Micro Dispensing of Electrically Conductive Materials: Small Bead-Size Form-in-Place Gaskets
March 5, 2025
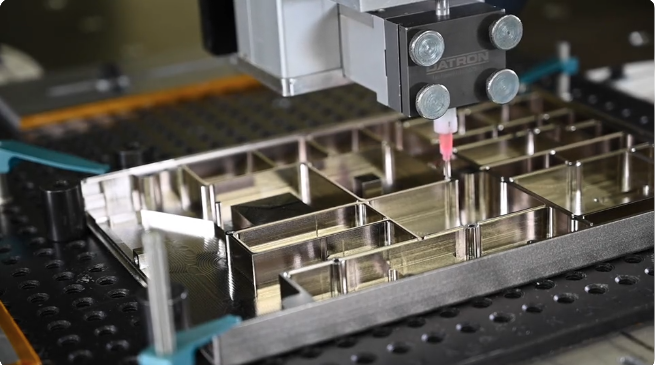
Manufactured with Speed and Precision
The manufacturing capabilities you need and the engineering support you want, all from a single partner.
Submit a DesignKey Points
- As electronic devices shrink in size, the demand for micro-scale FIP gaskets has grown significantly, particularly in aerospace, defense, and medical device industries.
- Traditional FIP gasket materials were not designed for extremely small bead dispensing, creating technical barriers that innovative manufacturers must overcome.
- Advances in dispensing technology, including specialized needles and precision equipment, have enabled the reliable production of micro-bead FIP gaskets.
- Partnering with a manufacturer experienced in micro-dispensing ensures proper quality control and measurement processes, critical for mission-critical applications.
- Modus Advanced has developed proprietary techniques for dispensing bead sizes smaller than material manufacturers considered possible, breaking boundaries in FIP gasket technology.
Introduction: The Growing Need for Micro-Scale FIP Gaskets
In today's rapidly advancing technological landscape, electronic devices continue to shrink while simultaneously becoming more complex. This miniaturization trend places mounting pressure on component manufacturers to deliver increasingly precise solutions that function in tighter spaces. Form-in-Place (FIP) gaskets—traditionally used for electromagnetic interference (EMI) shielding and environmental sealing—are no exception to this trend.
Engineers across aerospace, defense, and medical device sectors are now designing housings with thinner walls and smaller footprints than ever before. These designs require gaskets with micro-scale bead sizes that push the boundaries of what many material manufacturers considered possible. As technology advances into new frontiers, manufacturing capabilities must evolve to keep pace.
Everything you've ever wanted to know about FIP Gaskets - here!
The Technical Challenges of Micro-Bead Dispensing
Dispensing extremely small FIP gasket beads presents several significant technical challenges that manufacturers must overcome. These challenges go beyond simply using smaller needles or adjusting machine settings.
Most conductive adhesive FIP materials were originally formulated for standard bead sizes and don't naturally lend themselves to micro-dispensing applications. The conductive particles needed for EMI shielding—typically nickel, silver, silver-coated aluminum, or silver-coated copper—can create dispensing issues when forced through very small gauge needles. Material viscosity, particle distribution, and flow characteristics all become more critical as bead size decreases.
Quality control presents another major hurdle. Measuring and verifying micro-bead dimensions requires specialized equipment and techniques. Traditional quality measurement approaches often lack the precision needed to confirm that these tiny beads meet tolerance requirements, especially across the entire dispensed path.
Maintaining consistent bead height and width along complex geometries requires extraordinary precision in both dispensing equipment and fixturing. Even slight variations in z-height can lead to significant percentage changes in these micro-beads, potentially causing functional failures.
The combination of these challenges explains why many FIP material manufacturers specify minimum bead size limitations. However, with proper engineering expertise and innovative approaches, these limitations can be overcome.
Breaking the Bead Size Boundary
Recent advancements in dispensing technology have made micro-bead FIP gaskets not just possible but reliable for production environments. These innovations have enabled manufacturers to break through previously established limitations.
Several technological developments have contributed to this breakthrough:
- Advanced needle technology with specialized geometry designed specifically for micro-dispensing
- Precision dispensing equipment with enhanced motion control systems
- Material optimization techniques that improve flow properties at micro scales
- Sophisticated vision systems and measurement capabilities to verify bead dimensions
- Improved fixturing to compensate for part variation and ensure consistent bead placement
Engineers have discovered that by carefully controlling dispensing parameters and leveraging these technological advancements, they can achieve reliable results with bead sizes smaller than previously thought possible. This has opened new design possibilities for product engineers working on miniaturized applications.
Additionally, the integration of thermal interface materials in micro-dispensing applications has expanded possibilities for heat management in compact electronic assemblies. These materials play a crucial role in ensuring thermal conductivity while maintaining electrical performance.
The keys to successful micro-dispensing lie in understanding the complex interplay between material properties, dispensing equipment, and environmental conditions. Small changes in any of these factors can significantly impact the final result.
Real-World Application: Defense Industry Case Study
A real-world example demonstrates how these challenges can be overcome in practice. One of Modus Advanced's defense partners approached us with a machining project featuring an extremely complex design with extraordinarily thin walls. The project specified a significantly smaller FIP gasket than typically dispensed—smaller than what the material manufacturer had rated as possible.
The customer initially requested sample straight lines to evaluate feasibility. However, our engineering team recognized an opportunity to deliver more value by demonstrating our capabilities on the actual part.
Through rigorous testing and experimentation, our FIP department developed a repeatable process for dispensing the micro-bead gasket within the customer's tight tolerances. This required carefully balancing dispensing speed, pressure, needle selection, and material properties to achieve consistent results.
What made this project particularly challenging was not just the small bead size but also the need for proper quality verification. Our quality control team leveraged advanced measurement technology to provide millimeter-by-millimeter confirmation that the entire dispensed path remained within tolerance—something the customer had previously been unable to achieve.
By utilizing functional materials optimized for micro-dispensing, we ensured that the gasket met both electrical and mechanical performance standards. The result was a successfully implemented micro-bead FIP solution that met all functional requirements while maintaining consistent quality. This demonstrates that with the right expertise and technology, manufacturers can push beyond conventional limitations.
Visit the Modus Form-in-Place Gasket Resource Center
Quality Control for Micro-Bead FIP Gaskets
When working with micro-bead FIP gaskets, quality control takes on heightened importance. The smaller the bead, the more significant any dimensional variation becomes as a percentage of the overall size.
Effective quality control for micro-bead FIP requires several specialized approaches:
- Advanced optical measurement systems capable of sub-millimeter precision
- Automated pattern tracking that can identify deviations from the intended dispensing path
- Cross-sectional analysis to verify bead profile and dimensions
- Comprehensive documentation of dispensing parameters for process repeatability
- Statistical process control to monitor trends and prevent quality drift
The quality control process starts with establishing clear specifications based on the application's functional requirements. These specifications must be realistic and measurable given the extremely small dimensions involved.
For mission-critical applications in aerospace, defense, or medical devices, extensive validation testing may be required to ensure the micro-bead gasket will perform as expected under all operating conditions. This testing frequently includes environmental exposure, compression set evaluation, and electrical performance verification.
Quality control for micro-bead FIP represents a significant technical challenge, but with the right equipment and expertise, manufacturers can consistently deliver gaskets that meet even the most demanding specifications.
Modus Advanced's Micro-Dispensing Capabilities
At Modus Advanced, we've made significant investments in the people, processes, and equipment needed to master micro-bead FIP gasket dispensing. Our approach combines engineering expertise with state-of-the-art technology to deliver solutions that push beyond conventional limitations.
Our capabilities in micro-dispensing include:
- Dispensing conductive FIP materials with bead heights smaller than material manufacturers deemed possible
- Advanced measurement systems that can verify the entire dispensed path to confirm tolerance compliance
- Engineering expertise to optimize designs for manufacturability while maintaining functionality
- Vertical integration capabilities that allow us to machine the housing, dispense the gasket, and perform other operations under one roof
- Extensive experience with challenging aerospace, defense, and medical applications where failure is not an option
One of our key advantages is our investment in specialized dispensing needles and precision equipment. Recent innovations have allowed us to significantly reduce cycle times while improving quality. For example, new micro-dispense needles combined with optimized dispensing parameters have enabled us to increase dispensing speed by 150% while maintaining consistent bead dimensions.
Our quality control processes ensure that even the smallest FIP gaskets meet all dimensional and functional requirements. We can provide comprehensive documentation to validate that your micro-bead gaskets will perform as expected in your application.
Case Study: Redefining the traditional supplier relationship.
Designing for Successful Micro-Bead FIP Implementation
When incorporating micro-bead FIP gaskets into your design, several considerations can help ensure successful implementation. Addressing these factors early in the design process can prevent manufacturing challenges and optimize performance.
Housing design plays a critical role in micro-bead FIP success. Consider these design recommendations:
- Maintain consistent Z-height along the gasket path to ensure uniform compression
- Design walls with sufficient width to accommodate the gasket (even micro-beads need adequate surface area)
- Incorporate appropriate compression stops to prevent over-compression
- Consider surface finishes and treatments that may affect adhesion
- Account for manufacturing tolerances in the housing that could impact gasket performance
Material selection should be based on your application's specific requirements. While all conductive material can potentially be dispensed in micro-bead form, some are better suited than others based on particle size, viscosity, and flow characteristics.
Related: Parker Chomerics EMI Shielding Material Guide
Early engagement with your manufacturing partner is essential when designing for micro-bead FIP gaskets. By involving manufacturing engineers during the design phase, you can identify potential issues before they become costly problems.
Incorporating these considerations into your design process will help ensure that your micro-bead FIP gaskets perform as expected while minimizing manufacturing challenges.
Future Trends in Micro-Bead FIP Technology
The field of micro-bead FIP technology continues to evolve rapidly, with several emerging trends that promise to further expand capabilities. Understanding these trends can help engineers plan for future applications.
Advancements in material science are creating new possibilities for micro-bead FIP gaskets. Nano-particle versions of traditional conductive fillers are being developed specifically for micro-dispensing applications. These materials offer improved flow characteristics while maintaining electrical conductivity and other key properties.
Dispensing equipment is becoming increasingly sophisticated, with enhanced vision systems, better motion control, and more precise dispensing mechanisms. These improvements will enable even smaller bead sizes while improving consistency and reducing waste.
Automation is playing a growing role in micro-bead FIP production. Automated inspection systems can verify bead dimensions and detect defects with greater precision than manual methods. This not only improves quality but also enables higher production volumes for micro-bead applications.
As these technologies mature, the possibilities for micro-bead FIP gaskets will continue to expand. Engineers who stay current with these developments will be positioned to leverage these capabilities in their future designs.
Final Thoughts: Partnering with the Right Manufacturer
As electronic devices continue to shrink while becoming more complex, the demand for micro-bead FIP gaskets will only increase. Meeting this demand requires a manufacturing partner with the right combination of experience, equipment, and expertise.
At Modus Advanced, we understand that one day matters when bringing life-changing products to market. Our engineering-first approach and vertical integration capabilities allow us to solve complex micro-dispensing challenges that others can't. Whether you're designing aerospace systems, defense electronics, or life-saving medical devices, our team can help you implement micro-bead FIP gaskets that meet your most demanding requirements.
When failure is not an option, choose a partner who understands what's at stake. Our team is ready to work with you from idea to ignition, ensuring your designs become reality with the quality and precision your applications demand.