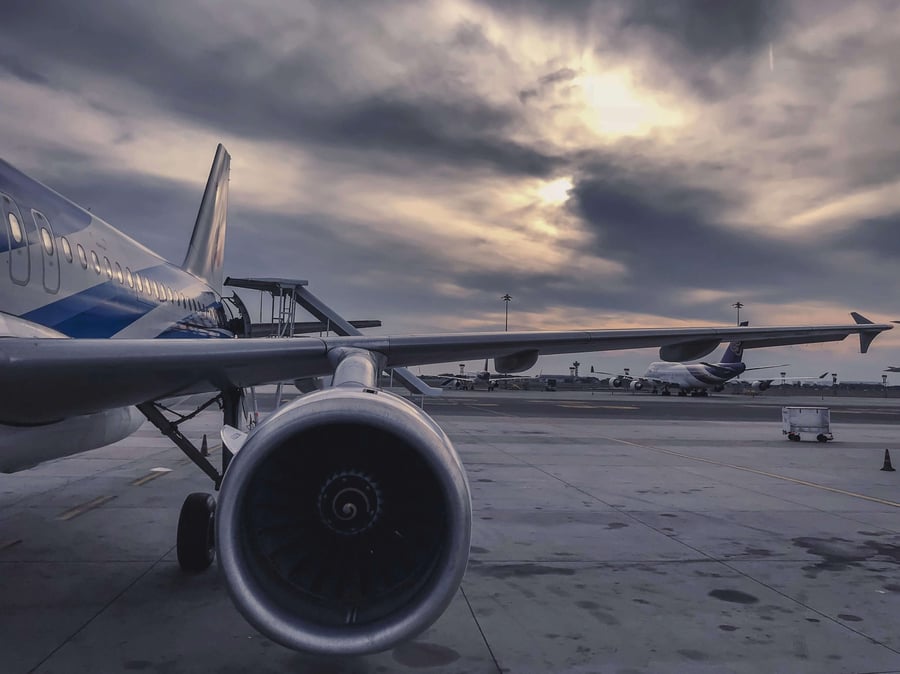
Manufactured with Speed and Precision
The manufacturing capabilities you need and the engineering support you want, all from a single partner.
Submit a DesignKey Points
Understanding when and how to use LORD 100 Series Plate Form Mounts requires careful consideration of several critical factors:
- These mounts provide efficient isolation of steady-state vibration while controlling occasional shock in loads from 0.25 to 12 pounds
- When properly loaded, they achieve approximately 18 Hz natural frequency, delivering effective isolation above 40 Hz
- The mounts feature uniform stress distribution through contoured flexing elements
- Available in both square and diamond configurations to accommodate various design requirements
- Recommended for use with snubbing washers to create an interlocking safety system
In aerospace and defense applications, protecting sensitive equipment from damaging vibration and shock is crucial for ensuring reliable operation and long service life. The LORD 100 Series Plate Form Mounts represent a proven solution that combines simplicity, versatility and predictable performance in a standardized package. Let's explore the key considerations for selecting and implementing these mounts effectively.
Design Features and Benefits
The 100 Series mounts incorporate several engineered features that make them particularly well-suited for aerospace and defense applications. The foundation of their performance comes from their sandwich-style construction, with two metal plates bonded to a precisely formulated elastomeric element.
Key design advantages include:
- Contoured flexing elements that provide uniform stress distribution
- High-strength bonding system ensuring long-term durability
- Specially compounded elastomers optimized for aerospace environments
- Simple installation with standard hardware
- Available in both square and diamond configurations
- Optional snubbing washers for enhanced safety
The carefully engineered profile of these mounts delivers consistent performance while maintaining a compact form factor.
LORD 100 Series Model Variants
When selecting a mount from the 100 Series family, engineers must consider not only load requirements but also mounting configuration and space constraints. Each variant in the series offers specific advantages while maintaining the core benefits of the plate form design.
100APL Series
The 100APL Series represents the standard square configuration for lighter load applications. These mounts support loads from 0.25 to 6 pounds (0.10 to 2.7 kg) and provide consistent performance across their operating range. Their square mounting pattern makes them particularly suitable for applications where traditional mounting orientations are preferred.
100APDL Series
Identical in load capacity to the 100APL Series, the 100APDL Series features a diamond mounting configuration. This orientation can be advantageous in applications where space constraints or mounting hole patterns favor a 45-degree offset. The series maintains the same performance characteristics while offering additional installation flexibility.
150APL Series
The 150APL Series extends the load capacity range up to 12 pounds (5.4 kg) while maintaining the square mounting configuration. These mounts are ideal for medium-weight applications requiring the same reliable vibration isolation performance of the lighter-duty models. The increased size and load capacity make them suitable for larger electronic enclosures and instruments.
150APDL Series
Completing the family, the 150APDL Series combines the higher load capacity of the 150APL with a diamond mounting configuration. This series offers the maximum flexibility for mounting heavier components while accommodating various mounting orientations and space constraints.
Comparative Specifications
The following table provides a detailed comparison of specifications across all 100 Series variants:
Model Series | Load Capacity | Natural Frequency | Dynamic Spring Rate (Axial) | Dynamic Spring Rate (Radial) | Mount Configuration | Available Elastomers |
100APL | 0.25-6 lb <br>(0.10-2.7 kg) | 18 Hz | 8-200 lb/in <br>(1.4-34.8 N/mm) | Approx. 2-3x axial | Square | BTR® Silicone <br>BTR® II Silicone |
100APDL | 0.25-6 lb <br>(0.10-2.7 kg) | 18 Hz | 8-200 lb/in <br>(1.4-34.8 N/mm) | Approx. 2-3x axial | Diamond | BTR® Silicone <br>BTR® II Silicone |
150APL | 1-12 lb <br>(0.45-5.4 kg) | 18 Hz | 33-400 lb/in <br>(5.7-70 N/mm) | Approx. 2-3x axial | Square | BTR® Silicone <br>BTR® II Silicone |
150APDL | 1-12 lb <br>(0.45-5.4 kg) | 18 Hz | 33-400 lb/in <br>(5.7-70 N/mm) | Approx. 2-3x axial | Diamond | BTR® Silicone <br>BTR® II Silicone |
Material Options
All 100 Series mounts are available with either BTR® or BTR® II elastomers. The choice between these materials typically depends on the operating environment:
- BTR® Silicone offers the broadest temperature range (-65°F to +300°F) and is ideal for applications exposed to extreme environmental conditions
- BTR® II Silicone provides excellent performance in more moderate conditions (-40°F to +300°F) and may offer cost advantages in appropriate applications
Each variant in the 100 Series family maintains consistent design principles while offering specific advantages for different applications. Understanding these differences helps ensure proper mount selection for your specific requirements.
Performance Characteristics
Understanding the performance envelope of 100 Series mounts is essential for proper application. These mounts demonstrate specific behaviors that engineers must consider during the design phase.
Critical performance attributes include:
- Load capacity range of 0.25 to 12 pounds per mount
- Natural frequency of approximately 18 Hz when properly loaded
- Effective isolation for disturbing frequencies above 40 Hz
- Radial stiffness approximately 2-3 times the axial stiffness
- Predictable load-deflection characteristics
- Consistent performance across their rated temperature range
The combination of these characteristics makes them particularly effective for protecting sensitive electronics and instruments.
Application Considerations
Proper implementation of 100 Series mounts requires careful attention to several key factors to ensure optimal performance. The mounting system must be engineered as a complete solution rather than just individual components.
Important considerations include:
- Proper load distribution across multiple mounts
- Maintaining recommended compression ratios
- Accounting for all static and dynamic loads
- Environmental exposure conditions
- Installation space constraints
- Safety requirements and fail-safe considerations
Taking a systematic approach to these factors helps ensure successful implementation.
Related: Read our Guide to Parker LORD Vibration Isolation Mounts.
Installation Best Practices
Achieving optimal performance from 100 Series mounts depends heavily on proper installation procedures. Following established best practices helps ensure the mounts will deliver their intended performance.
Key installation guidelines include:
- Use of proper torque specifications for mounting hardware
- Implementation of recommended snubbing washers
- Proper alignment during installation
- Verification of load distribution
- Maintenance of specified clearances
- Regular inspection of mounting integrity
Careful attention to these details during installation helps maximize mount effectiveness and service life.
Maintenance and Inspection
While 100 Series mounts are designed for long-term reliability, implementing a proper maintenance program helps ensure continued performance. Regular inspection and maintenance activities protect your investment in these critical components.
Essential maintenance activities include:
- Visual inspection for signs of degradation
- Verification of proper preload maintenance
- Checking for proper clearances
- Evaluation of snubbing washer condition
- Documentation of mount condition
- Replacement at recommended intervals
A proactive maintenance approach helps prevent unexpected issues and extends service life.
Final Thoughts
LORD 100 Series Plate Form Mounts provide aerospace and defense engineers with a proven solution for vibration and shock control when properly specified and implemented. Their standardized design, predictable performance, and robust construction make them an excellent choice for protecting sensitive equipment in demanding applications.
Working with Modus Advanced for Aerospace and Defense Applications
Aerospace and defense projects that include vibration isolation components often require careful consideration of the entire system, including the housing and mounting structure. Modus Advanced brings particular expertise to these applications through our comprehensive approach to aerospace and defense projects.
Engineering-First Approach
Modus Advanced's engineering team, comprising over 10% of our staff, provides comprehensive technical support across all aspects of aerospace and defense projects. Our engineers work directly with customers from initial design through production, offering expertise in materials science, manufacturing processes, and system-level optimization.
This engineering-first mindset enables us to assist with critical decisions about material selection, manufacturing methods, and design optimization that can significantly impact project success.
When working with aerospace and defense customers, our engineering team provides invaluable insights into design for manufacturability, helping to identify potential issues before they become costly problems.
We understand the complex requirements of aerospace and defense applications, from material compatibility and environmental considerations to quality control and documentation requirements. This deep technical knowledge, combined with our practical manufacturing experience, helps ensure that designs move smoothly from concept to production while meeting all necessary specifications and standards.
Vertical Integration Benefits
When developing complex aerospace and defense components, traditional manufacturing approaches often require coordinating with multiple vendors for different processes, leading to extended lead times, increased shipping costs, and greater risk of quality issues or delays.
Modus Advanced's vertically integrated manufacturing capabilities eliminate these challenges by bringing critical processes under one roof, allowing us to maintain strict quality control while significantly reducing both production time and cost. This integration means customers can work with a single point of contact while having confidence that their components will meet specifications across all aspects of manufacturing.
Modus Advanced's vertically integrated manufacturing capabilities provide significant advantages for aerospace and defense projects:
- Complete in-house manufacture of housings and mounting systems
- Form-in-place gasket dispensing for environmental sealing
- EMI shielding integration
- Thermal management solutions
- Quality control across all manufacturing processes
This integration reduces lead times and ensures consistent quality across all components.
Quality and Security Standards
Our commitment to aerospace and defense requirements is demonstrated through our comprehensive certifications and standards:
- AS9100 certification
- ITAR registration
- ISO 9001 certification
- Working toward CMMC Level 2
- Strict quality control processes
These certifications ensure we meet the exacting standards required for aerospace and defense applications.
Partnership Approach
Rather than operating as a traditional supplier, Modus Advanced functions as a strategic partner in our customers' success. We engage early in the design process, providing technical insights and manufacturing expertise that help optimize designs for both performance and producibility. This collaborative approach often leads to significant improvements in design efficiency, reduced manufacturing costs, and accelerated time to market.
Our commitment to partnership extends throughout the entire project lifecycle, with ongoing support for quality improvement, process optimization, and problem resolution. We understand that aerospace and defense projects often evolve over time, and we maintain the flexibility to adapt our support as requirements change. This long-term perspective helps build lasting relationships that continue to deliver value for both parties.