Form-in-Place Gasket Material Guide
July 1, 2021
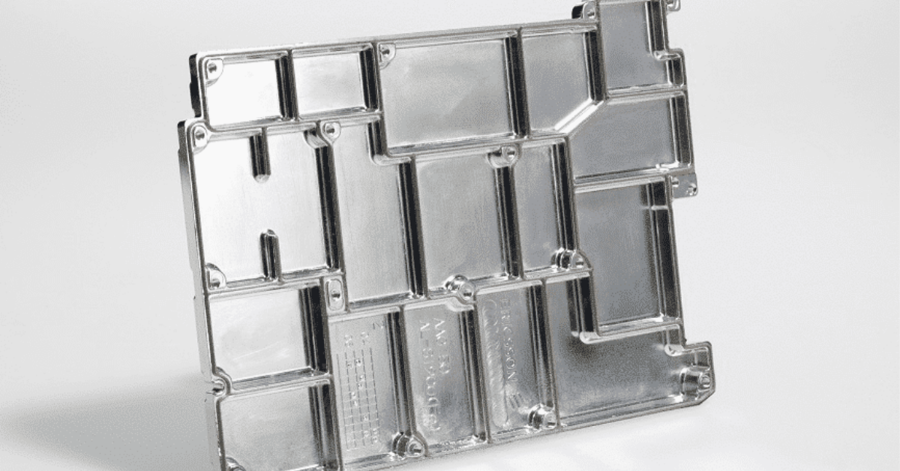
Manufactured with Speed and Precision
The manufacturing capabilities you need and the engineering support you want, all from a single partner.
Submit a DesignKey Points
- Form-in-Place (FIP) gaskets combine precision, durability, and affordability, making them popular across numerous industries for sealing and shielding applications.
- FIP gasket materials fall into two main categories: base materials (primarily silicone, synthetic rubber, or fluorosilicone) and conductive materials (including nickel, silver, graphite, copper, aluminum, and ferrite).
- When selecting FIP gasket materials, consider budget constraints (silver is highly efficient but expensive), temperature requirements (silicone offers better high-temperature resistance), and environmental factors (fluorosilicone provides superior resistance to oil and fuel).
- Leading FIP gasket material manufacturers include Nolato (TriShield series), Parker Chomerics (CHO-FORM and ParPHorm), and Laird Technologies, each offering various combinations of base materials and conductive fillers.
- Modus Advanced offers vertically integrated manufacturing through their SigShield™ process, handling everything from metal housing machining to FIP gasket dispensing, reducing lead times and simplifying the production process.
If you want to include a form-in-place (FIP) gasket in your design, you’re not alone. These gaskets are incredibly popular across a large variety of industries because of their precision, durability and affordability. But to actually get that FIP gasket into your prototype, you’re going to have to decide what it will be made of.
There are dozens of possible combinations of FIP gasket materials, each of which brings particular strengths and weaknesses for various applications. Admittedly, the choice of gasket material can quickly become overwhelming. That’s why we put together this guide. Read on to learn more about FIP gasket materials.
Selecting FIP gasket materials is only one step in the process. For top-to-bottom understanding of FIP gaskets, check out our comprehensive FIP gasket guide.
Visit the Modus Form-in-Place Gasket Resource Center
Types of FIP Gasket Materials
FIP gaskets are versatile, and they derive this quality in part from the large number of materials they can be made of. Regardless of the FIP gasket material you choose, it will come in paste form, which is then dispensed onto the device’s housing as a liquid.
There are two broad categories of FIP materials: base materials and conductive materials. All FIP gaskets will have a base material, but only conductive gaskets or those that act as electromagnetic interference (EMI) shields will need to include a conductive material.
Conductive Materials for FIP Gaskets
In many applications for FIP gaskets, electrical conductivity is a key consideration. FIP gaskets are actually quite adept in these applications. Here is how it works: you select both a base material and a conductive material, and the conductive metal you choose is mixed into the base material paste.
You can use one or a combination of the following conductive materials in your FIP gasket:
- Nickel: A versatile and cost-effective conductive filler that offers good corrosion resistance and moderate conductivity, making it suitable for general EMI shielding applications.
- Silver: The most electrically conductive metal available for FIP gaskets, providing superior shielding effectiveness but at a significantly higher cost than other fillers.
- Graphite: A lightweight carbon-based material that offers good conductivity, thermal stability, and chemical resistance at a more affordable price point than precious metals.
- Copper: Highly conductive material that provides excellent EMI shielding performance at a more moderate cost than silver, though it may be susceptible to oxidation over time.
- Aluminum: A lightweight, economical conductive filler that offers good shielding effectiveness and is particularly compatible with aluminum housings to prevent galvanic corrosion.
- Ferrite: A magnetic ceramic compound that absorbs rather than reflects electromagnetic waves, making it especially effective for higher frequency applications where signal absorption is preferred over reflection.
Base Materials for FIP Gaskets
The base material you choose will make up the bulk of your FIP gasket. The most common FIP gasket base material is silicone, but synthetic rubber and fluorosilicone are also common options.
- Silicone: The most widely used FIP gasket base material, offering excellent temperature resistance (-55°C to +260°C), good compression set properties, and UV stability, making it ideal for both indoor and outdoor applications.
- Synthetic Rubber: A cost-effective base material option that provides good flexibility and elasticity at moderate temperatures, though typically less resistant to environmental factors than silicone-based alternatives.
- Fluorosilicone: A specialized silicone variant that maintains silicone's temperature resistance while adding superior resistance to fuels, oils, and solvents, making it the preferred choice for aerospace, automotive, and other applications where exposure to these substances is expected.
Selecting FIP Gasket Materials
Choosing FIP gasket materials can be a challenge if you aren’t sure of the properties each material possesses. But before you dive into endless lists of material descriptions on manufacturer websites, you can rule out several of the options with a few key considerations.
For conductive FIP gaskets, you can use your project budget as a starting point. For example, silver is a highly efficient conductive material, but it is much more expensive than nickel and graphite. If budget is a concern, your choice of conductive material might help.
For base materials, you can start to get an idea of what you want by understanding a few key properties of each of the three typical options. If you’re considering silicone or fluorosilicone, you should know that silicone is more resistant to high temperatures, but fluorosilicone is more resistant to oil and fuel. Meanwhile, synthetic rubber can be less expensive but is typically not ideal for outdoor applications because of its vulnerability to the elements.
Of course, many engineers and designers turn to their manufacturing partner for advice on which materials to choose. The team at Modus Advanced maintains expert and up-to-date knowledge of the available FIP gasket materials so we can answer any questions our customers have.
Top FIP Gasket Material Manufacturers
There are plenty of manufacturers of FIP gasket materials around the world. We would love to discuss every material available from every manufacturer, but for the purposes of time and readability, we will focus on the top three manufacturers in this industry.
Parker Chomerics
Parker Chomerics produces the CHO-FORM and ParPHorm line of FIP gasket materials. The company offers these FIP material options:
- CHO-FORM 5513: silicone base with silver and copper filler
- CHO-FORM 5541: silicone base with nickel and graphite filler
- CHO-FORM 5550: silicone base with nickel and graphite filler
- CHO-FORM 5560: silicone base with nickel and aluminum filler
- ParPHorm 1800: non-conductive silicone base
- ParPHorm S1945-25: non-conductive silicone base
- ParPHorm L1938-45: non-conductive fluorosilicone base
Nolato
Nolato produces the Nolato TriShield & TriShield 2.0 series of conductive silicone rubber materials. These are the applicable materials in this line:
- Nolato TriShield 8800: silicone rubber base with silver and nickel filler
- Nolato TriShield 8817: silicone rubber base with nickel and graphite filler
- Nolato TriShield 8812: silicone rubber base with nickel and graphite filler
- Nolato TriShield 8813: silicone rubber base with nickel and graphite filler
Laird
Laird Technologies produces conductive FIP gaskets with metal-coated powder fillers. These products include the following:
- SNC70-RXP: silicone base with nickel and graphite filler
- SNK55-RXP: silicone base with silver and copper filler
- SNL60-RXP: silicone base with silver and aluminum filler
- SNN60-RXP: silicone base with silver and nickel filler
- SIL25-RXP: non-conductive white silicone base
- SNC70-HXP: silicone base with nickel and graphite filler
- SNK60-HXP: silicone base with silver and copper filler
- SNL70-HXP: silicone base with silver and aluminum filler
- SNN65-HXP: silicone base with silver and nickel filler
- SIL35-HXP: non-conductive transparent silicone base
Learn how we broke the mold on traditional supplier relationships
Get Top-Quality FIP Gaskets and More
We wrote the guide on FIP gasket materials, and you read it. Now, it’s time to make your design a reality with the perfectly designed FIP gasket. We can help with that, too.
The team of engineering experts at Modus Advanced can take on every phase of the FIP gasket production process with ease, but we take this strength even further with SigShield™. This is our way of vertically integrating multiple phases of the design process so you don’t have to work with multiple manufacturers, risk miscommunications, pay extra shipping costs or wait for weeks on end. With SigShield™, Modus machines the metal housing, applies platings and coatings, dispenses your FIP gasket and adds thermal or microwave-absorbing materials.
Are you ready to cut typical lead times in half and work with a leading FIP gasket manufacturer? We’re ready to hear from you. Contact Modus Advanced by calling (925) 960-8700 or contacting us online.
Why Choose Modus Advanced for Your FIP Gasket Dispensing?
At Modus Advanced, we've mastered the art and science of FIP gasket dispensing while offering a complete manufacturing ecosystem that accelerates your path to market. Our engineering-first approach means your critical components receive expert attention at every stage.
With Modus, you gain:
- Vertical integration that eliminates shipping between vendors and reduces lead times
- Concurrent manufacturing processes including machining, plating, and thermal material application
- Engineering expertise with over 10% of our staff being engineers who understand your technical challenges
- Enhanced quality control through a single quality system governing the entire process
- Simplified communication with one partner instead of multiple vendors
When one day matters—and we believe it does—our vertically integrated approach doesn't just save time; it helps your innovations reach the field faster, whether that's life-saving medical devices or mission-critical defense systems.
FIP Dispensing Services